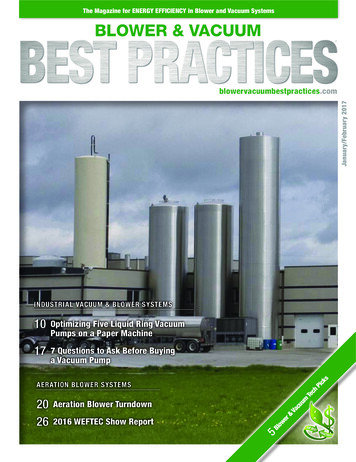
Transcription
January/February 2017The Magazine for ENERGY EFFICIENCY in Blower and Vacuum SystemsINDUSTRIAL VACUUM & BLOWER SYSTEMS10 Optimizing Five Liquid Ring VacuumPumps on a Paper Machine17 7 Questions to Ask Before BuyingPicksa Vacuum PumpkWVacuumlower&5B20 Aeration Blower Turndown26 2016 WEFTEC Show ReportTechAERATION BLOWER SYSTEMSCO2
kaeser.comVisit us at IPPE in Booth #C768Don’t Settle for Less than the BestThe best efficiency. The quietest operation. The highest savings.Energy is the single highest operating cost in a wastewatertreatment plant and 60% of a plant’s energy costs are spenton aeration. At Kaeser, we’ve been providing efficient aerationsolutions for many years.Kaeser’s Sigma screw blower packages are 35% more efficientthan conventional blower designs. In addition to exceptionalefficiency, our screw blower packages are designed and builtfrom the ground up for reliability and service accessibility.They come complete with motors, starters/drives, silencers, anonboard controller, and a full complement of sensors to saveyou time and money on design and installation costs.If you’re looking for reliability and efficiency, talk toKaeser and get the best.COMPRESSORSKaeser Compressors, Inc. 866-516-6888 us.kaeser.com/BVBPBuilt for a lifetime is a trademark of Kaeser Compressors, Inc. 2017 Kaeser Compressors, Inc.customer.us@kaeser.com
COLUMNSJ A N U A R Y / F E B R U A R Y2 0 1 7 V O L U M E3 ,N O .1 INDUSTRIAL VACUUM & BLOWER SYSTEMS10Optimizing Five Liquid Ring Vacuum Pumpson a Paper MachineBy Tim Dugan, P.E., Compression Engineering Corporation177 Questions to Ask Before Buying a Vacuum PumpBy Greg Marciniak, Atlas Copco17AERATION BLOWER SYSTEMS20Aeration Blower Turndown262016 WEFTEC Show Report:Aeration Blower TechnologyBy Tom Jenkins, JenTech Inc.By Rod Smith, Blower & Vacuum BestPractices Magazine20COLUMNS4From the Editor5Resources for Energy EngineersTechnology Picks30Blower & Vacuum System Industry News33Advertiser Index34The MarketplaceJobs and Technology26blowervacuumbestpractices.com3
COLUMNS0 1 – 0 2 / 1 7FROM THE EDITORAeration BlowersIndustrial vacuum pumps are beginning to be the subject of moreenergy efficiency system assessments than ever before. Tim Dugan, fromCompression Engineering Corporation, provides an excellent article onhow he conducts a system assessment. Information provided includes whatmeasurements to take. The article uses paper machines as an example.Paper machines use vacuum in the forming, press, and drying sections.BLOWER & VACUUM BEST PRACTICESEDITORIAL ADVISORY BOARDTom Jenkins, from JenTech Inc., has counseled and trained many leaders in the aerationblower industry. In his article, “Aeration Blower Turndown”, he discusses how to calculateturndown and the many variables to consider when making the calculations. The article startswith a strong statement, “Blower turndown is a parameter that is generally more importantthan efficiency in optimizing energy use.”The 2016 WEFTEC Technical Exhibition and Conference was held at the New Orleans MorialConvention Center in New Orleans, La. The 2016 event made the list of the top five largest andbest-attended events in the conference’s 89-year history. A total of 20,113 registrants and 1,006exhibitors using a net of 28,000 m2 (301,900 ft2) of space attended WEFTEC. We hope youenjoy our coverage of the aeration blower technologies on display at the show.Industrial Energy ManagersIn his article, “7 Questions to Ask Before Buying a Vacuum Pump”, Greg Marciniak from theIndustrial Vacuum Division at Atlas Copco, provides end users and sales engineers with a set ofquestions to consider to properly select a vacuum pump. Many of these questions may warranta system assessment before answering.Doug BarndtManager, Demand Side BallEnergy-SustainabilityCorporationRichard FeustelSenior Energy AdvisorLeidosThomas SullivanEnergy PerformanceManagerMichelinWilliam JeraldEnergy ManagerCalPortlandJennifer MeierGlobal EH&S/Plant EngineeringManagerVarroc LightingSystemsThomas MortSenior AuditorThomas MortConsultingBrad ReedCorporate Energy TeamToyotaLeaderBrad RundaGlobal Director, EnergyKochIndustriesUli SchildtEnergy EngineerDarigoldDon SturtevantCorporate EnergyManagerSimplotBryan WhitfieldPaint & Powder BoothSpecialistFiat ChryslerAutomotive USThank you for investing your time and efforts into Blower & Vacuum Best Practices.ROD SMITHEditortel: 412-980-9901rod@airbestpractices.com2017 Expert Webinar SeriesJoin Tom Jenkins and Blower & Vacuum Best PracticesMagazine for a Webinar titled, “Aeration Blower TurndownEfficiency Variations Across Operating Ranges.”Register and view our 2017 Webinar Calendar ars.2017 MEDIA PARTNERS4blowervacuumbestpractices.com
