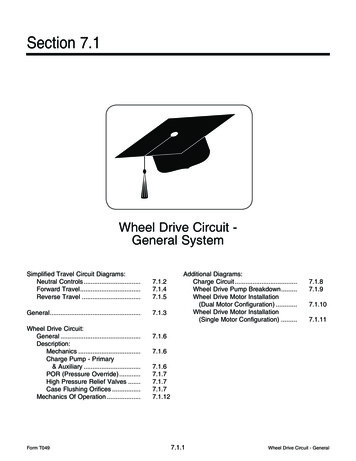
Transcription
Section 7.1Wheel Drive Circuit General SystemSimplified Travel Circuit Diagrams:Neutral Controls .Forward Travel.Reverse Travel .7.1.27.1.47.1.5General.7.1.3Wheel Drive Circuit:General .Description:Mechanics .Charge Pump - Primary& Auxiliary .POR (Pressure Override) .High Pressure Relief Valves .Case Flushing Orifices .Mechanics Of Operation .Form T049Additional Diagrams:Charge Circuit .Wheel Drive Pump Breakdown.Wheel Drive Motor Installation(Dual Motor Configuration) .Wheel Drive Motor Installation(Single Motor Configuration) 1.77.1.127.1.1Wheel Drive Circuit - General
00735Figure 1: Simplified Travel Circuit Diagram - NEUTRAL CONTROLS (Dual Wheel Drive Motors)Wheel Drive Circuit - General7.1.2Form T049
General7) 14-port rotary manifold for 360 continuousrotation swing. In the wheel drive circuit itprovides the hydrostatic link to the wheel drivemotors, brake connections to the axles, andshift connections to the transfer case.(See Figures 1, 2 & 3)The wheel drive, or travel circuit, is a closed loophydrostatic system made up of the following maincomponents:1) 110 gal. (416 litre) hydraulic oil tank forstorage and cooling of the hydraulic oil.See Section 2.2 in this manual for importantinformation on the hydraulic tank and itscomponents.8) Rexroth AA6VM160 variable displacementwheel drive motor(s). Standard configuration isdual motors matched to an auto-shift gearbox.A single motor installation matched to a2-speed gearbox is optional.The speed and drawbar pull of the machineis varied by changing the displacement of thewheel drive motor(s). In high range (fast speedless drawbar) the motor(s) are at minimumdisplacement. If the machine is in low range(low speed high drawbar) the motor(s) are atmaximum displacement.2) 100-mesh suction strainers.3) Suction line shut-off valve.4) Rexroth AA4VG125/3.2 series variabledisplacement, over-center, axial piston wheeldrive pump.5) Charge pump piggy-back mounted to thewheel drive pump. The charge pump provides30 GPM (114 litre) of flow at 400 PSI(2,76 Mpa). Charge pressure is controlled bythe charge pressure manifold/filter assembly(Ref #6). The purpose of the charge pumpis to provide make-up oil for the closed loophydrostatic travel circuit. Flushing orifices inthe pump and motors (and natural internalleakage) allow a small amount of oil to bleedfrom the hydrostatic loop. This leakage isreplenished by the charge pump. A filter in thecharge pressure manifold/filter assembly(Ref #6) cleans the charge oil before it entersthe hydrostatic loop.The dual motor configuration has an automaticshift mode that will seek the best displacementfor the ground condition and machine load.9) High capacity oil cooler with a 120 -140 F(49 -60 C) thermal bypass and 50 psi(3,45 kPa) back pressure bypass.10/11) Return and case drain filters in the hydraulictank. See Section 2.2 in this manual forimportant information on the hydraulic tankand its components.6) The charge pressure manifold/filter assemblycontains the charge pressure relief and thecharge oil filter. A sequence cartridge isused because the downstream pressure doesnot effect the valve pressure setting. Anyincrease . . . . . . . . . . . . . . . . . . of pressuredownstream will not be additive to the chargepressure. This makes the charge pressuresetting more constant. Charge pressure alsoprovides stroke control for the wheel drivepump, swing brake release pressure, and pilotpressure at the pilot pressure manifold.Form T0497.1.3Wheel Drive Circuit - General
00736Figure 2: Simplified Travel Circuit Diagram - FORWARD TRAVEL (Dual Wheel Drive Motors)Wheel Drive Circuit - General7.1.4Form T049
00737Figure 3: Simplified Travel Circuit Diagram - REVERSE TRAVEL (Dual Wheel Drive Motors)Form T0497.1.5Wheel Drive Circuit - General
