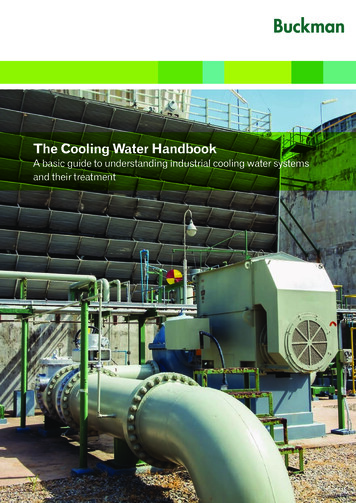
Transcription
The Cooling Water HandbookA basic guide to understanding industrial cooling water systemsand their treatment
2
ContentsCooling water—an introduction . . . . . . . . . . . . . . . . . . . . . . . . . . . . . . . . . . . . . . . . . . . . . . .5Types of cooling systems . . . . . . . . . . . . . . . . . . . . . . . . . . . . . . . . . . . . . . . . . . . . . . . . . . . . .7Once-through . . . . . . . . . . . . . . . . . . . . . . . . . . . . . . . . . . . . . . . . . . . . . . . . . . . . . . . . . . . . . .7Open recirculating . . . . . . . . . . . . . . . . . . . . . . . . . . . . . . . . . . . . . . . . . . . . . . . . . . . . . . . . .7Closed recirculating . . . . . . . . . . . . . . . . . . . . . . . . . . . . . . . . . . . . . . . . . . . . . . . . . . . . . . . .8Specialized . . . . . . . . . . . . . . . . . . . . . . . . . . . . . . . . . . . . . . . . . . . . . . . . . . . . . . . . . . . . . . . .8Common cooling water issues . . . . . . . . . . . . . . . . . . . . . . . . . . . . . . . . . . . . . . . . . . . . . . . .9Scale . . . . . . . . . . . . . . . . . . . . . . . . . . . . . . . . . . . . . . . . . . . . . . . . . . . . . . . . . . . . . . . . . . . . .9Corrosion . . . . . . . . . . . . . . . . . . . . . . . . . . . . . . . . . . . . . . . . . . . . . . . . . . . . . . . . . . . . . . . . .9Organic fouling . . . . . . . . . . . . . . . . . . . . . . . . . . . . . . . . . . . . . . . . . . . . . . . . . . . . . . . . . . . .10Microbiological deposits . . . . . . . . . . . . . . . . . . . . . . . . . . . . . . . . . . . . . . . . . . . . . . . . . . . .10Foam . . . . . . . . . . . . . . . . . . . . . . . . . . . . . . . . . . . . . . . . . . . . . . . . . . . . . . . . . . . . . . . . . . . . .10Basic cooling water treatment . . . . . . . . . . . . . . . . . . . . . . . . . . . . . . . . . . . . . . . . . . . . . . . .11Audit and assessment . . . . . . . . . . . . . . . . . . . . . . . . . . . . . . . . . . . . . . . . . . . . . . . . . . . . . .11Cooling water pretreatment . . . . . . . . . . . . . . . . . . . . . . . . . . . . . . . . . . . . . . . . . . . . . . . . . .11Chemical applications . . . . . . . . . . . . . . . . . . . . . . . . . . . . . . . . . . . . . . . . . . . . . . . . . . . . . .12Fighting scale . . . . . . . . . . . . . . . . . . . . . . . . . . . . . . . . . . . . . . . . . . . . . . . . . . . . . . . . . . . .12Fighting corrosion . . . . . . . . . . . . . . . . . . . . . . . . . . . . . . . . . . . . . . . . . . . . . . . . . . . . . . . . .12Fighting microbiological fouling . . . . . . . . . . . . . . . . . . . . . . . . . . . . . . . . . . . . . . . . . . . . .13Fighting foam . . . . . . . . . . . . . . . . . . . . . . . . . . . . . . . . . . . . . . . . . . . . . . . . . . . . . . . . . . . . .14Monitoring . . . . . . . . . . . . . . . . . . . . . . . . . . . . . . . . . . . . . . . . . . . . . . . . . . . . . . . . . . . . . . . .15Conclusion – taking the heat off your operating budget . . . . . . . . . . . . . . . . . . . . . . . . .17Learn more . . . . . . . . . . . . . . . . . . . . . . . . . . . . . . . . . . . . . . . . . . . . . . . . . . . . . . . . . . . . . . . . . .193
Open Recirculating SystemHeat ExchangerEvaporationBlowdownMakeupWaterCooling TowerPump Once-Through SystemDischargeIntakePumpHeat Exchanger Closed Recirculating SystemColdPump4Heat ExchangerHot
