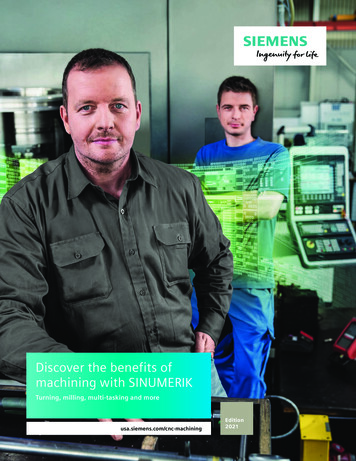
Transcription
Discover the benefits ofmachining with SINUMERIKTurning, milling, multi-tasking and moreusa.siemens.com/cnc-machiningEdition2021
Machining with SINUMERIK OverviewThere's a SINUMERIK CNC forevery machining application!OverviewNo matter if you're milling, turning, multi-tasking or 5-axis machining,there's a Siemens CNC that will increase your manufacturing productivityand accelerate your business.SINUMERIK offers you such an easy-to-use graphical interface that hasbecome the standard for efficient machine tool operation. Whether it's abasic part or a complex workpiece, the Siemens control system offers youa wealth of functionality with a very high degree of operator friendlinessand manufacturing efficiency.Contents2SINUMERIK CNC Family 04Operation and Programming 06Turning 09Milling 16Multi-tasking 22Other Machining Technologies 26Machine Tool Digitalization 28Technical information 30
Overview Machining with SINUMERIKTurningBenefit from the highest machining precision and manufacturing productivity from cycle-controlledand standard CNC turning by milling on lathes, up to multi-channel and multi-tasking machining.MillingFrom 3-axis milling through 5-axis simultaneous machining up to multi-tasking machining, thegreatest milling performance can be achieved with SINUMERIK MDynamics, Advanced Surfaceand Top Surface together with with Collision Avoidance.Multi-taskingBased upon SINUMERIK Operate, the easy-to-use graphical interface, multi-tasking machiningis seamlessly supported across every type of machining — whether in serial production or in singlepart production on the shopfloor.3
Machining with SINUMERIK CNC FamilySINUMERIKThe CNC portfolio for the machine tool industrySINUMERIK controls offer the perfect solution for each and every machine design. No matter ifyou're manufacturing individual parts or mass producing, basic or complex workpieces —SINUMERIK delivers the greatest return on your CNC investment.SINUMERIK 808The entry-level CNC for basic machinesnPanel-based compact CNCnUp to 6 axes / spindlesn1 machining channeln8.4" color displaynSIMATIC S7-200-based PLCnSINAMICS V70 drive, SIMOTICS S-1FL6 motorSINUMERIK 828The compact and advanced CNC for standard machines4nPanel-based compact CNCnUp to 10 axes / spindles and 2 auxiliary axesnUp to 2 machining channels T, M, Gn10.4" display or 15.6" touch displaynSIMATIC S7-200 PLCnSINAMICS S120, SINAMICS S120 Combi drives
CNC Family Machining with SINUMERIKSINUMERIK 840The open CNC for modular machine tool designsnDrive-based, modular controllernMulti-technology CNCnUp to 31 axes / spindles per NCU* and any number of PLC axesnUp to 10 machining channels per NCU*nModular panel concept up to 24" color displaynSIMATIC S7-300 PLCnSINAMICS S120 Booksize /Combi / Chassis drive, SIMOTICS motors*Up to 3 NCUs can be connected via NCU-LinkSINUMERIK ONEThe first-ever digital-native CNC —the next level of digital transformationnDigital twin as an integral component of the controllernDrive- and panel-based modular CNCnMulti-technology CNCnUp to 31 axes / spindles and any number of PLC axesnUp to 10 machining channelsnModular panel concept up to 24" multitouch color displaynSIMATIC S7-1500F PLCnSINAMICS S120 Booksize /Combi / Chassis drive, SIMOTICS motorsSINUMERIK MCThe CNC for special manufacturing technologiesnPC-based CNCnOpen user interface design based on WinCC or Run MyHMI / 3GLnUp to 8 axes / spindlesnUp to 4 machining channelsnModular panel conceptnSIMATIC S7-1500F PLCnSINAMICS S120 Booksize, SINAMICS S210 drives, SIMOTICS motors5
