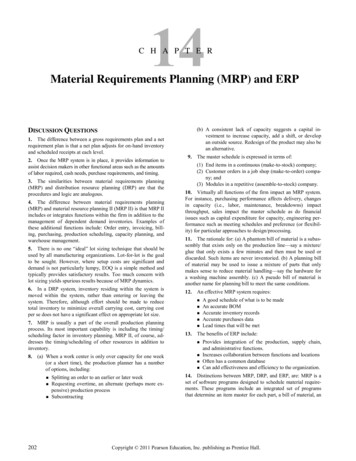
Transcription
14C H A P T E RMaterial Requirements Planning (MRP) and ERP(b) A consistent lack of capacity suggests a capital investment to increase capacity, add a shift, or developan outside source. Redesign of the product may also bean alternative.DISCUSSION QUESTIONS1. The difference between a gross requirements plan and a netrequirement plan is that a net plan adjusts for on-hand inventoryand scheduled receipts at each level.2. Once the MRP system is in place, it provides information toassist decision makers in other functional areas such as the amountsof labor required, cash needs, purchase requirements, and timing.3. The similarities between material requirements planning(MRP) and distribution resource planning (DRP) are that theprocedures and logic are analogous.4. The difference between material requirements planning(MRP) and material resource planning II (MRP II) is that MRP IIincludes or integrates functions within the firm in addition to themanagement of dependent demand inventories. Examples ofthese additional functions include: Order entry, invoicing, billing, purchasing, production scheduling, capacity planning, andwarehouse management.5. There is no one “ideal” lot sizing technique that should beused by all manufacturing organizations. Lot-for-lot is the goalto be sought. However, where setup costs are significant anddemand is not particularly lumpy, EOQ is a simple method andtypically provides satisfactory results. Too much concern withlot sizing yields spurious results because of MRP dynamics.6. In a DRP system, inventory residing within the system ismoved within the system, rather than entering or leaving thesystem. Therefore, although effort should be made to reducetotal inventory to minimize overall carrying cost, carrying costper se does not have a significant effect on appropriate lot size.7. MRP is usually a part of the overall production planningprocess. Its most important capability is including the timing/scheduling factor in inventory planning. MRP II, of course, addresses the timing/scheduling of other resources in addition toinventory.8.(a) When a work center is only over capacity for one week(or a short time), the production planner has a numberof options, including: 202Splitting an order to an earlier or later weekRequesting overtime, an alternate (perhaps more expensive) production processSubcontracting9.The master schedule is expressed in terms of:(1) End items in a continuous (make-to-stock) company;(2) Customer orders in a job shop (make-to-order) company; and(3) Modules in a repetitive (assemble-to-stock) company.10. Virtually all functions of the firm impact an MRP system.For instance, purchasing performance affects delivery, changesin capacity (i.e., labor, maintenance, breakdowns) impactthroughput, sales impact the master schedule as do financialissues such as capital expenditure for capacity, engineering performance such as meeting schedules and preference (or flexibility) for particular approaches to design/processing.11. The rationale for: (a) A phantom bill of material is a subassembly that exists only on the production line—say a mixture/glue that only exists a few minutes and then must be used ordiscarded. Such items are never inventoried. (b) A planning billof material may be used to issue a mixture of parts that onlymakes sense to reduce material handling—say the hardware fora washing machine assembly. (c) A pseudo bill of material isanother name for planning bill to meet the same conditions.12.An effective MRP system requires: 13.A good schedule of what is to be madeAn accurate BOMAccurate inventory recordsAccurate purchases dataLead times that will be metThe benefits of ERP include: Provides integration of the production, supply chain,and administrative functions.Increases collaboration between functions and locationsOften has a common databaseCan add effectiveness and efficiency to the organization.14. Distinctions between MRP, DRP, and ERP, are: MRP is aset of software programs designed to schedule material requirements. These programs include an integrated set of programsthat determine an item master for each part, a bill of material, anCopyright 2011 Pearson Education, Inc. publishing as Prentice Hall.
