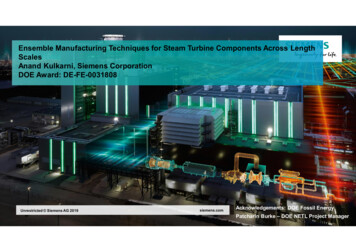
Transcription
Ensemble Manufacturing Techniques for Steam Turbine Components Across LengthScalesAnand Kulkarni, Siemens CorporationDOE Award: DE-FE-0031808Unrestricted Siemens AG 2019siemens.comAcknowledgements: DOE Fossil EnergyPatcharin Burke – DOE NETL Project Manager
OutlineIntroductionProject Objective and TeamProject Approach to Meet Technical TargetsDigital Manufacturing Efforts for Optimization of Parts for AMEnsemble Manufacturing Techniques and Process EnvelopeSteam Turbine Materials Development using AMs for Process-Structure-Property (PSP) RelationshipsNon-Destructive Evaluation (NDE) Inspection of Printed ComponentsConduct Rig/Engine Testing of AM Steam turbine ComponentsConclusionsUnrestricted Siemens AG 2019Page 2Kulkarni/ Siemens
Synergistic Research for Technical Advancements to meet theCost/Performance Targets Utilizing Additive ManufacturingProject informationTechnical HighlightsPI: Anand KulkarniFunding Opportunity ObjectiveApplying current AM technologiesto an existing partFunder: DOE Office of Fossil Energy (FE) – NETLStrategic Partner: Siemens Energy, Electric Power Research Institute, Oak RidgeNational Laboratory, Connecticut Center for Advanced TechnologyImprove cost and performance ofsteam turbine componentsKey Research AreasAdvanced turbine design- Novel blade designs forincreased efficiency andreduced CO2 emissions- Advanced internal coolingcircuit for reduced leakages- Hollow structured blades forreduced loadingAdvanced Materials/ NDE- Improved alloy chemistriesfor performance improvements-Process-structure-propertylinkages for multiple AMmethods for design window- Advanced NDE concepts forrapid qualification of AMcomponentsKeyContributions toU.S. TechnicalInnovationAdvanced Manufacturing- High powered additivemanufacturing process forsteam turbine alloys- Adaptive process for rapidbuildup of steam turbine parts- Ensemble processing acrosslength scales for cost reductionComponent scale up &Validation- Steam turbine rig forperformance evaluationof AM components vsbaseline- Validated flow CFDsimulations for improvedperformance (reducedlosses/leakages)Retire all risks associated with afollow-on field testPotential for repair/replacement ofexisting partObjective of Proposed ProgramThe application of existing AM processes (Directedenergy deposition (Optomec/DMG-Mori, Large areawire manufacturing), Selected laser melting (EOSM400) and Atomistic diffusion AM (Markforged) forredesigned steam turbine components across lengthscales for new/repair opportinities.Topology optimization for performance improvementsfor blades, seals and valve components planned.Potential activities include novel blade designs forincreased efficiency and reduced CO2 emissions,advanced internal cooling circuit for reduced leakagesand hollow structured blades for reduced loadingAdvanced NDE development for rapidqualification/inspection of AM components.Functional/performance testing of Steam turbine testrig for turbine flow CFD validation to demonstratereduced leakages, improved efficiency and reducedCO2 emissionsPotential to develop an on-site repair process via scanto print option for damage parts to create a 3D model torepair or re-print a new oneAn ensemble of multidisciplinary technologies to accelerate thedevelopment of materials, high-throughput experiments for theirqualification and design flexibility/topology optimization forrepair/redesign of components for AMUnrestricted Siemens AG 2019Page 3Kulkarni/ Siemens
Steam Turbines - Broad range for 50- and 60-Hz-gridsand drive applicationUnrestricted Siemens AG 2019Page 4Kulkarni/ Siemens
Project Team and ActivitiesSiemensOverall Project Lead. Activities involve repair component scanning and CADmodel repair, Design for AM, CFD modeling, Markforged/Selective LaserMelting (EOS-M400) materials development, NX based toolpath design forrepaired and redesigned components, Component buildup, Steam turbine rigtesting, Technology maturation into supply chain.ORNLLarge scale metal AM fabrication Lead. This includes materials feasibilityselection, process optimization, controls, and toolpath design for repaired andredesigned components. Component build up.EPRINDE task Lead. Conduct Field and shop deployable NDE for secondarycheck of finished component quality and critical to the life management cycleof new and repaired components. Will utilize its in-house state-of-the-artvolumetric and surface NDE technologies (including standard and advancedtechniques) to determine the best methods and limitations for NDE for thedifferent AM methods and component geometries built within this project.CCATDirect energy deposition AM Lead. CCAT will utilize their advancedmanufacturing assets (Optomec and DMG-Mori systems) to developprocesses and fabricate components of interest identified for this program.This includes materials development, build components using additive and/orhybrid machine tools, and measure quality metrics for the builds.Unrestricted Siemens AG 2019Page 5Kulkarni/ Siemens