Machining with SINUMERIK Operation and ProgrammingUser-friendly operationand programmingOperationA wealth of functionality in SINUMERIK Operate ensure a highdegree of user-friendliness. This includes state-of-the-arttouch and gesture control, as well as the ability to workin several panes and the use of animated elements.Touch and gesture operationThe new generation of SINUMERIK touch-panels with projectedcapacitive touch technology offers you the highest degree ofperformance for demanding, PC-based visualization tasks.This comes along with an attractive front panel design.With its scratch-proof, non-reflecting surface and brilliantdisplay, SINUMERIK-equipped machines can be operatedeven in harsh manufacturing envrionments.Animated ElementsSINUMERIK Operate makes it very easy to enter parameters.With its unique moving image sequences, Animated Elementsmake machine operation even more user-friendly.Display Manager and SidescreenUsing the Display Manager, the display area can be sub-dividedinto three or four panes — allowing large screens to be usedeffectively. Additional information can be selected anddisplayed making machine operation customized and flexible.Sidescreen offers machine tool users an additional display tohave the needed information at their fingertips. Users canscroll horizontally and vertically through the data displayedon the screen.6
Operation and Programmingy Machining with SINUMERIKMachine tool setupBased on an intelligent JOG mode and intuitive toolmanagement found in SINUMERIK Operate, typical setupfunctions can be supported graphically and interactively.This keeps unproductive times to an absolute minimum.MeasurementMeasuring tools and workpieces are supported in intelligentJOG mode. It's sufficient to just probe an edge, corner orhole to determine the clamping position including the basicrotation of the tool — even in swiveled workpiece planes.Simply by pressing just one key, the geometry is transferredinto the CNC's tool offset memory. Logging measurementresults is simplified using standard or user logs.Zero pointsIntegrated measuring cycles guarantee workpiece precisionduring the machining process. Tool geometries and workoffsets are automatically corrected so that the requiredproduction tolerances are maintained, even for largebatch quantities.Tool managementTool data and magazine location information are clearlydisplayed on a screen. Selecting a suitable magazine locationis fully automatic — simply select a tool, press a key andSINUMERIK CNC does the rest. It goes without saying thattool life is monitored, and when required, the appropriatereplacement tool is loaded. This reduces the amount of timeneeded for machine tool setup.Protection of your peopleThe intelligent SINUMERIK Safety Integrated system functionsallow user-friendly operation, with the highest degree ofsafety for the operator and the machine itself — for example,when setting up the machine with the protective door opened.Users have an integrated Failsafe PLC at their disposal withSINUMERIK Safety Integrated plus. Safety-relevant logic isprogrammed in the TIA Portal.When commissioning the SINUMERIK 840D sl, applicationengineers can use various innovative functions, such asthe ability to graphically configure safety functions and thetransparent diagnostic screen forms.For Safety Integrated and Safety Integrated plus, as soon ascommissioning is completed, a prompted, partially automatedacceptance test can be performed in SINUMERIK Operate.7