CHAPTER 14MATERIAL REQUIREMENTS PLANNING (MRP)explosion scheme, a lead-time file, an inventory status file, andvendor information. DRP is a time-phased stock-replenishmentplan for all levels of the distribution network. Its focus is onretail and wholesale distribution network. On the other hand,enterprise resource planning (ERP) systems are systems thatoften integrate MRP and a variety of other accounting systems,human resource management, and communication with vendorsand suppliers.15. In MRP, demand need not be constant. Also, in an MRPsystem, the demand for one item depends on the demand forothers—in particular, the end item. (There are exceptions suchas spare parts and maintenance orders.)16. The disadvantages of ERP include: Is very expensive to purchase and even more costly tocustomize. Implementation may require major changes in the company and its processes. Is so complex that many companies cannot adjust to it. Involves an ongoing process for implementation, whichmay never be completed. Expertise in ERP is limited, with staffing an ongoingproblem.17.Partner relationship management solutionSales solution Service solution CRM analytics CRM industry solutions Marketing solution(b) SAP’s Supply Chain Management product includes: Supply strategy development Supplier qualification Supplier selection Contract negotiation and management ERPLife-cycle collaborationQuality managementEnvironment health & safety(See www.sap.com/solutions.)19. Moving toward JIT and kanban suggest that the traditionalweekly “buckets” (or even daily buckets) in an MRP systemmay be inadequate. MRP systems may need to move to hourlybuckets for some items. Some MRP systems now deliver to“positions” in the production process—a “flow” criterion ratherthan a bucket criteria.Additionally, if tracking of small lots is necessary (and it maynot be) then not only will such “buckets” be necessary, but ease ofinputs via bar codes or other automated means may be necessary.ETHICAL DILEMMAERP is going to cost more than expected.What do you do? Certainly, any sense of fairness and decencysuggest that the customer must be told the truth. However,a sales representative can be expected to try to solve the problemfor his customer. This may mean that: The first stop is the sales representative’s manager to seeif another customer or pending customer may have dealtwith this problem and solved the problem or may be willing to share development costs.A second option is to ask the manager “Is there anybudget or pending budget for this type of enhancement orcan we help the customer out by paying for part of theenhancement?”The bottom line is that not telling the customer the truth and/orselling the customer something that will not do the job is notonly unethical, but also probably bad business—certainly badbusiness in the long run.ACTIVE MODEL EXERCISEACTIVE MODEL 14.1: Order Releases1. Suppose that item B must be ordered in multiples of dozens.Which items are affected by this change?Items D and E2. Suppose that the minimum order quantity for item C is 200units. Which items are affected by this change?Items E, F, G, and DEND-OF-CHAPTER PROBLEMS14.1An exploded bill yields the following:Item J: 200 units; Item K: 200 1 200 units; Item L: 200 4 800 units; Item M: 200 2 400 units.14.2The time-phased assembly plan for the gift bags is:(c) SAP’s Product Lifecycle Management productincludes: Life-cycle data managementAsset life-cycle managementProgram & project management203 (a) The Web sites of most of the major ERP vendors willinclude “successful solutions” using their software.See Web pages of the major vendors:American Software: www.amsoftware.comJD Edwards: www.jdedwards.comThe Baan Company: www.baan.comOracle: www.oracle.comSAP: www.sap.comIQMS: www.iqms.com(b) The poor ERP efforts or installations may take a littlemore digging, but a look at www.CIO.com and www.Information Week.com should get students started.18. (a) PeopleSoft includes the following in its CRM offerings (see ent/index.html):Supplier Relationship Management Manage supplierrelationships including indirect and direct goods, aswell as services procurement with:ANDSomeone should start on item M by noon.Copyright 2011 Pearson Education, Inc. publishing as Prentice Hall.
