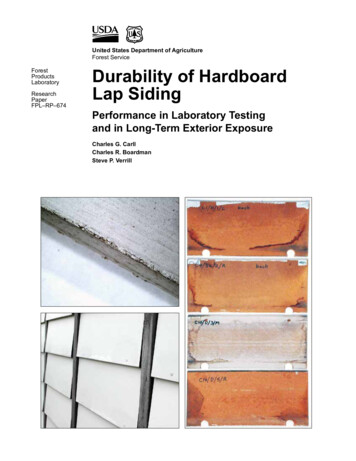
Transcription
United States Department of AgricultureForest RP–674Durability of HardboardLap SidingPerformance in Laboratory Testingand in Long-Term Exterior ExposureCharles G. CarllCharles R. BoardmanSteve P. Verrill
AbstractAcknowledgmentsThis paper describes a study that was undertaken to evaluatethe degree of correlation between in-service performance ofhardboard siding and its performance in the industry standard test procedure for “weatherability of substrate.” Thestudy included 13 different hardboard sidings: 6 noncommercial boards and 7 commercial products. All manufacturing plants operating in the United States in 1996–1997 wererepresented in the study. Twenty replicate specimens of eachof the 13 different boards were exposed on the south side ofan unconditioned building near Madison, Wisconsin, for155 months (almost 13 years). Although the climate at theexposure site was less challenging with regard to rainfallor decay hazard than most locations in the eastern UnitedStates, paint coating on test specimens was only about halfas thick as recommended. Two failure modes were observedin service, drip-edge paint cracking and edge welting,although paint condition on board faces remained essentiallyperfect throughout the exposure period. With regard to thetwo observed failure modes, substantial differences wereobserved among the 13 sidings. Relative frequency of thetwo failure modes was related to residual thickness swelling (RTS) value of the board, as identified by the substrateweatherability test procedure. Lower RTS values were associated with lower relative frequency of failure and lowerrelative frequency of more intense failure. In general, therewas no “plateau” value below which further reductions inRTS were not associated with greater relative frequency ofimproved in-service performance.This study was funded by the U.S. Department of Housingand Urban Development. Additional support was providedby the American Hardboard Association. Anton TenWolde(retired from FPL) played a lead role in design of the study.Gerry Laughinghouse, formerly of Georgia-Pacific Corporation, assisted in developing the study, and coordinatedproduction of noncommercial board. Harry Warren (retiredfrom Masonite Corporation) and Louis Wagner (formerlywith the American Hardboard Association) provided advice and coordinated the acquisition of commercial board.Vyto Malinauskas (deceased) prepared the test building forinstallation of specimens and served as data recorder forinspections conducted during the early years of exposure.Robert Munson assumed the role of helper/recorder for theinspector from 2002 through 2007. Alex Wiedenhoeft performed the microscopic inspections of board back surfacesthat identified that fungal colonizations had occurred. FlavioRuffinato (visiting scholar at FPL, and PhD student at theUniversity of Turin) produced the micrographs shown asFigures 7a, 7b, and 12. David Marr (formerly with FPL) andNeil Gribbins performed density distribution measurements,which yielded data presented in Table 4. Chris Hunt produced micrographs from which paint film thicknesses weremeasured and provided the lead author with information thatpermitted him to download and use the ImageJ software.In MemoriumKeywords: Hardboard siding, long-term exposure,durability, edge welt, drip edgesCharlie Carll passed away shortly before the publication ofthis paper. His coauthors acknowledge his strong leadershipin this research and recognize that his death represents agreat loss to his family, his friends, and the wood researchcommunity.September 2013ContentsCarll, Charles G.; Boardman, Charles R.; Verrill, Steve P. 2013. Durabilityof hardboard lap siding—performance in laboratory testing and in longterm exterior exposure. Research Paper FPL-RP-674. Madison, WI: U.S.Department of Agriculture, Forest Service, Forest Products Laboratory.25 p.Background.1A limited number of free copies of this publication are available to thepublic from the Forest Products Laboratory, One Gifford Pinchot Drive,Madison, WI 53726–2398. This publication is also available online atwww.fpl.fs.fed.us. Laboratory publications are sent to hundreds of librariesin the United States and elsewhere.The Forest Products Laboratory is maintained in cooperation with theUniversity of Wisconsin.The use of trade or firm names in this publication is for reader informationand does not imply endorsement by the United States Department ofAgriculture (USDA) of any product or service.The USDA prohibits discrimination in all its programs and activities on thebasis of race, color, national origin, age, disability, and where applicable,sex, marital status, familial status, parental status, religion, sexual orientation, genetic information, political beliefs, reprisal, or because all or a partof an individual’s income is derived from any public assistance program.(Not all prohibited bases apply to all programs.) Persons with disabilitieswho require alternative means for communication of program information (Braille, large print, audiotape, etc.) should contact USDA’s TARGETCenter at (202) 720–2600 (voice and TDD). To file a complaint of discrimination, write to USDA, Director, Office of Civil Rights, 1400 IndependenceAvenue, S.W., Washington, D.C. 20250–9410, or call (800) 795–3272(voice) or (202) 720–6382 (TDD). USDA is an equal opportunity providerand employer.Objectives.2Approach and Methodology.2Results. 10Discussion and Analysis. 18Conclusions. 22Literature Cited.23Appendix—Rainfall and Scheffer Index Values forOne Location in Each State East of and ImmediatelyWest of the Mississippi River.25
