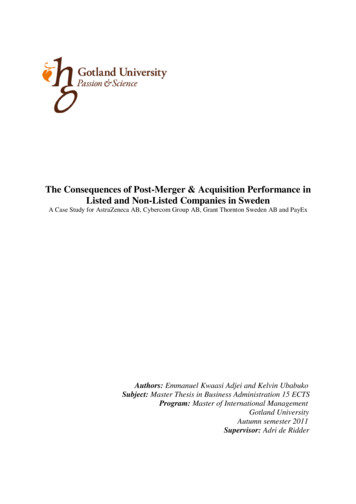
Transcription
DEGREE PROJECT INSTRUCTURAL ENGINEERING AND BRIDGESSECOND LEVELSTOCKHOLM, SWEDEN 2014Development of a Bridge SteelEdge Beam DesignFE Modelling for a Vehicle Collision andCase StudyDIEGO RAMOS SANGRÓSKTH ROYAL INSTITUTE OF TECHNOLOGYSCHOOL OF ARCHITECTURE AND THE BUILT ENVIRONMENT
Development of a Bridge SteelEdge Beam DesignFE Modelling for a Vehicle Collision andCase StudyDIEGO RAMOS SANGRÓSMaster of Science ThesisStockholm, Sweden 2015
TRITA-BKN. Master Thesis 465, 2015ISSN 1103-4297ISRN KTH/BKN/EX--465--SE Diego Ramos, 2015Royal Institute of Technology (KTH)Department of Civil and Architectural EngineeringDivision of Structural Engineering and BridgesKTH School of ABESE-100 44 StockholmSWEDEN
AbstractThe degradation of bridge edge beam systems in Sweden entailed the study of new alternativedesigns, which may become more optimal from a life-cycle perspective than the currenttypical solution used (concrete integrated). Subsequently, a U-shaped steel edge beamproposed by the consulting engineering group Ramböll was considered by the SwedishTransport Administration for its use in a real bridge project. This thesis follows theimplementation of this alternative in a bridge project.The goals of the thesis are to study the development of the U-shaped steel edge beam solutionin the case study, and to identify the key factors behind it. The case study consists of a roadframe bridge where a heavily damaged bridge edge beam system is going to be replaced.For the structural design of the solution, a static linear analysis of a vehicle collision has beencarried out with the help of Finite Element Modelling and current codes. The report shows themodelling of the design solution throughout different development phases in the project. Thecommercial software used has been LUSAS.As an outcome of the project, four models have been designed and analysed, two of themdeveloped by the author as proposed solutions. The factors behind the different changes in thedesign have been identified as: (1) structural resistance, (2) constructability and (3) the use ofstainless steel. Moreover, the connection between the steel edge beam and the concrete slabhas been the main critical part for the structural resistance. Finally, the current preliminarymodel at the moment this thesis is written, which was proposed in the project meetings, meetsthe requirements from a structural point of view.Keywords: steel edge beam, collision analysis, edge beam development, bridge edge beamsystem, finite element modeling.i
PrefaceI would like to express my sincere gratitude to José Javier Veganzones for his supervisionduring the thesis and especially for his advice during the writing process of this report.Moreover, I would like to give thanks to Håkan Sundquist for their wise guidance and helpand Ramböll engineers (Ulf Nilsson and Jukka Ikäheimonen) for their valuable time and forallowing me to participle in the project.Stockholm, June 2015Diego Ramos Sangrósiii
ContentsAbstract . iPreface . iii12Introduction. 11.1General background . 11.2Aim and scope . 31.3Methodology . 41.4Assumption and limitations . 5Bridge edge beam system . 72.1Definition. 72.2Types of Bridge Edge Beam System . 82.32.2.1According to de-watering or drainage criteria . 82.2.2According to design . 92.2.3According to the material . 102.2.4According to railing/barrier system. 10The project “Optimala Kantbalkssystem” . 112.3.12.4Types of safety barriers (railing system) . 142.5Problematic with BEBS. 152.5.13U-shaped steel edge beam . 12Common countermeasures . 16Collision analysis . 173.1Current regulations . 173.2Load Definition . 193.33.2.1Load case 1: Eurocode . 193.2.2Load case 2: Vertical post failure . 20Resistance verification . 243.3.1Footplate bolts . 243.3.2Anchorage bolt . 28v
