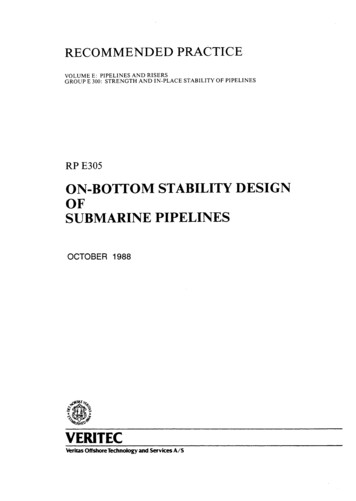
Transcription
RECOMMENDED PRACTICEVOLUME E: PIPELINES AND RISERSGROUP E 300: STRENGTH AND IN-PLACE STABILITY OF PIPELINESRP E305ON-BOTTOM STABILITY DESIGNOFSUBMARINE PIPELINESOCTOBER 1988VERlTECVeritas Offshore Technology and.Services A/S
II Veritec has no liability for loss or damage caused by the use of this document if usedwithout the involvement ofVeritec.To the extent Veritec is performing services in connection with the use of thisdocument, the liability of Veritec will be regulated in specific agreement between theclient and Veritec.No part of this document may be reproduced in any form without the prior writtenpermission from Veritec. Veritas Offshore Technology and Services AJS08.88.500
IIIPREFACERecommended Practice are guidelines for solutions, calculation methods,technical specifications (Volume A-E) and design of offshore objects (Volume 0).The Recommended Practice publications cover proven technology andsolutions which have been experienced by Veritec to represent good practice. Thepublications do not cover all areas of offshore technology, but are meant tosupplement the recognized codes and standards frequently used within theindustry.The Recommended Practice publications are divided into 6 volumes, and eachvolume is divided into groups. Within each group the RecommendedPractices are issued as selfcontained booklets. See table on next page. Volume 0 gives guidelines on design of offshore objects. These publications areconsidered as Recommended Practices related to offshore objects.Volume A-E give guidelines on specific technical solutions, methods ofcalculations etc. These publications are considered as Recommended Practicesrelated to subjects.RP E305 On-Bottom Stability Design of Submarine Pipelines. GeneralThis Recommended Practice replaces the following Veritec publications,None Changes in this revision of Recommended Practice.None .
IVGeneral view of content ofVeritec's Recommended Practices.Table 1:RECOMMENDED PRACTICES related to offshore objectsDesign of offshore objectsVolume 0GroupGroupGroupGroupo100oo300400o 200Design of drilling and production facilitiesDesign of structuresDesign of pipeline systemsDesign of subsea production systemsRECOMMENDED PRACTICES related to subjectsVolume AGroupGroupGroupGroupGroupGroupGroupA 100A 200A 300A 400A 500A 600A 700Volume BGroupGroupB 100B 200GroupGroupGroupGroupGroupB 300B 400B 500B 600B 700Quality assurance methodologyQuality systemsEvaluation of contractors and suppliersQuality auditsQualification of QAJQC personnelSafety assurance systemsSafety and risk analysisDocumentation and information systemsMaterials technologyMaterials for structural applicationMaterials for application in drilling, completion, productionand processing systemsMaterials for pipelines and risersCorrosion protectionSampling and testing of materialsWelding and heat treatmentNon-destructive examinationVolume CFacilities on offshore installationsGroup C 100Group C 200Group C 300Group C 400Group C 500Group . C 600Group C 700Group C 800Group C 900General safetyProduction and processing systemsInstrumentationElectrical systemsDrilling and well completionMechanical equipment and piping systemsFabrication of drilling, production and processing plantsHook-up and commissioningIn-service inspection and maintenance of drilling, productionand processing plants.Volume DStructuresGroupGroupGroupGroupGroupGroupRisk and reliability of structuresLoads and conditionsFoundationSteel structuresConcrete structuresAluminium structuresD 100D 200D 300D 400D 500D 600
vGroupGroupGroupD 700D 800D 900Volume E GroupGroupGroupGroupGroupGroupGroupEEEECompliant structuresFabrication, transportation and installation of structuresIn-service inspection and maintenance of structuresPipelines and risers100200300400E 500E 600E 700Risk and reliability of pipeline systemsEnvironmental loads for pipeline systemsStrength and in-place stability of pipelinesPipeline weight coating and corrosion protectionFlexible risers, pipe hoses and bundlesStorage, transportation and installationIn-service inspection and maintenance of pipeline systems
VIAcknowledgementThis Recommended Practice for On-Bottom Stability, prepared by Veritec, hasbeen sponsored by:Esso NorgeNorskHydroStatoilThe unlimited access to data, as well as the very valuable technicaldiscussions/comments, from the representatives from above companies, havebeen highly appreciated throughout the process of preparing the RP.SINTEF and Danish Hydraulic Institute have been subcontractors for part of thework, and we also thank them for their contributions.We will also like to thank the members from the industry who took their time tocomment and attend the review meeting on the draft version of the RP.
