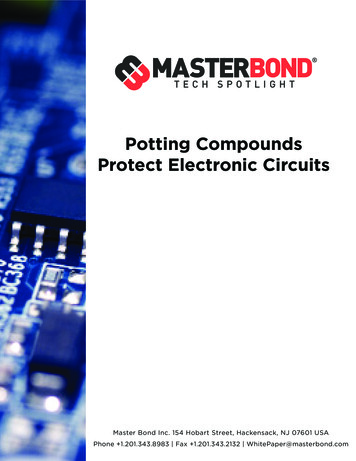
Transcription
TECH SPOTLIGHTPotting CompoundsProtect Electronic CircuitsMaster Bond Inc. 154 Hobart Street, Hackensack, NJ 07601 USAPhone 1.201.343.8983 Fax 1.201.343.2132 WhitePaper@masterbond.com
Potting Compounds ProtectElectronic CircuitsProduct reliability is an absolute must for manufacturers tosucceed in today’s competitive marketplace. As customersdemand ever increasing levels of performance at lower unitcosts, it becomes increasingly challenging to ensure thatelectronic circuits operate as designed for a prolongedperiod of time. Delicate components, densely populatedprinted circuit boards (PCBs), confining packaging, andhighly demanding service environments have the potentialto lead to increased failure rates as a result of excessiveheat build-up and electrical interference.Hostile conditions jeopardize productreliabilityElectronic equipment is often subjected to one or morestresses that may impair performance. Prolonged exposureto high temperatures or cryogenic conditions, chemicals,rigorous thermal cycling, mechanical shock, thermal shock,and other conditions can adversely affect electronic devices— causing them to fail.During manufacturing and assembly, components mustoften withstand high soldering temperatures and aresometimes exposed to cleaning agents and other chemicalsthat can interfere with circuit operation. Additionally,electronic assemblies are commonly subjected to rigorousqualification testing. This includes challenging conditionssuch as extreme heat, chemical exposure, thermal cycling,thermal shock or mechanical shock, excessive vibrations,all of which can cause product failure. Often qualificationtesting is more rigorous than the actual operatingconditions.Potting isolates electronics from theenvironmentPotting and encapsulation compounds impart the highestlevel of protection from environmental, thermal, chemical,mechanical, and electrical conditions. Designed tocompletely encapsulate a component, module, or PCB,these specially formulated compounds effectively shieldthe unit from its surroundings while providing structuralsupport. Potting compounds offer a higher level of physical,chemical, electrical, and temperature protection than doconformal coatings. The flip side is potting can often addextra processing time, cost and weight.Epoxies and silicones are among the most frequentlyused potting compounds. These can be applied to PCBs,capacitors, power electronics, LED lighting, sensors,and more. Some of the desired properties include goodadhesion, excellent electrical insulation, thermal stability,superb chemical resistance, low shrinkage upon curing, anappropriate coefficient of thermal expansion (CTE), andsuitable viscosity for the specific application. Formulationscan be blended to provide a balance of these and otherproperties through careful selection of resin, agent, andfillers.Potting, Casting & EncapsulationPotting compounds can be applied to an electronicdevice in one of three ways: potting, casting, orencapsulation. The most commonly used method ispotting, in which the device is placed in a “pot”, orcase, and a liquid potting compound is poured intothe case until it is filled to the brim. The case is leftintact, becoming part of the finished unit. Castingis similar to potting, except that instead of a case,a mold is used and is removed after the compoundhardens. Casting is used to create a molded unit.Encapsulation involves dipping the component intoa resin system so that a thick coating forms aroundthe component.Although the methods differ somewhat, in eachcase, the component is completely surrounded bythe protective potting compound. The terms pottingand encapsulation are often used generically todescribe the complete covering of an electroniccomponent with a potting compound via any of thethree methods.Master Bond Inc. Tel: 1 (201) 343-8983 www.masterbond.com whitepaper@masterbond.com2
Variety of potting formulations to suitdiverse application needsA critical part of choosing the right product is prioritizingthe requirements and realizing that tradeoffs are associatedwith choosing a material. That is to say, a balance mustbe developed between the final properties with handlingand processing issues such as open time, viscosity, cureschedule, and other factors.Epoxies are the most commonly used material for pottingand encapsulation, due to their wide range of propertiesand unmatched versatility. Epoxies offer exceptionalchemical resistance, excellent physical properties, andstrong adhesion to metals, most plastics, ceramics, andcomposites — materials commonly used for pottinghousings. They typically have superior dielectric propertiesand are normally thermally insulative, but can be madethermally conductive and electrically insulative whenneeded. They can also be formulated to withstandthermal cycling, stresses, and shocks while retaining theirexcellent dielectric properties. Although epoxies are usuallyconsidered to be rigid and permanent in nature, they canbe made more flexible when required, with some gradesexhibiting enough flexibility to allow for possible retrievalof a component. However, when epoxies are formulated tobe more flexible, chemical and temperature resistance areinvariably compromised.Epoxies can be engineered for use in potting applicationsthat call for very specific characteristics, such as opticalclarity, flame retardancy, thermal