Wheel Drive CircuitMechanicsGeneralThe machine uses a dedicated pump and a singlespeed, auto-shifting gearbox powered by dualhydraulic motors for the wheel drive (travel) circuit.There is an optional drive for the Feller Buncherconfigurations which uses a 2-speed gearbox anda single motor.The circuit type is a closed loop hydrostatic system.The directional changes in machine movement arecontrolled by swiveling the pump rotating groupfrom a centered, neutral position to either forwardor reverse. This is controlled by an electrical signalsent from a travel pedal actuated by the operator.DescriptionA Rexroth 125cc AA4VG3.2 series pump is usedon all configurations. This pump are referred to asa over-center pump. This means that the rotarygroup, which provides oil flow around the hydrostaticloop, can travel over-center on either side of theneutral swash plate position. This allows oil flow tobe reversed in the hydrostatic loop. The directionof machine travel is controlled by the angle of thepump swash plate to either side of neutral.The 125cc wheel drive pump is driven through agearbox with a 1.38 speed increaser. Doing soallows the top engine RPM to be reduced from2200 to 1900 (which is the peak torque level of theCummins C8.3-C260 engine). This is being done toreduce the fuel required and reduce the noise levelin the cab. Also, the fuel tank is now in the frontframe and the implement valves have been movedbehind the cab for easier service access.One or two Rexroth AA6VE series variabledisplacement motors which are mated to either asingle or 2-speed gearbox. The motors are set fordifferent displacements to optimize the performanceof the machine. These motors also utilize a 2speed auto-shift mechanism as well as having caseflushing orifices installed.Wheel Drive Circuit - GeneralWhen the operator activates the travel pedal forthe forward direction, an electrical signal is sentto the pump controller via the IQAN digital controlsystem.The electrical signal activates the solenoid on thepump controller, which in turn moves a small controlspool that allows command oil to the pump servo.The pump servo is connected directly to the swashplate in the pump and when it is shifted, strokes upthe pump in the desired direction and forces thepump to produce flow to the motors via the rotarymanifold. When changing directions, the swashplate goes to the opposite side of neutral to changethe direction of oil flow.The oil returning from the motors is then routedthrough the rotary manifold to the opposite workport on the pump. This oil is then reused by thepump and sent back down to the motors.Charge PumpBecause of the cooling requirements of the wheeldrive circuit, it is necessary to push oil throughflushing circuits to keep the pump and motorscool. The charge pump provide the make-up oilfor cooling the closed loop hydrostatic pump/motorsand to provide pump control pressure. The pumpand motors have a natural manufacturing leakagewhich cannot be eliminated. This leakage must bemade up or the closed loop system would run dry ofoil. The charge system continually feeds oil into thelow pressure side of the closed hydrostatic loop.The maximum pressure setting of the charge circuitis regulated by a charge sequence valve locatedon the hydraulic tank support. Charge pressureis set at 400 PSI (2,76 Mpa) at 1500 RPM with ascrew-type adjustment cartridge. Charge pressurealso is used to release the swing brake, supply thepilot pressure manifold, and as make-up oil for theimplement valve to prevent cavitation.7.1.6Form T049
POR (Pressure Override)oil and component damage would occur.The pressure override valve is unique in that it canlimit the maximum allowed pump pressure withoutputting high pressure oil over a relief. See Figure5.When the machine encounters a condition wherethe drive pressure starts to exceed the maximumsetting, the POR valve senses this. The POR valvethen dumps the command oil that controls the pumpservo to case. This allows the swash plate to moveback towards the neutral position and reduce thepump flow to an amount that is enough to maintainthe maximum allowed pressure.The POR valve is adjustable and is set at 6000 PSI(41,4 Mpa) at 1500 RPM. See Section 7.2 in thismanual for adjustment procedures.High Pressure Relief ValvesThe high pressure reliefs perform two importantfunctions:1) Prevent system or machine damage byventing oil from the hydrostatic loop should themachine stall against an immovable object. Inthis situation, a pressure spike is created inthe circuit which could damage components.The high pressure reliefs sense this pressurespike and, if it exceeds the relief setting, ventsoil from the hydrostatic loop into the