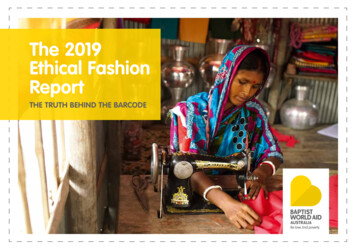
Transcription
The 2019Ethical FashionReportTHE TRUTH BEHIND THE BARCODE
THE 2019 ETHICAL FASHION REPORTTHE TRUTH BEHIND THE BARCODEDate: April 2019Project Leads: Libby Sanders, Jasmin MawsonLead Researchers: Jessica Tatzenko, Claire Hart, Annie Hollister-JonesResearcher Support: Meredith Ryland, Luke Medic, Emily TaylorBehind the Barcode is a project of Baptist World Aid Australia.New Zealand headquartered companies researched in partnershipwith Tearfund New Zealand.Front cover photo: Baptist World Aid Australiawww.behindthebarcode.org.auReport Design: Susanne GeppertInfographics (pp 10–11): Cadence Media2
CONTENTS1. Executive Summary. . . . . . . . . . . . . . . . . . . . . . . . . . . . . . . . . . . . . . . . 42. Methodology. . . . . . . . . . . . . . . . . . . . . . . . . . . . . . . . . . . . . . . . . . . . . . . . 123. Industry Influences. . . . . . . . . . . . . . . . . . . . . . . . . . . . . . . . . . . . . . . . 174. Policies. . . . . . . . . . . . . . . . . . . . . . . . . . . . . . . . . . . . . . . . . . . . . . . . . . . . . . . . . 255. Traceability and Transparency. . . . . . . . . . . . . . . . . . . . . 286. Auditing and Supplier Relationships. . . . . . . . . . . . 33Appendices7. Worker Empowerment. . . . . . . . . . . . . . . . . . . . . . . . . . . . . . . . . 37Statements from non-responsive brands 908. Environmental Management. . . . . . . . . . . . . . . . . . . . . . . 40Letter from auditor 959. Brand Index. . . . . . . . . . . . . . . . . . . . . . . . . . . . . . . . . . . . . . . . . . . . . . . . . . 4510. Survey Data. . . . . . . . . . . . . . . . . . . . . . . . . . . . . . . . . . . . . . . . . . . . . . . . . . 64Sources 96About Baptist World Aid Australia 97Acknowledgements 983
1Executive SummaryThis section outlines the research aimand scope; data collection and findings;and overall results of all companies.4
�FFDFD–D–FD FDDD D–DC–FDC FBBD C–FDA FC–FFFC–A D–D FD C C–C–C B FD–DDFA–B B CFD D–C–FB C–B–A–D FD–A C–FB–D D DFEnvironmentalmanagementDAA–FFBCA–BBFFC FFC FC–FB C–DCDDFD DFB B FB–FC–A FC FDDB A D–A–FB A–B A B A FD–D BC–A A A ACD FB–DB C–B A A–D A A FFA–C A FFAuditing andsupplierrelationshipsD–A A–FD A BA BA–FC–B FC–C D B FC C–B C–C BFA–AC A ADB FC AD A–FDFA–A CAFB AA–A–A–AFB–AB CA AB A–C C CB–C–A AA–A B C–A–A B–FABA BFTrancparency andTraceabilityD–B B–FC–AC–A–CBFD–D FC–CDCFC CC CD CFCA–DA–AC–BFC A–DC–FDFC A DC FBACB–BA FC C–C–DA ABB D B–D BD–A–B A–AB D B–B B–FA B–CCFD–AB–FCA–C A–CBFD C FD CDB–FC C–C C–CC FC B D A–A–C–BD–C A D B–FDD–BA D BD–BA–BB B AFCB–C D A AA–B CC C–BD AB A–A BC–BA C FA–B–B CFPoliciesAbercrombie & Fitch*adidasALDI StoresAlly Fashion*Anthea Crawford*APG & Co.Arcadia GroupAS ColourASICSASOSBaby City*BardotBarkers Clothing*Bec and Bridge*Ben Sherman AustraliaBest & LessBetts GroupBig WBloch*Blue IllusionBoardridersBodenBoohooBrand Collective (Apparel)Brand Collective (Footwear)Camilla and Marc*Canterbury NZCity Chic CollectiveColes*Cotton On GroupCountry Road GroupCueDavid JonesDecjuba*DesignworksEtikoEzibuyFactory XFarmers*Fast Future BrandsForever 21*Forever NewFreeset T–ShirtsFruit of the Loom*Gap Inc.Gazal*General Pants GroupGildan ActivewearGormanH&MHallenstein Glasson HoldingsHanesbrandsHot Springs*House of QuirkyHufferHugo Boss GroupHunting & Fishing NZIcebreakerInditexIndustrieJeanswestJETSJust GroupK&KKaren Walker*Kate Sylvester*KathmanduKmart AustraliaKookaiKowtowL BrandsLacosteLevi Strauss & Co.*Liminal ApparelLorna JaneLowes*Lululemon AthleticaMacpacMarks & SpencerMax*Merric Apparel NZ*OVERALL GRADEB–A A FA A A A AA FA–A FA–A A–A FA A–A A–A A FA A A–A A AA B A A AA BA–CA A AA A A A A A A A FA A A A–A A A A A A A A A A A A A A A A A A B–A A A A FEXECUTIVE SUMMARYINTRODUCTIONBaptist World Aid is pleased to deliver its sixthconsecutive report on labour rights andenvironmental management systems in thefashion industry. The 2019 Ethical FashionReport grades 130 companies from A to F,based on the strength of their systems tomitigate against the risks of forced labour, childlabour, and exploitation in their supply chains.Overall Grades: A– MExcitingly, in addition to its traditional focus onlabour rights, this year’s research also incorporatesnew environmental management metrics in theassessment criteria. In 2019, 75% of companiesassessed actively engaged in the research process,shedding light on the global fashion industry’sperformance in the arenas of labour rights andenvironmental management.For the 43 million workers in the Asia Pacific1region, and for millions of others across the world,the global fashion industry remains a significantemployer. It also spurs economic growth,generates tax revenue, provides valuable skills andtraining, and delivers crucial foreign exchange.All of these factors can, and often do, contributeto improving the lives of workers and theircommunities.At the same time, however, the fashion industryis a source of exploitation for millions.