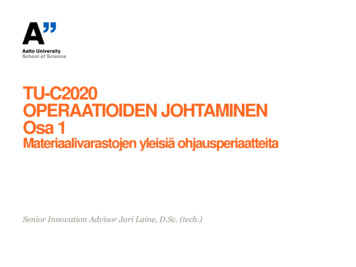
Transcription
TU-C2020OPERAATIOIDEN JOHTAMINENOsa 1Materiaalivarastojen yleisiä ohjausperiaatteitaSenior Innovation Advisor Jari Laine, D.Sc. (tech.)
A Fast Moving Consumer Goods Supply Chainand its information flowsDemand and Supply information FlowMoney FlowGoods Flow3.3.20222
Demand Picture Demand Forecasts–––– StatisticalHeuristicMarket sentimentCustomer collaborationOrder backlog/coverageSell-throughChannel stockPOS deliveriesReturns CampaignsCompetitor infoMarketing activitiesPricingTender coverageRFIs, RFQs3.3.20223
Supply Picture AvailabilityOrder statusNew products/versionsCapacity loadingOrder backlogRe-schedulingProduction lead timesProduction bottlenecks Special work arrangementsAllocationsOverstock infoContingency plansQuality issuesSupplier bottlenecksSupplier lead timesTransportation bottlenecks3.3.20224
Incoming Materials Planningand Execution ProcessMaterial deliveriesMaterial call-off signals (”Order”)Demand visibility info3.3.20225
Key points Sufficient Demand Visibility info is the key to keep the wholesupply chain aware of the situation big picture Automated information (S2S) sharing with key suppliers is (still)dominating in volume operations Supplier web, Extranets, Excel spreadsheets and email areused in more compact operations3.3.20226
Triggering the demandExecution i.e. triggering the materials replenishment can have multipleways, e.g.: Deliveries against rolling forecast Automated signal generated by inventory re-order point Visual order (e.g. Kanban) VMI signal A order sheet Phone call (beware) Email 3.3.20227
The life of an inventory, intheoryAverage Inventory3.3.20228
Types of Inventories Buffer (Safety) inventory– Precaution for unpredictable demand increase/availabilitychallenge Cycle inventory– Batch production, between work phases (WIP) De-coupling inventory– Between operations with different cycle times Anticipation inventory– Build ahead in aticipation of predictable demand peak (e.g.seasonal Pipeline Inventory– Goods in transit, not available immediately3.3.20229
How much toorder?3.3.202210
The effect of order quantity tolevel of inventory3.3.202211
Economic Order Quantity(EOQ)Figure: www.prenhall.comWikipedia: Economic order quantity (EOQ) is the order quantity that minimizes the total inventoryholding costs and ordering costs. It is one of the oldest classical production scheduling models. Theframework used to determine this order quantity is also known as Wilson EOQ Model, Wilson Formulaor Andler Formula. The model was developed by Ford W. Harris in 1913,[1] but R. H. Wilson, a consultantwho applied it extensively, and K. Andler are given credit for their in-depth analysis.[2]3.3.202212
What are the costs related Holding Cost– Cost of capital employed (working capital)– Storage & handling costs– Risk of obsolecence Ordering Cost– Cost of placing the order (office costs)– Transportation cost– Price (volume) discount costs3.3.202213
Criticism to EOQ Rather descriptive than prescriptive use Static, reactive model Assumes that costs and conditionsrelated are ”fixed” Only cost view Lean/JIT philosophy are opposing due tomissing ”improvement of processes”3.3.202214
When to order?3.3.202215
Inventory Re-Order Level(ROL)Drivers:Delivery Lead TimeConsumption over time3.3.202216
Re-Order Point (ROP)Figure: www.adbook.net3.3.202217
Summary of ROL, ROP Typically inbuilt in ERP/MRP sw as replenishment options. Can be used simultaneously Simplifications of real life:– Assume constant demand– Assume known delivery lead time Useful in non-complicated environments Statistical planning tools are replacing those in complicatedenvironments3.3.202218
TU-C2020OPERAATIOIDEN JOHTAMINENOsa 2,Materiaalitarvelaskenta ja mittaaminenSenior Innovation Advisor Jari Laine, D.Sc. (tech.)