chargesystem. This allows the pressure spike todissipate without causing damage.Case Flushing OrificesBoth the pump and motors are equipped with caseflushing orifices. The purpose of these orifices is tohelp keep the hydrostatic loop cool.Hot oil in the hydrostatic loop is vented through thecase flushing orifices into the case drains and thenrouted through the oil cooler. The vented loop oil isreplaced by cool charge oil. This is very important,overheating would occur without the constantremoval and replacement of a small amount of loopoil.Pump Case Flushing OrificeThe pump case flushing orifice is located in the headof the pump and is part of the charge pressure spikerelief. The charge spike relief protects the chargeoil circuit from high pressure spikes.The charge pressure spike relief is adjustable and isset at 490 PSI (3,8 Mpa) at 1500 RPM. See Section7.2 in this manual for adjustment procedures.Motor Case Flushing OrificeThe motor case flushing orifice is located in thecontrol head of the motor.Venting oil through a high pressure relief alsogenerates an excessive amount of heat, so it isimportant that they are adjusted properly. Thehigh pressure reliefs are like a safety relief andare seldom active in a properly designed andadjusted circuit.The high pressure reliefs are adjustable andare set at 6400 PSI (44,1 Mpa) at 1500 RPM.See Section 7.2 in this manual for adjustmentprocedures.2) A high pressure relief, when located on thelow pressure side of the hydrostatic loop, alsoacts as a check valve to allow charge oil toreplenish the hydrostatic loop oil volume. Thisis required because of internal leakage in thepump and motors. If the leakage oil is notreplaced, the hydrostatic loop would run low onForm T0497.1.7Wheel Drive Circuit - General
Charge pressure manifold/filter assembly located onthe hydraulic tank support.Charge pressure is set to400 PSI (2,8 Mpa) at 1500RPM.30 GPM (114 litre)charge pump.Provides charge oilflow for cooling thehydrostatic drivecircuit (flushingorifices) and forimplement valvemake-up oil.00738Figure 4: Charge Circuit DiagramWheel Drive Circuit - General7.1.8Form T049
Pump Controller. Controlsthe pump’s swash plateangle for directional control.High Pressure Relief. Clips highpressure spikes that the PORrelief cannot react to.Pressure Override Relief(POR). Primary highpressure relief for thetravel circuit.HighPressureRelief00739Figure 5: Wheel Drive Pump BreakdownForm T0497.1.9Wheel Drive Circuit - General
Superior SingleSpeed GearboxFrontRexroth AA6VM160Wheel Drive Motor,S/N# tag stamped5652-004-031/002.160cc Full StrokeRearRexroth AA6VM160Wheel Drive Motor,S/N# tag stamped5652-004-031.Front 031/002 Motor0-160ccRear 031 Motor85-160cc160cc Full Stroke85cc Start0cc StartShift Pressure4000 PSI (27,6 Mpa)Shift Pressure4400 PSI (30,3 Mpa)Wheel Drive Motors & Gearbox (Dual Motor Configuration)Dual wheel drive motor configurations use dual Rexroth axial piston drive motors boltedto a Superior single speed gear reduction box. This motor/gearbox combination can belocated in the rear frame. The front and rear motors are different from each other in startingdisplacements and shift pressure settings. It is very important to replace the motor back withthe same type if one should have to be replaced or removed.IMPORTANT: The front motor S/N# tags are all stamped 5652-004-031/002 and the rearmotor S/N# tags are all stamped 5652-004-031.00599Figure 6: Wheel Drive Motor Installation (Dual Motor Configuration)(Typical)Wheel Drive Circuit - General7.1.10Form T049
Rexroth AA6VM160Wheel Drive MotorN.A.F. VG652-Speed GearboxWheel Drive Motor & Gearbox (Single Motor Configuration)The TB600 configurations are equipped with a single Rexroth axial piston drive motor boltedto a NAF 2-speed gear reduction box. This motor/gearbox combination is also located in therear frame.00608Figure 7: Wheel Drive Motor Installation (Single Motor Configuration)(Typical)Form T0497.1.11Wheel Drive Circuit - General