conductivity, or lowoutgassing properties, while retaining their electricalisolation capabilities. Specially formulated flame resistantepoxies that are certified to meet UL 94V-0 specificationsare self-extinguishing and offer superior electrical insulationproperties, making them ideal for potting power supplies,signal transformers, and other high power electronicdevices.withstand repeated temperature excursions above the glasstransition temperature (Tg), a particular grade should notbe ruled out for applications that involve only shorter dwelltimes at higher temperatures. For instance, an epoxy witha Tg of 150 C can easily withstand repeated excursions ofmany hours above 200 C, depending upon the nuances ofthe application.Epoxies are commonly used with fillers to lower shrinkage,enhance dimensional stability and improve abrasionresistance. The use of fillers is the critical factor forobtaining thermal conductivity while retaining electricalresistance. Through careful selection of chemistry,additives, and fillers, formulators are able to develop epoxycompounds with properties that are tailored to addressmost application needs.Silicones offer an unparalleled combination of hightemperature resistance (up to 400 F), superb electricalproperties, and flexibility, but sometimes require the useof primers to improve adhesion. They are often selectedfor their unmatched ability to resist thermal shock andrepeated thermal cycling. Softer than epoxies, siliconesexert less stress on sensitive electronics and also makeit possible to retrieve components that need repair orremoval. The properties of silicones can be adjustedthrough the addition of fillers, such as those used toachieve thermal conductivity and flame retardancy.UV curable potting compounds have a unique chemistrythat allows for ultra fast curing, normally under a minute.These materials cure through exposure to a UV light source.The thinner the layer, the faster the rate of cure. If the areabeing potted contains shadowed out portions, a secondarycuring mechanism, often utilizing heat, is required. Thesecondary cure temperature ranges from 80 C to 125 C forup to 30 minutes. This system is called a dual cure UV.The unparalleled versatility of epoxies is exemplifiedby their wide service temperature range. Some gradescan withstand cryogenic conditions while others resisttemperatures up to 500 F. However, unique B-stage epoxycompounds offer high temperature resistance and are moreflexible than typical high heat resistant epoxies. Normally,epoxies that resist higher temperatures are rigid. They canwithstand rigorous thermal cycling and thermal shock, butrequire more involved processing in order to realize theirspecial properties. For example, they must be converted toliquid from solid state. Most importantly, B-stage materialshave lower exotherm than typical one part epoxies, and aresuitable for larger castings. Fillers can be added to achieveother performance properties such as thermal conductivityand enhanced dimensional stability.Epoxies are clearly the best choice when chemicalresistance, good physical strength and first-rate electricalinsulation properties are required. Because epoxies canThermally conductive, electrically insulative epoxypotting compound provides superior heat dissipationproperties.Master Bond Inc. Tel: 1 (201) 343-8983 www.masterbond.com whitepaper@masterbond.com3
Both UV and their dual cure counterparts can cure rigidor flexible. They have good electrical insulation propertiesand are optically clear. However, fillers cannot be added tothese kinds of systems and their usage is limited by depthof cure, rarely exceeding ¼ inch. Invariably, they are usedselectively in special small encapsulating applications.Thermal and geometric factors impactprocessingTo ensure the optimum level of protection and avoidharming delicate components, care must be taken whenapplying and curing potting compounds. Some materialsrequire surface preparation and primers in order to achievegood adhesion. During application, the liquid pottingmaterial must flow easily so that it completely covers thecomponent, leaving no voids. If air becomes trapped in thehousing, the moisture it contains may cause corrosion —eventually leading to component or product failure.Removing air bubbles is very important. There are twotechniques that are commonly used: vacuum degassingor centrifuging. It is possible to degas either after thematerial is mixed or after it is applied. The best techniquefor vacuum degassing is referred to as “bumping” whichis alternately pulling and relaxing a vacuum in 30 to 60second cycles. Centrifuging is very straightforward. Themixed material is placed in the centrifuge and spun for 10to 15 minutes at 500 to 1000 rpm.These techniques may not be necessary for pottingcompounds with very low viscosity, since air bubbles maybe negligible. However, in certain pottings, higher viscositysystems are more desirable due to geometry or designissues, so vacuum degassing or centrifuging remains acritical processing step.take place. With deeper castings, more heat is generated,and the reaction goes even faster. Because most pottingcompounds do not dissipate heat, faster reactions resultin higher internal temperatures — which can damage heatsensitive components. This is why depth of cure is such animportant consideration in potting applications.Potting compounds have relatively low shrinkage