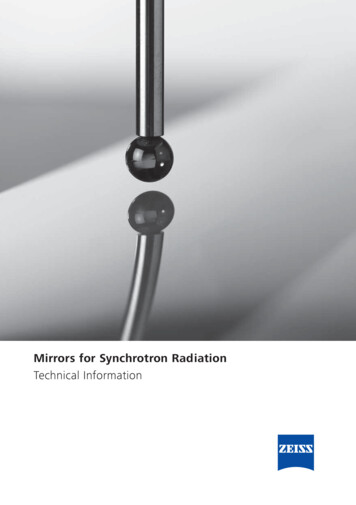
Transcription
Mirrors for Synchrotron RadiationTechnical Information
// PRECISIONMADE BY ZEISS
Making your researcheven more brilliant.Synchrotron X-ray mirrors
IntroductionArtist view of a 3rd generation synchrotron.The figure is courtesy of Synchrotron Soleil.Today, synchrotron radiation is anestablished powerful tool for many kindsof research in basic sciences and industry.The increasing interest in this type oflight source is demonstrated by a soaringnumber of large synchrotron radiationlaboratories worldwide. New generationsof synchrotron sources with enhancedperformance, such as Free ElectronLasers (FEL), open new possibilities forfundamental and applied research.4Sources with higher brilliance and superiorbeam performance put increasinglystringent demands on beamline optics.Extremely high heat load density requiressophisticated cooling and reflectiongeometries. Recently Si became the materialof choice for front end optics for its highheat conductivity, low degradation andaccessible quality. Zerodur and fused silicaare still frequently used for downstreamoptical elements where beam exposure isnot an issue. Typical requirements are slopeerrors significantly below 1” for asphericelements and below 0.1” for flats orspheres. Roughness down to the Angstromlevel helps to keep every photon in yourexperiment. Coherency considerationsdemand even harder specifications for theheight errors in the order of 1 nm rms overoptics as long as 1 m or even longer.Today, our decades of experience make usone of the leading optics manufacturers inthe world. Dedication to mirror fabricationand in particular to synchrotron optics arethe focus of our commitment. Continuousadvances in fabrication processes, metrologyand coating offer our customers state ofthe art products for superior synchrotronbeamline performance. You will later findmore details about mirror fabrication atCarl Zeiss SMT GmbH.
Reflecting X-ray OpticsGeometrical ConsiderationsReflective mirrors are most commonlyused in synchrotron radiation optics.Due to the typically extremely small grazingangles required for X-ray wavelengths, thelength-to-width ratio is usually between4:1 and 20:1 and is therefore very differentfrom the geometry of conventional optics.In addition, the tangential and sagittalradii differ by a factor of 102 to 105.In most cases the task of the optics is tofocus light from one point to another, orto focus a parallel or divergent beam to awell defined point. This can generally beachieved by using conic sections, e.g.These fundamental geometries approximateto a certain extent ellipsoidal or parabolicmirrors. In the case of cylindrical (and alsoflat) mirrors active supporting systems areoften used for in-situ changing of radiusof curvature, thus optimizing the focusingconditions within different experimentalsituations. Table 2.1 gives typical surfacegeometries supplied by ZEISS for variousoptical applications. As a rule of thumb,fabrication efforts increase from top todown with complexity. ellipsoidal or paraboloidalmirror surfaces, respectively. Dependingon the desired imaging quality, substitutionof the conic sections by more fundamentalgeometries such as spherical cylindrical, toroidal toroidal with meridionalelliptical curvaturemay be desirable.5
Reflecting X-ray OpticsGeometrical ConsiderationsClassBase idConicSectionsParaboloidEllipsoidHyperboloidPlane parabolaParaboliccylinderPlane ellipseEllipticalcylindercombinede.g. WolterfreeformfreeformTable 2.1: Range of typical surface geometries manufacturable at Carl Zeiss SMT GmbH.6
Optical Surface ErrorsTo characterize the quality of an opticalcomponent, the following categories ofspecifications are generally used:S 1 – exp (- 4π/λ sin θ σ)2, where:λ . wavelength of lightθ. angle of incidenceσ. rms roughness Tolerance of geometry parametersaccording to the experimentalrequirements and in particular to thepossibility of adjusting these parametersin compliance with the assembly. Surface figure error: This term describesthe maximum (pv: peak-to-valley) oraverage (rms: root mean square) deviationof the actual form from the ideal surface.Since the quality of the focus with grazingincidence optics is primarily determined bythe slope distribution on the surface, it ismore common to use the rms slope erroras a specification for global form accuracy. The focus spot size containing 68% ofintensity can be directly calculated fromthis specification. Microroughness: The scattering propertiesof the optical surface result mostlyfrom its microroughness. The key valuecharacterizing the microroughness isthe rms value. The total scattering S isapproximately correlated to the roughnessby the relation.7