Mechanics Of OperationHydraulic MotorShift “ON/OFF”Oil flow is controlled by engine speed or RPM ofthe pump. The wheel drive motor(s), being drivenby the pump, change displacement automaticallydepending on the drawbar requirements.In a no load situation, the front motor (031/002) isset at 0cc displacement and the rear motor (031) isset at a minimum displacement of 85cc. When themachine starts to move and the pressure reaches4000 PSI (27,6 Mpa) the front motor begins toshift. It will go from 0cc displacement all the wayto the maximum displacement of 160cc. In thiscondition, when the pressure required to move theload reaches 4400 PSI (30,3 Mpa), the rear motorstarts to shift off its minimum displacement of 85cc.It is likely, at this load requirement, that you will notsee over 4500 PSI (27,6 Mpa) on the gauge for thefollowing reason:With the flow produced by the 125cc wheeldrive pump at 1900 RPM feeding two 160ccmotors, it would take more than 260 HP toreach the pump POR setting of 6000 PSI(41,4 Mpa).ParkingBrakeAxle Lock“ON/OFF”00396Figure 8: Auxiliary Rocker Switch Bank #2(Wheel Drive Function Switches)When maximum drawbar is required for a toughpull, a rocker switch on the dash can be used to lockthe wheel drive motor(s) in maximum displacement(low speed). See Figure 8.Because of the HP requirement, it is very importantto back off on the foot pedal to maintain engineRPM when a tough pull is encountered. By backingoff on the pedal, the displacement of the pump isreduced allowing the engine to maintain its RPMwhile holding pressure to keep moving the load atthe sacrifice of speed. The reason it is so importantto maintain engine RPM is because when theengine is slowing under heavy load there is moreheat being generated and without RPM the enginefan and water pump slow down, not giving thecooling efficiencies required.Wheel Drive Circuit - General7.1.12Form T049
THIS PAGE LEFT BLANK FOR NOTESForm T0497.1.13Wheel Drive Circuit - General
Section 7.2Wheel Drive Circuit Tests & AdjustmentsSafety Information . . . . . . . . . . . . . . . . . . . . . . . . . . . . . . . . . . . . . . . .7.2.2Tools Required . . . . . . . . . . . . . . . . . . . . . . . . . . . . . . . . . . . . . . . . . .7.2.2Wheel Drive Pump:Wheel Drive Charge Pressure . . . . . . . . . . . . . . . . . . . . . . . . . . . .Wheel Drive Pump Directional Relief Pressure . . . . . . . . . . . . . . .Wheel Drive Pump POR Pressure . . . . . . . . . . . . . . . . . . . . . . . . .Wheel Drive Pump Null . . . . . . . . . . . . . . . . . . . . . . . . . . . . . . . . .Wheel Drive Pump Case Drain Pressure . . . . . . . . . . . . . . . . . . . .7.2.37.2.57.2.77.2.97.2.11Wheel Drive Motor:Wheel Drive Motor Begin Of Stroke . . . . . . . . . . . . . . . . . . . . . . . .Wheel Drive Motor Case Drain Pressure . . . . . . . . . . . . . . . . . . . .Wheel Drive Motor Case Drain Flow . . . . . . . . . . . . . . . . . . . . . . .MAX Displacement Lock Signal Pressure(Hydraulic motor shift signal pressure in singlewheel drive motor configurations) . . . . . . . . . . . . . . . . . . . . . . .Form T0507.2.17.2.127.2.157.2.177.2.18Wheel Drive Circuit - Tests & Adjustments
Safety informationTools Required You must read and understand the warningsand basic safety rules, found in Group-1 of theOperation & Maintenance manual, beforeperforming any operation, test or adjustmentprocedures. 00015Diesel exhaust fumes contain elements that arehazardous to your health. Always run engine in awell ventilated area. If in an enclosed space, ventexhaust to the outside.Tachometer0 - 60 psi (0 - 1000 kPa) pressure gauge0 - 600 psi (0 - 5 Mpa) pressure gauge0 - 6000 psi (0 - 50 Mpa) pressure gauge0 - 10,000 psi (0 - 80 Mpa) pressure gauge9/16”, 5/8”, 11/16”, 3/4”, 7/8”, 13/16”, 15/16”,1-1/4”, & 1-3/8” wrenches5/32” & 1/4” allen wrenches10mm, 13mm, 17mm, 24mm wrenches3mm, 4mm, 5mm, 8mm allen wrenches(2) PN# 15869, TIMBCO quick-coupleadapterPN# 16031, #4 ORS plugPN# 16032, #8 ORS plugPN# 15176, #4 ORS run teeGauge test hose(2) Gauge test hose w/#4 JICF ends#8 test hose w/#8 ORSF ends24” (61cm) jumper hose w/#4 JICM ends(2) #6 ORBM - #4 JICM adapter#12 ORBM - #4 JICM adapterCalibrated container - 10 gallons (38 litres)Stop watch The operator or another mechanic may berequired to operate a control while a pressurereading is being taken.NOTE: Each machine is shipped fromthe factory with at least one 600 psi and one10,000 psi gauge with quick-couple adapters.The gauges can be found in the machineUp-Time Kit.00017At operating temperature, the engine, exhaustsystem components, cooling systemcomponents and hydraulic system components areHOT. Any contact can cause severe burns.Wheel Drive Circuit - Tests & Adjustments7.2.2Form T050