An Introduction to Cooling Water Water works for usWater is used around the world in industrialapplications because it has a number ofvaluable properties. It’s non-toxic. It’s readilyavailable in many parts of the world. Its flowcan be controlled easily through pressureor gravity. And, perhaps most important forcooling water systems, it provides a high levelof thermal conductivity, the ability to absorbheat and transport it away.steel, mining, leather and manufacturingoperations of every description depend onwater for cooling.When we use water to lower the operatingtemperature of equipment or entire plants,it is called cooling water. Industries such aspower, pulp and paper, oil and gas, ethanol, And against usWater is extremely good at dissolvingsubstances and distributing them through out itself. That’s good when you want todeliberately dilute and mix chemicals. It’snot so good when unwanted impuritiesare dissolved.Surface waters used to supply coolingsystems are open to the greater environ mentand can contain a wide variety of organicsuspended matter that causes microbiologicalfouling. Ground water, while protected fromsome of the contaminants surface watersface, can contain high amounts of corrosioncausing metals, such as manganese and iron.When unwanted compounds build to thepoint that solubility is no longer possible,scale forms. When algae and bacteria enterthe system, water temperatures and nutrientscan quickly aid in their growth, reducingwater quality, fouling system surfaces andpromoting corrosion.5
That’s why proper treatment is importantBecause water is so good at dispersing mineralsand helping living things grow, water incooling systems must be specially treated andmonitored. The goal is water that runs free andclean, maximizing its ability to absorb heat andcarry it away, so your systems stay cool.The key is water treatment optimization—theability to not only apply the right chemistriesbut also to constantly monitor and controlwater quality to keep it balanced at all times. Bymonitoring pH, water temperature, electrical6conductivity, microbiological activity, corrosion,chemistry levels and other variables, your plantcan be proactive. That not only helps keepcontaminants from growing in your system butalso helps you grow the bottom line. The rightprogram can: Increase production Reduce downtime Lower operating and chemical costs Reduce your operation’s impact onthe planet
Types of Cooling SystemsTreatment of cooling water will be different depending upon thekind of system in use. Here are the basic types: Once-throughA once-through cooling system pumps waterinto equipment where it passes over a hotsurface in order to cool it. The water then exitsthe equipment, taking heat with it. Simple andeffective in a wide range of applications, thissystem can be undermined by the quality ofthe raw water. Lakes and rivers can bring insuspended matter and pollutants. Well waterscan contribute large amounts of iron and scaleforming materials. Because water is only usedonce, a large amount of water is required. Open recirculatingThis system sends cooling water out of theequipment and into a pond or cooling tower,which is open to the atmosphere. Hereevaporation occurs, removing heat along withthe evaporated water. As a result, the remainingwater cools. It is then combined with makeupwater, which replaces the evaporated water,and is sent through the system again.Open-recirculating systems have becomeprevalent as water has become scarcer andenvironmental restrictions have been placed onbleedoff discharge.7
Closed recirculatingAll water used to carry heat away fromequipment is run through a heat exchanger,which is cooled by air, mechanicalrefrigeration or a separate open cooling watersystem. There is no evaporation or makeupwater required, so contamination—and the SpecializedA specialized cooling systemmight utilize compression orabsorption-type refrigerationor air conditioning systems,which can be used to cool bothprocesses and work spaces. Itmight utilize a cooling coil belowthe deck of the cooling tower.Or it might include the use ofindustrial air washers in whichair is filtered, sprayed and thenforced through a series of misteliminators. Each system has itsown unique risks for fouling andmust be treated accordingly.8Scalemaintenance that results—is less likely.Since the same water is used over andover, water and sewage costs are lower andenvironmental compliance is easier. Manyonce-through systems have been converted toclosed systems for this reason.