* non-responsive companies5
EXECUTIVE SUMMARYINTRODUCTIONFor the majority of workers in the fashion industry,wages are so low that it leaves them, and theirfamilies, trapped in the cycle of poverty. Beyondthis, fashion production throughout the AsiaPacific is marred by the prevalence of slavery andchild labour. In addition, whilst safety standardshave improved, fire safety, structural defects withinfactories, and unsafe working conditions remainreasons for continued concern.non-responsive companiesWorkerempowermentA FD B–DD–D–B FB–D A FD–BFC–D D–D–FD–D B–B D DD–FFC D FFC–FD–FD FD FDD FFDFC EnvironmentalmanagementA FD A B B–A AFB FA DFA FCAB–DD D BA–A C–ADFFC BFFC–FC DC–D–DFA A FFDFD Auditing andsupplierrelationshipsA DC A–A–B A–A D AC A DB–A D–CA–B A–B–BAAA CBC–FD BBFFA–FBCA–DCFAA–FFB–FC Trancparency andTraceabilityThese 130 companies represent480 brands. To check brandgrades, go to the brand indexon page 45 or online atwww.behindthebarcode.org.auB D–BA–C B–CB DB–BA DC–AFD BCBD BBB–B C–B C–FD B D FFBFC–C–B–FCFB C FFC FBPoliciesA A–A A A A A A A–A A A AA A FA A A A A AA A A A A A FAA A FFA FA A A C–AB A A FFAAAMighty Good GroupMunro Footwear GroupMyerNature BabyNew BalanceNextNikeNobody DenimNoni B GroupNudie Jeans Co.Oroton GroupOutland DenimOxfordPaganiPatagoniaPavement United Brands*Postie PumaPVH Corp.*R.M. WilliamsRalph Lauren*Retail Apparel GroupRip CurlRodd & GunnRREPPRuby ApparelSeafollySeed HeritageShowpo*Simon de Winter GroupSussan GroupSwanndri NZ3 Wise Men Ltd.*T&T Fashions*Target AustraliaThe Baby Factory*The Iconic*The PAS GroupThe Warehouse GroupTigerlily*Tree of LifeTrelise Cooper*UNIQLOVF Corp.Voyager Distributing Co.*Wish Designs*Workwear GroupWORLD*ZimmermannOVERALL GRADE* healthy. Correspondingly, it is the workers in thefashion supply chain that most acutely feel thedetrimental effects of poor environmentalmanagement. This is the first year that the EthicalFashion Report will assess companies on theirenvironmental management systems, alongsidetheir labour rights management systems, inconsideration of their final grade.A DB–A–BB–B–A–DB C A DC–AFCBC B–C–C B A–ACBC–FD BC FFBFC C–B–D–CFB BFFCD–B–Overall Grades: M– ZFor six years, this research has assessedcompanies across the globe on the strength oftheir labour rights management systems. In the2018 Ethical Fashion Report, we acknowledgedthat a “truly ethical” company not only ensuresthat its supply chain empowers workers and paysthem a living wage, it also understands its impacton the environment and manages its footprint tokeep waterways, the earth, and the atmosphere6
EXECUTIVE SUMMARYINDUSTRY PROGRESS Solidarity Center via https://flic.kr/p/LcxknwThe annual nature of this research enables us to track theprogress in ethical sourcing, made by the fashion industry.Since last year, improvements have been made across theindustry in 79% of the areas assessed. Most noteworthyareas of improvement in 2019 are:Gender inequality 61% of companies (an increase of22%) have created policies addressing gender inequalityin their supply chain, including the introduction ofstrategies addressing discrimination faced by women.Responsible purchasing practices 45% of companies(an increase of 18%) have introduced policies addressingresponsible purchasing practices, with an aim to improveworking conditions.Child and forced labour 35% of companies (an increaseof 17%) have robust remediation plans to redress child orforced labour if it is found in their supply chain.Manufacturing Restrictive Substance List (MRSL)35% of companies (an increase of 14%) have acomprehensive MRSL that they test against to ensureworkers are not exposed to hazardous chemicals withdire environmental impacts.An important part of the annual reporting process isto give companies the opportunity to report on theimprovements they have made, which encouragescontinual improvement across the industry. Of thecompanies that were assessed by both the 2018 and2019 Ethical Fashion Reports, 38% improved their overallgrade. The area showing the highest improvement in2019 is Auditing and Supplier Relationships, followedby Environmental Management (which was assessedin 2018, but not included in the grading until 2019).Workers with Bangladesh Independent Garment Workers Union.7