From Inventory Control to ERPCloud3.3.202220
A Small Piece of MRP HistoryWikipedia:Prior to MRP, and before computers dominated industry, Reorder point (ROP) /reorder-quantity (ROQ) type methods like EOQ (Economic Order Quantity) hadbeen used in manufacturing and inventory management.[1]In 1964, as a response to the Toyota Manufacturing Program, Joseph Orlickydeveloped Material Requirements Planning (MRP). The first company to use MRPwas Black & Decker in 1964, with Dick Alban as project leader. Orlicky's 1975book Material Requirements Planning has the subtitle The New Way of Life inProduction and Inventory Management.[2] By 1975, MRP was implemented in 700companies. This number had grown to about 8,000 by 1981.In 1983 Oliver Wight developed MRP into manufacturing resource planning (MRPII).[3] In the 1980s, Joe Orlicky's MRP evolved into Oliver Wight's manufacturingresource planning (MRP II) which brings master scheduling, rough-cut capacityplanning, capacity requirements planning, S&OP in 1983 and other concepts toclassical MRP. By 1989, about one third of the software industry was MRP IIsoftware sold to American industry ( 1.2 billion worth of software).[4]3.3.202221
Materials Requirement Planning (MRP),why? Ensure materials are available for production Ensure products are available for delivery to customers. Maintain the lowest possible material and product levels in store Plan manufacturing activities, delivery schedules and purchasing activities3.3.202222
”Net MRP in nutshell”CalculatorX -/%Master dataBOMXSalesvolume/inventoryscheduleWorking calendarand annualcalendar-Inventories andopen orders athand Net demand intime buckets3.3.202223
Product Summary and re3.3.202224
Product Master Data, example"Schneckengetriebe" by Thorsten Hartmann - Own work. Licensed under CC BY-SA 3.0 viaCommons 02225
Towards Open, Digitaland Modular Common parts(product platform)Picture source: Kentaro Nobeoka, iew/028.html3.3.202226
Role of the inventories (discussion)Speed (Quick Response)FlexibilityCost optimizationSafetySynchronization of demand and supply or differentoperationsPlanning/Scheduling of operations phases and logistics3.3.202227
Disadvantages of Holding Inventory(Discussion)Lack of speed & flexibility Why?Cost Cost of capital employed Storage and handling Especially risk of obsolesence, price erosion3.3.202228
Central Issues InManagement, recap Right materialsRight timeRight PlaceOptimum (?) between availability(service level) and total cost (ICC)3.3.202229
Typical metrics Total capital employedInventory RotationDays of Supply (DOS)Landed costPrice developmentTransportation & fwd costLiabilitySlow movers%Obsolete%Work efficiency (receiving, picking lines/person/daySpace utilization rateQuality reclaims & returnsetc3.3.202230
ABC principle (Pareto analysis)Classification of value of consumptionValue ofinventoryNumber of items3.3.202231
ABC and XYZ analysisABC/XYZ analysis is a method of grouping planning objects (characteristic valuecombinations, SKUs) based on their value (revenue or sales volume) and dynamics ofconsumption or sales. During the analysis, the planning objects are assigned one of theclasses of ABC and XYZ simultaneously.Analysis based on value (ABC analysis) can be done by applying Pareto's rule on the value ofindividual items in a specific time horizon. The analysis ranks planning objects according totheir value contributions in terms of sales or contribution margin.Analysis based on the dynamics of consumption (XYZ analysis) means the calculation of avariance coefficient of consumption or sales in a specific time horizon. For example, aplanning object that has the values BY might mean a planning object with medium volume,and trend or seasonal demand.Source: SAP help portal3.3.202232
ABC XYZ analysis, from costcontibution to right timing3.3.202233
LEAN and JIT, implications toinventory management, discussionLeveled, steady flowElimination of all wasteContinuos improvementCustomer valuePull-principleVisual controlKanban3.3.202234
Central Issues in Inbound Logistics,discussionResponsivenessDelivery timeFlexibilityRisk managementMeans of transportationSustainability3.3.202235
Thank you3.3.202236
developed Material Requirements Planning (MRP). The first company to use MRP was Black & Decker in 1964, with Dick Alban as project leader. Orlicky's 1975 book Material Requirements Planning has the subtitle The New Way of Life in Production and Inventory Management.[2] By 1975, MRP was implemented in 700 companies.