Mirror Substrate MaterialThe material selection for synchrotronmirrors is mainly determined by thefollowing criteria: good optical machinabilitylong-term stabilityresistance to high heat loadUHV compatibilityFor components which are only used inlow intensity systems, fused silica orZerodur is generally chosen. Zerodur isa material with near-zero CTE (coefficient ofthermal expansion) at room temperature.Both materials have good machinabilityconcerning grinding, lapping and polishing,the essential optical manufacturing methods.8If high heat load has to be applied to themirrors, the bulk material needs to havebetter heat conductivity than the materialsmentioned before. In this case, metal mirrorsare used if the heat load is not too high.The materials used in these applications aremostly aluminum or copper (GlidCop) witha thin (i.e. 100 µm) electroless Ni-coating.These metal mirrors are more difficult tohandle during polishing, and according tostress phenomena the resulting accuraciesare lower in general. Well-suited for veryhigh heat loads are mirrors made frommonocrystalline silicon. This material caneven withstand undulator beam powerdensities. For applications with extremelyhigh heat loads the components can beactively cooled either internally or byexternal elements (e.g. side cooling).Table 4.1 shows a selection of commonlyused substrate materials for synchrotronmirrors. All listed materials are regularymanufactured at Carl Zeiss SMT GmbH.Contact us to discover our full capability.
MaterialProsFused SilicaZerodurULELow CTEGood machinabilityEconomically pricedsubstrate materialConsApplication areaSiliconHigh power resistantLow degradation underhigh exposureGlidCop or Cuwith NiP layerHigh thermal acceptanceSophisticated coolingdesigns realizableAl with NiP layerPopular replicationsubstrateDeformation underheat loadEasy and economicalmachinabilitySiC withpolishing layerLow CTELaborious substratemanufacturingSuperior materialstabilityFor components whichare only used in lowintensity systemsNeeds more extensivemachiningHigh heat loadapplicationSpecial coolingapplicationsTable 4.1: Range of typical substrate materials manufacturable at Carl Zeiss SMT GmbH.Other substrate materials on special request.9
Manufacturing TechniquesAs a consequence of the unique propertiesof synchrotron beams, the geometry of mostsynchrotron radiation optics is very differentfrom conventional optical components.Low vertical beam divergence leads torectangular geometries with large lengthto-width ratios. This in turn establishes theneed for specially designed manufacturingtechniques. The objective of these techniquesis the shaping of the substrate and adjustmentof the optical surface or optical axesrelative to the substrate generation of the optical surfaceshape with the desired accuracy achievement of the desiredmicroroughness and handling of the requestedsubstrate material.The direct manufacturing process generallyincludes the following steps: grinding approaches for premanufacturingof substrates and optical surface geometry etching for reducing stress and subsurfacedamage lapping for performing good thermalcontact at the side faces and foroptimizing the optical surface forsubsequent steps polishing for the complete removalof subsurface damage and figuring for the correction of residualsurface errors and finally smoothing for achieving the requiredmicroroughness.Usually the entire process consists of loopsof the individual manufacturing steps withintermediate metrology stages. The loopsare continued until the surface attains thedesired specification level. For figuring,metrology is usually integrated into afeedback loop. Thus, very close interactionbetween metrology and figuring is necessary.Depending on the type of mirror geometryand on the required accuracy, the figuringof residual errors has to be performed bysuitable tools. A summary of fabricationtools is available from ZEISS. Find outabout the wide selection of tools for themanufacturing of the optical componentfor your special needs.10