20414.3MATERIAL REQUIREMENTS PLANNING (MRP)CHAPTER 14WeekW Gross reqOn handNet reqOrder receiptOrder release(b)Gross material requirements plan:WeekItem123S Gross reqOrder releaseT Gross reqOrder releaseU Gross reqOrder releaseV Gross reqOrder release100W Gross reqOrder release 200X Gross reqOrder releaseY Gross reqOrder release 400Z Gross reqOrder release60014.5ERP(a) Product structure:Item14.4AND4Lead Time5678(weeks)10010010022S Gross reqOrder release3T Gross reqOrder releaseU Gross reqOrder releaseV Gross reqOrder release200100100400126001S Gross reqOn handNet reqOrder receiptOrder releaseT Gross reqOn handNet reqOrder receiptOrder releaseU Gross reqOn handNet reqOrder receiptOrder releaseV Gross reqOn handNet reqOrder receiptOrder release4Lead 535351352402400023604032032013201604012012023Lead Time45678(weeks)10010021001001200 20*200 20100210022002003100100400400Z Gross reqOrder release140402600600 60601Week1Item212060303030W Gross reqOrder releaseX Gross reqOrder releaseY Gross reqOrder release1*needed for maintenance.14.7 Net material requirements plan, modified to include the20 units of U required for maintenance:60306120309090X Gross reqOn handNet reqOrder receiptOrder releaseY Gross reqOn handNet reqOrder receiptOrder releaseZ Gross reqOn handNet reqOrder receiptOrder releaseItem10035Week200241Week13200Net material requirements plan:Item214.6 Gross material requirements plan, modified to include the20 units of U required for maintenance purposes:21001Lead Time212S Gross reqOn handNet reqOrder receiptOrder releaseT Gross reqOn handNet reqOrder receiptOrder releaseCopyright 2011 Pearson Education, Inc. publishing as Prentice Hall.34Lead Time5671002080808080206060608(weeks)21
CHAPTER 14MATERIAL REQUIREMENTS PLANNING (MRP)WeekItem12U Gross reqOn handNet reqOrder receiptOrder releaseV Gross reqOn handNet reqOrder receiptOrder releaseW Gross reqOn handNet reqOrder receiptOrder releaseX Gross reqOn handNet reqOrder receiptOrder releaseY Gross reqOn handNet reqOrder receiptOrder releaseZ Gross reqOn handNet reqOrder receiptOrder release34Lead Time56160 20*40 0120 20120 2078(weeks)ERP2120 206030303023012030909039060253535135240 40240 04040240360 6040 0320 60320 60320 601(b) Castings need to start in week 4.Level(a)20514.9 (a) Time-phased product structure for bracket with starttimes:* To achieve these results in POM for Windows, add Part U as a newBOM line, level O, so that the software will recognize an additional independent demand, not scheduled receipts.14.8AND0123(b) For 50 brackets, the gross requirements are for 50 bases, 100 springs, 250 clamps, 250 handles, 250 castings, 100 housings, 200 bearings, and 100 shafts.(c) For 50 brackets net requirements are: 25 bases, 100springs, 125 clamps, 125 handles, 125 castings, 50housings, 100 bearings, and 50 shafts.Copyright 2011 Pearson Education, Inc. publishing as Prentice Hall.
206MATERIAL REQUIREMENTS PLANNING (MRP)CHAPTER 1414.10(a)Gross material requirements plan:WeekX1B1B2A1CDE1234Gross reqOrder relGross reqOrder relGross reqOrder relGross reqOrder rel50Gross reqOrder rel200Gross reqOrder rel100Gross req200Order rel 200 50 80 2056789 10 11 020201004020010080ERP(b) Net material requirements (planned order release) plan:Note: Elements have been listed in the gross material requirements plan in the order of level, and within a level, from left toright as viewed in the product structure.ItemANDLevel: 0Item: X1Week No.1Parent:—Lead Time: 12 3 4 567GrossrequirementScheduledreceiptOn hand50NetrequirementPlanned orderreceiptPlanned orderreleaseQuantity:Lot Size: L4L8 9 10 11 12502010050000201002010020100400400402004020050 80 20 400 100400 100Level: 1Item: B1Week No.1Parent: X1Lead Time: 223456Quantity: 1XLot Size: L4L789Gross requirementScheduled