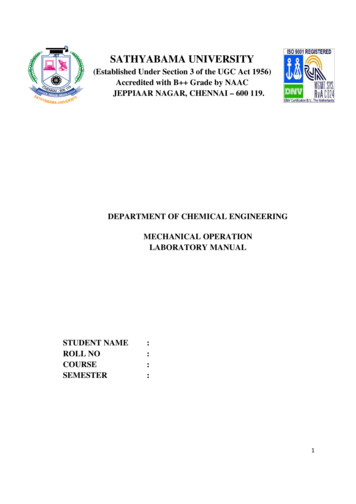
Transcription
SATHYABAMA UNIVERSITY(Established Under Section 3 of the UGC Act 1956)Accredited with B Grade by NAACJEPPIAAR NAGAR, CHENNAI – 600 119.DEPARTMENT OF CHEMICAL ENGINEERINGMECHANICAL OPERATIONLABORATORY MANUALSTUDENT NAMEROLL NOCOURSESEMESTER::::1
MECHANICAL OPERATION LAB MANUALLIST OF EXPERIMENTSCYCLE 1SL.NO.NAME OF THE EXPERIMENT1BALL MILL2JAW CRUSHER3DROP WEIGHT CRUSHER4SCREEN EFFECTIVENESS BYMECHANICAL METHOD5SCREEN EFFECTIVENESS BYMANUAL METHOD2
1. BALL MILLAIM:To determine the energy required for crushing the given feed and thus obtain the workindex for the same. Also determine the reduction ration and critical speed of the mill.THEORY:The ball mill is classified as an intermediate and fine grinder where the action of thegrinding is based on impact and attrition. The ball mill consists of a cylindrical shell slowlyturning about a horizontal axis and filled to about half its volume with a solid grindingmedium. The shell is usually steel lined with silica rock and rubber. When the mill is rotatedthe balls are picked by the mill wall and carried nearly to the top where they break contactwith the wall and fall to the bottom to be picked up again. Centrifugal force keeps the ball incontact with the wall and with each other during the upward movement.At low speeds of rotation the balls simply roll over one another and little crushing actionis obtained. At slightly higher speeds, they are projected short distances across the mill, andat still higher speeds balls are thrown greater distance and considerable wear of the lining ofthe mill takes place. At very high speeds the balls are carried right round in contact with thesides of the mill and little grinding takes place, the mill is then said to be centrifuging. Thespeed of the mill at which centrifuging occurs is called Critical speed. For efficient operationof the mill, it should always be run at a speed less than the critical speed and hencedetermination of critical mill speed becomes important.APPARATUS REQUIRED:Ball mill experimental setup, sample and sieves.PROCEDURE:1. The grinding elements are placed in the mill and the mill is allowed to run underno load condition.2. Time takes for 1 revolution of the disc in the energy meter is noted fortheoperation of ball mill under no load condition.3. Mill is stopped and about 250 grams of the sample is charge In to the ball millalong with the balls. Before feeding the sample into the mill feed size (Df) ismeasured either by volume displacement method or Feret’s method.4. The ball mill is started and allowed to run for 15 minutes.5. Time taken for 1 revolution of the disc in the energy meter is noted for theoperation of ball mill under on load condition.6. The sample after crushing is transferred to the sieves and mechanically agitatedfor 10 minutes.7. The quantity of sample retained on each sieve is weighed and tabulated as shownin the table. The screen analysis data is used to determine the mass meandiameter of the product (Dp).3
OBSERVATION:Quantity of feed sampleFeed size, DfTime taken for 1 complete revolution ( no load)Time taken for 1 complete revolution ( on load)Total time the mill is put to operationEnergy meter constants for ball mill(To be observed from the Experimental Setup) Tonesmmhrhrhr TABULATION:SL.NOMeshNo.Size ofAperture Da(mm)Mass inAverage Particlesize in each fraction eachfractionDpi (mm)(gms)MassfractionxiDp xiDpiFORMULAE REQUIRED:1)2)3)4)Energy required for crushingE [n1-n] [m x EMC] kW hr/TonesWork IndexWi [E] [1/ Dp-1 Df]Reduction ration Feed size % Product sizeCritical speed of ball millnc 1/2π[ g R-r]4
Wheren1 is the no. of revolutions of the energy meter disc during the mill operation under on loadcondition.n is the no. of revolution of the energy meter disc during the mill operation under no loadcondition.m is mass of sample in tones.EMC is Energy meter constant.Dp is mass mean diameter of the product sample in mmDf is the diameter of the feed sample in mmg is acceleration due to gravity in m/sec2R is radius of the Ball mill in m (25 x 10-2m)r is the radius of the ball in m (4.125 x 10-2m)RESULT:Using the Ball mill experimental setup the following were determined1)Energy required for crushing k W hr/Ton2)Work index kW hr mm/Ton3)Reduction ratio 4)Critical speed of the ball mill rps5