EXECUTIVE SUMMARYINDUSTRY CHALLENGESDespite the significant progress we’veseen across the industry in the last sixyears, serious concerns remain thatneed addressing.TraceabilityA company’s investment in traceability and itsknowledge of suppliers remains a key pillar ofa strong labour rights management system.If companies don’t know (or don’t care) whotheir suppliers are, then there’s virtually no wayof ensuring that the workers who make theirproducts aren’t being exploited. It is encouragingthen, that this continues to be one of the mostsignificant areas of improvement for the industry— since Baptist World Aid began publishing thisresearch in 2013, there has been a 32% increase incompanies who are tracing their inputs suppliersand a 31% increase in companies who are tracingtheir raw materials supplier.Notwithstanding these improvements, traceabilityremains a significant challenge across the industry.While 69% of companies could demonstratetracing all final stage suppliers, only 18% havetraced all inputs suppliers, and just 8% have tracedall raw material suppliers. Although the majority ofcompanies have begun tracing suppliers at thesedeeper stages of their supply chain, it is evidentthat many still have no knowledge of where theirinputs and raw materials are being sourced. Withless visibility, comes greater risk. The prominenceof forced and child labour is well documented atthese earlier stages of production.2TransparencyInvestment in transparency demonstrates acompany’s willingness to be accountable toconsumers, civil society, and workers; and makesit easier for these groups to collaborate to ensurethat the rights of workers are upheld. There aremany examples of corporate transparency aroundsupply chain practices, but one of the mostsignificant examples would be the publicationof a list of suppliers, that includes supplierbusiness names and addresses. The 2019 EthicalFashion Report has found that 37% of companieshave published a complete list of all final stagesuppliers, increasing to 50% when includingcompanies that have published information aboutat least some suppliers.Despite the percentage of companies publishingfull supplier lists having more than doubled sincewe began this research in 2013, transparencyremains an ongoing challenge in the industry. Lowtransparency is one of the biggest determinantsfor the receipt of a low grade, because companiesare graded based on a combination of publiclyavailable information and any information they arewilling to disclose to our researchers.As mentioned previously, 75% of companies choseto engage with the research process this year, withmost companies seeing value in the process ofbeing benchmarked and gaining feedback.Several companies with no publicly availableinformation regarding their ethical sourcingpractices have chosen not to engage with theresearch process, and so receive F grades in the2019 Ethical Fashion Report. Without makinginformation known, it becomes impossible forthe public to know if these companies are doinganything to combat exploitation in their supplychains. A number of companies in this Report werenon-responsive, but still scored reasonable grades,as high as a B, due to the amount of publiclyavailable information they published. For moreinformation about the research process and nonresponsive companies, refer to the methodology(page 12). Non-responsive companies were alsogiven the opportunity to provide a statementabout why they chose not to engage with thisresearch. These statements are included onpage 90.But transparency is no longer an expectation onlydriven by consumers, this expectation has alsobeen legislated in a number of countries. The USA,France, the UK, and, now, Australia (through theintroduction of a Commonwealth Modern SlaveryAct) all require companies to publish details of thesystems they have in place to ensure that workersaren’t being enslaved. You can read more aboutthe introduction of modern slavery legislation inAustralia on page 18.8