receiptOn hand20Net requirementPlanned order receiptPlanned order releaseLevel: 1Item: B2Week No.1Parent: X1Lead Time: 223Gross requirementScheduled receiptOn handNet requirementPlanned order receiptPlanned order release2000100100456Quantity: 2XLot Size: L4L789201Parent: B1Lead Time: 1234561011402002020202000200200Quantity: 1XLot Size: L4L789Gross requirementScheduled receiptOn hand5Net requirementPlanned order receiptPlanned order releaseLevel: 2Item: CWeek No.1110012100Gross requirementScheduled receiptOn hand20Net requirementPlanned order receiptPlanned order releaseLevel: 2Item: A1Week No.10201210111210111210059595951Parent: B2Lead Time: 123456Quantity: 2XLot Size: L4L7894040004040040040040Copyright 2011 Pearson Education, Inc. publishing as Prentice Hall.400
CHAPTER 14Level: 2Item: DWeek No.Parent: B2Lead Time: 12314MATERIAL REQUIREMENTS PLANNING (MRP)5Gross requirementScheduled receiptOn handNet requirementPlanned order receiptPlanned order releaseLevel: 2&3Item: EWeek No.1Parent: B1 & DLead Time: 2234Gross requirementScheduled receiptOn handNet requirement 10Planned order receiptPlanned order release3056Quantity: 1XLot Size: L4L78920200020200200200202006Quantity: 1X & 2XLot Size: L4L78940400100040040001001004001030301003414.11 (a)10111210111289ANDWeekItemAHC1256Gross reqOrder rel7100100Gross reqOrder rel(b) Level: 01Parent: —Lead Time: 123451006Gross requirementScheduled receiptOn handNet requirementPlanned order receiptPlanned order releaseLevel: 0Item: HWeek No.10050Gross requirementScheduled receiptOn handNet requirement 50Planned order receiptPlanned order release10050150145650150Quantity:Lot Size: t Size: : A, HLead Time: 2235050150100Parent: —Lead Time: 1231215050Gross requirementScheduled receiptOn handNet requirementPlanned order receiptPlanned order releaseLevel: 1Item: CWeek No.501001001150100Gross reqOrder relItem: AWeek No.101250Quantity: 1XLot Size: 0500150150Copyright 2011 Pearson Education, Inc. publishing as Prentice Hall.12ERP207
208CHAPTER 1414.12MATERIAL REQUIREMENTS PLANNING (MRP)ANDERP(a) Net material requirements plan:WeekItemAHBCJKDEFG1Gross requirementOn hand: —Net requirementOrder receiptOrder releaseGross requirementOn hand: —Net requirementOrder receiptOrder releaseGross requirementOn hand:Net requirementOrder receiptOrder releaseGross requirementOn hand:Net requirementOrder receiptOrder releaseGross requirementOn hand:Net requirementOrder receiptOrder releaseGross requirementOn hand:Net requirementOrder receiptOrder releaseGross requirementOn hand:Net requirementOrder receiptOrder releaseGross requirementOn hand:Net requirementOrder receiptOrder releaseGross requirementOn hand:Net requirementOrder receiptOrder releaseGross requirementOn hand:Net requirementOrder receiptOrder 00150150Copyright 2011 Pearson Education, Inc. publishing as Prentice 00150150
CHAPTER 14MATERIAL REQUIREMENTS PLANNING (MRP)(b)Copyright 2011 Pearson Education, Inc. publishing as Prentice Hall.ANDERP209
210CHAPTER 14MATERIAL REQUIREMENTS PLANNING (MRP)ANDERP9101112Quantity: 1XLot Size: L4L789101112Quantity: 2XLot Size: 50078910111214.13 (a)(b)(c)Level: 0Item: 20 fanWeek No.1Parent: —Lead Time: 12345Gross requirementScheduled receiptOn hand 100Net requirementPlanned order receiptPlanned order releaseLevel: 1Item: housingWeek No.1,0001009009009001Parent: 20 fanLead Time: 1 week234Gross requirementScheduled receiptOn hand 100Net requirementPlanned order receiptPlanned order releaseLevel: 1Item: grillsWeek No.Gross requirementScheduled receiptOn hand 200Net requirementPlanned order receiptPlanned order release6Quantity:Lot Size:78569001008008008001Parent: 20 fanLead Time: 2 weeks234561,8002001,6002,0004002,000Copyright 2011 Pearson Education, Inc. publishing as Prentice Hall.
