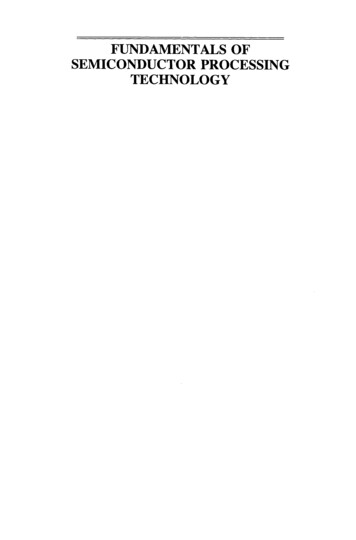
Transcription
FUNDAMENTALS OFSEMICONDUCTOR PROCESSINGTECHNOLOGY
FUNDAMENTALS OFSEMICONDUCTOR PROCESSINGTECHNOLOGYbyBadih EI-KarehIBM CorporationGraphics and Layout: Richard J. BombardSPRINGER SCIENCE BUSINESS MEDIA, LLC
ISBN 978-1-4613-5927-2ISBN 978-1-4615-2209-6 (eBook)DOI 10.10071978-1-4615-2209-6Library of Congress Cataloging-in-Publication DataCIPCopyright1995 Springer Science Business Media New YorkOriginally published by Kluwer Academic Publishers in 1995Softcover reprint of the hardcover 1st edition 1995 All rights reserved. No part of this publication may be reproduced, stored ina retrieval system or transmitted in any form or by any means, mechanical,photo-copying, recording, or otherwise, without the prior written permission ofthe publisher, Springer Science Business Media, LLC.Printed on acidjree paper.
Contents1 Semiconductor Crystals1.1 Crystals and Crystallographic Orientations1.2 The Silicon Crystal1.2.1 Crystal Growth1.2.2 Crystal Doping1.2.3 Defects in Silicon Crystals1.3 Wafer Preparation1.3.1 Wafer Type and Orientation1.3.2 Axial and Radial Variations1.4 Compound Semiconductors1.4.1 Crystal Growth1.4.2 Impurities and Crystal Doping2 Thermal Oxidation and Nitridation2.1 SiO z and SiOz-Si Interface2.1.1 Properties and Structure of Si0 22.1.2 Properties and Structure of the SiOrSiInterface2.2 Thermal Oxidation2.2.12.2.22.2.32.2.42.2.52.2.6Oxidation ReactionsOxidation KineticsInitial Oxidation StageOxidation SystemsSecond-Order Effects in Oxidation KineticsEffects of Oxidation on Silicon126812152325262731333940404244454651546067
vi2.3 Silicon Nitride2.3.1 Thermal Nitridation2.3.2 Properties of Silicon Nitride2.3.3 Local Oxidation of Silicon (LOCOS)2.3.4 Composite Insulators3 Thin Film Deposition3.1 Chemical Vapor Deposition3.1.1 Epitaxy3.1.2 Polysilicon3.1.3 Selective Epitaxial Growth (SEG)3.1.4 Chemical Vapor Deposition of Silicon Dioxide3.1.5 Phospho- Boro- and Borophosphosilicate Glass3.1.6 CVD Deposition of Silicon Nitride3.1.7 Composite Dielectrics68686970758788891031081161191201213.2 Chemical-Physical Deposition Processes1233.3 Physical-Vapor Deposition1353.2.1 Photo-CVD Processes3.2.2 Plasma-Enhanced Chemical Vapor Deposition3.2.3 Electron Cyclotron Resonance Plasma Deposition3.3.1 Vacuum Evaporation3.3.2 Sputter Deposition3.3.3 Molecular Beam Epitaxy3.3.4 Ionized Cluster and Focused Ion Beam Deposition4 Lithography4.1 Optical Lithography4.1.1 Light Sources4.1.2 Photomasks4.1.3 Exposure Systems4.1.4 Review of Important Concepts in Optics4.1.5 Perfonnance of Optical Exposure Systems4.1.6 Photoresists4.1.7 Dimensional Control and 3201212
vii4.2 Resolution Enhancement Techniques4.2.1 Optical Phase-Shifting4.2.2 Off-Axis (or Oblique) illumination4.3 Electron-Beam. Lithography4.3.1 Proximity Effects4.3.2 Electron-Beam Exposure Systems4.3.3 Electron Resists4.4 X-Ray Lithography4.4.1 X-Ray Masks4.4.2 X-Ray Sources4.4.3 Imaging4.4.4 X-Ray Resists and Resolution4.5 Ion-Beam. 4.5.1 Ion-Beam Exposure4.5.2 Ion Sources4.5.3 Pattern Definition2452452465 Contamination Control and Etch2615.1 Clean Processes5.1.1 Contaminants5.1.2 Wet Cleaning5.1.2 Dry Cleaning5.2 Etching5.2.1 Wet Etching5.2.2 Dry Etching6 Ion Implantation6.1 Principle of Operation6.1.1 Ion Sources261262266270272276280353355355
viii6.1.2 Analyzer Magnet6.1.3 Acceleration Column6.1.4 Scanning System6.1.5 Target Chamber6.2 Energy Loss and Range Distribution6.2.16.2.26.2.36.2.46.2.5Energy Loss MechanismsRange DistributionDeparture from the Normal DistributionMaskingLateral Spread of Implanted Ions6.3 Crystal Damage and Dopant Activity6.3.1 ary Defects6.3.2 Knock-On Ranges6.3.3 Annealing and Secondary Defects6.3.4 Annealing and Electrical Activity7 34264677.1 Point Defects4707.2 Fick.'s Laws4737.2.1 Diffusion from a Constant Source7.2.2 Diffusion from an Instantaneous Source7.2.3 Two-Dimensional Diffusion7.3 Non-Constant Diffusivity7.3.17.3.27.3.37.3.4Effect of Electric FieldDependence of Diffusion on Surface ReactionsDiffusion of Implanted ProfilesConcentration-Dependent DifIusivity4784794804824834844914937.4 Diffusion in Polysilicon5027.5 Diffusion in Insulators5057.6 Diffusion Sources5097.7 Gettering in Silicon511
ix8 Contact and Interconnect Technology8.1 Contact Metallurgy8.1.1 The Aluminum Silicon Contact8.1.2 Contact Materials and Barriers8.2 Poly-Metal Dielectrics8.2.1 Dielectric Composition8.2.2 Planarization Techniques8.2.3 Contact Definition8.3 Metal Interconnects8.3.1 Metal Deposition8.3.2 Contact Fill and Metal Patterning5275295315355465465475505515515598.4 Inter-Level Dielectrics5658.5 M ulti- Level Metals5718.6 Reliability Considerations8.6.1 Electromigration8.6.2 Stress Migration (Creep)8.6.3 Corrosion572576579580
