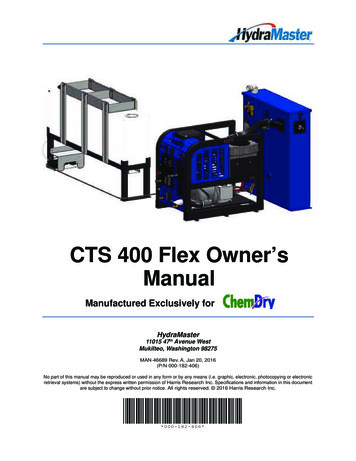
Transcription
CTS 400 Flex Owner’sManualManufactured Exclusively forHydraMaster11015 47th Avenue WestMukilteo, Washington 98275MAN-46689 Rev. A, Jan 20, 2016(P/N 000-182-406)No part of this manual may be reproduced or used in any form or by any means (i.e. graphic, electronic, photocopying or electronicretrieval systems) without the express written permission of Harris Research Inc. Specifications and information in this documentare subject to change without prior notice. All rights reserved. 2016 Harris Research Inc.*000-182-406*
Table of ContentsGENERAL INFORMATION. SECTION 1Contact Information. 1-3Warnings, Cautions and Notices. 1-4Responsibilities . 1-8Machine Specifications - Console. 1-10Machine Specifications - Flex Assemblies. 1-12High Altitude Operation . 1-13Local Water Precautions. 1-13OPERATING INSTRUCTIONS. SECTION 2Before Operating the CTS 400 Flex. 2-1Start-Up Procedure (All Modes). 2-2Carpet/Upholstery Procedure. 2-3Shut-Down Procedure. 2-4Tile/Stone Cleaning Procedure. 2-5Flex Tank Operation. 2-7FREEZE GUARDING . SECTION 3Freeze Guarding the Flex System. 3-2MACHINE MAINTENANCE. SECTION 4Operational Maintenance. 4-2High Pressure Pump Maintenance. 4-4Vacuum System Maintenance. 4-8Descaling Procedure (Required). 4-10Freeze Guarding. 4-11Tensioning the Pump Drive Belt. 4-13Descaling Flex System as Required. 4-14Pump Tuning Instructions . 4-15Clean QC Filter and Orifice . 4-18WATER AND CHEMICAL SYSTEM. SECTION 5ELECTRICAL SYSTEM. SECTION 6iii: CTS 400 Flex Owner’s Manual
TROUBLESHOOTING. SECTION 7Heating System. 7-2Engine. 7-3High Pressure System. 7-7Vacuum System. 7-10ASSEMBLIES AND PARTS LIST. SECTION 8Machine Assembly with 35 Gallon Tank and 15 Gallon Tank Parts List. 8-4Machine Assembly with 50 Gallon Tank Parts List. 8-6Console Assembly Parts List. 8-12Pump Cover Flex Assembly Parts List. 8-1335 Gallon and 15 Gallon Tank Flex Kit Assembly Parts List. 8-1435 Gallon Tank Flex Chemical Caddy Assembly Parts List. 8-1535 Gallon and 15 Gallon Tank Flex Assembly Parts List. 8-1750 Gallon Tank Flex Kit Assembly Parts List. 8-1850 Gallon Tank Flex Chemical Caddy Assembly Parts List. 8-1950 Gallon Tank Flex Assembly Parts List. 8-2065 Gallon Universal Recovery Tank (URT) Assembly Parts List. 8-23Passenger Side Pump Kit Assembly Parts List. 8-24Flex Pump Assembly Parts List. 8-25Blower Assembly Parts List. 8-27Dash Assembly Parts List. 8-30Engine Assembly Parts List. 8-33Exhaust Assembly Parts List. 8-34Diverter Valve Actuator Assembly Parts List. 8-35Exhaust Diverted Assembly Parts List. 8-37Exhaust Diverter Valve Assembly Parts List. 8-38Exhaust Manifold Assembly Parts List. 8-39Frame Assembly Parts List. 8-42Idler Pulley Assembly Parts List. 8-43Solenoid Valve Assembly Parts List. 8-45Heat Exchanger Assembly Parts List. 8-47Orifice Assembly Parts List. 8-48Pump Assembly Parts List. 8-50By-Pass Valve Assembly Parts List. 8-51Silencer Assembly Parts List. 8-52Water Box Assembly Parts List. 8-54Console Hose Routings. 8-55CTS 400 Flex Owner’s Manual: iv
HOW TO ORDER PARTS. SECTION 9Warranty Parts Orders. 9-1Parts Orders. 9-1Emergencies. 9-1WARRANTY INFORMATION. SECTION 10Blower . 10-1High Pressure Water Pump . 10-1Recovery Tank . 10-1Chemical System. 10-1Control Panel . 10-1Vacuum And Solution Hoses . 10-2Cleaning Wand And Tool. 10-2Water Heating System. 10-2Hard Water Deposits. 10-2Flex System Warranty. 10-4v: CTS 400 Flex Owner’s Manual
List of FiguresFigure 1-1. Hard Water Map of Mainland United States. 1-14Figure 2-1.Figure 2-2.Figure 2-3.Figure 2-4.Figure 2-5.Figure 2-6.Figure 2-7.CTS 440 Flex Dash Assembly. 2-2Select “CARPET/UPH.” on Solution Control Switch. 2-3Select “TILE/STONE” on Solution Control Switch. 2-5Side View of CTS 400 Flex Console. 2-6Flex Pump Levers. 2-7For 50 Gallon/Tank Assembly:. 2-7For 35 Gallon/15 Gallon Tank Assembly. 2-8Figure 4-1.Figure 4-2.Figure 4-3.Figure 4-4.Figure 4-5.Figure 4-6.Figure 4-7.Servicing the Valves. 4-5Adjusting Vacuum Relief Valve. 4-8Recirculation Fitting. 4-10Location of Pump’s Hex Screw. 4-15Insert Hex L-Key and Turn It Counterclockwise/Clockwise. 