CHAPTER 14Level: 1Item: fan assemblyWeek No.Parent: 20 fanLead Time: 3 weeks1234Gross requirementScheduled receiptOn hand 150Net requirementPlanned order receiptPlanned order releaseLevel: 1Item: electrical unitWeek No.Parent: 20 fanLead Time: 1 week1234Gross requirementScheduled receiptOn handNet requirementPlanned order receiptPlanned order release1112Quantity: 1XLot Size: L4L78591011126Quantity: 1XLot Size: L4L7891011126Quantity: 2XLot Size: 1007891011126Quantity: 1XLot Size: 500789101112Quantity: 1XLot Size: L4L7891011126900900900900Parent: housingLead Time: 2 weeks123458008008008001Parent: housingLead Time: 1 week23451,600501,5501,6001,6001Parent: housingLead Time: 1 week234Gross requirementScheduled receiptOn handNet requirementPlanned order receiptPlanned order releaseLevel: 2Item: hubWeek No.10750Gross requirementScheduled receiptOn handNet requirementPlanned order receiptPlanned order releaseLevel: 2Item: handleWeek No.96150750750Gross requirementScheduled receiptOn handNet requirementPlanned order receiptPlanned order releaseLevel: 2Item: supportsWeek No.5Quantity: 1XLot Size: L4L78900Gross requirementScheduled receiptOn handNet requirementPlanned order receiptPlanned order releaseLevel: 2Item: frameWeek No.MATERIAL REQUIREMENTS PLANNING (MRP)58004004005001005001Parent: fan assemblyLead Time: 1 week23456750750750750Copyright 2011 Pearson Education, Inc. publishing as Prentice Hall.ANDERP211
212MATERIAL REQUIREMENTS PLANNING (MRP)CHAPTER 14Level: 2Item: bladesWeek No.Parent: fan assemblyLead Time: 2 weeks1234Gross requirementScheduled receiptOn handNet requirementPlanned order receiptPlanned order release91011126Quantity: 1XLot Size: L4L7891011126Quantity: 1XLot Size: 12789101112Quantity: 1XLot Size: 25789101112503,8001Parent: electrical unitLead Time: 1 week2345900900900900Level: 2Item: switchWeek No.1Parent: electrical unitLead Time: 1 week2345Gross requirementScheduled receiptOn hand 20Net requirementPlanned order receiptPlanned order release900208808888888Level: 2Item: knobWeek No.1Parent: electrical unitLead Time: 1 week2345Gross requirementScheduled receiptOn handNet requirementPlanned order receiptPlanned order release01223122336Quantity: 5XLot Size: 100783,7503,800Gross requirementScheduled receiptOn handNet requirementPlanned order receiptPlanned order releaseLevelERP3,750Level: 2Item: motorWeek No.14.14 EFGHEC1111111111Note: with low-level coding, C would be a level 3 code.Copyright 2011 Pearson Education, Inc. publishing as Prentice Hall.
CHAPTER 14MATERIAL REQUIREMENTS PLANNING wLevelCode2LowLevelCode21Gross requirementScheduled receiptProjected on handNet requirementPlanned receiptPlanned releaseAllocatedLowLevelCodeItemID—2HPeriod (week)4567Gross requirementScheduled receiptProjected on handNet requirementPlanned receiptPlanned release102Period (week)456722222828823Period (week)45607105555558A5550523Period (week)456855555780078007855B533323Period (week)456511111F14441Gross requirementScheduled receiptProjected on handNet requirementPlanned receiptPlanned release381Gross requirementScheduled receiptProjected on handNet requirementPlanned receiptPlanned release210A1Gross requirementScheduled receiptProjected on handNet requirementPlanned receiptPlanned release8010101ItemIDG213101ItemIDD3ERPGross requirementScheduled receiptProjected on handNet requirementPlanned receiptPlanned releaseItemIDF2AND23Period (week)4565F1010Copyright 2011 Pearson Education, Inc. publishing as Prentice Hall.10101001000