Common cooling water issuesCooling water has many enemies. Sometimes they work alone.In other instances, they team up and compound the problem.For example, algae growth creates the perfect environment forcorrosion to take hold. Here’s a quick look at the major sourcesof cooling water fouling. ScaleScale and scalelike deposits include calciumcarbonate, calcium phosphate, magnesiumsilicate, silica and other mineral compounds.They build up on heat exchanger tubes,reducing heat transfer. In sufficient amountsthey can restrict water flow. When heattransfer is reduced, efficiency of productionis reduced and the quality of products can becompromised. Equipment can suffer damagefrom overheating. Scale can cause expensivedowntime for cleaning or repair, resulting in lostrevenue. In addition, scale and scalelike depositscan accelerate corrosion. CorrosionCorrosion occurs when electrically chargedparticles flow through metal components,causing the metal to oxidize and eventuallylose thickness. Corrosion causes pitting andleaks in cooling systems and can lead to thereplacement of pipes, pumps, heat exchangertubes and even entire cooling towers. Ironoxide, especially, contributes to foulingand deposition, which interfere with heattransfer. Downtime for equipment repair orreplacement is always costly.Corrosion9
Organic foulingMud, sand, silt, clay, biological matterand even oil can enter the system throughits makeup supply or from the air. Thesesuspended materials can accumulate andsettle in the system, blocking flow andreducing efficiency. Oil film can reduceheat transfer and encourage the growthof microorganisms. Microbiological depositsBiofilms severely restrict heat transfer.Slime masses bind inorganic and organicfoulants and plug systems. Algae and fungicause extensive plugging and fouling of heatexchanger tubes, water lines, tower spraynozzles, distribution pans, screens and fill.Microbiological fouling also contributes tounder-deposit corrosion as well as the growthof corrosion-causing bacteria. FoamCascading water, the continuous recyclingof contaminants and a high concentration offoam stabilizers can cause foam to overflowthe tower sump, blow off the towers or evencause an airlock in the water pumps. Worstof all, foam concentrates deposit-formingmaterials, increasing the chance of foulingin the system.10
Basic coolingwater treatmentTreatment can be dividedinto four steps: Audit and assessment Cooling waterpretreatment Chemical applications Monitoring Audit andassessmentBefore effective treatment can beprovided, a thorough assessmentof conditions in your coolingwater system must be made.Experienced field engineers backedby laboratory resources can audityour system, perform accurate teststo measure water quality and trouble shoot problems. Some commontests include: ATP testing Corrosion failure analysis Biocide efficacy Water and mass balances On-site physical audits byindustry experts Computer modelling Deposit analysis Biofilm and dispersion analysis Cooling water pretreatmentPretreatment for cooling systems includes: Modification of the water composition – clarifiersand cold-lime softening equipment removesuspended solids, organics and/or hardness thatare present in the makeup water or in recycledcooling water Removal of suspended solids in the cooling water –side‑stream filtration removes solids but doesn’talter the chemical composition of the cooling water11
Chemical applicationsTo control scale, corrosion, microbiologicalfouling, and foam, water quality mustbe maintained at all times, and the rightmicrobicides must be applied in just theright doses. That takes a delicate balance ofchemistries and application expertise.Photomicrograph of Ca3(PO4)2 scaleFighting ScaleScaling in cooling water systems can beprevented using four basic approaches:1. Limit the concentration of critical ions bymaintaining concentrations that are lower thanthose required to cause scaling. This can beaccomplished by pretreatment of the water or bylimiting the tower cycles of concentration.2. Reduce alkalinity with acid. This removescarbonate and bicarbonate by converting themto CO2. Since the carbonate level is controlled,the potential for calcium carbonate is restricted.3. Alter system design or operation. Scalingpotential can be altered by altering the system’smechanical operation. Options include:12 Increasing cooling water velocity, whichkeeps the water cooler Using compressed air to “air rumble” theheat exchanger inlet water on a periodicbasis to dislodge and remove scalesand deposits Modifying the exchanger design so that thecooling water is on the tube side, promotinghigher velocity Changing the metallurgy of the heat transfersurface. Mild steel heat
Because water is so good at dispersing minerals and helping living things grow, water in cooling systems must be specially treated and monitored . The goal is water that runs free and clean, maximizing its ability to absorb heat and carry it away, so your systems stay cool . The key is water treatment optimization—the