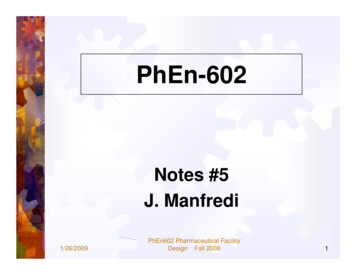
Transcription
PhEn-602Notes #5J. Manfredi1/26/2009PhEn602 Pharmaceutical FacilityDesign Fall 20081
Clean Rooms and Controlled EnvironmentsISO vs FS209E: key differencesISO limits are based strictly on a cubic meter FS 209E has limits for both ft3 and m3 Three new classes were introduced – ISOClass 1 and Class 2, (both of which arecleaner than FS 209E class 1), & ISO Class 9. ISO added the 1.0 micron particle size1/26/2009PhEn602 Pharmaceutical FacilityDesign Fall 20082
Clean Rooms and Controlled EnvironmentsISO vs FS209E: key differences ISO generally requires fewer sampling locations thanFS 209E With ISO, number of sample locations is based onclean room area, whereas with FS 209E it is basedon Class, size of clean room, and whether or notunidirectional flow is present ISO has a minimum 1 minute sample time, FS 209Edoes not.1/26/2009PhEn602 Pharmaceutical FacilityDesign Fall 20083
Clean Rooms and Controlled Environments European Union classifications – (this list excludesviable particulate limits)At-RestIn-OperationMax # particles perMax # particles per Max # particles percubic meter (per cubic cubic meter (per cubic meter (perft.)cubic ft.)cubic ft.)Max # particlesper cubic meter(per cubic ft.)0.5μm0.5μm5μmGrade D 3,500,000 (100,000) 20,000 (570)No spec.No spec.Grade C 350,000 (10,000)2000 (57)3,500,000 (100,000) 20,000 (570)Grade B 3,500 (100)None350,000 (10,000)2000 (57)Grade A 3,500* (100)None3500 (100)None1/26/20095μmPhEn602 Pharmaceutical FacilityDesign Fall 20084
Clean Rooms and Controlled EnvironmentsFDA vs. EU RequirementsGrade A approximates Class 100 in U.S.,but requires unidirectional flow.QGrade B in the “at rest” condition hasthe same particle limit as Grade A “atrest”, but does not require unidirectionalflow.QGrade C is similar to Class 100,000 “inoperation”.QGrade B in operation approximates Class10,000 “in operation”.Q1/26/2009PhEn602 Pharmaceutical FacilityDesign Fall 20085
Clean Rooms and Controlled EnvironmentsFDA Aseptic Guidelines:Uses both the FS 209E classifications andISO classifications for aseptic manufacturing. Non-viable particle levels must meet the FS209E classes and ISO classes. Mentions the as-built and dynamic state ofthe cleanroom with more emphasis on thedynamic (“In-operation”) condition. Contains limits for viable particles1/26/2009PhEn602 Pharmaceutical FacilityDesign Fall 20086
Clean Rooms and Controlled EnvironmentsFDA vs. EU Requirements EU has requirements for “At-Rest” and “InOperation” FDA Aseptic guidelines are based on “InOperation” condition only. EU focuses on two particle sizes – 0.5μm and 5μm FDA Aseptic guidelines: 0.5μm only EU has limits for the 5 micron particle, FDAAseptic Guidelines do not.1/26/2009PhEn602 Pharmaceutical FacilityDesign Fall 20087
Clean Rooms and Controlled EnvironmentsUseful cleanroom websites that cover some ofthe material discussed: www.s2c2.co.uk/docs/cccs.pdf www.particle.com www.clean-room.com www.fda.gov/cder/guidance/5882fnl.htm Website for FDA Aseptic guidelines 02 Pharmaceutical FacilityDesign Fall 20088
Clean Rooms and Controlled EnvironmentsTesting the Cleanroom for Particle ClassFS 209E Number of sampling locations is afunction of area and classification Different sampling location formula forunidirectional and non-unidirectionalflow clean rooms1/26/2009PhEn602 Pharmaceutical FacilityDesign Fall 20089