214MATERIAL REQUIREMENTS PLANNING (MRP)CHAPTER P12ItemIDCGross requirementScheduled receiptProjected on handNet requirementPlanned receiptPlanned releasePeriod (week)456782278111Period (week)45678010ItemIDE31Gross requirementScheduled receiptProjected on handNet requirementPlanned receiptPlanned release10210100031000448B1000Period (week)45634H4H,D400014.15 (a) Ten units are required for production, and 10 each of B and F for field service D—1B1Gross requirementScheduled receiptProjected on handNet requirementPlanned receiptPlanned release3100000000101010101Gross requirementScheduled receiptProjected on handNet requirementPlanned receiptPlanned release2222Copyright 2011 Pearson Education, Inc. publishing as Prentice Hall.32Period (week)456228710M10A288100101080
CHAPTER e2LowLevelCode2MATERIAL REQUIREMENTS PLANNING (MRP)ItemIDF1Gross requirementScheduled receiptProjected on handNet requirementPlanned receiptPlanned releaseItemIDDItemIDG5Period (week)456555523Period 7800780078007800B01010Period (week)45651B2157M5551051Gross requirementScheduled receiptProjected on handNet requirementPlanned receiptPlanned release3101Gross requirementScheduled receiptProjected on handNet requirementPlanned receiptPlanned release2ERPAND10F01010Note: M (in items B and F) means a repair or maintenance �LowLevelCode3LowLevelCode31Gross requirementScheduled receiptProjected on handNet requirementPlanned receiptPlanned releaseItemIDCGross requirementScheduled receiptProjected on handNet requirementPlanned receiptPlanned release101010F1055523Period (week)45613101Gross requirementScheduled receiptProjected on handNet requirementPlanned receiptPlanned release105F51ItemIDE10Period (week)4561021010310344103310D414Copyright 2011 Pearson Education, Inc. publishing as Prentice Hall.15B01010Period (week)45634H,BH,D114140
216MATERIAL REQUIREMENTS PLANNING (MRP)CHAPTER 1414.16ERP(a) Only item G has changed because it has no subassemblies or components.(b) If week 1 on the production plan is now, then an increase in the lead time for G means only one unit of Gwill be available for component F in week 5. Therefore, F and consequently four units of “A” will be delayed one week.(c) As production planner, several options are possible: 14.17ANDTell the customer that the four units (which areprobably “spares”) are going to be delayed oneweek.Ask the supplier of G to expedite production ordelivery.Reduce the production time for item F or A.Lot-for-Lot Ordering Policy:Week1Gr reqBeg invEnd invOrd rcptOrd 0020800109101112100010808000800050005050CT Order cost holding cost 7 orders 150/order 20 units 2.50/unit/period 1,10014.18Economic order quantity:Q 2 DSH 2 330 150 57.4, or 57 units2.50 12where D period demand, S setup or order cost, H holding cost.Reorder point:330Reorder point Demand during lead time units week 1 week12 27.5, or 28 unitsLevel:Item:Week No.Gross requirementScheduled receiptOn handNet requirementPlanned orderreceiptPlanned orderreleaseParent:Lead Time: 1231304040044010103027575757Quantity:Lot Size: 141144555757Setups: 5 150 750Holding: (allowing for 12 time periods) 2.50 352 880Setup holding total cost 1,630Theoretical total cost:CT Order cost Holding cost 12DS QH Q2330 150 57 (12 2.50) 572 868.42 855.00 1,723.42 Copyright 2011 Pearson Education, Inc. publishing as Prentice Hall.52
CHAPTER 14MATERIAL REQUIREMENTS PLANNING (MRP)ANDERPNote: Order and carrying costs are not equal due to rounding ofthe EOQ to a whole number. Actual total cost:CT Order cost Holding cost Stockout cost 5 orders 150 order 454 units 2.50 unit period 33 units 10 unit stockout 750 1,135 330 2,215Note: The actual cost of using the EOQ policy under this case ofvarying demand is more than the theoretical cost. In addition, wewere forced to use backorders when stockouts occurred. The poorperformance with respect to stockout is due to the fact that “average demand during lead time” is not a particularly good measureof the necessary reorder point.Note that the present versions of the Excel OM and POM forWindows software do not consider reorder points, stockouts, orbackorder costs.You may wish to make use of the following:EOQ ordering policy, modified for delayed order placement:WeekGross requirementBeginning