start polishingcoarsesurfaceshapingMCMMfinecorrectionCCP / IBFreductionof ripplesMM400 / IFMMM400 / IFMμ- roughnessGraph 5.1: Typical processflow of optical componentsfrom the start of polishing toachievement of specifications.MM400 / IFMNote the close interactionof figuring and metrology.IBF – Ion Beam Figuring(see chapter 6)Mμ-IFMAFMCCP – computer controlled finecorrection (6)CMM – 3D Profilometry (7)IFM – Interferometry (7)M400 – 3D Profilometry (7)spec OKμ-IFM – Microinterferometry (7)AFM – AFM analysis (7)11
Polishing and FiguringConventional polishingwith large tools, adapting the geometry ofthe substrate. This technique is applicableon plane and spherical surfaces down to 0.1 arcsec (rms), and for cylindrical andtoroidal surfaces down to about 0.2 – 0.5arcsec (rms). For other surface shapes likeparaboloids, ellipsoids etc. the residualfigure deviation can only be reduced toa value comparable to the asphericity. Forhigher form accuracy, ZEISS has developedspecial metrology and correction processes.Computer controlledfine-correction processes(CCP: Computer Controlled Polishing) Usingthese processes, form accuracies downto the order of 0.2 – 0.5 arcsec (rms) canbe achieved, even on strongly deformedaspheres. The residual errors are detectedby the high-resolution, M400 coordinatemeasuring machine or by interferometry(Interferometers: ZEISS D100 and ZYGOGPI). This surface data is used to generatecontrol data for the polishing process.Subsequently this process can removelocalized form deviations on the surfaceaccording to the accuracy of the metrology.The final achieved figure error heavilydepends on the curvature and variationof curvature.Computer controlled lapping (CCL) is the highlyablative process step for coarse figuring.Computer controlled fine correction is the finalprocess step for figure and roughness.Subsequently the processes mentioned inchapter 5 will be illustrated in more detail.Process steps consist of conventionalpolishing, computer controlled fine-correction,ion beam figuring and diamond turning.12
Gaussian IBF work functionGaussian type removal function typical of CCP or IBF.Ion Beam Figuring (IBF)is an established powerful tool for high-endfiguring of optical surfaces. Developments atZEISS lead to accuracies below 0.02 arcsec(rms) or 0.1 µrad (rms) for other geometries.The achieved results are ultimately limited bythe accuracy of the measurement technique.Diamond turningIf metal mirrors have to be machined,the surface generation can also beperformed by CNC diamond turningmachines developed at ZEISS or alsoby diamond flycutting method.13
Metrology, Testing and AnalysisZEISS offers metrology devices to coverthe entire spatial error range fromseveral nm to above 1 m: Full apertureinterferometry is best suited for planeand spherical surfaces with dimensionsbelow 12”. Thus, stitching interferometryand 3D profilometry are used whenit comes to large or complex surfaceswith high aspherical departure. For thispurpose, ZEISS offers the 3D ultrahighresolution, M400 coordinate measuringmachine. This device is able to measuresurfaces up to 550 mm with a resolution 10 nm where aspheric departure frombase geometries is almost unlimited(see example 1).InterferometryThis technique is best suited for plane andspherical surfaces. Aspherical surfacescan be tested if a component-specific nulllens is used. This lens compensates forthe wavefront aberrations resulting fromthe aspheric deformation. The measuringaccuracy for the ZEISS D100 direct measuringinterferometer is in the order l/100(l 633 nm) with resolution 1 nm.Several settings for magnification andaperture allow optimum lateral resolution.Devices up to 24” aperture are available.For larger mirrors, grazing modes allowmeasuring of the clear aperture withoutsignificant loss of precision.Interferometric metrology devices arenot strictly limited to plane or sphericalsurfaces. Cylindrical or weak freeformaspheres can be well measured byinterferometric setups. Measurementswith a plane stitching interferometer inthe sub-nm level have been successfullydemonstrated (example 2). Metrologyis completed by μ-interferometers andAFMs, covering the entire PSD fromthe nm to the m range.See the devices listed below foran overview of metrology at ZEISSdedicated to the synchrotronmirror fabrication:14A wide selection of devices and dedicatedmountings for the interferometry access of awide selection of geometries.