Machining with SINUMERIK Operation and ProgrammingProgrammingDiagnosticsSINUMERIK Operate offers the ideal programming for eachand every task: DIN ISO for large-series production and theshortest cycle times — as well as graphical programming,so individual parts and components can be programmedeven faster.Especially in large serial manufacturing, machine downtimescan result in an enormous loss of production. SINUMERIKOperate offers intelligent diagnostics if problems arise so thatmachine operation can be resumed as quickly as possible.High-level CNC languageThe SINUMERIK high-level language means that the varianceassociated with families of parts or special tools can be easilymastered. The SINUMERIK high-level language comes intoplay precisely where graphical programming, DIN ISO andcycle programming reach their limits. Quickly programmingworkpieces with a wide range of variance means that thecomplete range of workpieces can be flexibly addressed —which is what makes it so unique.DXF readerThe DXF reader supports the display of the CAD data formatand direct transfer into the CNC program. Programming timescan be slashed by up to 90 percent as the CAD reader is usedto transfer data. DXF files can be directly opened on the CNC,and transferred to the CNC program with a simple click ofyour mouse. The DFX reader can be called up in the contoureditor, and for positions, it can also be called inprogramGUIDE as well as ShopMill / ShopTurn.programGUIDEUsing programGUIDE, part programs can be easily combinedwith high-performance technology and measuring cycles.Even classic ISO codes can be programmed. As a result,SINUMERIK is especially attractive for CNC machinists whoprefer this classical method of programming.Machining step programmingMachining step programming (ShopMill / ShopTurn) ensuresthat demanding and complex parts and components can bequickly and simply programmed. Using the SINUMERIKcontour computer, each contour can be entered andprogrammed directly at the machine. This results inmaximum machine tool productivity when it comes toprogramming and operation.SinuTrain for SINUMERIK OperateThis control-identical, PC-based software tool is based uponthe original NC kernel of the SINUMERIK control. SinuTraincan be used for offline part programming and even fortraining. You'll benefit from increased machine availability,enhanced security, and greater manufacturing productivity.8In addition to the bus diagnostic tools for drive, peripheraland network components, there is also a powerful tracefunction, which is used to trace and troubleshoot NC, PLCand drive signals.
TurningHighly productive and precise with SINUMERIKStandard CNC turning is a rather simple task for every SINUMERIK control.Depending upon the functional scope, the required performance andthe number of axes, SINUMERIK 828, SINUMERIK 840D sl and evenSINUMERIK ONE are the ideal CNCs for every turning application.9
Machining with SINUMERIK TurningCycle-controlled turning with SINUMERIKCycle-controlled lathes are frequently used for the repair and machining of individualparts. One requirement placed on the control is quite clear — it has to be very easy toprogram. SINUMERIK controls are the perfect solution."Manual machine" offers the greatest flexibility when itcomes to operation and programmingCycle-controlled lathes are mainly used to manufactureindividual or small series parts. The operator of a manualmachine expects a high degree of programming flexibilityfrom the CNC.Every SINUMERIK contol offers this usability in the form ofthe “Manual Machine” function. This function allows usersto manually operate the machine — without a programhaving to be written.The machine operator is navigated in a user-friendly wayto the finished workpiece. This is achieved using specialfunctions, which support the handwheels of a machineof this type, together with the standard use of machiningcycles. This makes the “Manual Machine” function ideal forentry-level CNC machinists.808D828DCycle-controlled turning with SINUMERIK10840D slThe “Manual Machine” function also offers additionaloptions for cycle-controlled lathes. It allows straight linesand inclines to be turned using crossover switches, individualmachining of turning and drilling cycles, as well as contourswithout having to generate a program. This function alsomakes it quite easy to repair threads.