43.3.3Railing . 293.3.4Deck slab . 293.3.5U-shaped steel edge beam . 293.3.6Stiffeners . 30Case study and design solutions . 334.1Bridge description . 334.1.156BEBS . 374.2Installation . 384.3Design of the BEBS . 394.3.1Model 1: Basic design . 394.3.2Model 2: Steel optimization designs . 424.3.3Model 3: Reinforcement plates . 45Finite Element Model . 495.1General geometry . 495.2BEBS elements . 505.2.1U-Shaped Edge Beam . 505.2.2Footplates . 545.2.3Parapet system . 565.2.4Bolts . 575.3Connections . 585.4Supports . 595.5Loads . 595.6Material . 605.7Thickness . 605.8Quality assurance . 625.8.1Comparison with hand calculations . 625.8.2Convergence analysis . 625.8.3Peak stresses points . 63Results . 656.16.2Hand calculations . 656.1.1Footplate bolts . 656.1.2Anchorage . 666.1.3Stiffeners . 66Design models . 67vi
76.2.1Model: 1 Basic Design . 696.2.2Model 2 . 746.2.3Model 3 . 766.2.4Convergence Analysis . 846.2.5Comparison with FEM . 876.2.6Deck slab . 88Conclusions . 917.1General conclusions . 917.2Further recommended studies . 94Bibliography . 95ABProcess in the design . 97A.1Pre-model . 97A.2First prototype model (Model 0.1) . 98A.3Second prototype model (Model 0.2) . 101A.4Meeting and Bar model (Model 0.3) . 105A.5Load and Moment (back calculation) . 108A.6With and without railing (Model 0.4) . 110A.72nd Group project meeting (Model 0.5) . 114A.81st Personal meeting in Ramböll . 123A.93rd Group project meeting . 128Hand calculations. 131B.1Footplate bolts . 131B.2Anchorage bolts . 134B.3Stiffeners (plate buckling) . 137B.4Stiffeners (column buckling) . 140B.5Comparison hand calculation . 143vii
AbbreviationsBEBSBridge Edge Beam SystemLCCALife Cycle Cost AnalysisFEMFinite Element ModellingKTHKungliga Tekniska Högskolan (Royal Institute of Technology)TRVFSTrafikverkets Författningssamling (Swedish Traffic EnvironmentAuthority)QTS8Quadrilateral Thick Shell with 8 nodesHX20Hexahedral with 20 nodes and quadratic interpolationBMI313D thick beam, with 3 nodes plus and extra node used for definingthe local plane XY.viii
NotationsRoman upper case lettersA Gross cross-sectional areaAeff Effective areaAs Stress area of the bolts, as the shear plane cuts through unthreaded bolt shank is the grossareaAshear Area necessary for carry the shearE Modulus of elasticity (MPa)Ec EccentricityFd Design Load for the collision analysisFt,Ed Tension force in the designFv,Ed Shear force in the designIy.eff Second area moment of inertia of the effective area in the y-axisIz.eff Second area moment of inertia of the effective area in the z-axisLcr Buckling lengthMd Design momentMy,Ed Maximum design value of the first order bending moment along the beam in the yaxisMz,Ed Maximum design value of the first order bending moment along the beam in the zaxisWel Elastic section modulusWpl Plastic section modulusRoman lower case lettersb Wide of the platefctd Design value of concrete tensile strengthfck Characteristic strength of concreteix
fu Ultimate strengthfuk Ultimate strength in plastic analysisfuk,el Ultimate strength in elastic analysisfy Yield strengthh Height between load and base of vertical postlside Length side of the square cross section of the vertical postt Thickness of the platetb Thickness box Model 2tbp Thickness bottom reinforcement plate Model 3tc Thickness rest of the beam Model 2 and Model 3ttp Thickness top reinforcement plate Model 3tsp Thickness side reinforcement plate Model 3ts Thickness stiffeners Model 3tu Thickness U-shaped edge beam Model 1Greek lower case letters Diameter of anchorage boltγM1 Partial coefficient for global instabilityγM2 Partial coefficient for global instability.σcr Critical buckling stressσsd Design stress in the bar Poisson s ratiox
Table of figuresFigure 1: Parapet system and edge beam . 1Figure 2: Percentage distribution of 3747 damage remarks on structural members from 353(Racutanu, 2001) . 2Figure 3: Elevated edge beam (left) and Low edge beam (right) . 8Figure 4: Integrates edge beam system (left), and Not-integrated edge beam system (right) . 9Figure 5: Representative examples of BEBS type I (left), and type IV (right). . 11Figure 6: BEBS type II . 12Figure 7: BEBS type III. U-shaped steel edge beam . 13Figure 8: Safety barrier class H2 (left), and class H3 (right) . 14Figure 9: Load case 1. Fd 100 kN and Fd 200 kN. 20Figure 10: Steel behaviour with and without hardening . 