4-17Remove Quick Connect Assembly. 4-18Remove Filter and Orifice. 4-18Figure 5-1. Flow Diagram - View 1 of 2. 5-3Figure 5-2. Flow Diagram - View 2 of 2. 5-4Figure 6-1. Electrical Schematic. 6-3Figure 6-2. Wiring Diagram - View 1 of 2. 6-4Figure 6-3. Wiring Diagram - View 2 of 2. 6-5Figure 8-1. Adhesive/Sealant Material Reference. 8-2Figure 8-2. Machine Assembly with 35 Gallon Tankand 15 Gallon Tank - View 1 of 2 . 8-3Figure 8-3. Machine Assembly with 35 Gallon Tankand 15 Gallon Tank - View 2 of 2 . 8-4Figure 8-4. Machine Assembly with 50 Gallon Tank - View 1 of 2 . 8-5Figure 8-5. Machine Assembly with 50 Gallon Tank - View 2 of 2 . 8-6Figure 8-6. Console Assembly - View 1 of 5. 8-7Figure 8-7. Console Assembly - View 2 of 5. 8-8Figure 8-8. Console Assembly - View 3 of 5. 8-9Figure 8-9. Console Assembly - View 4 of 5. 8-10CTS 400 Flex Owner’s Manual: vi
Figure 8-10.Figure 8-11.Figure 8-12.Figure 8-13.Figure 8-14.Figure 8-15.Figure 8-16.Figure 8-17.Figure 8-18.Console Assembly - View 5 of 5. 8-11Pump Cover Assembly. 8-1335 Gallon and 15 Gallon Tank Flex Kit Assembly. 8-1435 Gallon Tank Flex Chemical Caddy Assembly. 8-1535 Gallon and 15 Gallon Tank Flex Assembly. 8-1650 Gallon Tank Flex Kit Assembly. 8-1850 Gallon Tank Flex Chemical Caddy Assembly. 8-1950 Gallon Tank Flex Assembly. 8-2065 Gallon Universal Recovery Tank (URT) AssemblyView 1 of 2. 8-21Figure 8-19. 65 Gallon Universal Recovery Tank (URT) Assembly - View 2 of 2. 8-22Figure 8-20.Figure 8-21.Figure 8-22.Figure 8-23.Figure 8-24.Figure 8-25.Figure 8-26.Figure 8-27.Figure 8-28.Figure 8-29.Pump - Passenger Flex Kit . 8-24Flex Pump Assembly. 8-25Blower Assembly - View 1 of 2. 8-26Blower Assembly - View 2 of 2. 8-27Dash Assembly - View 1 of 2. 8-28Dash Assembly - View 2 of 2. 8-29Engine Assembly - Part 1 of 2. 8-31Engine Assembly - Part 2 of 2. 8-32Exhaust Assembly . 8-34Diverter Valve Actuator Assembly. 8-35Figure 8-30.Figure 8-31.Figure 8-32.Figure 8-33.Figure 8-34.Figure 8-35.Figure 8-36.Figure 8-37.Figure 8-38.Figure 8-39.Exhaust Diverted Assembly . 8-36Exhaust Diverter Valve Assembly . 8-38Exhaust Manifold Assembly . 8-39Frame Assembly - View 1 of 2 . 8-40Frame Assembly - View 2 of 2 . 8-41Idler Pulley Assembly. 8-43Solenoid Valve Assembly. 8-44Heat Exchanger Assembly . 8-46Orifice Assembly. 8-48Pump Assembly . 8-49Figure 8-40. By-Pass Valve Assembly . 8-51Figure 8-41. Silencer Assembly. 8-52Figure 8-42. Water Box Assembly. 8-53vii: CTS 400 Flex Owner’s Manual
CTS 400 Flex Owner’s Manual: viii
1- General InformationThe CTS 400 Flex is manufactured exclusively for ChemDry by HydraMaster. It integratesHydraMaster’s popular and durable truckmounts with the specially designed Flex Systemwhich dispenses ChemDry’s proprietary solutions for carpet and upholstery cleaning, aswell and tile and stone cleaning.The CTS 400 Flex is available with a 50 gallon tank assembly or a 35 gallon/15 gallontank assembly.1-1: General Information
The truckmount portion of the CTS 400 Flex has been purposely modified to control theFlex System, ensuring that the two systems work seamlessly with each other.The truckmount system utilizes an internal combustion engine to provide the powernecessary to turn both a blower (also referred to as a vacuum pump) and a high pressurewater pump.The heat of the engine and blower exhausts is transferred to the high pressure water inthe heat exchanger of the system.The solution is recovered by the vacuum generated by the blower and is collected in therecovery tank for proper disposal.This Owner’s Manual provides operating instructions as well as information requiredfor proper maintenance and troubleshooting of the CTS 400 Flex. In addition, assemblyillustrations and parts ordering information are included for your convenience.It is the purpose of this Manual to help you properly understand and maintain your CTS 400Flex system. Follow the directions and maintenance recommendations carefully, and youwill be rewarded with years of profitable, trouble-free operation.It is imperative that no section be overlooked when preparing for operation of thisequipment. Please read this Owner’s Manual to familiarize yourself with the operation ofthe CTS 400 Flex System, paying special attention to all Warnings and Cautions.This section of the manual contains the following helpful information: Contact Information Warnings, Cautions And Notices Machine Specifications - Truckmount Machine Specifications - Flex Assemblies Responsibilities Hard Water Precautions Waste Water Disposal AdvisoryGeneral Information: 1-2