3D Profilometry (CMM)The figure errors of complex surfaces canbe completely evaluated by means of theM400 3D ultrahigh-resolution coordinatemeasuring machine, developed at ZEISS.This device is able to measure surfaces up to550 x 380 mm2 with a resolution 10 nm.Stitching approaches also allow qualificationof larger mirrors. Surfaces with an angularspectrum of about 40 for both axes canbe measured within one fixed set-up.The measurement data from either M400 orD100 can then be directly used as input fora computer controlled fine-polishing processor for ion beam figuring methods describedabove.In addition, for workpieces up to 1.2 mcommercial coordinate measuring machinesfrom the ZEISS Industrial Metrology businessgroup are in operation (UPMC 850 Carat).The vertical resolution of these devices isgenerally 200 nm. Within the framework ofthe manufacturing process these measuringmachines also allow highly accurate absoluteadjusting or centering of optical surfacesin relation to the substrate with absoluteaccuracies below 1 micron. For mirrors largerthan 1200 mm stitching methods are usedfor the qualification and iterative processes.Metrology volume of the high precisionM400 coordinate measurement machine.3D profilometry reveals the full picture:The figure of the optical surface withrespect to the entire substrate geometry.15
Metrology, Testing and AnalysisPSD analysis with different measurement techniques: Interferometer, microinterferometerwith different magnifications and atomic force microscopy with different scan sizes.MicrointerferometryQualification of mid spatial frequencyroughness (MSFR) or mid spatial frequencyfigure errors (MSFF) is performed bymicrointerferometry.For these microroughness errors a non-contactoptical device (e.g. ZYGO, NewView 700)is used. Height resolution of the commercialdevice is below 0.1 nm. Objectives withmagnifications of 2.5x, 10x and 50xmagnification are in use. This correspondsto spatial sampling wavelengths between0.6 μm and 5.8 mmAFM analysisDetermination of high spatial frequencyroughness (HSFR) is accessible by means ofatomic force microscopy (AFM). HSFR is anessential surface characteristic for normal16incidence X-ray optics and, depending onenergy, also for grazing incidence optics.In particular, low HSFR requirements comeinto play when the optical surface is coatedwith multilayers. At Carl Zeiss SMT GmbHa Nanosurf AFM with special designed holderis in operation. This system performs spatialsampling between a few nanometers and ninemicrons. Depth resolution is below 0.1 nm.Mirror in AFM action.
Mid-spatial frequency roughness (MSFR) detected with microinterferometry (ZYGO NewView 700).Analyzing and qualificationTogether, these measurement techniquesgive a complete description of an opticalsurface. Starting at surface wavelengths inthe order of a few nanometers, all typesof surface errors can be determined up tothe full size of the optical element.As a very powerful mathematical tool,PSD analysis (Power Spectral Density) isused at ZEISS for qualifying the completesurface over all spatial sampling frequencies.Fourier decompositions of all measurementsfrom the different types of metrologyare performed and the correspondingpower spectra are overlapped in a doublelogarithmic interpretation. The slopingproperties of such spectra give informationabout the surface behavior. Arbitrarywavelength intervals can be cut out of thespectra and according to Parseval’s theoremthe corresponding rms figure or roughnessvalue can be integrated. By analogy, the rmsslope error can be calculated for specificfrequency ranges by means of a slope-PSD.Only by these means is it possible to removefigure deviations during the manufacturingprocess and at the same time optimizeall kinds of surface roughness and finallyprovide a complete description of thefinished component to the customer.17