PrefaceThe drive toward new semiconductor technologies is intricatelyrelated to market demands for cheaper, smaller, faster, and morereliable circuits with lower power consumption. The developmentof new processing tools and technologies is aimed at optimizingone or more of these requirements. This goal can, however, onlybe achieved by a concerted effort between scientists, engineers,technicians, and operators in research, development, and manufacturing. It is therefore important that experts in specific disciplines,such as device and circuit design, understand the principle, capabilities, and limitations of tools and processing technologies. It is alsoimportant that those working on specific unit processes, such aslithography or hot processes, be familiar with other unit processesused to manufacture the product.Several excellent books have been published on the subjectof process technologies. These texts, however, cover subjects intoo much detail, or do not cover topics important to modem technologies. This book is written with the need for a "bridge" betweendifferent disciplines in mind. It is intended to present to engineersand scientists those parts of modem processing technologies thatare of greatest importance to the design and manufacture of semiconductor circuits. The material is presented with sufficient detailto understand and analyze interactions between processing andother semiconductor disciplines, such as design of devices and circuits, their electrical parameters, reliability, and yield.The book was developed from notes prepared for coursestaught at IBM and the University of Vermont. It serves as a baseon which to build an understanding of the manufacture of semiconductor products. It is written in a form to satisfy the needs ofengineers and scientists in semiconductor research, developmentand manufacturing, and to be conveniently used for a one-semestergraduate-level course in a semiconductor engineering or materialscience curriculum. The book consists of eight chapters on unitprocesses that are arranged in a conventional sequence thatreflects typical integrated process technologies. It begins with thepreparation of semiconductor crystals and continues with thermaloxidation, thin-fIlm deposition, lithography, etching, ion implant a-
xiition, diffusion, and contact and interconnect technology. The lastchapter is co-authored by 1. G. Ryan, manager of Thin Film andChemical-Mechanical Polishing Development at IBM.One of the challenges faced when writing a book on semiconductor technologies is finding satisfactory explanations toobservations reported in the literature. Semiconductor processesare based more heavily on empirical data than on prediction bysimulation of physical or chemical phenomena. This by itself,requires a thorough review and comparison of published data andobservations. It is easier to predict electrical parameters from givenhorizontal and vertical device geometries than to deflne processingconditions that result in such geometries. The reader should therefore not be surprised ·to flnd sections describing "how" a process isperformed without the accompanying "why".The author is indebted to all those who helped shaping thebook in its present form. He is very grateful to his friends and colleagues, Albert Puttlitz and Ashwin Ghatalia, for relentlesslychecking for flaws in the manuscript and making valuable suggestions. He also thanks Robert Simonton (Eaton Corporation)and Larry Larson (SEMA TECH) for spending a great deal of timewith him on ion implantation equipment. The author gratefullyacknowledges all his IBM colleagues for their invaluable inputsand discussions; Don Chesebro, Burn Lin, Tim Brunning, MikeHibbs for their inputs on advanced lithographY, Geoff Akiki forproviding information on advanced mask preparation, HansPfeiffer on electron-beam lithography, Randy Mann and RobertGefiken on silicides and metallization.The author and R. 1. Bombard are indebted to IBM andSEMATECH for their tremendous support.The book was prepared using computer facilities at IBM.B. El-Kareh, R. 1. Bombard, and 1. G. Ryan (Chap. 8), however,take full responsibility for its contents.
FUNDAMENTALS OFSEMICONDUCTOR PROCESSINGTECHNOLOGY
FUNDAMENTALS OF SEMICONDUCTOR PROCESSING TECHNOLOGY by . IBM Corporation Graphics and Layout: Richard J. Bombard SPRINGER SCIENCE BUSINESS MEDIA, LLC . ISBN 978-1-4613-5927-2 ISBN 978-1-4615-2209-6 (eBook) DOI 10.10071978-1-4615-2209-6 Library of Congress Cataloging-in-Publication Data . checking for flaws in the manuscript and making .