21Figure 11: Load cases 2.1 and 2.2 . 23Figure 12: Load calculation . 24Figure 13: Shear resistance in a bolt (Norlin, 2014) . 25Figure 14: Tension resistance in two bolts with two thick plates (Norlin, 2014) . 26Figure 15: Circular profile. White area represents the area avoided in the calculations. 27Figure 16: U-shaped steel edge beam profile . 29Figure 17: Mellösa bridge location . 34Figure 18: Picture of the two tracks in the bridge . 34Figure 19: Drawings of the plan view of the bridge 4-306-1 . 35Figure 20: Lateral view of the bridge (Frame structure) . 36Figure 21: Edge beam (heavily damaged) of Mellösa bridge . 36Figure 22: Drawings of the BEBS (concrete integrated) . 37Figure 23: Replacement of an old existing edge beam in a cantilever bridge (grey) for a newU-shaped Steel edge beam with the anchorage bolts (green) with a cover plate (blue), therailing post and footplates (pink). . 38Figure 24: Factors behind the design development. 39Figure 25: Model 1: Basic design. Lateral view of the U-shaped beam without stiffeners . 40Figure 26: Top railing (left), tubular railing (middle) and W-profile railing (right). 41Figure 27: Drawings of the U-shaped steel edge beam in Mellösa Bridge . 41Figure 28: Model 2.1: Different thickness design. Thicker thickness (green) in parts betweenstiffeners and thinner thickness (red) in the rest . 43Figure 29: Model 2.2: “The box”. Boxes and footplates (green), bolts, verticals post andrailings (pink). The line represents the W-profile railing. 44Figure 30: Solution number 3 proposed in “Optimala Kantbalkssystem” (Petterson &Sundquist, 2014). 45Figure 31: Model 3.1: Two reinforcement plates. Lateral view of the U-shaped beam withoutstiffeners . 46Figure 32: Model 3.2: Three reinforcement plates. Lateral view of the U-shaped beamwithout and with stiffeners . 47Figure 33: Frontal view of the whole model . 49Figure 34: Frontal view of the central part of the model . 50Figure 35: Model for load case 2.2 (simplified model) . 50Figure 36: U-shaped edge beam profile . 51Figure 37: Surface mesh screen in LUSAS. 52xi
Figure 38: Mesh in connection between one bolt and the top plate . 53Figure 39: Anchorage connection modelled with a volume element (blue) and spring support(green). . 53Figure 40: Stiffeners with a L-profile end. 54Figure 41: Mesh in the a footplate without the squares in contact with the bolts . 55Figure 42: Lateral view of the base of a vertical post (left) and a footplate (right) . 55Figure 43: Frontal view of the whole parapet system. Beams (pink) and supports (green). 56Figure 44: Line mesh screen in LUSAS . 56Figure 45: Four bolts (pink) with the surfaces in contact with them (green) . 57Figure 46: Connection with the footplate bolts and anchorage bolt . 58Figure 47: Sketch of the load in vertical post between top and tubular railing. 59Figure 48: Lateral view of the U-shaped beam and the thickness screen in LUSAS . 60Figure 49: Stress contour (Von Mises) in the side plate . 67Figure 50: Stress contour (Von Mises) in the top plate . 68Figure 51: Stress contour (Von Mises) in the left stiffeners and right footplate. 68Figure 52: Sketch of the volume elements in the base of the vertical post . 69Figure 53: U-profile of the Model 1 with thickness (tu). 70Figure 54: Model 2 thickness in the box tb (green) thickness in the rest tc (red) . 74Figure 55: Model 2.1 tc 4 mm, tb 25 mm Stress contour (Von Mises) in the side plate. 75Figure 56: Model 3.1 top plate thickness (ttp), side plate thickness (tsp), and U-shaped beamthickness (tc) . 77Figure 57: Model 3.1 tc 4 mm, tsp 25 mm Stresses contour (Von Mises) in the side plate(bottom face) . 77Figure 58: Model 3.1 tc 6 mm, tsp 25 mm Stresses contour (Von Mises) in the side plate(top face). . 78Figure 59: Model 3.1 Stress contour (Von Mises) top plate (left) and stiffeners (right) . 79Figure 60: Model 3.1 Contour stresses in the stiffeners. Peak stresses point in the top face(left), gentle distribution in the bottom face (right) . 80Figure 61: Model 3.2 thickness in the reinforcement plates (ttp, tsp, and tbp), U-shaped beam(tc), and stiffeners (ts) . 