Turning Machining with SINUMERIKStandard turning with SINUMERIK CNCWhen it comes to the machining of basic turned parts, the right control with shopfloorprogramming is necessary. CNC performance that is precisely tailored to the applicationis just as important. So no matter which control system you choose from theSINUMERIK family, we guarantee you'll benefit from the right CNC.Broad SINUMERIK portfolioStandard CNC turning is easy for every SINUMERIK CNC. Based upon the requiredfunctional scope, the required performance and the number of axes, the idealSINUMERIK control is available for every application.Machines with main and counter-spindle, Y-axes and driven tools are supportedby the extensive turning and milling cycle package of SINUMERIK 828 andSINUMERIK 840D sl controls.Machining technology cycles for standard CNC lathesIntelligent turning cycles are the “core" of a lathe. This is why SINUMERIK CNCshave a comprehensive range of turning functions: cutting, grooving, undercutand thread cycles, up to machining freely definable contours and residualmaterial detection. SINUMERIK CNCs comply with every turning requirementwhen it comes to machining strategies — such as roughing or finishing parallelto the axis and contour, plunging or plunge-turning.Fast and effective plunge-turningMove quickly from the drawing to the finished workpiece. Especially for difficultcontours with relief cuts, plunge-turning represents the ideal machining process.Using just one tool, the complete contour can be machined with plunge andplunge-turning cycles. It's not necessary to setup and change tools. As you'reprogramming, the contour is generated and linked with the plunge-turningcycle. There are no additional programming costs.Technology cycle, counter-spindleThe counter-spindle technology cycle allows machining to be performed on twospindles on one lathe. With this configuration, workpieces are automaticallytransferred between the spindles.Counter-spindle machining increases your productivity and machining quality —there's no need to manually re-clamp the workpiece.808D828D840D slStandard CNC turning with SINUMERIK11
Machining with SINUMERIK TurningMilling on lathes with SINUMERIKFlexible, high-performance CNCs — suitable even forprogramming directly on the shopfloor— are requiredif workpieces are to be milled on turning machines.12
Turning Machining with SINUMERIKInnovative CNC functions for milling on lathesSINUMERIK Operate, the state-of-the-art, intuitive graphical user interface makesmilling on lathes easy. It's the exact same look-and-feel when it comes tomachining with comprehensive CNC functions leading to the the ideal solutionfor the particular application.Regardless of whether parts should be milled or machined on the face or peripheralsurface — with TRANSMIT and TRACYL, the machine plane is transformed at theprecise location. This is done automatically thanks to the NC functionality embeddedin SINUMERIK Operate without requiring a CAD/CAM system or calculator.TRANSMIT makes face machining easyA lathe spindle operated in the C-axis mode is more than just a simple positioningaxis. Using the TRANSMIT function in SINUMERIK Operate, driven tools can beused to drill and mill on the face side of a workpiece.Outstanding peripheral surface machining with TRACYLTurning machines equipped with SINUMERIK Operate are perfect when it comesto peripheral surface machining. Even when the tool offset is activated, slotswith parallel walls can be machined. Geometries are easily programmed in theflattened surface and the CNC takes care of everything else.SINUMERIK technology cycles for milling applicationsSINUMERIK cycles support machine tool users when it comes to quick and easyworkpiece programming. Even for complex tasks, comprehensive machiningsteps can be performed faster and more easily by using innovative cycles —for example trochoidal milling and plunge-cutting for machining with low cuttingpressure and low deformation levels. SINUMERIK CNCs provide all of the cyclesand functions that are needed for the milling application.808D828D840D sl–Milling on lathes with SINUMERIK13
Machining with SINUMERIK TurningMulti-channel machining with SINUMERIKFor multi-channel machining on lathes, high cutting volumesmust be removed. For large-series production, it's also crucialto have short cycle times. High-performance and flexible CNCsystems are needed to address these requirements.14