Wheel Drive ChargePressureSpecification:DO NOT set charge pressure above 450 psig(3,10 Mpa). Overheating of the circuit anddamage to the system can result.00582425 psig (2,93 Mpa)Figure 1: Wheel Drive Charge Pressure Gauge Port TapTest Standards: Hydraulics at operating temperature of140 F (60 C) or greater. Engine operating at high idle(approx. 1200 RPM).Procedure:1. Ensure the hydraulics are at correct operatingtemperature.2. Start the engine and run at low idle.005013. Connect the 600 psi pressure gauge, with thequick-couple adapter attached, to the gaugeport tap provided on the centralized pressurecheck manifold. See Figure 1.Figure 2: Wheel Drive Charge Pressure Manifold(Shown With Optional Charge Heater Installed)NOTE: Only install a 600 psi pressure gaugeafter the engine is running. If the gauge isinstalled before the engine is started it canbe damaged.6. Increase engine throttle to high idle (approx.1200 RPM).7. Read the pressure gauge, the wheel drivecharge pressure should be set at 425 psig(2,93 Mpa).00377If wheel drive charge pressure setting iscorrect, go to step #10. If adjustment isrequired, continue with step #8.Form T050Figure 3: Wheel Drive Charge Pressure Adjustment7.2.3Wheel Drive Circuit - Tests & Adjustments
8. Open the swing-out pump access guardand locate the wheel drive charge pressuremanifold assembly. See Figure 2.9. Locate the large charge pressure reliefcartridge. See Figure 3. Use the 9/16” wrenchand 5/32” allen wrench to loosen the jam nut.Turning the adjustment setscrew CLOCKWISEincreases the pressure setting. Turning thesetscrew COUNTER-CLOCKWISE decreasesthe pressure setting.10. Read the pressure gauge, re-adjust pressuresetting as required. After the correct pressuresetting is made, tighten the jam nut to lockadjustment setting.11. Shut down the engine. Remove the pressuregauge and secure the swing-out pump guard.Wheel Drive Circuit - Tests & Adjustments7.2.4Form T050
Wheel Drive PumpDirectional Relief PressureSpecification:6400 psig (44,14 Mpa)Test Standards: Hydraulics at operating temperature of140 F (60 C) or greater.00565 Engine operating at high idle(approx. 1200 RPM).Figure 4: Lower Solenoid Manifold(TB600 installation shown)Procedure:Operating the wheel drives over relief producesextreme heat that can damage hydraulicsystem components. Expedite all pressurereadings and adjustments.1. Ensure the hydraulics are at correct operatingtemperature.2. Locate and disconnect the parking brakesolenoid coil harness (yellow wire) at the lowersolenoid manifold. See Figure 4. This willprevent the parking brake from releasing.00582Figure 5: Wheel Drive Pump Pressure Gauge Port TapNOTE: Lower solenoid manifold locationvaries by machine configuration.3. Connect the 10,000 psi pressure gauge, withthe quick-couple adapter attached, to thegauge port tap provided on the centralizedpressure check manifold. See Figure 5.4. Access the wheel drive pump behind theswing-out guard located below the hydraulictank.5. Before the directional reliefs can be set thewheel drive POR relief must be cancelled.Locate the POR relief on the wheel drivepump. See Figure 6.Form T05000675Figure 6: Wheel Drive PRO Relief7.2.5Wheel Drive Circuit - Tests & Adjustments
6. Use the 13mm wrench and 4mm allen wrenchto loosen the jam nut on the POR reliefadjustment setscrew.FORWARDTravel Relief7. Very carefully, turn the POR adjustment screwin CLOCKWISE until it just touches bottomthen back it off 1/4 turn. This cancels thePOR relief and allows the gauge to read thedirectional relief settings.NOTE: Do not turn the POR adjustmentsetscrew in too far or it will damage the reliefvalve when it bottoms out.REVERSETravel Relief006758. Instruct the operator or another mechanic tostart the engine and run at high idle (approx.1200 RPM).Figure 7: Wheel Drive POR Relief14. After the correct pressure setting is made,hold the adjustment setscrew stationary andtighten the jamnut to hold the pressure setting.9. On your signal, have the operator or anothermechanic apply the travel brake and activatethe FORWARD travel function while youtake a pressure