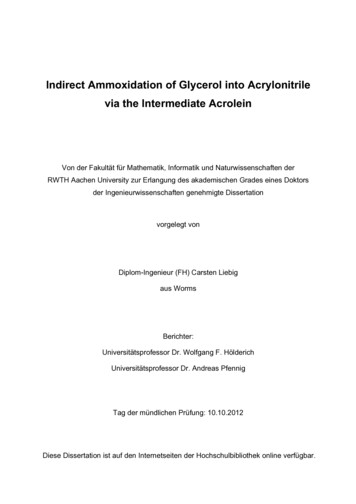
Transcription
Indirect Ammoxidation of Glycerol into Acrylonitrilevia the Intermediate AcroleinVon der Fakultät für Mathematik, Informatik und Naturwissenschaften derRWTH Aachen University zur Erlangung des akademischen Grades eines Doktorsder Ingenieurwissenschaften genehmigte Dissertationvorgelegt vonDiplom-Ingenieur (FH) Carsten Liebigaus WormsBerichter:Universitätsprofessor Dr. Wolfgang F. HölderichUniversitätsprofessor Dr. Andreas PfennigTag der mündlichen Prüfung: 10.10.2012Diese Dissertation ist auf den Internetseiten der Hochschulbibliothek online verfügbar.
This work was carried out between February 2010 and September 2012 within a cotutorial thesis at the Department of Chemical Technology and HeterogeneousCatalysis at RWTH Aachen University, Germany and at the Unité de Catalyse etChimie du Solide, UMR CNRS 8181, at the Université des Sciences et Technologiesde Lille, France.I would like to thank Prof. Dr. Wolfgang Hölderich and Prof. Dr. Sébastien Paul forkindly providing the interesting and challenging research topic, for their critical adviceand inspiration as well as the excellent working conditions in Aachen and Lillerespectively.Thanks to Prof. Dr. Andreas Pfennig and Prof. Dr. Jacques Vedrine for reviewing thisthesis and for accepting their role as referee for this thesis.I am very grateful to the European Union for the financial support of this thesis withinthe Seventh Framework Program (FP7/2007-2013) under grant agreement n 241718EuroBioRef. Especially, I would like to thank Prof. Dr. Franck Dumeignil for hissupport throughout my studies. Furthermore, I owe thanks to Dr. Jean-Luc Dubois ofArkema for the critical discussions and his advices.Moreover, I want to thank Prof. Dr. Gerhard Raabe and Dr. Jacques Kervennal forbeing examiners of this thesis.Furthermore, I wish to thank Dr. Benjamin Katryniok for his continuous support andmany discussions, ideas and advices during my stay in Lille.I would like to thank all technicians in Aachen and Lille for their help - especially ElkeBiener, Heike Bergstein, Noah Avraham, Marianne Nägler, Gerard Cambien, OlivierGardoll and Arnaud Beaurain.Moreover, I would like to thank my colleagues in Aachen and Lille Dr. MoritzVenschott, Kyunghoon Kim, Dr. Raweewan Klaewkla, Dr. Oana Rusu, Dr. MatthiasArend, Yun Chen, Thomas Eschemann, Verena Ritzerfeld, Axel Pyrlik, Anna Matzen,Cyrille Guillon, Jorge Beiramar, Dr. Maryam Safariamin-Karimi, Fangli Jing, Kaewarpha Thavornprasert and Dr. Svetlana Heyte for their help and many fruitfuldiscussions.I owe thanks to my research students Paulo Schmitz, Sebastian Guski, JonasDeitermann and Fabrice Tanguy for their active engagement and commitment in thiswork.Finally, I would like to thank my parents, my sister and my girlfriend Inga for theireverlasting support and encouragement during my studies.