Turning Machining with SINUMERIKMulti-channel machining made easyLathes with several tool slides are considered to be high-end CNC machines.SINUMERIK Operate ensures that these multi-channel machining operations can beprogrammed even more efficiently. The SINUMERIK control manages individualtool slides in the various channels. Programs must be generated for each channel,which then run simultaneously during machining. In SINUMERIK Operate, the“programSync” function is a high-performance editor, which permits programs tobe edited, aligned and optimized simultaneously, when adapted to the channelstructure of the machine — no matter if programmed in DIN/ISO or in ShopTurn.Workpiece simulation for multi-channel machiningOutstanding visualization of multi-channel machining can be achieved by usingsimulation in SINUMERIK Operate. This results in a higher degree of reliabilityand safety through 3D simulation with 3-plane view and volume model of themachined part — including simultaneous recording in automatic operation.Simulation also offers machine users comprehensive monitoring and optimizingoptions for multi-channel programming by automatically calculating the timeneeded for each machining step.SINUMERIK cutting cycleUsing the SINUMERIK contour cutting cycle, sophisticated and demanding 4-axisturning can be programmed directly at the machine without needing a CAD/CAMsystem. Contour and basic cutting parameters can be entered easily in the controlchannel. The contour cutting cycle automatically generates the CNC sequencesrequired for the specific 4-axis turning strategy. Machining with one tool can beexpanded to involve two tools for highly-productive Balance Cutting by using justtwo additional parameters.808D828D840D sl–Multi-channel machining with SINUMERIK15
MillingPerfect surfaces with SINUMERIK MDynamicsMilling expertise, powerful SINUMERIK CNCs and intelligent controlfunctions to handle the CAD-CAM-CNC process, all combined in onepackage — this is SINUMERIK MDynamics — high-end motion controlresulting in perfect workpiece surface finishes.SINUMERIK MDynamicsIncludedFunctions in detailSINUMERIK 840D slSINUMERIK 840D sl3-axis / 3 2-axis machining3-axis / 3 2-axis machining5-axis machiningMilling system software packageSINUMERIK MDynamics technologyfor 3-axis milling packagenAdvanced SurfacennHMI user memory on user CF-cardnnTop SurfacennDXF readernnnOptional functionsSINUMERIK 828DnnnnnEES — access and execution from anyexternal memorySINUMERIK MDynamics technology for 5-axis milling packageAdvanced SurfacenAdditional HMI user memory on theNCU's CF-cardnShopMill machining step programmingnAutomatic residual material detectionand machiningnAdditional HMI user memory on theNCU's CF-cardShopMill machining step programmingAutomatic residual material detectionand machiningnMeasuring cycles in the automatic modenMeasuring cycles in the automatic modeMeasuring kinematics CYCLE996 / 9960n3-D simulation and simultaneous recordingn3-D simulation and simultaneous recordingShopMill machining step programmingnAutomatic residual material detectionand machiningTRANSMIT (face transformation) andTRACYL (cylinder surface transformation)nSpline interpolationnTop SurfacenDXF readernTRANSMIT (face transformation) andTRACYL (cylinder surface transformation)nSpline interpolationgnTRAORI 5-axis machining packagen3-D tool radius correctionnMeasuring kinematics CYCLE996 / 9960nTop SurfacenDXF readerMeasuring cycles in the automatic mode3-D simulation and simultaneous recordingTRANSMIT (face transformation) andTRACYL (cylinder surface transformation)nnSpline interpolationnExtended operating functionsnEES — access and execution from anyexternal memoryMeasuring kinematics CYCLE996 / 9960n16Advanced SurfaceEES — access and execution from anyexternal memory
Milling Machining with SINUMERIKIntelligent motion control usingAdvanced Surface and Top SurfaceTop Surface optimizes CAM data for the subsequent pathcontrol leading to an even better surface finish. AdvancedSurface has an optimized “Look ahead” algorithm, whichleads to perfect surface quality with identical results inadjacent milling paths.The compressor ensures high contour precision and veryhigh machining speeds. Intelligent jerk limiting puts lessstress on the mechanical system of the machine. It enablessmooth acceleration and deceleration even at the highestrates of acceleration, therefore extending the service lifeof the machine.An essential advantage is the automatic harmonization ofvelocity profiles to adjacent milling paths by the control.It is also effective during forward / backward line-by-linemilling of contours and free-form surfaces, resulting in ahigher surface quality .In addition, the ORISON function smooths out orientation fluctuations across several blocks.With functions such as Advanced Surface and TopSurface, SINUMERIK controls can achieve the bestsurface finish and the highest possible speeds.This enables the complete machining of workpiecesin just one clamping — allowing users to reach newlevels of productivity for the high-speed milling ofcomplex parts and free-form surfaces.808D828D840D sl808D828D840D sl–Advanced SurfaceTop Surface17