Project Approach for AM Process Technologies for Field Trial ReadyComponents for Steam TurbinesYear 1Process optimization anddesign for AM for improvedcomponent performanceTechnical Progress Topology optimizationdemonstrated for optimal functionality of components Process parameter for optimalmaterials microstructureoptimizationGo / No-Go Down-selection of processparameter for optimal depositdensity/surface finish acrosslength scales Design for AM for performance/cost improvementsYear 3Performance improvementsfor AM Components inSteam turbine test rigYear 2PSP linkages and componentbuildup for production scale-upTechnical ProgressTechnical Progress Materials PSP linkagesestablished for designDemonstration of robustproduction control for AM ofadvanced steam turbine alloysacross length scalesGo / No-Go Components demonstrated viaAM compared to conventionalmanufacturing (MRL 4) First Rig test to demonstrateperformance improvements ofAM components AM component performanceimprovements in test rigAM of multiple components forrepeatability and scale-upDefined product specification forNDE inspection of AM partsProgram SuccessDemonstration of field ready AMcomponents in multi-stages todemonstrate reduced leakages andsecondary losses in steam turbine(TRL6)/(MRL5)Unrestricted Siemens AG 2019Page 6Kulkarni/ Siemens
Digital Manufacturing Efforts for Optimization of Parts for AMCAD Guided Repair of ComponentsDesign for Additive ManufacturingCorners and edges repairScanOutputScanUnrestricted Siemens AG 2019Page 7OutputDesign for AM needed for improved cost/performance of AM componentsKulkarni/ Siemens
Ensemble Manufacturing Techniques and Process EnvelopeProject Approach for AM Process Technologies for Field Trial Ready Components for Steam TurbinesUnrestricted Siemens AG 2019Page 8Kulkarni/ Siemens
Fast Technology ValidationAM enables paradigm shift in design, testing & validationIntegrated development: Accelerated iteration cycles in few months3D (Re-)DesignSLM processingPost processingInstrumentationTestingTest BedConventional processNovel paradigm“Testing is final validation at the end of development process““Testing is integrated part of development process“Clean Energy Center§Sequential development processes§Parallel and integrated development processes§Conservative development approach§Radical development approaches§Moderate development goals§Ambitious development goals§Long development cycles§Accelerated development goals, short iteration cyclesUnrestricted Siemens AG 2019Page 9Kulkarni/ Siemens
Selective Laser MeltingEOS M400 -1/-4Build volume – 400 x 400 x 400 mm§ Industrial implementation of SLM has successfully started BUT additionaldevelopment needs are substantial:- Design for Additive Manufacturing- Costs- Quality -Robustness and repeatability process control- Production Line integration standardized interfaces are requiredHigh performancecomponents with complexdesign and high potential toimprove customer value(efficiency, durability)Unrestricted Siemens AG 2019Page 10Kulkarni/ Siemens
DMG-Mori Lasertec 65 3D– Hybrid Precision Machining and LaserPowder Directed Energy Deposition 5-Axis Metal Powder Additive/Subtractive System Milling and Turning Additive Working Envelope: 19” x 19” x 13” Laser Powder Directed Energy Deposition 2.5 kW Laserline Laser Non-reactive metals (alloys of: steel, nickel,cobalt) Build complex components reducing part count Wide range of geometries with 5-axis motionUnrestricted Siemens AG 2019Page 11Kulkarni/ Siemens
Optomec LENS 850R – Laser Powder Directed Energy Deposition 5 Axis Metal Powder Additive System 3 Powder Feeders for Mixed and Gradient Builds Working Envelope: 36” x 60” x18” (on top of thetable) Argon Purged Enclosure (PPM Monitoring and O2Scrubber Control) 3 kW IPG Fiber Laser Reactive and Non-reactive Metals (alloys of:aluminum, steel, nickel, cobalt, titanium, refractorymetals; limited studies with graphite, ceramics)Unrestricted Siemens AG 2019Page 12Kulkarni/ Siemens
Low Cost Markforged AM PrintingIndustrial Printing Software:Cloud software turns drawingsinto high strength printing - Toanywhere from anywhere in theworldIndustrial Printers:Full range of printers forplastic, composite, & metalparts on a single platformIndustrial Materials:Plastics, Composites, and MetalsPurpose-built for strong parts witha beautiful finishUnrestricted Siemens AG 2019Page 13Kulkarni/ Siemens
Large Area Wire DepositionUnrestricted Siemens AG 2019Page 14Kulkarni/ Siemens