CONTACT INFORMATIONIf you have any questions regarding the operation, maintenance or repair of this machine,please contact your local distributor.When calling your distributor, be sure to reference the serial number and date of purchase.FOR YOUR REFERENCE:Serial No.Date of Purchase:Purchased From (Distributor):1-3: General Information
WARNINGS, CAUTIONS AND NOTICESThe manufacturer uses this WARNING symbol throughout the guide to warn ofpossible injury or death.This CAUTION symbol is used to warn of possible equipment damage.This NOTICE symbol indicates that federal or state regulatory laws may apply,and also emphasizes supplemental information.General Information: 1-4
During the operation of the truckmount many components are in motion. Nevertouch any part of the truckmount that is in motion. Serious injury may result.During the operation of the truckmount many surfaces will become extremely hot.Never touch hot surfaces. Serious injury may result.The operation of this truckmount can produce noise levels exceeding 85 decibelsto a distance of 10 feet. The Occupational Safety and Health Administration(OSHA) recommends the use of hearing protective equipment if a person isexposed to an average of 85 decibels over an eight hour period. Check with localand state agencies concerning hearing conservation rules.During the operation of the truckmount carbon monoxide and other toxic fumesare produced. Position the vehicle so that any fumes produced will be directedaway from inhabited areas and any points of building entry (doors, windows, airconditioning units, fans, etc.). Do not occupy the vehicle while the truckmount isin operation. Serious injury may result.During the operation of the truckmount chemicals known to the State of Californiato cause cancer, birth defects and other reproductive harm are produced by theengine exhaust.Never operate the truckmount with a portable gas container inside the vehicle.Doing so will increase the risk of fire and explosion. Serious injury or death myresult.Transporting a vented fuel container that presently contains, or has ever containedin the past, a flammable liquid is strictly forbidden by HydraMaster and by federaland state regulations. Doing so will increase the risk of fire and explosion. Seriousinjury or death may result.1-5: General Information
Never smoke in or around the truckmount. Doing so will increase the risk of fireand explosion. Serious injury or death may result.Be cautious when drilling holes through the van floor. Many vans have criticalcomponents mounted directly below the van floor that could be damaged by amisplaced drill bit.During the operation of the truckmount the exhaust system will become extremelyhot. Keep all flammable materials away from the truckmount exhaust system.Failure to do so will increase the risk of fire and explosion. Serious propertydamage may result.Never operate the truckmount when the vehicle is tilted more than 10 degreesin any direction. Doing so will result in improper lubrication of the internalcomponents, and will increase the risk serious component or engine damage.Never perform cleaning operations when the truckmount engine is running at theIDLE throttle position. Failure to do so will increase the risk of serious componentor engine damage.Never operate the truckmount with the vehicle doors closed. Doing so results inextremely high temperatures inside the vehicle and will lead to serious componentor engine damage.Never use concentrated acids or solvents (including d-limonene) in the truckmountwater system or chemical system. Use of these products will cause seriouscomponent damage.General Information: 1-6