Machining with SINUMERIK MillingSupplementary milling functionsTop Surface — new COMPSURF compressorThe COMPSURF compressor allows significantly better workpiece surfaces to beachieved for inclined line-by-line milled finishing programs, for “poor” dataquality and / or irregular point distribution in NC programs from the CAD/CAMsystem. COMPSURF also improves compliance with acceleration and jerk limits.As a result, machine-specific acceleration / jerk parameters can be increased.Standard values for contour and orientation tolerance are preset for almost allNC programs — independent of the calculation tolerance used in the CAD / CAM.NC programs and workpiece documents can be freely accessedThe new EES option (execution from external storage) allows data to be freelyaccessed on USB sticks, hard disks and network resources connected to the NCU.This means that workpiece documents can be directly viewed at the machine viathe graphical user interface — and part programs can be directly executed fromexternal memories and storage devices. From the NCU perspective, with EES,external memories and NC memories are functionally at the same level. Thismeans that only the capacity of the external data storage limits the maximumsize of a part program.Optimum protection against undesirable collisionsCollision Avoidance in the SINUMERIK control offers 3D collision monitoring inreal-time — for 1-channel machines with one NCU — and also for complexmachining such as 5-axis simultaneous milling. Collision monitoring is availablein every operating mode (JOG, MDA and automatic). The monitoring of machineelements with respect to one another, and with respect to tool cutting edges,can be visualized in 3D in SINUMERIK Operate.Quick moldmaking view (Quick Viewer)For milling machines, the moldmaking Quick Viewer allows programs with freeform surfaces to be quickly visualized. G0, G1, G2, G3 NC blocks are supportedalong with the display of vectors for 5-axis machining — both when programmingrotary axes as well as vectors.Process measuring cycles – automatic measuring cyclesUsing the SINUMERIK measuring cycles, the quality of machined parts can beeasily monitored in the machine. Powerful and user-friendly cycles for workpiecemeasurement and tools ensure high productivity. Automatic measuring cycles inprogramGUIDE and ShopMill — identical to the measuring cycles in JOG — clearlyreflect the high degree of user-friendliness and seamlessness of the control.808D–Supplementary milling functions18828D840D sl
Milling Machining with SINUMERIK3-axis milling with SINUMERIKThe tool position is approached in spaceusing linear axes X, Y and Z. This meansthat the tool tip can assume any position.For 3-axis machining, motion and machiningare achieved by programming the threelinear axes appropriately.SINUMERIK cycles for complex tasksSINUMERIK cycles support users so that workpieces can be programmed fasterand even more easily. For complex machining tasks, extensive machining stepscan be handled without issue by using innovative CNC cycles — for example,using CYCLE832 for mold-making.808D828D840D sl3-axis milling with SINUMERIK19
Machining with SINUMERIK Milling3 2-axis milling with SINUMERIKTheoretically, using three linear axes and two rotary axes, anypoint in space can be approached with any tool orientation.This is the basis for 5-axis machining. This means that a toolcan be aligned to the machine surface — or for peripheralmilling, a pocket can be milled with inclined walls.For all drilling and milling operations3 2-axis milling with SINUMERIK facilitates every conceivable drilling and millingoperation, including in any swiveled workpiece plane and on cylindrical workpieces.For simple handling, users have the popular CYCLE800 swiveling cycle available.Checking the machine's precision at the press of a buttonIn addition to innovative measuring cycles for workpieces and tools, the “measurekinematics cycle“ CYCLE996 / 9960 has been specifically developed to measuremulti-axis kinematics. It is simple to use and does not require expensive measuringequipment. The machine's kinematics can be measured at up to 12 positions perrotary axis using a 3D probe and the kinematics cycle. The cycle can be calleddirectly from the NC program. Compared to conventional measuring techniques,this can save a lot of time with extremely precise measuring accuracy.808D–3 2 axis milling with SINUMERIK20828D840D sl
