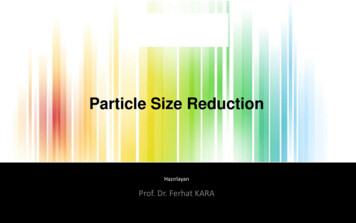
Transcription
Particle Size ReductionHazırlayanProf. Dr. Ferhat KARA
Particle Size ReductionAims of Particle Size ReductionSome of the most common reasons for reducing particle size areto; create appropriate particle sizes improve material blending and prevent segregation increase the material’s surface area liberate impurities reduce porosity of the particles modify shape of the particles
Particle Size ReductionSize Reduction Comminution, a term used for the techniques for reducingparticles size in ceramics processing, delivering mechanicalenergy in various forms. Two general types of communition operations are distinguished:-Crushing-Grinding
Particle Size ReductionSize Reduction Crushing – the reduction of large lumps from the mine to smallersizes (from cm size to 1-2mm) for subsequent further reduction.Several stages may be required (e.g. primary crushing, secondarycrushing)
Particle Size ReductionSize ReductionCrushing equipmentsJaw crusherRotary crusherCrushing rollersHammer mill
Particle Size ReductionSize ReductionGrinding (Milling) refers to the operation of reducing the smallpieces after crushing to a fine powder. Grinding is accomplishedby abrasion and impact of the crushed mineral by the free motionof unconnected hard media such as balls, pebbles, or rods. Ball MillsStirred Mills (Attrition Mills)Vibratory MillsJet MillsOthers
Particle Size ReductionOperating Variables Size, type and angular velocity of the mill Size and type of media Size of feed Loading of the mill Physical characteristics of the media Agglomeration of feed and product Viscosity Temperature Milling atmoshpere
Particle Size ReductionMilling PerformanceThe choiceof a millmay depend ultimate capital cost, mineral properties, capacity, reduction ratio and final size requirement, wet or dry product, continuous or batch operation, period of a milling cycle,on
Particle Size ReductionStrength of ParticlesWhen the particle size is decreased, energy required tofracture the particle increases according to Griffith equation. strengthE Young's modulus the energy required to break the bonds associated with the unitarea of surfacec crack lengthThus, it is easier to reduce the size of the big particles whichcontain larger cracks compared to the small ones.
Particle Size ReductionParticle Size Reduction with TimeD/DoD/DoD0D0tlog tDo initial particle sizeD particle size changing depending on the milling time
Particle Size ReductionGrinding MediaThere are several types of grinding media generally used inthe mills. Some examples are;SteelTungsten carbideAluminaGlassFlintstonesSilicon nitride
Particle Size ReductionGrinding MediaSelection of grinding media depends upon several factors,some of which are interrelated;1.2.3.4.5.Specific gravityInitial feed sizeFinal particle onAvailabilityCostsConsistency in size
Particle Size ReductionGrinding Media Commonly Used inTraditional Ceramic IndustrySteelTungsten carbideAluminaGlassFlintstonesSilicon nitride
Particle Size ReductionBall MillingBall milling is the most widely used particle size reduction technique.The ceramic particles move between the much larger media andbetween the media and the wall of the mill and are effectively brokeninto successively smaller particles.
Particle Size ReductionBall Milling
Particle Size ReductionOperating Variables Size and angular velocity of the mill Size ratio between the balls and the particles to be ground Loading of the mill (Volume of the balls and the powder in the mill) Physical characteristics of the media Agglomeration of feed and product Viscosity in wet milling
Particle Size ReductionOperating Variables: Ball MillingThe critical angular frequency WCr (Hz) causing centrifuging isWCr 0.5xR-1/2R radius of the mill (meter)The mill is normally operated at WCr all-mill-critical-speed
Particle Size ReductionOperating Variables: Ball ill-critical-speed
Particle Size ReductionOperating Variables: Ball MillingBall size / particle size 25Ball sizeParticle size
Particle Size ReductionOperating Variables: Ball MillingLoading of the mill (Mill charge): Typically the media charge is about50 % of the volume of the mill and powder or slurry is added to slightlyexceed the void spaces in the media. This combination provides a goodcompromise between grinding efficiency and rate of wear of the media andlining. 50 vol % grinding media (balls) In wet willing, 30-40 % slurry (slurry to slightly exceed the voidspaces between the balls) In dry milling, 25 vol% urces/ball-mill-loading-dry-milling
Particle Size ReductionOperating Variables: Ball Milling 50 vol % grinding media (balls) In wet willing, 30-40 % slurry (slurry to slightly exceed the void spacesbetween the balls) In dry milling, 25 vol% powderViscosity of the slurry isimportantWet ources/ball-mill-loading-dry-milling
Particle Size ReductionOperating Variables: Ball MillingLoading of the mill (Mill charge):Dry ources/ball-mill-loading-dry-milling
Particle Size ReductionOperating Variables: Ball MillingPhysical properties of Silica2.2010WC-Co14-1514Steel7.807 Alumina is widely used in traditional ceramicindustry. Steel is cheap but contamination is a problem.Used in cement esources/ball-mill-loading-dry-milling
Industrial ball millsDiscontinuousContinuous
Industrial ball mills: LiningLining materials: Alumina, rubber
Milling PerformanceThe mill selected must be used efficiently to commensurate withwear and maintainance expense. We can gain insight into factorseffecting milling performance by examining the equation givenbelow.Particles generated Media collosions * Particle impacts * Particles brokenTimeTimeCollisionsImpact
Milling PerformanceParticles generatedTimeMedia collisionsTimeParticle impactsCollisionsParticles brokenImpacts Fractured particles amount , millingefficiency size , media collosion frequency , Mediakinetic energy of the impacts Catching a particle at the impact zone when cylindirical ball are usedTime , ease of fracturing https://www.youtube.com/watch?v L6sgGXXYdEU
Particle Size ReductionAttrition MillsIn attrition mills, the milling occurs by thestirring action of a vertical drive shaft withhorizontal arms.The shaft is rotated at high speeds.The motion causes an intensive movement betweenthe balls and results in an intensive diminution.In many cases, smaller particle sizes may beachieved by attrition mills than that by ball mills.
Particle Size ReductionAttrition MillsFeed material size is generally 50 μm.Solid content of the slurry, 30%-70%Size of the spherical grinding media, 0.3-5 mm
Particle Size ReductionAttrition MillsImpact RandomShearmovement are spinning in different rotation and,therefore, exerting shearing forces on the adjacent slurry.
Particle Size ReductionAttrition MillsADVANTAGES Fine homogeneous particles– Particles 0.5 μm can be obtained.Short grinding timesTemperature controlLow power consumptionLIMITATIONS Used most efficiently for fine grinding onlySmall feed size
Vibromill
Jet millA jet mill grinds materials by using a high speed jet of compressed air or inert gas to impactparticles into each otherFinal particle size:down to 0.5 microns
Size Reduction Crushing equipments Jaw crusher Rotary crusher Crushing rollers Hammer mill Particle Size Reduction. Size Reduction Grinding (Milling) refers to the operation of reducing the small pieces after crushing to a fine powder. Grinding is accomplished by abrasion and impact of the crushed mineral by the free motion of unconnected hard media such as balls, pebbles, or rods. Ball Mills .