EXECUTIVE SUMMARYINDUSTRY CHALLENGESLiving wageEnvironmental managementA living wage is a wage that is sufficient forworkers to be able to afford the basics (food, water,healthcare, clothing, electricity, and education)for themselves and their dependants. Yet mostgarment sector workers receive wages well belowthis figure. It comes as no surprise, then, that lowwages are among the chief concerns for workers.3The environmental impact of the fashion industryis significant with the apparel industry accountingfor 10% of global emissions.4 Up to 20,000 litresof water is needed to produce 1 kg of cotton —with it taking up to 2,700 litres to produce thecotton needed to make a single T-shirt.5 Globally,humans are consuming 800 billion new pieces ofclothing per year, 400% more than we consumedtwo decades ago. Australia is the second largestconsumer of new textiles after the US, averaging27 kg of new textiles per year.6 Even moreconcerningly, Australians are currently disposingof 6,000 kg of fashion and textile waste every tenminutes, with the majority of this going to landfill.7It is the poor and vulnerable who feel the impactof this environmental damage most acutely, withthe effects of landfill, water pollution and poorchemical management impacting on the healthand wellbeing of workers throughout the apparelsupply chain.The benefits of a living wage are substantial. In fact,payment of a living wage could transform the livesof millions by allowing people to lift themselves outof poverty and, at the same time, drive economicgrowth within communities and nations. However,it remains one of the most poorly assessed areasof our research.Questions around living wage make up a significantportion of the Worker Empowerment section ofthis research. Worker Empowerment is 2019 EthicalFashion Report’s lowest scoring section, with amedian grade of D. Just 5% of companies coulddemonstrate that they were paying a living wageto all workers at their final stage of production.While the industry still has a great deal of workto do to in the area of living wage, small steps arebeing taken. In 2019, 48% of companies assessedreported that they had started to develop a livingwage methodology and 24% of companies hadpublished a commitment to pay a living wage.For more information on the fashion industry’sapproach to tackling the continuing issue of livingwage, see page 19.Of these areas of concern, water use is one of themost substantial issues. Up to 20,000 litres ofwater is needed to produce 1kg of cotton — withit taking up to 2,700 litres of water to produce asingle cotton T-shirt. We found that just 12% ofcompanies were collecting and benchmarkingwater use data from all of their water intensivefacilities. When it comes to wastewater, again, just12% of companies are monitoring the wastewaterfrom all wet-processing facilities to ensure it is notenvironmentally hazardous.Positively, an increased number of companiesare investing in more sustainable fibres. Justover a third of companies have assessed theenvironmental impact of the fibres they use andare investing in more sustainable fibres in theirproduct design and production as a result.More information about the fashion industry’senvironmental impact can be found on page 22.This year, for the first time, the Ethical FashionReport assesses the effort of companies tomitigate their environmental impact. 11 questionswere asked in order to measure a company’simpacts on climate, chemical managementpractices, water usage, use of sustainable fibres,provision of take-back and repair programs, and,finally, whether had completed an environmentalimpact assessment.9
2019 ata glance130C A PoliciesBTraceability &Transparency7Companiesreceived A C38%of Companies saw animprovement in their Gradefrom the 2018 ReportCompaniesassessedMediangradeC-Auditing &Supplier relationshipssome of the biggest gainsEnvironmentalManagement17Companiesreceived FDWorkerEmpowerment22%moreCompaniesare ready toaddress andRemediateChild andForced Labour17%15%moremoreCompaniescompaniesare investingare investingin Responsiblein GenderPurchasingEquality withinPracticesthe supplychain10