reading. Then activate theREVERSE travel function and take a reading.Wheel drive directional relief pressure shouldbe set at 6,400 psig (44,14 Mpa) in bothdirections.15. After testing or making adjustments to thewheel drive reliefs, re-adjust the wheel drivePOR pressure setting to specification.16. Shut down the engine and remove thepressure gauge.If wheel drive directional relief pressuresettings are correct, go to step #15. If anadjustment is required, continue with step #10.17. Re-connect the parking brake solenoid coilharness. Close and secure the swing-outpump guard.10. Locate the directional relief for the direction oftravel that requires adjustment. See Figure 7.18. If possible, start the engine and operate thewheel drives to help cool the circuit down.11. Use the 17mm wrench and 5mm allen wrenchto loosen the jam nut on the directional reliefadjustment setscrew.19. Shut down the engine.13. On your signal, have the operator or anothermechanic apply the travel brake and activatethe required direction of travel while you set thedirectional relief to 6400 psig (44,14 Mpa).Turning the adjustment setscrew CLOCKWISEincreases the pressure setting. Turning thesetscrew COUNTER-CLOCKWISE decreasesthe pressure setting.Wheel Drive Circuit - Tests & Adjustments7.2.6Form T050
Wheel Drive Pump PORPressureSpecification:6000 psig (41,38 Mpa)Test Standards: Hydraulics at operating temperature of140 F (60 C) or greater.00565 Engine at high idle (approx. 1200 RPM). Wheel drive pump charge pressure andcharge spike relief set to specification.Figure 8: Lower Solenoid Manifold(TB600 installation shown)Procedure:Operating the wheel drives over relief producesextreme heat that can damage hydraulicsystem components. Expedite all pressurereadings and adjustments.1. Ensure the hydraulics are at correct operatingtemperature.005822. Locate and disconnect the parking brakesolenoid coil harness (yellow wire) at the lowersolenoid manifold. See Figure 8. This willprevent the parking brake from releasing.Figure 9: Wheel Drive Pump Pressure Gauge Port Tap5. On your signal, have the operator or anothermechanic apply the travel brake and activatethe FORWARD travel function while you takea pressure reading. Wheel drive pump PORpressure should be set at 6000 psig(41,38 Mpa).NOTE: Lower solenoid manifold locationvaries by machine configuration.3. Connect the 10,000 psi pressure gauge, withthe quick-couple adapter attached, to thegauge port tap provided on the centralizedpressure check manifold. See Figure 9.If wheel drive pump POR pressure is correct,go to step #11. If an adjustment is required,continue with step #7.4. Instruct the operator or another mechanic tostart the engine and run at high idle (approx.1200 RPM).Form T0507.2.7Wheel Drive Circuit - Tests & Adjustments
6. Locate the POR relief on the wheel drivepump. See Figure 10. Use the 13mm wrenchand 4mm allen wrench to loosen the jam nuton the POR relief adjustment setscrew.7. On your signal, have the operator or anothermechanic apply the travel brake and activatethe FORWARD travel function while you setthe POR relief to 6000 psig (41,38 Mpa).Turning the adjustment setscrew CLOCKWISEincreases the pressure setting. Turning thesetscrew COUNTER-CLOCKWISE decreasesthe pressure setting.00675Figure 10: Wheel Drive POR Relief8. After the correct pressure setting is made,hold the adjustment setscrew stationary andtighten the jamnut to hold the pressure setting.9. Shut down the engine and remove thepressure gauge.10. Re-connect the parking brake solenoid coilharness. Close and secure the swing-outpump guard.11. If possible, start the engine and operate thewheel drives to help cool the circuit down.12. Shut down the engine.Wheel Drive Circuit - Tests & Adjustments7.2.8Form T050