Clean Rooms and Controlled EnvironmentsFS 209E: For non-unidirectional flow clean rooms, the lesser of:SI (metric) units:English units:NL Ax64/(10M)0.5NL A/(Nc)0.5 Where M SI A floor area ofdescription of class A floor area ofclean zone in m21/26/2009clean zone in ft2 Where Nc is EnglishclassPhEn602 Pharmaceutical FacilityDesign Fall 200810
Clean Rooms and Controlled EnvironmentsISO – number of sampling locations Particulate Testing - Number ofsampling locationsNL A NL minimum number of sampling locations A area of clean room in square meters1/26/2009PhEn602 Pharmaceutical FacilityDesign Fall 200811
Clean Rooms and Controlled Environments Particle testingParticle Size(Microns)Cumulative #(Per Ft.3)Differential #(Per 02 Pharmaceutical FacilityDesign Fall 200812
Clean Rooms and Controlled EnvironmentsParticle Size(Microns)0.3Cumulative #(Per Ft.3)175Differential #(Per Ft.3)700.51.05.01051029582 Does the above data show that the room meets Class 100conditions at 0.5 micron? NO Does the above room pass for ISO Class 5 at 1.0 micron? YES1/26/2009PhEn602 Pharmaceutical FacilityDesign Fall 200813
Clean Rooms and Controlled EnvironmentsISOvsFS209E:1/26/2009ISO 14644-1 FED Std 209EISO ClassEnglish Metric1234567891101001,00010,000100,000PhEn602 Pharmaceutical FacilityDesign Fall 2008M1.5M2.5M3.5M4.5M5.5M6.514
Clean Rooms and Controlled EnvironmentsISOvsFS209E:1/26/2009ISO14644-1ISO Class123456789FED Std 3.5M4.5M5.5M6.5PhEn602 Pharmaceutical FacilityDesign Fall 200815
Clean Rooms and Controlled Environments25 MicronsDust0.5 MicronsOthercontaminants100MicronsHuman Hair1/26/2009PhEn602 Pharmaceutical FacilityDesign Fall 200816
Clean Rooms and Controlled EnvironmentsParticle counting The particle count limits are for the particularsize and larger The particle counter can distinguish betweendifferent particle sizes The counter typically prints out data thatprovides actual counts at the specific particlesize (differential) and the cumulative count1/26/2009PhEn602 Pharmaceutical FacilityDesign Fall 200817
Continuous Particle Monitoring Systems Particle counting: continuous sampling –two types Sequential monitoring system (manifoldsystem) Simultaneous monitoring system1/26/2009PhEn602 Pharmaceutical FacilityDesign Fall 200818
Clean Rooms and Controlled EnvironmentsTypical Particle Counter1/26/2009PhEn602 Pharmaceutical FacilityDesign Fall 200819
Controlled Environments-Cleanroom Standards1/26/2009PhEn602 Pharmaceutical FacilityDesign Fall 200820
Continuous Particle MonitoringSequential (manifold)1/26/2009Simultaneous – remoteparticle countersPhEn602 Pharmaceutical FacilityDesign Fall 200821
Continuous Particle Monitoring Systems Particle counting: continuous sampling Sequential monitoring system: Single particle counter sequences through samplelocations Disadvantage: particle loss from long sampling tubelengths Rotate thru sensors, can miss a potential high-readingSimultaneous monitoring system1/26/2009 Multiple particle counters Every location has a particle counter More expensive than sequentialPhEn602 Pharmaceutical FacilityDesign Fall 200822
Clean Rooms and Controlled EnvironmentsOther important notes Particle counting: continuous sampling Sequential monitoring system (centralized manifoldsystem): Sample ports connected to central vacuum source Air taken from each port in rotational fashion Central vacuum pump and particle counterSimultaneous monitoring system Particle sensors connected via cabling to a centralcomputer Both allow auto notification if particle levels exceed alertand action levels1/26/2009PhEn602 Pharmaceutical FacilityDesign Fall 200823