AbstractDue to the depleting reserves of coal, oil and natural gas and to their negative impacton the environment, the humanity is forced to find renewable alternatives to replacethe fossil feedstocks for the production of energy and chemical products. An examplefor an area of application where renewables are already used to substitute fossilfeedstocks is the production of fuels. Biodiesel is one of the most popular biofuelsnowadays. It is produced by transesterification of vegetable oils and fats. In thisprocess, glycerol is formed as a by-product (approximately 10 wt.%). Glycerol is aversatile starting material which has up to 2000 applications. One very promising useof glycerol as starting material would be the dehydration of glycerol into acrolein. Itcould then be further converted into acrylonitrile - one of the most importantmonomers in the polymer production worldwide - by ammoxidation in the presence ofammonia and oxygen over mixed metal oxide catalysts. Today, acrylonitrile isexclusively synthesized from fossil feedstocks like propene and propane on anindustrial scale. Therefore, a process combining the dehydration of glycerol toacrolein and the ammoxidation of the latter to acrylonitrile would be an alternative tothe production processes based on fossil feedstocks. Thus, both reaction steps werestudied separately at first - with focus on the ammoxidation of acrolein - andconnected in a tandem reactor setup finally.For the first step of dehydration of glycerol to acrolein, we used previously optimizedWO3/TiO2 catalysts, while oxide catalysts containing antimony, iron, vanadium andmolybdenum were developed and used for the second ammoxidation step. Especially,the Sb-Fe-O catalysts were found highly selective and the influence of Sb/Fe ratiowas subsequently studied. The presence of a FeSbO4 mixed phase on thesynthesized samples was correlated to a high selectivity to acrylonitrile. Further, anincrease in selectivity to acrylonitrile with the reaction time was observed, which wasexplained by the progressive formation of additional amounts of FeSbO4 over thecatalysts during the reaction. After optimizing the key reaction parameter (reactiontemperature, catalyst amount, NH3/acrolein ratio, O2/acrolein ratio) within a design ofexperiments, both reaction steps were connected in a tandem reactor. A maximumyield in acrylonitrile of 40 % (based on glycerol) was obtained.
Table of Contents1Introduction and Aim of Work . 12Basic Knowledge . 42.1Glycerol . 42.1.1Glycerol Production . 42.1.2Uses of Glycerol . 82.2Acrolein . 122.2.1Acrolein Production. 122.2.2Uses of Acrolein. 152.3Acrylonitrile . 182.3.1Acrylonitrile Production . 182.3.2Uses of Acrylonitrile . 213Scientific State of the Art . 243.1Direct Ammoxidation of Glycerol . 243.2Indirect Ammoxidation of Glycerol via Acrolein . 273.2.1Step I: Dehydration of Glycerol . 283.2.1.1Intermediate Conclusion for the Dehydration of Glycerol . 323.2.2Step II: Ammoxidation of Acrolein. 333.2.2.1Mechanism and Kinetics . 363.2.2.2Intermediate Conclusion for the Ammoxidation of Acrolein . 394Results and Discussion . 414.1Dehydration of Glycerol . 414.1.1Reactor Setup . 414.1.2Characterization. 444.1.2.1Nitrogen Physisorption . 444.1.2.2X-ray Diffraction . 474.1.2.3Temperature Programmed Desorption . 504.1.3Results . 524.1.3.1Catalysts Prepared According to Method I . 524.1.3.2Catalysts Prepared According to Method II . 564.1.3.3Combination of Method I and II . 584.1.3.4Identification of By-products . 594.2Ammoxidation of Acrolein . 604.2.1Reactor Setup . 60I
4.2.2Characterization. 644.2.2.1Antimony Iron Mixed Oxides . 644.2.2.2Antimony Vanadium Mixed Oxides . 764.2.2.3Additional Ammoxidation Catalysts . 844.2.3Results . 924.2.3.1Preliminary Experiments . 924.2.3.2Catalyst Screening . 994.2.3.3Best Catalysts for the Ammoxidation of Acrolein . 1064.2.3.4Design of Experiments . 1074.2.3.5Influence of Water . 1174.2.3.6Long-term Stability . 1214.2.3.7By-Products, Carbon and Mass- balance . 1224.3Indirect Ammoxidation of Glycerol . 1234.3.1Reactor Setup . 1234.3.2Results . 1274.3.2.1Preliminary Experiments . 1274.3.2.2Adjustment of the Residence Time in presence of SbFeO . 1284.3.2.3Best Catalysts for the Ammoxidation of Acrolein . 1314.3.2.4Adjustment of the Residence Time in the presence of MoO3 . 1334.3.2.5Comparison of Crude and Synthetic Glycerol . 1344.3.2.6Long-term Stability . 1364.3.2.7Identification of By-Products . 1375Synopsis . 1385.1Summary . 1385.1.1Dehydration of Glycerol . 1385.1.2Ammoxidation of Acrolein . 1395.1.3Indirect Ammoxidation of Glycerol . 1415.2Outlook . 1436Experimental Section . 1446.1Chemicals . 1446.2Design of Experiments . 1446.3Contact Time . 1446.4Analytics . 1446.4.1Calculation of Conversion and Selectivity. 144II