Wheel Drive Pump NullSpecification:Obtain the lowest possible pressure betweenports “X1” and “X2” with the jumper hoseinstalled.Test Standards: Hydraulics at operating temperature of140 F (60 C) or greater.00565 Engine operating at idleFigure 11: Lower Solenoid Manifold(TB600 installation shown)Procedure:1. Ensure the hydraulics are at correct operatingtemperature.2. Locate and disconnect the parking brakesolenoid coil harness (yellow wire) at the lowersolenoid manifold. See Figure 11. This willprevent the parking brake from releasing.NOTE: Lower solenoid manifold locationvaries by machine configuration.3. Access the wheel drive pump behind theswing-out guard located below the hydraulictank.005824. Using the 3/16” allen wrench, remove theplugs from ports “X1” and “X2”. See Figure 13.Install the #6 ORBM - #4 JICM adapters intothe ports.Figure 12: Wheel Drive Pump Pressure Gauge Port Tap5. Connect the 24” (61cm) jumper hose betweenports “X1” and “X2”.6. Start the engine and run at idle. The enginewill remain running throughout the procedure.7. Connect the 10,000 psi pressure gauge, withthe quick-couple adapter attached, to thegauge port tap on the wheel drive pump. SeeFigure 12.Form T0507.2.9Wheel Drive Circuit - Tests & Adjustments
Port “X2”Port “X1”Hydraulic NullAdjustment SetscrewMechanical NullAdjustment Setscrew00675Figure 13: Hydrostatic Pump Null Adjustments8. The mechanical null adjustment is made with alarge setscrew in the control piston cover. SeeFigure 13. Use the 24mm wrench and 8mmallen wrench, to loosen the jamnut and turn theadjustment setscrew in and out until the gaugereads the lowest possible pressure.11. The hydraulic null adjustment is made with asmall setscrew on top of the stroke control.See Figure 13. Use the 13 mm wrench and4 mm allen wrench, to loosen the jamnut andturn the adjustment setscrew in and out untilthe gauge reads the lowest possible pressure.NOTE: The lowest pressure reading indicateswhen the control piston is in the centered nullposition.9. Remove the 10,000 psi gauge and install the600 psi gauge in its place. Repeat step #8 tomake the final adjustment.10. Remove the 600 psi gauge and install the10,000 psi gauge in its place.The hydraulic null adjustment is made with aneccentric pin and should not be turned morethan 90 from center (as indicated by a notchon the adjustment screw), otherwise damage tothe eccentric pin could result.Wheel Drive Circuit - Tests & AdjustmentsNOTE: The lowest pressure reading indicateswhen the control spool is in the centered nullposition.12. Remove the 10,000 psi gauge and install the600 psi gauge in its place. Repeat step #11 tomake the final adjustment.13. Shut-down engine and remove jumper hose,fittings, and gauge.14. Re-connect the parking brake solenoid coilharness. Close and secure the swing-outpump guard.15. Procedure complete.7.2.10Form T050
Wheel Drive Pump CaseDrain PressureSpecification:Maximum 30 psig (0,21 Mpa) allowed.Test Standards: Hydraulics at operating temperature of140 F (60 C) or greater with correct wheeldrive and charge pressure settings.00565 Engine operating at full throttleFigure 14: Lower Solenoid Manifold(TB600 installation shown)Procedure:1. Produce a gauge test hose that will allow youto connect a 60 psi gauge to the #4 JICMadapter that will be installed into the wheeldrive pump case drain port.Hydraulic MotorShift “ON/OFF”2. Ensure the hydraulics are at correct operatingtemperature.3. Locate and disconnect the parking brakesolenoid coil harness (yellow wire) at the lowersolenoid manifold. See Figure 14. This willprevent the parking brake from releasing.00396NOTE: Lower solenoid manifold locationvaries by machine configuration.Figure 15: Hydraulic Motor Shift Control4. Access the wheel drive pump behind theswing-out guard below the hydraulic tank.9. On your signal, have the operator or anothermechanic apply the travel brake and activatefull FORWARD travel while you take apressure reading. Then activate full REVERSEtravel and take a reading.5. Locate and remove the wheel drive pump casedrain plug in port “R”. Install the #12 ORBM #4JICM adapter into the port.The wheel drive pump case drain pressureshould not exceed specification. If thespecification is exceeded, look for conditionsthat would increase backpressure in the casedrain circuit such as a plugged case drain filterelement, failing component, etc.6. Install the gauge test hose and pressure
8) Rexroth AA6VM160 variable displacement wheel drive motor(s). Standard configuration is dual motors matched to an auto-shift gearbox. A single motor installation matched to a 2-speed gearbox is optional. The speed and drawbar pull of the machine is varied by changing the displacement of the wheel drive motor(s). In high range (fast speed