Milling Machining with SINUMERIK5-axis milling with SINUMERIKThe three linear axes X, Y and Z and two rotary axesA, B or C are used for milling with aligned tools, reliefcuts or geometries arbitrarily located in space.The axes must be able to be controlled and movedsimultaneously.Simplified work sequencesThe SINUMERIK control has powerful functions, whichsignificantly simplify multi-axis programming and operation.For example, TRAORI (tool center point programming),ORISON (orientation smoothing), CUT3DCD (tool radiuscompensation) and CUT3DFD (tool wear).TRAORITRAORI is a dynamic process — rotary and linear axescan be traversed simultaneously during machining.The orientation of the tool in space can be changedcontinuously. And all axes (rotary and linear axes) areinterpolated at the same time.Orientation smoothing for 5-axis milling with ORISONUsing ORISON, the “smoothing of the orientationcharacteristic” function, orientation fluctuations aresmoothened across several blocks. As a result, a smoothorientation and contour are achieved — and in turn, axesare smoothly and harmoniously traversed.3-D tool radius compensation CUT3DC — CUT3DFSINUMERIK supports the handling and machining ofcomplex workpieces. For example, peripheral millingand face milling with tool radius compensation in 5-axis.808D828D––840D sl5-axis milling with SINUMERIK21
Multi-taskingLeading-edge machining with SINUMERIKIf your series production or small-batch part manufacturing involvesmill-turning or turn-milling, Siemens has you covered. The SINUMERIKcontrol supports you with various milling and turning tools; plus severaldifferent programming languages such as DIN / ISO, programGUIDE,ShopMill and ShopTurn; as well as simulation for both mill-turning andturn-milling applications. Siemens offers you the complete package forhighly efficient and very productive CNC machining.22
Multi-tasking Machining with SINUMERIKInnovative cycles for multi-taskingSINUMERIK cycles support machine tool users so that they can program the mostcomplex workpieces more easily and even faster.CYCLE800 swivel cycleMachining operations can be easily programmed in the swivel plane (swiveltable, swivel head) using the CYCLE800 swivel cycle. Also when using turningtools, this function — known from milling applications — can be used on a millingmachine to approach turning tools or to align them. CYCLE800 is available in aneasy-to-understand version for multi-tasking applications — perfectly combiningturning and milling in one user interface.Turning cycleTurning cycles have been expanded in programGUIDE, ShopMill and ShopTurnfor easy operation of complex multi-tasking machines. A graphical contourcomputer supports users when entering data, while parameterization is easilyachieved. This function is especially intuitive, as turning tools are displayed inthe form of symbols. For the turning cycles function with ShopTurn and B-axis,aligned turning tools can be programmed both graphically and interactively.The approach angle of the B-axis and the positioning angle of the tool spindleare specified directly in the technology area of the cycle.Milling cycleMilling cycles with programGUIDE and B-axis are used to program machiningoperations on swiveled planes. After selecting the “Swivel plane“ function inCYCLE800, a new machining plane is generated on which all milling functionsare created, also using cycles. Milling cycles with ShopTurn and B-axis allowworkpieces to be milled on swiveled planes on a turning machine. Milling atthe face or peripheral surface is defined by selecting the plane in the cycle.All milling cycles running on a lathe are identical with those in ShopMill.High-Speed SettingCYCLE832, the user-friendly High-Speed Settings cycle, simplifies parametizationin mold-making and multi-tasking applications. Using just a few parameters, theSINUMERIK control is set to the particular machining task — roughing, finishingor semi-finishing — as well as the required machining tolerance.808D828D––840D slSupplementary milling functions23
Machining with SINUMERIK Multi-taskingWorkpiece simulation for turn-millingand mill-turningThe more complex the application and the more expensive the workpieceto be machined are, the more important it becomes to have simulation —in other words, virtually checking the production process avoids costlymistakes and helps users calculate the machining time even beforecut
and direct transfer into the CNC program. Programming times . can be slashed by up to 90 percent as the CAD reader is used . to transfer data. DXF files can be directly opened on the CNC, and transferred to the CNC program with a simple click of your mouse. The DFX reader can be called up in