81Figure 62: Model 3.2 without stress transmission (3 mm not modelled) Stress contour (VonMises) .Side reinforcement plate (up), and bottom reinforcement plate (down) . 82Figure 63: Model 3.2 Stress contour (Von Mises). Stiffeners. . 82Figure 64: Model 3.2 with stress transmission (3 mm modelled).Stress contour (Von Mises).Side plate (up), and bottom plate (down) . 83Figure 65: Anchorage connection vertical view . 84Figure 66: Comparison between 5mm and 20 mm size mesh. Vertical axis, stresses (MPa)and horizontal axis, distance from the left stiffener (mm) . 85Figure 67: Comparison between 5mm and 10 mm size mesh. Vertical axis, stresses (MPa)and horizontal axis, distance from the left stiffener (mm) . 85Figure 68: Comparison between 5mm and 2.5 mm size mesh. Vertical axis, stresses (MPa)and horizontal axis, distance from the left stiffener (mm) . 86Figure 69: Comparison between 2.5 mm, 5mm, 10mm and 20mm size mesh. Vertical axis,stresses (MPa) and horizontal axis, distance from the left stiffener (mm) . 86Figure 70: Stresses in the model (left), stresses in a plate pinned in the lateral faces (right). 87Figure 71: Reaction in the bottom. Vertical axis, reaction in the contact with the concrete(kN) and horizontal axis, distance from the left stiffener (mm). 88Figure 72: Compressive stresses in the concrete slab due to the compression loads. Thepicture represents a portion of concrete 300 mm wide (horizontal axis) . 89Figure 73: Three factor involved in the solution development . 91xii
Figure 74: Evolution of the U-shaped Steel edge beam solution . 92Figure 75: Sketch of the 30 mm gap . 98Figure 76: Frontal view of the first prototype model . 99Figure 77: Frontal view of the concrete slab in the first prototype model . 99Figure 78: Frontal view of the side plate in the first prototype model . 100Figure 79: Perspective view of the beam in the first prototype model, without the top plate. 100Figure 80: Vertical view of the top plate in the first prototype model . 100Figure 81: Stress contour of the side plate (Von Mises) . 101Figure 82: Stress contour of the side plate (Von Mises) . 101Figure 83: Frontal view of the second prototype model . 102Figure 84: Double constrain equation . 103Figure 85: Stress contour of the side plate (Von Mises) . 103Figure 86: Stress contour of the side plate (Von Mises) . 104Figure 87: Old top railing profile (left) and New top railing profile (right). . 104Figure 88: Stress contour of the side plate (Von Mises) . 106Figure 89: Anchorage bolt modelled as bar (pink) and volume (blue) . 106Figure 90: Stress contour of the side plate (Von Mises) . 107Figure 91: Load height sketch . 108Figure 92: Peak point stresses created by a punctual moment (left) and a line distributedmoment (right). 109Figure 93: Model with only one vertical post (simplified) . 109Figure 94: Top plate and footplate (green), bolts and base of the post (blue), vertical post(pink) . 110Figure 95: Deformation (grey) of the vertical post (pink) . 111Figure 96: Base of the vertical post (volume) with peak point stresses in the corners . 112Figure 97: Stress contour in the top plate, without the bolts areas (white) . 113Figure 98: Beam profile after second project meeting . 114Figure 99: Model with 9 mm thickness (red) and 25 mm (green) . 118Figure 100: Model with only the "boxes" . 119Figure 101: Lateral view of the U-shaped edge beam and the pavement . 124Figure 102: Frontal view of the model with two more rows of railings . 125Figure 103: Base of the vertical post modelled with 4 volume elements (blue) . 127Figure 104: Reinforcement plate in the side of the beam . 128Figure 105: Boundary conditions in stiffeners calculation . 138Figure 106: Buckling length for a two pinned column . 140Figure 107: L-profile features . 141Figure 108: Di
DEGREE PROJECT IN STRUCTURAL ENGINEERING AND BRIDGES SECOND LEVEL STOCKHOLM, SWEDEN 2014 . 2 Bridge edge beam system . U-shaped Steel edge beam with the anchorage bolts (green) with a cover plate (blue), the railing post and footplates .