Durability of Hardboard Lap SidingPerformance in Laboratory Testingand in Long-Term Exterior ExposureCharles G. Carll, Research Forest Products Technologist, RetiredCharles R. Boardman, General EngineerSteve P. Verrill, Mathematical StatisticianForest Products Laboratory, Madison, WisconsinBackgroundDuring the 1990s, researchers at the USDA Forest ProductsLaboratory (FPL) undertook two studies concerning performance of hardboard lap siding. The first study involved exposure of hardboard lap siding on test buildings in southernFlorida for a period of 29 months (Carll and others 2000).The study was intended to evaluate the effectiveness of aLocal Acceptance Standard (LAS) promulgated by the Department of Housing and Urban Development (HUD) thatwould have required factory finishing of hardboard sidingand priming of all surfaces (including the back surface).All siding in that study was produced at one manufacturingplant and had physical properties that were substantially better than required by the industry standard for hardboard siding (AHA 1990).1 Moisture content of the siding remainedlow over the course of the exposure period, regardless ofwhether the siding was site-finished or factory-finished orwhether it was primed on its back surface. The siding remained in excellent condition, reflecting its consistently lowin-service moisture content. No conclusions that might havebeen generically applicable to hardboard siding could bedrawn from the study, because the study had included siding from only one manufacturing plant. Commercial hardboard siding available during the late 1980s and early 1990sshowed substantial variation in physical properties (Biblis1989, 1991). A second study, which addressed performanceof hardboard siding from all manufacturing plants in theUnited States (Carll and TenWolde 2004) was thereforeinitiated in 1997.The American National Standard for Hardboard Siding, inits three most recent editions (AHA 1990, 1998; CPA 2006),outlined a number of test procedures for evaluation of theproduct and specified acceptance criteria related to the testprocedures. Keplinger and Waldman (1998) and Baldwin(1988) indicated that when there are durability problemswith hardboard siding, irreversible (or “residual”) thicknessswelling is frequently a contributing factor to, or a cause of,1Thestudy was performed under a Sponsored Research andDevelopment Agreement between the USDA Forest Service, ForestProducts Laboratory, and a manufacturer of hardboard siding. Themanufacturer operated more than one plant, but produced sidingfor the Florida market at only one of their plants.problems. This suggested that the procedure in the AmericanNational Standard that involves measurement of residualthickness swell (RTS), referred to as the “weatherability ofsubstrate” test, would predict performance in service. As ofthe late 1990s, however, the literature did not contain evidence that performance in the substrate weatherability testprocedure correlated with performance in service.A main objective of the Carll and TenWolde (2004) studywas to evaluate the degree of correlation between performance in the industry standard test procedure for “weatherability of substrate” and performance in use. The studyinvolved laboratory testing and field exposure of a varietyof hardboard sidings with a wide range of residual thicknessswelling. Painted siding specimens, matched to unpaintedlaboratory test specimens, were installed on a test building(exterior exposure without additional water spray) and ontwo test fences that were sprayed with water for 1 h once aday during warm months (accelerated exterior exposure).The exposure site was FPL’s Valley View test site, just westof Madison, Wisconsin. Results from the 39-month accelerated exterior exposures were reported (Carll and TenWolde2004). RTS, as measured by the “weatherability of substrate” test procedure, proved to be a good indicator of thelikelihood of three modes of problematic performance onthe spray fences: edge welting, mildew growth, and paintcracking on drip edges. Each of these problematic performance modes was moisture related. The exposure period forspecimens placed on the test building (nonaccelerated exterior exposure) was intended to be a decade or slightly more.At the time of publication of Carll and TenWolde (2004), theexposure period had been substantially less than a decade,so data for specimens on the test building were, for the mostpart, not reported. The exposure period reached 10 years inSeptember 2007 and was continued until August 2010.The present paper addresses performance of specimens onthe test building over their approximately 13 years of exposure, in other words, the completion of the study initiated in1997. Among other things, it reports on correlation betweenin-service performance of specimens and their performancein laboratory testing. It covers, in some detail, the twoproblematic behaviors (“failure modes”) that were observedduring exposure.
