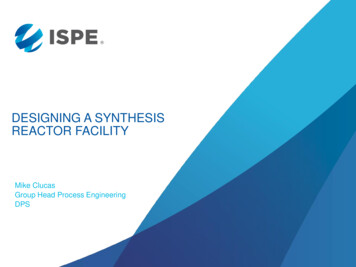
Transcription
DESIGNING A SYNTHESISREACTOR FACILITYMike ClucasGroup Head Process EngineeringDPS
THE PROJECTFRAMING THE DESIGN
A qualified, commercial scale fully automated SynthesisFacility The facility is based on using a modified Neutsche Filter /Dryer as a chemical synthesis reactor This project has delivered a successful novel approach forcommercial scale manufacture of the product in a safe, fullyautomated multiproduct facilityConnectingPharmaceuticalKnowledgeispe.org
Project INDUSTRIALISEKnowledgeispe.org
THE SAFETY DRIVERNEW SYNTHESIS PLANT
Facility SafetyA Basis Of Safety ApproachHaving safety as a design driver Preliminary Hazard Analysis (PHA) HAZOP Containment Ergonomics ATEX Report and Drawings LOPA SILConnectingPharmaceuticalKnowledgeispe.org
Basis of SafetyCHEMICALStep 1HAZARDABCDEStep 2Reagent AFlammableReagent BCorrosiveReagent CStep 3Acute Toxicity, Irritant, SensitiserAcute ToxicityFSensitiser, Mutagen, Carcinogen,Reproductive ToxinGConnectingPharmaceuticalKnowledgeispe.org
ChemicalOpen andmanual solventtransfersABCHard Pipedautomatedtransfers fromTank FarmDFOpen solventdrum pumpingPPE & RPEGHContained drumboothHard piped fixedIBC’sAutomated transfersIOpen reagentdispensingPPE & RPEReagent AReagent BContained reagentaddition systemReagent C8ConnectingPharmaceuticalKnowledgeispe.org
Powder Sampling & Liquid HandlingNew SynthesisNew SynthesisAutomated& containedvesselsamplerContainedpowdertransfers ConnectingPharmaceuticalAutomated solvent transfer systemSophisticated instrumentation foraccurate & repeatable transfersFully contained chargingKnowledge9ispe.org
Facility SafetyA Basis Of Safety ApproachHaving safety as a design driver Fully Contained Charging, Bulk solvent and Liquid Waste Handling, Vent Header Design Recipe Controlled Vacuum swing Inertion and Collected, Abated Venting. Contained Potent Dispensing and Charging Fully contained, long term technically sealed solvent transfer and collection systems. Fully ATEX, PED and FM Global Compliance Relief Sizing to g
THE INDUSTRIALISATION DRIVERNEW SYNTHESIS PLANT
Basis of DesignDesign of aSynthesis FacilitySafeProcess1 week batchcycle timeMultiproductand l280lbatch reactorConsistent andincreased yieldKnowledgeispe.org
Early DesignPDF’s, MassBalance and BatchCycle calculationEngagementwith FacilityteamProof of Concept –Key ech Transferand VendorTrialsEquipmentSelection-Neutsche FilterKnowledgeispe.org
THE REACTORNEW SYNTHESIS PLANT
New SynthesisExisting SynthesisControlledagitationPressure ratedhastelloy vesselwith pressurecontrolControlledheating & cooling40 um filterbase ConnectingAutomated productdischargeOperations take place in single vesselAutomated CIP cycleAutomated filter base loweringNo lifting or manual handling requiredPharmaceuticalKnowledgeispe.org
Reactor OCESSKnowledgeispe.org
Reactor ceuticalFLEXIBILITYKnowledgeINNOVATIONispe.org
THE NEW FACILITY
ConnectingPharmaceuticalKnowledgeispe.org19
Thank YouStephen Judd , Lead Process EngineerMike Clucas, Group Head Process Engineeringwww.dpsgroupglobal.com
A qualified, commercial scale fully automated Synthesis Facility The facility is based on using a modified Neutsche Filter / Dryer as a chemical synthesis reactor This project has delivered a successful novel approach for commercial scale manufacture of the product in a safe, fully automated multiproduct facility