6.4.2Gas Chromatography . 1456.4.2.1Aachen . 1456.4.2.2Lille . 1466.4.3High-Performance Liquid Chromatography . 1466.4.4Nitrogen Physisorption. 1466.4.5X-Ray Diffraction. 1466.4.6X-Ray Photoelectron Spectroscopy . 1476.4.7NH3 - Temperature Programmed Desorption . 1476.4.8H2 - Temperature Programmed Reduction . 1476.4.9Thermo Gravimetric Analysis. 1476.4.10Inductively Coupled Plasma . 1486.5Preparation Methods . 1486.5.1Catalysts for the Dehydration of Glycerol . 1486.5.1.1Method I: Impregnation Method of Powder in the Slurry . 1486.5.1.2Method II: Impregnation of Extrudates . 1496.5.1.3Method III: Impregnation in a Slurry Followed by Extrusion . 1506.5.2Catalysts for the Ammoxidation of Acrolein . 1516.5.2.1Antimony Iron Mixed Oxides . 1516.5.2.2Antimony Vanadium Mixed Oxides . 1526.5.2.3Additional Catalysts for the Ammoxidation of Acrolein . 1537References . 156III
IV
List of AbbreviationsÅAngstromABSAcrylonitrile Butadiene StyreneACAcroleinACNAcrylonitrileBETSpecific surface area, according to Brunauer, Emmet, TellerDoEDesign of ExperimentsFAMEFatty Acid Methyl EsterHMDAHexamethylenediamineICPInductively Coupled PlasmaMHAMethyl Hydroxythiobutric AcidPAAPhthalic Acid AnhydridePEPolyethylenePLAPolylactic acidPPPolypropyleneSSelectivitySANStyrene AcrylonitrileSOHIOStandard Oil of OhioTGAThermo Gravimetric AnalysisTOSTime on StreamTPDTemperature Programmed DesorptionTPRTemperature Programmed ReductionXConversionXPSX-ray Photoelectron SpectroscopyXRDX-ray DiffractionYYieldV
VI
Introduction and Aim of Work1 Introduction and Aim of WorkOne of the key challenges of the 21st century is to find solutions to ensure asustainable energy supply for the next generations since the depletion of the fossilenergy resources such as oil, gas and coal is ongoing. Nowadays, the energyproduction is mainly based on those fossil feedstocks. The produced energy fractionbased on renewable feedstocks is rather small. Less than 2 % of the world energyconsumption is assured by renewables.[1] However, the world energy consumption isfurther increasing and will follow this trend for the next decades notably due to thegrowth in emerging countries (Figure 1). With this in mind, it is a major task of oursociety to expedite the development of technologies that allow the usage ofrenewable feedstocks - like biomass - in a profitable way for the energy production ingeneral.Figure 1: World energy consumption in million tons oil equivalent.[1]An example for an area of application in which already renewables are used tosubstitute fossil feedstocks is the production of transport fuels such as diesel.The increasing number of the global vehicle fleet from approximately 1 billionnowadays (commercial vehicles and passenger cars) to 1.6 billion by 2030necessitates the development of renewable based fuels as for example biodieselfrom fats and oils by transesterification.[2-4] For example, the European Union has1
Introduction and Aim of Workdefined that until 2020, a 20 % share of energy from renewable sources must bereached which will most probably not be accomplished. This legislation includes amandatory target of 10 % biofuels blended with transport gasoline and diesel.[5] Inorder to achieve those requirements the production of biodiesel (corresponding to thefirst generation) has increased during the last decade.[6] Consequently, theavailability of glycerol has increased as well, since approximately 10 wt.% glycerol isproduced as a by-product of the transesterification process yielding biodiesel of thefirst generation. Estimations indicate that the supply of glycerol will overpass theactual demand by a factor six in 2020.