CoatingThe picture is courtesy of GKSS,Incoatec and Prof. Stampanoni /SLS and shows a 2 stripe coatedmirror with a Ru / C and W / Simultilayer coating mounted in themonochromator of the TOMCATbeamline at the SLS.The design of an optical coating has to beadapted to the intended field of applicationof each customer and is thus an integralpart of the complete mirror fabrication.Essentially, the coating is determined bythe photon energy and the grazing angleor angular spectrum. Synergies of thedifferent ZEISS coating laboratories andthe experience of ZEISS scientists providea broad spectrum of customer designedcoatings. In addition, special coatingscan be realized by our external partners.Table 8.1 shows the most commonly usedcoating materials. In some cases (e.g. Ru) athin binding layer (e.g. 5nm Cr) is necessaryfor reducing stress and also for maintainingthe microroughness performance.Standard MaterialsMetallic coatingAuPtRhNiPdAlAlMgF2RuOthersCSiSiO2Binding layersCrHfTable 8.1: Commonly used coating materials.All other coating materials on special request.18Mo
ExamplesExample 1: Tangential cylinder low residual slope errors low figure roughness (height error) tight radius specification full roughness specification (MSRF HSFR)FeaturesSpecification / ManufactureMaterialSi 100 Dimensions450 x 30 x 50 mm3Clear aperture385 x 5 mm2 zone 1430 x 15 mm2 zone 2PropertiesSpecificationResultsGeometrycylinder radius: 150 km R 195 kmR 170 kmSlope errortangential: zone 1: 0.25 μrad rmszone 2: 0.63 μrad rmssagittal: zone 1 2: 2.0 μrad rms0.09 μrad rms0.09 μrad rms0.41 – 0.46 μrad rmsHeight errorzone 1: 2.0 nm rmszone 2: 5.0 nm rms0.98 nm rms1.35 nm rmsSurface roughnessMSFR: 5.2 – 1000 μm 0.25 nm rmsHSFR: 0.02 – 2 μm 0.4 nm rms0.12 – 0.13 nm rms0.12 – 0.32 nm rmsresidual figure errorResults Excellent tangential slope errorsbelow 0.1 μrad for zones 1 and 2 Height error below 1 nm rms for zone 1 Roughness results superior tospecifications19
ExamplesExample 2: Paraboloid strongly aspherical shape (local curvature) sagittal pitch 3 mm on only 40 mm base variation. very small sagittal radius (50-60 mm) sagittal radius variation 25 % withinclear aperture length of 190 mm. low sagittal slope error (1.89 “)FeaturesSpecification / ManufactureMaterialZERODUR Dimensions 190 x 30 x 50 mm3Clear aperture 150 x 20 mm2Coating50 nm standard etersVertex: R 4.0 0.05 mmoff-axis: Xm 400 1 mmas specifiedSlope errormeridional: 5.0 arcsec (rms)sagittal: 1.5 arcsec (rms)1.20 arcsec (rms)1.89 arcsec (rms)Surface roughness 0.5 nm rms0.41 – 0.51 nm rmsresidual figure error20Results Geometry has been successfully fabricated Meridional slope error and roughnessfully comply with specification Very challenging sagittal slope error of1.5 arcsec has been missed by 25%
Example 3: Calibration spheresSet of 4 spheres with tight radius specifications (370 m 2%)- corresponds to 95 nm pitch over substrate length of 120 mm. challenging slope errors ( 0.5 μrad) high identicalness for radii 0.5 m- corresponds to only 6.5 nm pitch variationover substrate length of 120 mmFeaturesSpecification / ManufactureMaterialULE (premium grade)Dimensions100 x 20 x 20 mm3Clear aperture90 x 15 pherical radius: R 370 m 2 %all substrates are to have the same radius: 0.5 mRmean 368.21 mR1 368.68 mR2 368.20 mR3 368.21 mR4 367.74 mSlope error (rms)tang. slope error: 0.5 μrad (rms)G 1:G 2:G 3:G 4:Surface roughness(rms)MSFR: 1.0 nm, 10 μm λ mm0.27 – 0.33 nm, 20x0.18 – 0.21 nm, 2.5xresidual figure )(rms)(rms)Results Radius precision within 0.94 m.This corresponds to a pitchidenticalness of 10 nm. All slope errors comply with specifications.Average slope 0.29 μrad almosttwice in specification. Roughness results about 0.25 nmon average21