Research Paper FPL–RP–674ObjectivesThe study objectives, outlined by Carll and TenWolde(2004), were (1) to examine to what extent performance inthe industry standard test procedure for “weatherabilityof substrate” correlated with siding performance in use,(2) to determine if change in the acceptance criterion for“substrate weatherability” in the American National Standard was justified, and (3) to examine to what degree resultsfrom other laboratory tests correlated with siding performance in use. The acceptance criterion in the American National Standard for substrate weatherability was changed in2006, with maximum allowable value for RTS lowered from20% to 17% (CPA 2006). This change was based on resultsfrom the part of the study involving accelerated exposure(Carll and TenWolde 2004) that indicated that RTS was animperfect but nonetheless useful predictor of performancecharacteristics on test fences and that the likelihood of certain problematic behaviors (“failure modes”) was noticeablygreater when RTS exceeded 17%. In light of the 2006 revision of the American National Standard, the second objective for the remaining phase of the study has been revised.The revised objective is to evaluate the now-current17% RTS criterion value in the industry standard. A fourthstudy objective has been added, which is to identify prevalence of different “failure modes” in long-term exterior exposure and to document the patterns in which they develop.as unprimed 4- by 8-ft (1.2- by 2.4-m) sheets. At FPL, thesheets were sawn into 8-ft (2.4-m) by 8-in.- (0.2-m-) widestrips of lap siding; these siding strips therefore did not haveshaped drip edges. In preliminary testing, RTS value withinindividual strips was found to be largely predictable basedon production lot and position of the strip from within the4- by 8-ft sheet. The six classes of noncommercial boardwere thus based on production lot and strip position.Each of the seven commercial classes of hardboard sidingwas produced at a different production plant. The commercial hardboards were shipped to FPL as factory-primedstrips of nominally 8-in.- (0.2-m-) wide lap siding with beveled or slightly rounded drip edges, which had been shapedprior to priming. All the hardboard sidings (commercialand noncommercial) had flat smooth (not textured) frontsurfaces.Because OSB siding was, at the time of study initiation, notreadily available as lap siding, 8-in.-wide by 8-ft-long stripsof siding were sawn at FPL from 4- by 8-ft (1.2- by 2.4-m)sheets of panel siding obtained from a lumber retailer. TheOSB siding had an embossed (textured) face. It containedzinc borate, which was confirmed by atomic emission spectroscopy. The OSB siding was assigned a class number of 9,reflecting that it was received at FPL after two of the commercial hardboards (classes 7 and 8) but before five of thecommercial hardboards (classes 10 to 14).Approach and MethodologySpecimen Selection and PreparationThe approach of the study and the methodologies it employed were described previously (Carll and Ten Wolde2004). Nevertheless, essential elements of the study’s approach and methods are reiterated here. Materials in thestudy included six noncommercial hardboard sidings andseven commercial hardboard sidings. One oriented strandboard (OSB) siding was also included as a reference material. All U.S. hardboard manufacturing plants producing hardboard siding in 1996–1997 were represented in the study.Twenty 8-ft-long strips were selected from each “class”(a total of 260 hardboard siding strips and 20 OSB sidingstrips) to provide specimens for laboratory testing and foroutdoor exposure. Laboratory testing included substrateweatherability (residual thickness swell), edge water absorption, and water vapor sorption. The cutting diagram forspecimens obtained from the selected strips was presentedas figure 3 in Carll and TenWolde (2004). Three specimensfor exterior exposure were obtained from each strip, two foraccelerated exposure on spray fences and one for long-termexposure on a test building.Siding ClassesThe 13 different hardboard sidings in the study were eachassigned a “class” number. In the case of noncommercialboards, class number was based on level of RTS observedin preliminary testing. In the case of commercial boards,class number was based on the order in which shipmentswere received at FPL from production plants.The six noncommercial classes of siding were selected fromdifferent lots of board produced for the study at an industrialplant. One of the lots was produced using the plant’s normalpressing procedures