Sequential Particulate Monitoring1/26/2009PhEn602 Pharmaceutical FacilityDesign Fall 200824
1/26/2009PhEn602 Pharmaceutical FacilityDesign Fall 200825
Sequential ParticleMonitoring SystemSequentialParticleMonitoringSystem – analternatelook at it ationsAirTubingSensorRoom 11/26/2009VacuumPumpSensorRoom 2PhEn602 Pharmaceutical FacilityDesign Fall 2008SensorRoom 326
Simultaneous ParticleMonitoring SystemInput boardElectrical signal4 - 20 mA to PCSimultaneousParticleCountingParticleCounterRoom 11/26/2009ParticleCounterRoom 2PhEn602 Pharmaceutical FacilityDesign Fall 2008ParticleCounterRoom 327
Clean Rooms and Controlled EnvironmentsCommon items - ISO Standard 14644-1 & 2 and FS 209E No fewer than two sample locations Minimum sample volume and time is also dictatedin each standard For the most part, ISO Class 3 through 8 are verysimilar to FS 209E Class 1 through 100,000. The particle limits are for the particle size statedand larger1/26/2009PhEn602 Pharmaceutical FacilityDesign Fall 200828
Clean Rooms and Controlled EnvironmentsFS 209E & ISO Standard 14644-1 & 2 Note that the number of sampling locations is the minimumrequired. It’s often easier to sample a room at 10 or more locations,rather than going through the statistical analysis1/26/2009PhEn602 Pharmaceutical FacilityDesign Fall 200829
Clean Rooms and Controlled EnvironmentsImportant note regarding FDA Aseptic Guidelines: FDA Aseptic guidelines do not allow averaging at asampling site! Each discrete sample must be below the class limit. This is important, since you can pass ISO and FS 209E, andnot meet FDA requirement. FDA aseptic guidelines still reference the FS 209E classes. FDA has no formal position regarding the ISO standardsimpact on pharmaceutical manufacturers1/26/2009PhEn602 Pharmaceutical FacilityDesign Fall 200830
Clean Rooms and Controlled EnvironmentsEuropean Union Guide to GMP (EU cGMP) Formal title:“The Rules Governing MedicinalProducts in the European Union. Volume 4.Good Manufacturing Practices – MedicinalProducts for Human and Veterinary Use” Establishes four grades: Grade A, B, C, D Grade A is cleanest, Grade D is least clean Each grade has limits for viable and non-viableparticulates Refers to ISO standard for more details1/26/2009PhEn602 Pharmaceutical FacilityDesign Fall 200831
Clean Rooms and Controlled EnvironmentsEuropean Union Guide to GMP (EU cGMP) “Grade A: The local zone for high-risk operations, e.g.filling zone, stopper bowls, open ampoules and vials,making aseptic connections. Normally such conditionsare provided by a laminar flow work station. Laminarflow air systems should provide a homogeneous airspeed” “Grade B: For aseptic preparation and filling, this is thebackground environment for Grade A zone.” “Grade C and D: Clean areas for carrying out lesscritical stages of the manufacture of sterile products.”1/26/2009PhEn602 Pharmaceutical FacilityDesign Fall 200832
Clean Rooms and Controlled EnvironmentsEU Classifications – (excludes viable particulate limits)At-RestIn-OperationAt-Rest Max #particles per cubicmeterAt-Rest Max #particles per cubicmeterIn-Operation Max #particles per cubicmeterIn-OperationMax # particlesper cubic meter0.5μ m5μ m0.5μ m5μ mGrade D3,500,00020,000No spec.No spec.Grade C350,00020003,500,00020,000Grade B3,500None350,0002000Grade A3,500*None3500*None*EU Grade A requires unidirectional flow1/26/2009PhEn602 Pharmaceutical FacilityDesign Fall 200833