There have been manyimprovement in 2019,such as.61%Changes in theindustry throughthe yearsof Companies are investingin using sustainable fibres.but despite the progress,significant issues remain:5%of Companies candemonstrate paying a livingwage to all workers at FinalStage facilities49%17%201348%20192013Companies working totrace where their rawmaterials come from18%81%2019Companies workingto trace where theirfabrics come from37%From 2013 to 2019 the percentage ofcompanies publishing full directsupplier lists has increased
2MethodologyThis section outlines the aims and scope of ourresearch, the process of data collection andevaluation, and our company grading system.12
METHODOLOGYThe 2019 Ethical Fashion Report providesa picture of ethical sourcing practices in thefashion industry as a resource for consumers,corporations, investors, and policymakers.This research seeks to empower consumersto make more informed and ethical choices inpurchasing fashion and footwear and providesinsight into supply chain governance forinvestors. It also aims to assist companies withbenchmarking and learnings, as well as identifyissues for policymakers to address. By presentingthe performance of companies (relative to oneanother) in an A to F grading system which isupdated on an annual basis, individual companies,and the wider industry, are encouraged to engagein continuous improvement with respect to theirethical sourcing practices.We recognise the fashion industry’s potential forpositive impact around the world. The ultimategoal of this project is to work collaborativelyalongside companies in the fashion industryto contribute to ending worker exploitation,alleviating poverty, and building environmentalsustainability throughout the fashion industry.Scope of the researchThe 2019 Ethical Fashion Report Grading Toolclassifies the fashion manufacturing supply chaininto three stages of production: final stage, inputsstage, and raw materials (outlined on page 15).Across these three stages of production, thisStatement on Non-Responsive CompaniesCompanies that are non-responsive, alongwith those that do not provide any substantiveinformation, are indicated in the Reportand Guide with an asterisk (*) next to theirname. These companies are also given theopportunity to provide a short statement asto why they chose not to respond, found onpage 90 of this report.We acknowledge that many of the nonresponsive brands may be doing more toimprove their ethical sourcing that we havebeen able to assess them on. However, ifbrands do not disclose, or are unwilling todisclose, what they are doing to ensure thatworkers are not exploited in their supplychains, then it becomes almost impossible forconsumers and the public to know if theseresearch considers five broad themes of socialresponsibility and environmental impact: policies,traceability and transparency, auditing andsupplier relationships, worker empowerment, andenvironmental management (outlined on page 15).This year marks the first year that environmentalmanagement metrics have been included in theassessment criteria, expanding this researchfrom its purely labour rights focus. It is widelyunderstood that the fashion industry has aconsiderable, and often negative, impact on thebrands are investing sufficiently to mitigatethese risks.Companies may prefer to disclose their supplychain management practices publicly, insteadof responding to our survey (e.g. they mightbe surveyed by multiple research projects orthey might prefer a single public disclosure,rather than disclosing through the survey).By assessing non-responsive companies onpublicly available information we can givedue credit to these efforts. In the history ofour research, non-responsive companieshave received a wide range of grades basedon their publicly available information. In the2019 Ethical Fashion Report non-responsivecompanies received grades ranging from a Bto an F.environment. In order to ensure that the researchremains the fashion industry benchmark whenit comes to ethical and sustainable sourcingenvironmental metrics were developed in 2018.These metrics were initially weighted at 0%, toensure participating companies had adequatelead time ahead of a new focus area being addedto the performance assessment process. Fromthis report onwards, the environmental metricswill inform each company’s grade, contributingto 10% of the final grade.13