ExamplesExample 4: Grating Blanks extremely low residual slope errors low roughness specification (MSFR)FeaturesSpecification / ManufactureMaterialSi 100 Dimensions120 x 30 x 23 mm³Clear aperture110 x 15 Plane with:Tangential radius 30 kmSagittal radius 3 kmTangential radius 200 kmSagittal radius 200 kmSlope errorTangential: 0.1 µrad (rms)Sagittal: 0.4 µrad (rms)Tangential: 0.095 µrad (rms)Sagittal: 0.13 µrad (rms)Surface roughnessMSFR: 0.2 nm (rms)MSFR: 0.13 nm (rms)residual figure error22Results No high frequency errors leftwithin the clear aperture Below 1 nm PV height error
Example 5: Toroidal Mirror Low slope errors Tight radius specification Very high gradients due to small radiiFeaturesSpecification / ManufactureMaterialFused Silica HOQ310Dimensions200 x 30 x 30 mm³Clear aperture180 x 25 mm²Coating30 nm AuPropertiesSpecificationResultsGeometryToroidal Parameters:Tang. radius 5119 25 mmSag. radius 125 0.625 mmTang. radius 5128.7 mmSag. radius 124.4 mmSlope errorTang.: 1.5 µrad (rms)Sag.: 3.0 µrad (rms)Tang.: 1.47 µrad (rms)Sag.: 2.88 µrad (rms)Surface roughnessMSFR: 0.5 nm (rms) (50x)HSFR: 0.5 nm (rms) (1µm AFM)MSFR: 0.34 nm (rms)HSFR: 0.1 nm (rms)residual figure errorResults Geometry successfully manufactured Tight radius specification has been met23
ExamplesCarl Zeiss SMT GmbH is a reliable partner for the manufacturingof synchrotron mirrors. We have implemented powerfulmetrology and manufacturing techniques for the upcominggeneration of highest-quality optical components forsynchrotron radiation and other X-ray applications. Formaccuracies below 0.3 arcsec (1.4 µrad) (rms) have beenachieved on highly deformed aspherical components, andsurface qualities below 0.02 arcsec (0.1 µrad) (rms) areprovided for flat mirrors. Mirrors up to 1200 mm in lengthcan be produced in a wide variety of materials ranging fromthe glass ceramic Zerodur‚ to monocrystalline silicon.Any exploration of the limitations for optical tolerancesalways needs the full picture of all optical parameters andtolerances. Consideration of material choice, dimensionsand mechanical requirements leads to a serious discussionabout achievable quality.We stay tuned for future requirements: The advent of a newplane stitching interferometer enabled the fabrication andmetrology of surfaces with figure errors below 1 nm rms and0.01 arcsec (rms) slopes respectively.In special cases customer requirements may be targetedthrough collaborations in order to overcome technicalbarriers. We are always open for your ideas and suggestions.Please let us know about your projects and special challenges.If the desired component is not included in our productionrange listed above, please don’t hesitate to contact us.We will be glad to find a tailored solution to your technicalchallenge.24