[7] Hence, the glycerol prices will decrease tobe less than 0.20 /kg and due to its various applications it will become an even moreinteresting platform molecule for the industry than it is already nowadays.[8, 9]Another example for the replacement of fossil feedstock by renewables is theproduction of polymers. The polymer industry consumes almost 4 % of the globalcrude oil consumption nowadays.[10] Therefore, a sustainable replacement of thedepleting feedstock for this application is of tremendous importance.Polymers based on renewables can be classified into two groups. On the one hand,research is carried out in order to produce polymers from renewable feedstocks withsimilar properties as fossil feedstock-based polymers. An example is polylactic acid(PLA) that is made of lactic acid which is obtained by fermentation of glucose orstarch.[11] One application of PLA is the production of packaging.[12] Therefore, it canbe used to replace fossil-based polymers like polyethylene (PE) or polypropylene(PP).[11]On the other hand, research is conducted in order to produce already establishedpolymers from renewable sources instead of crude oil for example. One example isacrylonitrile (ACN) which is among the top 50 chemicals produced in the US.[13]Today, propene is mainly used as starting material for the synthesis of ACN. Usually,ACN is utilized in the production of styrene-acrylonitrile (SAN) and acrylonitrilebutadiene-styrene (ABS) resins and nitrile elastomers.[14]2
Introduction and Aim of WorkA process using glycerol as a feedstock that is converted into acrylonitrile would bean alternative to the production processes based on fossil feedstock. Therefore, thisindirect route starting from the renewable feedstock glycerol would illustrate a “green”possibility to produce acrylonitrile.As a part of the EuroBioRef project (European Multilevel Integrated BiorefineryDesign of Sustainable Biomass Processing) - a European project supported withinthe EU’s Seventh Framework Program - the aim of this work is to study theconversion of glycerol into acrylonitrile following an indirect route via the intermediateacrolein (AC). In a first reaction step, glycerol will be dehydrated in the presence ofan acidic catalyst into acrolein. Afterwards, acrolein will be ammoxidized to formacrylonitrile in the presence of oxygen and ammonia over a heterogeneousmulticomponent catalyst. Therefore, both reaction steps were studied first separatelywith a specific focus on the ammoxidation of acrolein into acrylonitrile as thedehydration of glycerol was already studied in the group of Hoelderich withremarkable results which were applied to the first reaction step in this project.[15-20]Thereafter, the indirect ammoxidation of glycerol was studied in tandem reactor mode.Suitable heterogeneous catalysts were prepared, characterized and screened fortheir catalytic performance for each reaction step in continuous plug flow fixed-bedreactors in the gaseous phase. Furthermore, the influence of different reactionparameters on the catalytic performance was studied for the second reaction step.3
Basic Knowledge2 Basic Knowledge2.1 GlycerolGlycerol is the simplest trihydric alcohol and has been a well-known chemical sinceits discovery by the Swedish chemist Carl Wilhelm Scheele in 1783. The name“glycerol” is deduced from the Greek word “glykos” which means “sweet”.[21] It is thecarbon backbone which can be found in all natural fats and oils. Furthermore, it is animportant intermediate in the metabolism of living organisms.[7]2.1.1 Glycerol ProductionUntil the 1940s, glycerol was mainly obtained as a byproduct in the production ofsoaps from triglycerides as shown in Figure 2. After the introduction of syntheticsurfactants the production of soaps based on oils and fats became less profitable.Additionally, the glycerol consumption increased due to its application in the tobaccoand food industry as a humectant and in the cosmetic industry as well as in theproduction of explosives.[22]OR1COOCH2R2COOCHR3COCH2 3 NaOHR1COONaHOR2COONa HOR3COONaHOCH2CHCH2Figure 2: Glycerol as a byproduct in the production of soaps.Hence, it was necessary to develop synthetic production processes to satisfy theupcoming demand in glycerol. The first commercial glycerol production processbased on fossil feedstock was the hydrolysis of epichlorohydrin which was firstlyapplied by I.G. Farben in Germany in 1943.[23]4