Process-Structure Property RelationshipsProcess DevelopmentMaterials Data Generationnominal UTS / %Stress [a.u.]horizontal (0 )123456vertical (90 )17515015012575alloy 150alloy 30300 µmSurface quality500750100002505007501000Temperature / C0.097% Porosity300 µm4 mmStandard qualificationbuild jobUnrestricted Siemens AG 2019Page 15250Temperature / CMicrostructural assessmenthorizontal (0 )50250alloy 2250vertical (90 )12510075100nominal elongation / %Properties compared to cast/forged material ( 100%)UTS for different setsof process parametersParameter SetParameter SetParameter SetParameter SetParameter SetParameter SetManufacturing Feasibility§§§§Distinctive properties in AM materials:T, t, dynamic, anisotropy, residual stress, distortion,defects, microstructure Huge range of data for several temperatures needed:tensile, HCF, LCF, creep/stress rupture, TMF,corrosion, physical props .X12CrMoWVNbN10-1-1X21CrMoNiV4-717-4 PH Stainless SteelIN625#Sealing segments - weight: 3 kglength 48 to 70 mm#Stationary drum blades - weight: 0.1 - 0.6 kglength: 70 to 350 mm#Rotating drum blades - weight: 0.1 - 0.6 kgLength: 70 to 350 mm#Last stage bladesSecond last end stage - weight: 12 kgLength: 520 mmStationary blade end stage - weight: 28 kgLength: 1200 mmMaterial design tools not available yetLimited range of materials for gas turbine applications availableTime consuming and costly validation (full qualification: 500 k ; 1.5 to 2 years)Approach: provide i) estimated, ii) limited or iii) fully validated material dataKulkarni/ Siemens
Non-Destructive Evaluation (NDE) Inspection of Printed ComponentsTypeEddy CurrentFlexible Eddy CurrentPhased Array UTTFM/FMCProcess CompensatedResonant Technique(PCRT)ProcessExample UsesRationalConventional surface inspectionsSurface-Conv. Airfoil surfaces, blade rootbeyond visual methods(exposed), shrouds (verification ofEnhanced inspections for curvedvisual) and sealsSurface-Advgeometries, hard to access locationsToday's state-of-art for crackVol.-Conv.detectionDisc attachments, blade rootsFull volumetric Data with less part(attached), repair quality of blades,knowledge, Multiple Data EvaluationVol.-Adv.new blade geometry and qualitySchemes (data science enabled), Nonlinear examinationsQuality' Measure for Part-to-partVol.-Adv.Entire Blade Volumevariations, post-test exposure shapeand material changesQuestion for AdditiveNew geometries may makeinspection more difficult, differentAM processes give differentsurface texturesNew geometries may hinderconventional UT processinspections, new grain structureswill attenuate UT signalsdifferently, new potentialdefect/damage locationsCan process variations in additivebe identified using resonancetechniquesEPRI has NDE technologies/techniques used currently on steam turbines and being considered forAM produced componentsUnrestricted Siemens AG 2019Page 16Kulkarni/ Siemens
Milestones and DeliverablesTask / SubtaskDeliverable TitleNumberSuccess Criteria at Decision PointsDue DateUpdate due 30 days after award.1.0Project Management PlanMilestoneNo.Year 1Plan4Down-selection of process parameter for optimal depositdensity/surface finish across length scales- Process parameter optimization and materials characterization ofbuilds to successfully meet defined material properties for the chosencomponent performance requirements and design constraints07/15/20Revisions to the PMP shall besubmitted as requested by theNETL Project Manager.1.02.0Technology Maturation PlanUpdate due 30 days after award.Topology optimization demonstrated for optimal0.8 year after award.MilestoneNo.Year 2Plan7Components demonstrated via AM compared to conventionalmanufacturing (MRL 4)- Demonstration of robust production control for AM of advanced steamturbine alloys for redesigned components with low cost/highperformance. The success criterial would be repeatability andreproducibility analysis through quality assurance reports from multiplecomponents that meet the product requirements06/30/21MilestoneNo.Year 3Planfunctionality of componentsDemonstration of Proof of concept (TRL3) for4.01.25 years after award.AM of advanced alloys for steam turbinecomponentsComponents demonstrated via AM compared to4.01.75 years after award.conventional manufacturing (MRL 4)Demonstration of AM components in multi-stages2.5 years after award.to demonstrate reduced leakages and secondary6.0losses in steam turbine (TRL6)Demonstration of AM manufactured process for7.0advanced alloys (MRL 5)2.75 years after award9Demonstration of AM components in multi-stages to demonstratereduced leakages and secondary losses in steam turbine (TRL6)Successfully conceive, develop, and demonstrate the performance ofAM components vs baseline for reduced leakages and secondarylosses in a steam turbine. Verify output with existing operational data.04/06/22Unrestricted Siemens AG 2019Page 17Kulkarni/ Siemens
Conduct Rig/Engine Testing of AM Steam turbine Components Conclusions. Unrestricted Siemens AG 2019 . An ensemble of multidisciplinary technologies to accelerate the . -Production Line integration standardized interfa