inventoryEnding inventoryOrder receiptsOrder 125757575757* Stockouts 16 12 5 33Total inventory 10 10 27 27 54 21 21 68 238Actual total cost:CT Order cost Holding cost Stockout cost 6 orders 150 order 238 units 2.50 unit period 33 units 10 unit stockout 900.00 595.00 330.00 1,825.00Thus, if we are able to “time” order placement in an optimal fashion, the EOQ ordering policy can be made more efficient. Note,however, that this optimal timing requires that we accuratelyforecast demand—something that for varying demand we areusually unable to do. Note, also, that this “optimal” timing doesnot reduce the likelihood of a stockout and, by increasing the customer “wait” period, may contribute to additional customer dissatisfaction. The elimination of stockouts can only be accomplishedby using a higher reorder point (reorder safety stock).EOQ ordering policy, modified to include safety stock:Week1Gr reqBeg invEnd invOrd rcptOrd 501025257Copyright 2011 Pearson Education, Inc. publishing as Prentice Hall.1250–12–5*5757217
218CHAPTER 14MATERIAL REQUIREMENTS PLANNING (MRP)Reorder when ending inventory 70ANDERP14.19 Solution with lead time 1: Holding cost 2.50; Setupcost 150. PPB ordering policy:Combined reorder safety stock:DemandduringLead 30.9171.0001Gr reqBeg invEnd invOrd rcptOrd rel304010231010401030604530303030060Week6770 200 3030 1010089101112101010100800 5050 5013050500100130Calculating EPP:EPP To reduce the likelihood of a stockout to approximately 10%, wemust use a combined reorder point/safety stock of 70 units. Notethat this “reorder” point is approximately two and one half timesthe reorder point calculated using the measure of “average demand over lead time.”Actual total cost:Setup cost150 60Holding cost 2.50PeriodsCombined11, 21, 2, 31, 2, 3, 41, 2, 3, 4, 5*1, 2, 3, 4, 5, 6CT Order cost Holding cost Stockout cost 6 orders 150 order 763 unitsCumulativeNet Req.CostsOrder HoldPart Periods00303060 30 0 30 2 60130 30 0 30 2 70 3 27000150150150150 25257575* The part periods for an order encompassing periods 1, 2, 3, 4, and 5most nearly approximates the EPP of 60. 2.50 unit period 0 units 10 unit stockout 900.00 1907.50 0 2,807.50Note: (1) We have assumed that: (a) a product ordered during acalendar week is available at the beginning of the following week;(b) shipments during a week take place at the beginning of theweek. (2) POM for Windows will produce the same answer. ExcelOM will produce the same answer when lead time is zero.Note that as we might expect, the holding cost has increased.PeriodsCombinedCumulativeNet Req.66, 76, 7, 86, 7, 8, 9*6, 7, 8, 9, 10709090100180Part Periods70 0 070 0 20 1 2070 0 20 1 2070 0 20 1 10 3 5070 0 20 1 10 3 80 4 370CostsOrderHold150 05050125* The part periods for an order encompassing periods 6, 7, 8, and 9 most nearly approximates the EPP of 60.PeriodsCombinedCumulativeNet Req.1010, 1110, 11, 12*8080130Part Periods80 0 080 0 080 0 50 2 100CostsOrderHold150 00250* The part periods for an order encompassing periods 10, 11, 12 most nearly approximates the EPP of 60.Calculate total cost:CT Order cost Holding cost 3 orders 150 order 230 units 2.50 unit period 1,025.00Copyright 2011 Pearson Education, Inc. publishing as Prentice Hall.
CHAPTER 1414.20MATERIAL REQUIREMENTS PLANNING (MRP)ANDERPAlways order 100 units; fixed order quantity (FOQ) 100Gross requirementScheduled receiptProjected on handNet requirementPlanned order receiptPlanned order 300300202010080050050020351001001001003 setups at 100 each 350 units @ 1 650.14
(MRP) and distribution resource planning (DRP) are that the procedures and logic are analogous. 4. The difference between material requirements planning (MRP) and material resource planning II (MRP II) is that MRP II includes or integrates functions within the firm in addition to the management of dependent demand inventories.