as theytransition from a liquid state to a solid during cure. Filledpotting compounds exhibit the least amount of shrinkage,since only the polymer compound — and not the filler —shrinks during cure. In general, faster processing is notnecessarily better for potting and encapsulation becausefaster reactions result in more exotherm, higher shrinkage,and less open time. Faster curing compounds often cannotbe cast more than ¼ to ½ inch thick because they get toohot. Other than adding fillers, one can reduce shrinkage bymodifying the chemical formula to reduce exotherm, or byadjusting the design.Curing characteristics are of paramountimportance to successful pottingMost epoxy and silicone potting compounds are two-partsystems (resin and hardener). They take 24 to 48 hours orlonger to cure, although the cures can be accelerated byadding heat. One part, no-mix systems can also be usedfor potting although their use is limited because theircuring temperatures are typically 125 C to 150 C. Thesetemperatures can damage electronic components. One partepoxies are very exothermic and this can induce thermaldamage as well. The B-staged potting materials are theexception. While they have unique and very attractiveproperties, the processing is slightly cumbersome becausethey must be converted from a solid to liquid to use.One popular method of eliminating degassing orcentrifuging is to package the compound as a premixedand frozen system. These epoxies are mixed andcentrifuged prior to freezing. They are typically packagedin small syringes (3 to 10 cc’s) and shipped in dry ice. Thestorage temperature is -40 C. Premixed and frozen epoxiesare normally used in very small potting and encapsulationapplications where ultra precise dispensing is needed.Electronics are becoming smaller. As such, the use ofpremixed and frozen epoxies are becoming increasinglypopular. In fact, special dispensers are now availableallowing for fractions of a gram to be used in anencapsulation.The geometry of the unit and its housing are also importantconsiderations when applying potting compounds. Pottingcompounds cure exothermically; that is, they give off heatas the chemical reactions that link their polymer chainsFigure 1: Proper application of potting compoundsextends the functional life of electronic componentsand PCBs.Master Bond Inc. Tel: 1 (201) 343-8983 www.masterbond.com whitepaper@masterbond.com4
Reviewing product selection methodologyTo summarize, the performance requirement profile of thesystem is paramount. If chemical resistance is required,an epoxy is the way to go. If thermal cycling and thermalshock, along with high temperature resistance are needed,then silicones are the system of choice. With eachmaterial, the importance of electrical properties cannotbe overemphasized. Measurements of dielectric strength,dielectric constant, volume resistivity and the dissipationfactor are often critical in selecting the best material.Other factors that must be considered are the servicetemperature range, low outgassing requirements, opticalclarity, thermal conductivity, flame retardancy, andbiocompatibility, among other factors.Other major factors are product handling issues, includingopen time, viscosity, and flow properties. Ultimately theselection is based first and foremost on the overridingperformance requirements involved.Selecting a potting compound that addresses all the needsof a specific application without harming the electronicscan be quite complicated. The art of choosing a pottingmaterial depends on both properties and handling, andany design should strike a balance — achieving suitableprotection without using excessive potting material.Formulators are well equipped to advise on the optimalchoice of potting compound for a given situation.Potting compounds broaden the scope ofapplication environmentsCompeting demands for higher performance, lower unitcosts, and enhanced product reliability are compellingdesigners to view potting and encapsulation compounds asessential ingredients in electronic systems and devices. Bycushioning delicate components and protecting them fromextreme temperatures, potting compounds make it possiblefor electronics to withstand harsh manufacturing processesand operate reliably in hostile — even abusive — settings.Through careful selection of an appropriate compound,electronics manufacturers can ensure their productsoperate as designed in ever more challenging conditions.Because of the miniaturization of electronics andcomponents becoming smaller, the dispensing of pottingand encapsulation materials through the use of premixedand frozen syringes is becoming increasingly widespread.Most significantly, the B staged epoxy, with its unique blendof properties, is often a new and vibrant approach appliedto many difficult applications.For further information on this article, for answers to anyadhesives applications questions, or for information on anyMaster Bond products, please contact our technical expertsat Tel: 1 (201) 343-8983.Master Bond Inc. Tel: 1 (201) 343-8983 www.masterbond.com whitepaper@masterbond.com5
potting, in which the device is placed in a "pot", or case, and a liquid potting compound is poured into the case until it is filled to the brim. The case is left intact, becoming part of the finished unit. Casting is similar to potting, except that instead of a case, a mold is used and is removed after the compound hardens.