and was thus similar to commercialboard produced at the plant. Three additional lots werespecially produced at lower than usual press temperaturesand shorter press times to yield test materials that exhibiteda wide range of properties, in all cases inferior to those ofboards produced using the plant’s normal pressing procedures. The noncommercial boards were shipped to FPL2Specimens for exterior exposure were brush painted withtwo thin coats of satin exterior latex paint. On the commercial hardboards, the latex paint was applied over the factoryprimer. On the noncommercial hardboards, which werenot factory primed, the latex paint was applied over brushapplied alkyd primer. The alkyd primer was from the samemanufacturer as the latex topcoat. It was compatible withthe topcoat and recommended by the paint manufacturerfor use on hardboard that had not been factory primed. TheOSB siding had a resin-impregnated paper face, intended toserve as a topcoat base and was painted with two coats ofthe satin latex paint without priming. Average spread ratefor the combined two coats of latex paint was 387 ft2/gal(9.5 m2/L) on the hardboard and 267 ft2/gal (6.6 m2/L) onthe OSB. The solids content of the satin exterior paint wasapproximately 37% by volume. At the combined spread rate
Durability of Hardboard Lap Siding—Performance in Laboratory Testing and in Long-Term Exterior Exposureof 387 ft2/gal, dry thickness of the coating on the hardboardspecimens would have been approximately 1.5 mils(0.0015 in., 0.0381 mm) (ITW Resin Technologies [nodate]). By applying two thin coats of topcoat rather thanone heavy coat, uniform and complete coverage was assured; the risk of depositing irregular globs or fillets of paintaround specimen edges was avoided. The application of twothin coats, by virtually eliminating paint drips, also providedgreater confidence in recorded paint application weights,but resulted in topcoat dry film thickness (1.5 mils) beingconsiderably less than the industry-recommended value ofapproximately 3 mils, which would have been attained withtwo coats, each of approximately 1.5 mils dry film thickness, each applied at the paint manufacturer’s recommendedspread rate of around 400 ft2/gal. All brush painting wasperformed in a conditioned laboratory. The drip edges andfaces of specimens were painted, whereas specimen end cutswere left bare.Test Building ExposureBuilding and Exposure CharacteristicsThe test building, located at FPL’s Valley View test site, wasnot conditioned (it was not heated or humidified in winter,nor was it air-conditioned in summer). The building was48 ft (14.6 m) long and 8 ft (2.4 m) wide, with the long dimension in an east–west direction. Siding specimens wereinstalled on the south wall of the building as lap sidingcourses in 28 columns of 10 boards per column. The exposure of each course was 6.625 in. (0.17 m) (as had been thecase on the spray fences). The lowest course of siding wasinstalled over a 3.375-in- (0.086-m-) wide strip of wood–plastic composite lumber that had been planed to 0.375-in.(9.52-mm) thickness (the same thickness as some commercial hardboard siding). The lowest siding course overlappedthis strip by approximately 1 in. (25 mm). The means ofmounting specimens on the building was essentially thesame as that used to mount specimens on the spray fences,schematically depicted in figure 4 of Carll and TenWolde(2004); the wall framing was sheathed with 3/4-in. (19-mm)plywood, to which plywood nailing strips and treated lumber column separators were attached. The spaces betweennailing strips and column separators were then filled withextruded polystyrene foam. The mounting means, whichinvolved two layers of 3/4-in. (19-mm) plywood providedfor ample embedment of siding nails. (Nailing strips weresecured to the underlying layer of plywood with flat-headscrews, with the heads flush with the surface of the nailingstrip.) The foam between the nailing strips and column separators meant that the siding was not installed as a rainscreen;there was no continuous vertical air gap behind the sidingbecause the top edge of each course of siding was in contactwith foam infill or a plywood nailing strip. The buildinghad been erected in the late 1970s;
study included six noncommercial hardboard sidings and seven commercial hardboard sidings. One oriented strand-board (OSB) siding was also included as a reference materi-al. All U.S. hardboard manufacturing plants producing hard-board siding in 1996–1997 were represented in the study.Author: Charles Carll, Charles R. Boardman, Steve P. Verrill