Basic Knowledge Cl2O- HClClCl- CaCl2, - 2 H2O H2OClO HOCl, Ca(OH)2HOClO- HClHOOHO H2OHOHOOHOHFigure 3: Classical production route of glycerol from fossil feedstock.As depicted in Figure 3, propylene is used as a feedstock. In a first reaction step, thepropylene reacts with chlorine to form allyl chloride which afterwards is converted toepichlorohdrine in the presence of hypochlorous acid and calcium hydroxide. Theepichlorohydrin is then hydrolyzed to glycerol.Another process based on allyl alcohol was operated by Degussa and Shell forexample (Figure 4).HO H2O2[Cat.]- H2OOHO H2OHOOHOHFigure 4: Glycerol production from allyl alcohol.Propylene is firstly epoxidized to propylene oxide. Thereafter, the propylene oxide isisomerized to allyl alcohol. Allyl alcohol is then epoxydized with hydrogen peroxideover tungsten-VI-oxide catalysts to glycidol which is finally hydrolyzed to glycerol.Instead of hydrogen peroxide, peracetic acid can be used as well for the epoxidationof allyl alcohol.[7] In contrast to the process based on epichlorohydrin, the conversionof allyl alcohol into glycerol has the advantage that no chlorine is involved whichmakes the process more environmentally friendly.5
Basic KnowledgeDue to the rapidly increasing commercial production of fats and oils over the last 40years, glycerol is more and more obtained as a byproduct – e.g. of the saponificationor the hydrolysis - instead of being synthesized from fossil feedstocks.[24] Additionally,the transesterification of fats and oils to fatty acid methyl esters (FAME) and glyceroldepicted in Figure 5 has increased since the beginning of the 21st century - especiallyin Europe - due to the rising demand for biodiesel.OR1COOCH2R2COOCHR3COCH2 3 CH3OH[Cat.]R1COOCH3HOCH2R2COOCH3 HOCHR3COOCH3HOCH2Figure 5: Glycerol as byproduct in the transesterification of fatty acids with methanol.Figure 6 shows the scheme of a homogeneously catalyzed biodiesel processdeveloped by Lurgi. The process consists of two mixer/settler reactors wheremixtures of methanol, oil and catalyst (e.g. NaOH or the methanolate NaOCH3) areintensively mixed followed by a phase separation. Afterwards, the products arepurified by distillation.[25, 26] Conversions higher than 99.5 % are achieved. The mainadvantages of this process are high catalyst activity and the moderate reactionconditions.[27] However, the homogenously catalyzed transesterification entailsdrawbacks also. The formation of salts caused by the neutralization of the basiccatalyst and the necessarily high purity of the oil feed (the free fatty acid [FFA]content must not be higher than 0.5 % in order to avoid the formation of soaps) arethe major drawbacks.[28] Glycerol is obtained with 85 % purity and contains besides10 % water, 5 % salts. Therefore, in most cases an additional distillation is necessaryto achieve the high purities needed for the downstream processes.[8]6
Basic KnowledgeHClMixer/Settler IMixer/Settler tionR-2WaterRemovalFigure 6: Biodiesel process developed by Lurgi.R-1BiodieselWashingCrude Glycerol![27]A possibility to overcome the aforementioned drawback of salt formation would betransesterification over heterogeneous catalysts. Today, only one process reachedthe commercial level. In the so-called Esterfip-H process, developed by the InstitutFrançais du Pétrole (IFP) and commercialized by Axens, vegetable oil is converted toFAME over zinc alumina catalysts in two fixed bed reactors.[29-31]The glycerol is separated between the two reactors and purities over 98 % areachieved.[32] Total conversions above 99.2 % are obtained which makes this processcomparable to the homogenously catalyzed process by Lurgi. The necessity of highlypurified oil (free fatty acid content less than 0.5 %) has not been overcome by thisprocess either. The used catalysts are sensitive to FFAs as the synthesis of zinccontaining soaps is possible which makes an expensive purification of the oil feedindispensible.However, the results published by Rußbueldt et al. showed that by utilizing rare earthmetal oxides (preferably La on tetragonal ZrO2) as catalysts for the transesterificationit is possible to use oils with high FFA content as feedstock without having to dealwith catalyst saponification as observed in the Esterfip-H process.[33-35]7