METHODOLOGY ILO via https://flic.kr/p/V9uWtJIt is worth emphasising that Baptist World Aiddoes not conduct site inspections of factories.Therefore, company grades are not an assessmentof actual conditions in factories and farms, butrather an analysis of the strength of a company’slabour rights and environmental managementsystems. This research relies on data that is publiclyavailable, alongside evidence of systems andpractices provided by the companies themselves.Data collection and evaluationAs a proxy for the entire fashion supply chain,the 2019 Ethical Fashion Report assesses a largeselection of companies on 44 specific criteriaacross the five key themes, at three critical stagesof the supply chain.The survey and the weightings applied throughthe Grading Tool has been developed with inputfrom supply chain specialists, non-governmentorganisations, and company experts (see‘acknowledgements’ on page 97). The criteriacontained within the Grading Tool draws uponinternational standards, including those articulatedby the International Labour Organization, theSustainable Development Goals, and the UnitedNation’s Guiding Principles for Business andHuman Rights. The Grading Tool will continue toevolve over time to incorporate new learnings andreflect changing industry best practice.Garment factory in Hung Yên,In conducting a company evaluation, ourresearchers assess a company’s own publications,alongside any relevant independent reports anddata. Our researchers then send the findings(marked against the assessment criteria) to thecompany for comment and further input. Thisinput is then further reviewed. Baptist World Aidseeks to engage with companies, collect evidence,and understand their processes and systems;however, we do not conduct site inspections aspart of the grading process.Beyond engaging brands, our researchers alsowork with relevant certifiers to get a betterunderstanding of what systems are covered bytheir certification. Where companies use thesecertifications, information from the certificationbody is considered in the process of thecompany’s assessment. Certification bodies thathave been engaged with include Better CottonInitiative, the Global Organic Textile Standard,Fairtrade and Ethical Clothing Australia.Our researchers actively seek to engagecompanies (and pursue contact with nonresponsive companies) using at least threedifferent mediums: phone calls, emails, andletters. All non-responsive companies receive theirfindings twice by post. Letters are also mailed tothe company’s Board Chair and CEO. This processseeks to ensure that, in almost every instancewhere a brand has not responded, it is because ithas intentionally chosen not to do so.In 2019, 75% of brands engaged directly with thisresearch process.14
METHODOLOGYWhat the research coversThe research collects and evaluates datafrom fashion companies using the followingclassification of the supply chain and acrossthe following themes of social responsibility.RAW MATERIALS Cotton (farming) Wool, etc (husbandry,shearing etc) Crude Oil for syntheticfibres, plastics, etc(extraction, refining)INPUTS PRODUCTION Textiles production(ginning, spinning, knitting,dying, embroidery) Leather (tanning) Plastic (processing,moulding)FINAL STAGE PRODUCTION Cut-Make-Trim (CMT)manufacturing (cutting,sewing, printing)PoliciesTransparencyand TraceabilityAuditing and lManagement(and living wage)Why it matters:Policies form thestandards thatbrands want theirproduction toadhere to. Theyare the baselineby which a brandcan measure theeffectiveness ofits overall effortsto uphold workerrights.What we assess:Provisions toprohibit forcedlabour and childlabour, allowfor freedom ofassociation andprotect workerhealth and safety;whether a brandintends its policiesto cover the entireproduction process;whether the brandis undertakingimportant measurestowards improvingworking conditionsin facilities.Why it matters:In order to ensurethat worker rightsare being upheld,brands need toknow which facilitiesare responsible forthe production oftheir product.What we assess:How much ofthe supply chaina company hastraced; what itdoes