JAW CRUSHERAIM:To determine the crushing law constants using Blake jaw crusher Experimental setup.THEORY:Crushers are slow speed machines for coarse reductions and can break largelumps of various hard materials as in the primary and secondary reduction of rocks and ores.In a jaw crusher, the feed is admitted between the two jaws, said to form v-open at the top.One jaw is fixed and the other is movable. It makes an angle of 200- 300 with the fixed jaw.The movable jaw is driven by eccentric motor so that it applies great compressive force, largelumps caught in between the upper part of the jaw are broken then drop into the narrow spacebelow and are crushed again at the bottom of the jaw. After sufficient reduction, they dropout from the bottom of the machine.A crusher cannot be expected to perform satisfactorily unless.a) The product is removed as soon as they are of desirable size.b) Unbreakable material is kept out of the machine.c) In the reduction of low melting and high sensitive products, heat Generated in the mill isremoved.APPARATUS REQUIRED:Jaw crusher setup, screens, sample.PROCEDURE:1) Jaw crusher is started.2) Before the feed is fed into it, the time taken for one revolution of the energy meter discis noted for no load condition.3) The feed (1000 g ms) is fed now at constant and steady rate so as to avoid jamming andchoke feeding.4) When the jaw crusher is running under on load condition, time taken for one revolutionof the energy meter disc is noted.5) Also the time taken for feeding the entire material is noted.6) The crushed material is transferred to a sieve stack and mechanically agitated for 10minutes.7) The quantity of sample retained on each sieve is weighed and tabulated as shown in thetable. The screen analysis data is used to determine the volume surface mean diameter ofthe products (Dp)OBSERVATION:Quantity of feed sample TonesFeed size, Dfmm Time taken for 1 complete revolution ( no load) hrTime taken for 1 complete revolution ( on load) hrTotal time the mill is put to operation hrEnergy meter constants for ball mill(To be observed from the Experimental Setup) 6
TABULATION:SI.NO MeshNo.Size ofAperture Da(mm)AverageParticle size ineach fractionDpi (mm)Mass ineachfraction(gms)MassfractionXi/DpiFORMULAE REQUIRED:1) Energy required for crushingE [n1-n] [m x EMC] kW hr/Tones2) Volume surface mean diameter of the productDp 1 {xi/Dpi3) Work IndexWi [E] [1/ Dp-1/ Df]4) Rittinger’s constantKR fc [E] [1/Dp-1/Dr]5) Kick’s ConstantKKfc [E] 1n(Df/Dp]Wheren1 is the no. of revolutions of the energy meter disc during the mill operation under on loadcondition.n is the no. of revolution of the energy meter disc during the mill operation under no loadcondition.m is mass of sample in tones.EMC is Energy meter constant.Dp is mass mean diameter of the product sample in mmDf is the diameter of the feed sample in mmRESULT:The crushing law constants are determinedI.Wi II.KRfc III. Kkfc 7
3. DROP WEIGHT CRUSHERAIM:To determine the crushing law of constants using drop weight crusher.APPARATUS REQUIRED:Drop weight crusher set up, sieves, samples etc.PROCEDURE:1. About 25 grams of the sample size 4 5 is taken in the crusing chamber.2. The weight of the metallic block (weight to be dropped) and the height through whichit falls is determined.3. The block is kept in position and the plunger is placed on the top to the feed.4. The weight Is allowed to drop on the plunger. The sample in the chamber is reshuffledafter every 5 drops, so that the lower layers are also exposed to the impact.5. The product is analyzed after 100 drops using he standard set of screens.6. The crushed material is transferred to a sieve stack and mechanically agitated for 10minutes.7. The quantity of samples retained on each sieve is weighed and tabulation as shown inthe table. The screen analysis data is used to determine the volume mean diameter of theproduct (Dp)OBSERVATIONQuantity of feed sample TonesFeed size, Dfmm Height through which weight falls, h mWeight of the drop, w TonesNo.of Drops, n TABULATION:SL.NOMeshNo.Size ofApertureDa (mm)AverageDpi3Particle sizein eachfraction Dpi(mm)Mass ineachfraction(gms)MassFraction(Xi)xi/Dpi8
FORMULAE REQUIRED:1) Energy required for crushingE [nwgh] [m] kW hr/Ton2) Volume surface mean diameter of the productDp [1 xi/Dpi3]1/33) Work Index[Bond’s law constant)Wi [E] [1/ Dp-1/ Df]4) Rittinger’s constantKR fc [E] [1/Dp-1/Df]5) Kick’s ConstantKKfc [E] 1n(Df/Dp)RESULT:The crushing law constants are determinedWi KRfc Kkfc 9