Never operate the truckmount with a water hardness reading measuring 3.0grains per gallon or higher. Using reading than 3.0 grains per gallon will causescale to build up inside the truckmount water system. Scale build up causesserious component damage. Test all water prior to use and use water softeningequipment if necessary.Never allow water to freeze inside the truckmount. Serious component damagewill occur. Perform all freeze guarding procedures outlined in the digital Owner’sManual.Many vehicles have critical components mounted directly below the floor that caneasily be damaged. Before drilling holes in the floor of the vehicle, inspect theunderside of the vehicle for critical components. Failure to do so may result indamage to the vehicle.During the operation of this equipment, surfaces will become hot. Do not allowcomponents such as hoses to touch hot surfaces. Failure to heed this warningcan result in equipment damage which is not covered by warranty.1-7: General Information
RESPONSIBILITIESThe Purchaser’s ResponsibilitiesPrior to purchasing a van, ensure that the payload is suitable for all of the equipmentthat will be installed and transported. This includes and is not limited to: the truckmount,recovery tanks, fresh water tanks and on-board water, hose reels, hoses, cleaning tools,chemicals, drying equipment, etc. Payload capacity information is available through theauto dealer, the manufacturer’s web site, and is also located on the door pillar of thedriver’s side door.Purchase a heavy duty Group 24 (550 CCA or better) battery for this truckmount. This isnormally available from the installation dealer.Prior to dropping your van off at the distributor for the truckmount to be installed, have aspray-on bed liner applied to the floor such as Rhino Lining or Line-X .Prior to operating the truckmount read this manual in its entirety and familiarize yourselfwith the information contained here. Special attention should be paid to all cautions andwarnings.The distributor is responsible for the correct installation of the truckmount. The distributoris also responsible to train you in the correct and proper operation and maintenance ofthe truckmount.Any modification of the truckmount may void the warranty.The Distributor’s ResponsibilityAcceptance of ShipmentBefore accepting the truckmount, check the following: The truckmount should be free from any damage during shipping. Do not sign thedelivery receipt until you have closely inspected the truckmount and noted any damageon the delivery receipt. Hidden damage may be present even if the box looks okay. Itis recommended that the box be opened before signing for the shipment. Check the packing list and verify that all items are accounted for.General Information: 1-8
Installation Responsibilities Ensure proper payload capacity. It is the distributor’s responsibility to verify that theequipment package does not exceed the vehicle capacity. Ensure installation of a safe fuel tap system and through-floor fittings as provided byHydraMaster. Proper placement of the truckmount, recovery tank, fresh water tank, and accessoriesin the vehicle and securing them with bolts and back up plates. The distributor shouldverify that the owner is in agreement with the layout. Ensure proper connection of the fuel lines. Ensure proper connection and installation of the battery. Verify that the battery is inaccordance with HydraMaster’s recommendation. Check the pump, vacuum blower and engine oil levels prior to starting the truckmount. Start and run the truckmount and check that all systems function properly. Test all hoses, wands, etc. for correct operation. Ensure timely return of the document package.TrainingThe distributor should provide a thorough review of the operation manual with thepurchaser along with instruction and familiarization in: How all the truckmount’s systems function.All safety precautions and their importance.How to correctly start and shut down the truckmount.How to correctly clean with the truckmount.Where and how often to check and change component oil levels.Freezing damage and how to avoid it. This includes explaining proper freeze guardingprocedures. How to do basic troubleshooting of the truckmount. Hard water damage and how to avoid it. This includes how to determine if hard waterexists in your area and the installation and use of water softening systems. The truckmount’s warranty and warranty procedures.1-9: General Information