Clean Rooms and Controlled EnvironmentsEU Classifications – (excludes viable particulate limits)(per cubic foot numbers in parenthesis)At-RestIn-OperationMax # particles per Max # particles perMax # particles percubic meter (per cubic cubic meter (per cubic meter (percubic ft.)cubic ft.)ft.)Max # particlesper cubic meter(per cubic ft.)0.5μ m0.5μ m5μ mGrade D 3,500,000 (100,000) 20,000 (570)No spec.No spec.Grade C 350,000 (10,000)2000 (57)3,500,000 (100,000) 20,000 (570)Grade B 3,500 (100)None350,000 (10,000)2000 (57)Grade A 3,500* (100)None3500 (100)None5μ m*EU Grade A requires unidirectional flow1/26/2009PhEn602 Pharmaceutical FacilityDesign Fall 200834
Clean Rooms and Controlled EnvironmentsManufacturing Operation and CleanRoom Class – EU RequirementsAseptic Preparation: Washing of components - Grade Denvironment Compounding - Grade C if later filtered. Filling: Grade A with Grade Bbackground1/26/2009PhEn602 Pharmaceutical FacilityDesign Fall 200835
Clean Rooms and Controlled EnvironmentsManufacturing Operation and Clean Room ClassFDA/US Requirements – Aseptic processesTypical Process Step BackgroundenvironmentProduct/containerclosure exposureareaDispensingClass 100,000Local protection –specific enclosuresCompoundingClass 100,000Class 10,000FiltrationClass 10,000Class 100Initial prep/washingcomponentsPharmaceutical - Pharmaceutical Class 100,000Class 100,000“at rest”“at rest”Final rinse ofcomponents/containersClass 100,000Class 100,000From ISPE Baseline Guide – Volume 3 – Sterile Manufacturing Facilities1/26/2009PhEn602 Pharmaceutical FacilityDesign Fall 200836
Clean Rooms and Controlled EnvironmentsManufacturing Operation and Clean Room ClassFDA/US Requirements – Terminally sterilized processesTypical Process stepBackgroundenvironmentProduct/container/closure exposureareaDispensingClass 100,000Class 100,000CompoundingClass 100,000Class 100,000FiltrationClass 100,000Class 100Initial prep/washingcomponentsPharmaceutical-Class 100,000“at rest”Pharmaceutical Class 100,000 “atrest”Final rinse ofcomponents/containersPharmaceutical-Class 100,000“at rest”Class 100,000From ISPE Baseline Guide – Volume 3 – Sterile Manufacturing Facilities1/26/2009PhEn602 Pharmaceutical FacilityDesign Fall 200837
Clean Rooms and Controlled EnvironmentsManufacturing Operation and Clean Room ClassFDA/US Requirements – Aseptic processesTypical Process stepBackgroundenvironmentProduct/container/closure exposureareaLoading of components andcontainers forsterilization/depyrogenationClass 100,000Class 100,000Sterilization ofcomponents/depyrogenationof containers - unloadingClass 10,000Class 100(orwrapped/sealed)Filling and stopperingClass 10,000Class 100Lyophilization OperationN/AClosed systemLyophilization transferClass 10,000Class 100From ISPE Baseline Guide – Volume 3 – Sterile Manufacturing Facilities1/26/2009PhEn602 Pharmaceutical FacilityDesign Fall 200838
Clean Rooms and Controlled EnvironmentsManufacturing Operation and Clean Room Class – FDA/USRequirements – Terminal Sterilized processesTypical Process stepBackgroundenvironmentProduct/container/closure exposureareaSterilization ofcomponents/depyrogenationof containers - loadingPharmaceutical Class 10
Design Fall 2008. 3. Clean Rooms and Controlled Environments ISO vs FS209E: key differences ISO generally requires fewer sampling locations than FS 209E With ISO, number of sample locations is based on clean room area, whereas with FS 209E it is based on Class, size of clean room, and whether or not unidirectional flow is present ISO has a minimum 1 minute sample time, FS 209E does not. 1/26 .