vnCONTENTSPage o.LIST OF SYMBOLS11.INTRODUCTION32.2.12.22.32.42.52.6DESIGN CONDITIONSBasic ConditionsReturn PeriodsEnvironmental ConditionsGeotechnical ConditionsTopographical and Bathyrnetric ConditionsPipe Data33343.3.13.23.33.43.5DESIGN METHODGeneralLoad CasesAnalysis MethodsSinking/FloatationOverview of the Design Method1011124.4.14.24.34.4DESIGN CRITERIAGeneralPotential Lateral DisplacementBending StrainOther Relevant Criteria13131314155.5.15.25.3ANALYSIS METHODSDynamic AnalysisGeneralized Stability AnalysisSimplified Static Stability 5A.6APPENDIX A BOUNDARY LAYER REDUCTIONIntroductionVelocity ProfileCurrent FlowCombined Wave and Current FlowExamplesReferences30303031313337APPENDIX B CALCULATION EXAMPLESIntroductionSimplified MethodGeneralized Method38383840B.lB.28.3
1o.LIST OF SYMBOLSCDEGKLMR uT1 ToTpTuUcUsUs *U*UDUrU(z)WsWsdddsofw sgkVeritec RP E305constantnominal outside diameter of pipemodulus of elasticityrelative soil weight, sandKeulegan - Carpenter number, K Us T u/Dpipe weight parametercurrent to wave velocity ratio, M Uc/U sreduction factor due to wave directionality and wavespreadingshear strength parametertime parameter, T T1IT utotal displacementorbital semi-diameter of particle velocitysignificant accelerationdrag coefficientlift coefficientinertia coefficientouter steel pipe diam. incl. corrosion coatinginternal pipe diametersteel pipe outer diameterdrag forceinertia forcelift forceload factorsignificant wave heightequivalent sand roughness parametersafety factorwave spectrum (long-crested sea)near-bottom horizontal velocity spectrumundrained shear strength of clay soiltime lengthparameter, T n v' (d / g)spectral peak period of surface wave spectrummean zero up-crossing periodcurrent velocity perpendicular to the pipesignificant velocity perpendicular to the pipesignificant velocity perpendicular to the pipe (no reductionfactor included).friction velocityaverage velocity over pipe diameter, Dreference steady velocitysteady flow velocitysubmerged pipe weightdesign weightwater depthmean grain sizecorrection factor on submerged weightgravity constantwave numberspectral momentsspreading exponentstee 1pipe thicknesselevation above seabedbottom roughness parameterapparent roughness
Veritec RP E3052reference height above seabeda138 ,e'W({3,8)yK}lCUcupPcPccPi.PsPstPwa88pPhillips' constantsub-direction around main wave directionscaled lateral displacementengineering and generalized strainspreading functionpeakedness parameter in J onswap wave spectrumvon Karrnan's constantsoil friction factorangular frequencyangular frequency of spectral peakdensity of concrete coatingdensity of corrosion coatingdensity of internal contentdensity of sand soildensity of steel materialmass density of waterspectral width parametermain wave direction, phase angledirection perpendicular to the pipeline
31.Veritec RP E305INTRODUCTIONThis Recommended Practice outlines the basic considerations with regard to thestability design of submarine pipelines.The main objectives of this recommended practice are to make the latest state-ofthe-art information on pipeline stability available for use in the design ofsubmarine pipelines, and to provide a framework from which stability designmethods can be developed further as more information becomes available. TheRP is mainly based on the results from the Pipeline Stability project PIPESTABcarried out by SINTEF (1983 - 1987) and sponsored by Esso Norge A/S andStatoil, see /2/ - /8/.Results from other research programs may be equally applicable for On-BottomStability of Pipelines. It is the intention, through revisions of the present RP, to ·incorporate other results/data as they become available and thereby extend thelimits for use.The design method presented in this Recommended Practice relates to a pipelineresting on the sea bed throughout its lifetime, or prior to some other form ofstabilization (eg. trenching, burial, self-burial). The stability of the pipeline isthen directly related to the submerged weight of the pipeline, the environmentalforces and the resistance developed by the sea bed soil. Consequently the aim ofstability design is to verify that the submerged weight of the pipeline is sufficientto meet the required stability criteria.2.DESIGN CONDITIONS2.1Basic Conditions2.1.1 The following basic conditions should be considered during the on-bottomstability design of submarine pipelines: Environmental conditionsGeotechnical conditions of the sea bedTopographical conditions of the sea bed (eg, slope, rock outcrops,depressions)Bathymetry (water depth)Pipe data (diameter, wall thickness, concrete coating)Location of pipeline restraints (riser connections, crossings, etc)2.2Return Periods2.2.1 The stability design is to be based on a given return period of near-bottomenvironmental conditions acting perpendicular to the pipe. In general, bothnear-bottom wave induced particle velocities and near-bottom currents will needto be considered.2.2.2 If sufficient information is available on joint probability of waves andcurrent, then the combined wave and steady current with 100 year recurrenceinterval should be used. If inadequate information is available on the jointprobability of waves and current, then the following are suggested for theoperational condition:
4Veritec RP E305WavesIfwaves dominates forces. 100 year return condition of nearbottom wave-induced particle velocitynormal to the pipeline.Current: 10 year return condition.If current dominates forces {waves : 10 year return conditionCurrent: 100 year return condition.2.2.3 For temporary phases, the recurrence period should be taken as follows:Duration less than 3 days: The environmental parameters for determination ofenvironmental loads may be established based on reliable weather forcasts.Duration in excess of 3 days: a) No danger for loss of human lives. A returnperiod of 1 year for the relevant season can be applied.b) Danger for loss of human lives. The environmental parameters should bedefined with a 100 year seasonal return period.However, the relevant season should not be taken less than 2 months.2.3Environmental Conditions2.3.1 The following environmental conditions should be evaluated at a numberof positions along the length of the pipeline:WavesCurrents The number of positions necessary to adequately define the environment will bedependent on the length of the pipeline and the variations in water depth, seabedsoil and meteorological conditions.2.3.2 The environmental conditions used in the stability design should be basedon adequate data from the area in question. The data may be frommeasurements, hindcast models, or visual observations. If sufficient data on theparticular area is not available, reasonably conservative estimates based on datafrom other nearby locations may be used.2.3.3 Recognised methods of statistical analysis should be used to describe therandom nature of the environmental conditions. Seastates will normally bedefined in terms of the significant wave height (Hg), spectral peak period (Tp) andcorresponding return probability.2.3.4 The form in which the wave information is available, is dependent on theamount and quality of data available for the particular location in question. Thismay range from a joint distribution of H, and T p with directional information toan omnidirectional design value for H, with an estimated period. The designmethod presented in section 3. will accept wave input of varying degrees ofsophistication.2.3.5 The peak period (T p ) will depend on fetch and depth limitations as well asduration of the seastates. If no other information is available for the peak period,then the following relationship may be used for the upper limit:T p v(250 Hs!g)If a joint distribution of H, and T p is available, then the combination of H, - T pwhich gives the most extreme near-bottom conditions should be selected.
5Veritec RP E3052.3.6 The directional distribution of the wave conditions may be accounted forwhen selecting the design wave-induced particle velocity. Normally extremeseastates from different directions will need to be considered. If no directionalwave information is available then the extreme wave conditions should beassumed to act perpendicular to the axis of the pipeline.2.3.7 The short crestedness of the waves may be accounted for when selecting thedesign wave-induced particle velocity. Ifno site specific information is available,then this may be taken into account by consideration of the energy spreadingaway from the main direction of wave propagation.2.3.8 The wave-induced particle velocity to be used in the stability designanalysis is represented by the significant value of the near-bottom velocityperpendicular to the pipeline (Us), and the corresponding mean zero up-crossingperiod (Tu). 2.3.9 When calculating Us and Tu, the most appropriate formulation for thewater surface elevation spectrum should be used. For North Sea conditions theJonswap spectral formulation is recommended. For long-crested seas, theJonswap spectrum is given by:SI}l} (eo) ag2 (w)-5 exp {-5/4(w/w p)-4}
RP is mainly based on the results from the Pipeline Stability project PIPESTAB carried out by SINTEF (1983 - 1987) and sponsored by Esso Norge A/S and Statoil, see /2/ -/8/. 2.2.1 The stability design is to be based on a given return period of near-bottom environmental conditions acting perpendicular to the pipe. In general, both near-bottomwave induced particle velocities and near .