Basic Knowledge2.1.2 Uses of GlycerolNowadays, glycerol has more than 2000 different possible fields of application.[7] Thisfact highlights its incredible potential as a renewable feedstock for the chemicalindustry. Figure 7 gives an overview of the distribution of glycerol consumption bydifferent application %&Triace1n&10%&Others&11%&Figure 7: Distribution of the glycerol consumption by different application fields.[22]Due to its properties as humectant - it absorbs and retains water - glycerol is used bythe food and tobacco industry. Additionally, it is added to antifreeze solutions that areused in automobile radiators for instance (Table 1).Table 1: Characteristics of water solutions of glycerol.8Glycerol ConcentrationFreezing Point[wt.-%][ C]20- 5.040- 15.660- 34.0[36]
Basic KnowledgeBesides the application as an additive in the food industry for example, glycerol ispotentially also a versatile platform molecule for the synthesis of several value addedproducts. An overview is given in Figure 8.Figure 8: Possible applications of glycerol as a feedstock.[37]A promising example is the catalytic hydrogenolysis to 1,2 propylene glycol which isused in tooth paste, cosmetics or polyurethanes. Archer Daniels Midland (ADM)started a new 100.000 tonnes per year plant in March 2011. The glycerol obtained byADM’s biodiesel production will be purified and then converted into propylene glycolin the new plant.[37, 38]9
Basic KnowledgeThe first derivative of glycerol that reached commercial standard was trinitroglycerineadsorbed to silica gel (Dynamite) in 1866.[23]OH 3 HNO3/H2SO4OH- 3 H2OOHONO2ONO2ONO2Figure 9: Synthesis of trinitroglycerine from glycerol.As depicted in Figure 9, glycerol is converted with a mixture of nitric acid and sulfuricacid to trinitroglycerine. Nowadays, the synthesis of trinitroglycerine still accounts forabout 4 % of the total glycerol consumption.[23, 39]OHOHHO 2 HClOH- 2 H2OClCl ClOH NaOH- NaCl, - H2OOClClFigure 10: Two step Epicerol process for the production of epichlorohydrine from glycerol.Figure 10 shows another economically and environmentally advantageous utilizationof glycerol. Epichlorohydrine, originally being used for example as a feedstock for theglycerol production in the middle of the last century as shown in section 2.1.1, isproduced by a two step process. The process starting from glycerol has severaladvantages compared to the synthesis from propene:10 Reduction of chlorinated waste Non-toxic or non-flammable starting material Reduced process steps from four to two Main product 1,3-dichlorohydrine 1,3-dichlorohydrine reacts 10 times faster than 1,2-dichlorohydrine
Basic KnowledgeEpichlorohydrine is used in the production of epoxy resins, two-component adhesivesand as a solvent for cellulose esters and ethers.[37, 40] This process is carried out on acommercial scale by Solvay in France and by DOW in China.OOHnO n HOOH- n H2OOO OOO PAA- H2Ocross-linkingOHnFigure 11: Synthesis of alkyd resins from glycerol and phthalic acid anhydride.Glycerol is also utilized as a starting material for the production of alkyd resins . Alkydresins are applied as raw materials in the paint and varnish industry. In a first step, afusible resin is formed with approximately equimolar ratios of glycerol and phthalicacid anhydride (PAA). Afterwards, this resin is cross-linked with excess PAA to formthe non-fusible alkyd resin.[23]OHOHOOH- 2 H2OFigure 12: Synthesis of acrolein from glycerol.A reaction that has been studied intensively over the last years is the dehydration ofglycerol to acrolein over different acidic catalysts.[8,15, 16, 41, 42]The dehydration ofglycerol to acrolein will be discussed in detail in section 3.2.1.11
Basic Knowledge2.2 AcroleinAcrolein, the simplest unsaturated aldehyde, is a colorless and toxic liquid. Its nameis derived from the Latin word
RWTH Aachen University zur Erlangung des akademischen Grades eines Doktors der Ingenieurwissenschaften genehmigte Dissertation vorgelegt von Diplom-Ingenieur (FH) Carsten Liebig aus Worms Berichter: Universitätsprofessor Dr. Wolfgang F. Hölderich Universitätsprofessor Dr. Andreas Pfennig Tag der mündlichen Prüfung: 10.10.2012