AppendixAbridgement of metrologyOpticalparametersType ofmeasurementDeviceResolution Spatial sampling areaGeometry /surface qualitySurface scanningusing anopto-mechanicalprobe headZEISS M400precision coordinatemeasuring device 10 nm1 mm λ 560 mmGeometry /surface qualitySurface scanningusing anopto-mechanicalprobe headZEISS UPMC 850S-ACC Caratprecision coordinatemeasuring device 200 nm0.2 mm λ 1200 mmSurface qualityInterferometryZEISS D100direct measuringInterferometer 1 nm0.2 mm λ 1200 mmSurface qualityInterferometryZYGO 6“ with cylinder 1 nmCGH, stitching stage0.2 mm λ 1000 mmMSFRMicrointerferometry ZYGO NewView700, 1000x1000 px,(magnification 2.5x) 0.1 nm12 µm λ 5800 µmMSFRMicrointerferometry ZYGO NewView700, 1000x1000 px,(magnification 10x) 0.1 nm2.8 µm λ 1400 µmMSFRMicrointerferometry ZYGO NewView700, 1000x1000 px,(magnification 50x) 0.1 nm0.6 µm λ 290 µmHSFRAtomic forcemicroscopyNanosurf NaniteS200 AFM 0.1 nm4 nm λ 8 μmHSFRAtomic forcemicroscopyDigital Instruments, 0.1 nmDI nanoscope D3100M4 nm λ 10 μm25
AppendixAbridgement: Tolerances of optical parametersGeometriesRoughness (rms)Slope error (rms)Geometry /surface quality 0.1 nm 0.02 arcsec ( 400 mm) 0.05 arcsec(400 mm length 700 mm) 0.10 arcsec ( 700 mm)Spheres 0.1 nm 0.05”, if measurable byinterferometry 0.1” else (also depending ondimensions and curvature)Cylinders / toroids 0.2 nm 0.1“ 0.3“, depending on geometryElliptical / parabolic /hyperbolic cylinders 0.2 nm (SiO2, Zerodur), 0.3 nm (Si) 0.1“ 1“, depending on geometryOther aspheres 0.5 nm ( 0.2 nmdepending on asphericity) 0.1“ 1“, depending on geometry26
References to Carl Zeiss SMT GmbHfor Synchrotron OpticsFlatDr. Friedmar Senf, BESSY GmbH, Berlin, GermanyMr. Uwe Flechsig, Paul Scherrer Institut Swiss-Light-Source, Villingen PSI, SwitzerlandDr. Riccardo Signorato, Bruker AXS, Gladbach, GermanyDr. Daniele Cocco, LCLS, Stanford, USAMr. Peter Stefan and Dr. Michael Rowen, SSRL / SLAC Stanford Linear Accelerator Center, Stanford, USADr. Phil Heimann and Dr. Tony Warwick, Lawrence Berkeley National Laboratory, Berkeley, USADr. Marco Zangrando, ELETTRA, Trieste, ItalyLarge MirrorsDr. Friedmar Senf, BESSY GmbH, Berlin, GermanyDr. Guenther Goerigk, FZ Jülich GmbH Institut für Festkörperforschung, Jülich, GermanyDr. Kai Tiedtke, DESY GmbH, Hamburg, GermanyDr. Fank Scholze, PTB Physikalisch-Technische Bundesanstalt, Berlin, GermanyHigh CurvatureMr. Uwe Flechsig, Paul Scherrer Institut Swiss-Light-Source, Villingen PSI, SwitzerlandDr. Ray Barrett, ESRF Poly Scientifique Louis Néel, Grenoble Cedex, FranceDr. Phil Heimann and Dr. Tony Warwick, Lawrence Berkeley National Laboratory, Berkeley, USADr. Kai Tiedtke, DESY GmbH, Hamburg, GermanyDr. Friedmar Senf, BESSY GmbH, Berlin, GermanyDr. Ruben Reininger, APS, Argonne, USAAsphericalDr. Friedmar Senf, BESSY GmbH, Berlin, GermanyDr. Jens Biegert, ICFO, Castelldefels, SpainMr. Frank Hertlein, INCOATEC GmbH, Geesthacht, GermanyDr. Luca Poletto, CNR-INFM, Padova, ItalyDr. Kai Tiedtke, DESY GmbH, Hamburg, GermanyMr. Kyo Takahashi, ACCESS International Resources Ltd., Yokohama, JapanDr. Haruhiko Ohashi, JASRI, Sayo-Gun, JapanOtherDr. Peter Predehl, Max Planck Institut für Extraterrestrische Physik, Garching, GermanyMr. Frank Hertlein, INCOATEC GmbH, Geesthacht, GermanyDr. Ray Barrett, ESRF Poly Scientifique Louis Néel, Grenoble Cedex, FranceDr. Kai Tiedtke, DESY GmbH, Hamburg, GermanyDr. Stefan Moeller, SSRL / SLAC Stanford Linear Accelerator Center, Stanford, USAMr. Frank Siewert, BESSY GmbH, Berlin, GermanyDr. Simon Alcock, Diamond Light Source Ltd., Didcot, UK27
DDD-CZ-I/2016 UToPrinted in GermanyEN 11 021 0001ICarl Zeiss SMT GmbHZEISS GruppeRudolf-Eber-Straße 273447 OberkochenGermanyPhone: 49 (0) 7364 20-4300Fax: 49 (0) 7364 20-2109Email: info.smt@zeiss.comwww.zeiss.com/smt
concerning grinding, lapping and polishing, the essential optical manufacturing methods. If high heat load has to be applied to the mirrors, the bulk material needs to have better heat conductivity than the materials mentioned before. In this case, metal mirrors are used if the heat load is n