to monitorand addresssubcontracting;what efforts it isundertaking totrace the remainderof its supplychain; a brand’stransparencyand how willingthey are to beheld accountablethrough theinformation it sharesabout it’s supplychain.Why it matters: Monitoringfacilities and buildingrelationships are critical toensuring policies are adheredto and improvements inworking conditions arebeing delivered. Whileno monitoring processis perfect, high qualitymonitoring helps to providea better understanding ofthe conditions of workers.A focus on strengtheningrelationships allows trustbuilding, and increases abrand’s capacity to drivechange.What we assess: Whatpercentage of productionfacilities are audited;whether unannounced andoffsite worker interviewsand anonymous workersurveys are used; whetherchecks are done on high riskactivities like labour brokersand recruitment fees;whether the brand is willingto be transparent about itsresults and remedial actions;whether brands are activelyinvolved in building supplierrelationships throughconsolidation, collaboration,supplier training and longterm relationship building.Why it matters: For alabour rights systemto improve workingconditions, workers mustbe empowered, alloweda voice, and have theirmost critical concernsaddressed. It is workersthemselves who have thebest visibility of workingconditions.What we assess:Whether workers areable to unite throughdemocratic trade unions;whether collectivebargaining agreementshave been established;whether effectivegrievance mechanismsare in place; whetherworkers are receiving aliving wage so they cansupport their families; abrand’s efforts in movingtowards paying a livingwage.Why it matters: Thefashion supply chaincan cause significantenvironmentaldegradation, whichaffects the wellbeingof workers, thecommunities they livein, and their naturalenvironment. Byassessing the materialsand facilities they useto make their products,brands can takeinformed steps to reducetheir environmentalimpact from the farm tothe final item of clothing.What we assess:Whether the companyhas done its ownassessment of theenvironmental impactthroughout its supplychain; the percentageof sustainable materialsused; if the company hascollected data on wateruse and chemical use inits facilities; monitoringsystems to improvechemical and watermanagement; whethertake-back and repairprograms have beenoffered to customers.15
METHODOLOGYData verificationGradingTo verify the data provided by companies,company responses are reviewed and clarificationand supporting documentation are sought wherenecessary. In some instances, the audit dataprovided by companies is relied upon to verifyconditions and benefits that workers receive.Wherever possible, our researchers and companyrepresentatives work through the survey questionstogether, allowing both parties to be satisfied thatthe data presented is an accurate representationof the company’s policies and processes.The grades awarded in the Report are a measureof the efforts undertaken by each company tomitigate the risks of forced labour, child labour,worker exploitation, and environmental harmthroughout their supply chains. Higher gradescorrespond to companies with labour rightsand environmental management systems that,if implemented well, should reduce the risk andextent of worker exploitation and environmentalharm in the production of that company’sproducts. Low graded companies are those thatare not taking these initiatives, or those choosingnot to disclose if they are taking such initiatives.To ensure consistency in the assessment ofcompanies after completing the survey, companyresponses are cross-checked by another memberof our research team.Survey support document2018 saw the introduction of the Survey SupportDocument (previously referenced as the“Assessment Support Document”). This documentwas reviewed and updated after the release ofthe 2018 Ethical Fashion Report. It was onceagain provided to companies as part of this year’sresearch process.The Survey Sup
the global fashion industry remains a significant employer. It also spurs economic growth, generates tax revenue, provides valuable skills and training, and delivers crucial foreign exchange. All of these factors can, and often do, contribute to improving the lives of workers and their communities. At the