MACHINE SPECIFICATIONS - CONSOLEFrame DimensionsWeightEngine- Briggs andStratton Vanguard 18HP24.0" W x 31” H x 36" D570 lbsOil TypeCapacityIgnitionVacuum Blower- Tuthill3006 Competitor Plus SL(Dual Splash Lubrication)Water PumpElectric ClutchOperating PressureHeating SystemGeneral Information: 1-10Engine rpmFuel ConsumptionElectric Key StartMax. Vac.Oil TypeGear End CapacityDrive End CapacityBlower rpmOil TypeCapacity - oilPump RatePump rpm0 - 1,000 psiStainless Steel and CopperHybridSynthetic 5W-30Approx. 1 1/2 quarts (48 oz.)when changing oil and filter3,150 rpm1.0 gph12” HgPneuLube or other ISO 100ratingApprox. 7.0 oz.Approx. 5.0 oz.3,150 rpm30W non-detergentApprox. 8.0 oz.3.5 gallons per minute1,750 rpm
Standard EquipmentHigh Pressure HoseVacuum HoseRecovery TankOptional EquipmentBattery BoxVan DecalVan Installation KitOwner’s Manual (on CD)Owner’s Guide (paper copy)Flex System TanksFlex System TankAutomatic Pump Out (APO)1/4" High Temperature Lined/Vinyl Cover - 100 ft.2" Vacuum Hose- 100 ft.1-1/2" Wand Whip Line- 10 ft.65 gallon MaxAir UniversalTank35 gallon/15 gallon50 gallonDura-Flow APO1-11: General Information
MACHINE SPECIFICATIONS - FLEX ASSEMBLIES50 Gallon Tank Dimensions12” W x 33” H x 60” Lwith FrameWeight113 lbs35/15 GallonDimensions12” W x 33” H x 53” LTanks withFrameWeight108 lbsConstructionFramesSteelTanksPolyethyleneGeneral Information: 1-12
HIGH ALTITUDE OPERATIONElevation plays a key role in how the truckmount will operate. Operation at high altitude(above 5,000 ft.) may require a high-altitude carburetor jet. Use of this jet at high altitudewill improve power, reduce fuel consumption and help reduce excessive carbon build-upin the exhaust and heat exchanger systems.Contact the local Briggs and Stratton dealer or HydraMaster to obtain theproper jet size. Your local Briggs and Stratton dealer can be located ealerlocator .LOCAL WATER PRECAUTIONSThe quality of water varies greatly. Many areas have an excess of minerals in the waterwhich results in what is commonly called “hard water.” These minerals tend to adhere tothe insides of heater coils and other parts of the machines causing damage and a loss ofcleaning effectiveness. This influences the reliability and efficiency of equipment in directproportion to the level of hardness.Hard Water AdvisoryHydraMaster recognizes that any hard water deposits which might occur within the watersystem of our truckmounts is a serious problem. The precision technology of truckmountheat exchanger systems is intolerant of any foreign material. Hard water deposits willultimately decrease the performance of the system and are expected to seriously lowerthe reliability of the machine.To validate a machine’s warranty, HydraMaster requires that all machines operating indesignated “Hard Water Areas” (3.0 grains or more per gallon) be fitted with a watersoftening system, or a properly installed magnetic-type descaler must be used andmaintained. Periodic descaling or acid-rinsing alone is not adequate in these areas.HydraMaster does not recommend any particular type or brand; however, the relativeeffectiveness of some types of magnetic descalers or softeners may require additionalperiodic use of descaling agents.HydraMaster also recommends, in the strongest possible terms, that machines in allareas be fitted with a water softening system for improved operation and reliability.Failure to take appropriate measures to prevent scale build up can result insystem failure and loss of warranty on affected parts.1-13: General Information
Hard Wat
HydraMaster. 11015 47. th. Avenue West Mukilteo, Washington 98275. MAN-46689 Rev. A, Jan 20, 2016 (P/N 000-182-406) No part of this manual may be reproduced or used in any form or by any means (i.e. graphic, electronic, photocopying or electronic