4. SCREEN EFFECTIVENESS BY MECHCANICAL METHODAIM:To determine the percentage effectiveness of the given screen by mechanical Agitation ofthe Screen stack.THORY:Screen is a method of separating particles according to size alone. In practice, the solidsare dropped or thrown into a screening surface. The undersize or fines pass through thescreen opening. Materials passed through a series of screens of different sizes are separatedinto two fractions. In most screen, the particles drop through the opening by gravity, coarseparticle drop easily through the large opening in a stationary surface whereas with fineparticles the screen surface must be agitated in same way.PROCEDURE:1) Arrange a set of standard screens serially in a stack with the smallest mesh at the bottomand the largest at the top.2) Place the pan at the bottom3) After placing (500gms) the sample, shake mechanically to obtain the oversize andundersize separately.4) After shaking, weigh the particle from each mesh individually. Keep the pocketsseparately.5) Place oversize particles, shake mechanically to obtain the oversize separately.6) Place undersize particles, shake mechanically to obtain the undersize separately.Convert the weight into the mass fraction.CALCULATIONS:Total feed taken Feed fraction acc. Given mesh screen Xf Fraction of over size XD Fraction of under size flow xB (XF-XB) x (XD-XF) x XD(1-XB)E (XD-XB)2 x XF(1-XF)10
TABULATION:Mesh No. Aper.Sizewt . of sampleFeedO.SDiff. analysisU.SFeedO.SU.SCumm. MassfractionFeedO.SU.SA graph has to be drawn between cum. Mass fraction & Mesh No.RESULT:The percentage effectiveness of the given screen is %11
MECHANICAL OPERATION LAB MANUALLIST OF EXPERIMENTSCYCLE 2SLNO.NAME OF THE EXPERIMENT1BATCH SEDIMENTATION2COMPARISON – SCREENEFFECTIVENESS34PLATE AND FRAME PRESSVACCUM LEAF FILTER12
1.BATCH SEDIMENTATIONAIM:To determine the minimum area of a continuous thickener required to concentrate a feedof 4% calcium carbonate slurry at a rate of 150 tons/day solids to give an underflowconcentration of 50% by carrying out the batch sedimentation.THEORY:Sedimentation is a separation process by which dilute slurry is divided into a clear liquidand a slurry of high solid concentration by settling. When the particles are at sufficientdistance from the boundaries of the container and from other particles, so that it falls withoutbeing affected, then it is called “free settling”.For low Reynolds’s number the drag force on the particle obeys Stock’s law. The law isvalid at low velocities when the particles move through the fluid. In the gravitation settling‘g’ is constant and drag increase with velocity called the terminal velocity. The mechanismshows newly prepared slurry having uniform concentration throughout the cylinder. As theprocess begins, the particles start setting. Different zones of varying concentration areformed. Zone ‘d’ consists of heavier faster setting particles, Zone ‘C’ is called the transitionlayer consisting of variable size distribution and non uniform concentration. The layerspresent are channels through which fluid rises upward and particles settle down. At thisstage. The solid present in these layers split out into the clear zone.APPARATUS REQUIRED:One liter glass measuring jar, Calcium carbonate, Stirrer, scale etc.PROCEDURE:1.2.3.4.Prepare a 4% calcium carbonate slurry by taking 40 grams of dry sample into a beaker.Add a minimum amount of water and transfer the contents to a graduated cylinder.Make up the level by adding water up to the mark.Stir the slurry vigorously and constantly in a vertical manner until the concentration isuniform throughout the cylinder.5. Takeout the stirrer and start the stop clock.6. Note down the time for each centimeter traveled by the particles.7. Measure the height by using a scale fixed to the side of cylinder.8. For about half the length, note the time for every one centimeter.9. After that not down the time for every 0.5 cm drop in the height of the bed.10. Stop the experiment.13
OBSERVATION:Initial height of the interfaceInitial solid concentrationS.No Volume of clear liquid(ml)cmkg/m3Time taken forsetting (sec)Height (cm)FORMULAE REQUIRED:1. Slurry concentration at time ‘t’, C [OA/OT]C02. Settling velocity is obtain by drawing slopes to the curve obtained asshown in the graph below.3.Amin Qu(I/C – I/Cu)maxWherec- Concentration of slurry at any time ‘t’ (kg/m3)C0 – Initial slurry concentration (kg/m3)Cu –Underflow concentration (kg/m3)u- Settling velocity of particlesQ- Feed rate (kg/sec)14
MODEL GRAPH:AU dz / dtZCMT secTABULATION:S.NoTime secHeight ofInterface lingUVelocity 1/C – 1/Cu(u)RESULT:The minimum area of the thickener is m2.15
2. COMPARISON OF SCREEN EFFECTIVENESS BY MANUAL &MECHANICAL METHODAIM:To compare the percentage effectiveness of the give screen stack by Mechanical andManual Agitation.THEORY:Screening is a method of separating particles according to size alone. In practice, thesolids are dropped or thrown into a screening
mechanical operation lab manual list of experiments cycle 1 sl. no. name of the experiment 1 ball mill 2 jaw crusher 3 drop weight crusher 4 screen effectiveness by mechanical method 5 screen effectiveness by manual method