COLUMNS0 1 – 0 2 / 1 7 RESOURCES FORENERGY ENGINEERSTECHNOLOGY PICKSAtlas Copco Launches DZS Range of Dry ClawVacuum PumpsAtlas Copco has added the new DZS dry claw vacuum pump to theirportfolio. Claw vacuum pumps offer non-contact and dry pumpingchambers with high performance and power efficiency, makingthem suitable for many applications including pneumatic conveying,CNC routing and milking parlors. Atlas Copco was the first companyto innovate multi-claw technology for compressors.“We’ve worked for many years with claw technologies within thecompressor and vacuum industries,” said Koen Lauwers, Vice PresidentIndustrial Vacuum at Atlas Copco. “This is a pump built on simplicityand durability that will be with your facility for years to come.”The new DZS design offers removable stainless steel claws that are easyto clean and features easily changeable seals. Because of its innovativestructure, the DZS can be reassembled without touching the drive train,saving a massive amount of downtime and expense. The modular designof the pumping chamber, gearbox and silencer allows for replacementof individual components in the case of failure due to process upsets,resulting in higher efficiency and lower life cycle costs. This design alsooffers major advantages with heat dissipation, employing Atlas Copco’spatented cooling design concept for efficient and quiet air distribution.The new DZS design offers removable stainless steel claws that are easy to clean andfeatures easily changeable seals.blowervacuumbestpractices.com5
COLUMNS0 1 – 0 2 / 1 7RESOURCES FOR ENERGY ENGINEERSTECHNOLOGY PICKS“The DZS provides reliable operation evenin the harshest conditions,” said Jerry Geenen,vice president of North American utilityvacuum with Atlas Copco. “Most process gasseseventually pass through the pump, which canlead to premature failure. The new DZS rangeprovides a corrosion-resistant chamber toprevent maintenance downtime.” The DZSjoins Atlas Copco’s wide range of vacuumpump offerings.About Atlas CopcoAtlas Copco is a world-leading provider ofsustainable productivity solutions. The Groupserves customers with innovative compressors,vacuum solutions and air treatment systems,construction and mining equipment, powertools and assembly systems. Atlas Copcodevelops products and services focused onproductivity, energy efficiency, safety andergonomics. The company was founded in1873, is based in Stockholm, Sweden, andhas a global reach spanning more than 180countries. In 2015, Atlas Copco had revenuesof BSEK 102 (BEUR 11) and more than43,000 employees.About Atlas Copco Compressors LLCAtlas Copco Compressors LLC is part of theCompressor Technique Business Area, and itsheadquarters are located in Rock Hill, S.C.The company manufactures, markets, andservices oil-free and oil-injected stationaryair compressors, air treatment equipment,and air management systems, including localmanufacturing of select products. The AtlasCopco Group, which celebrated its 140thanniversary in 2013, is among the Top 100sustainable companies in the world and amember of the Dow Jones World Sustainability6blowervacuumbestpractices.comIndex. Atlas Copco has also been recognizedby Forbes, Thomson-Reuters and Newsweek,among others, for its commitment to innovationand sustainability. Atlas Copco Compressorshas major sales, manufacturing, production,and distribution facilities located in California,Illinois, Massachusetts, North Carolina, SouthCarolina, and Texas.About Vacuum SolutionsVacuum Solutions is a division within AtlasCopco’s Compressor Technique Business Area.It develops, manufactures and markets vacuumpumps, abatement systems, valves and relatedservice products mainly under the Edwardsand Atlas Copco brands. The main marketsegments served are: semiconductor, flat paneldisplay, solar, scientific and utility vacuum.The division’s focus and main drive is tofurther improve its customers’ productivity.The divisional headquarters are in CrawleyUnited Kingdom.For more information, visitwww.atlascopco.us or for moreinformation on the DZS lineof vacuum pumps, visit cuum-pumps/dryclaw-vacuum-pumps/.Tuthill Introduces New MPAK BlowerPackageTuthill Vacuum & Blower Systems introducesthe new MPAK 2000 blower package. EachMPAK 2000 is value-engineered to meetspecific applications for optimized efficiencies.Its design allows for simple installation anduse. Features include: air or gas blowers,accurate blower sizing for an applicationincluding Tuthill’s PD Plus, CP Series or QxMPAK2000 with inlet filterMPAK2000 enclosedmodels, open or closed package design withfield retrofittable enclosure option, and highendurance and Tuthill reliability.The MPAK 2000 blower package provides CFMup to 2200, pressure up to 18 PSI, and vacuumdown to 17" Hg. MPAK blower packages aremanufactured at the Tuthill Vacuum & BlowerSystems site in Springfield, Missouri, USA.
COLUMNS0 1 – 0 2 / 1 7 TECHNOLOGY PICKSAbout Tuthill Vacuum & Blower SystemsTuthill Vacuum & Blower Systems,manufacturer of KINNEY vacuum pumpsand M-D Pneumatics blowers and vacuumboosters, is a leader in the design andmanufacture of high performance, reliablepositive displacement blowers, mechanicalvacuum pumps, vacuum boosters andengineered systems ready to install and run.Since 1969, Tuthill Vacuum & Blower Systemshas been manufacturing at its main facilitylocated in Springfield, Missouri.For more information, visitwww.tuthillvacuumblower.comNew Kaeser 20-50 hp DBS ScrewBlowersKaeser Compressors has expanded its awardwinning screw blower product line with theaddition of the new DBS series. These integratedpackage blowers are available with motor sizesfrom 20 to 50 hp and flows from 150 to 770cfm and boast an energy efficiency advantageover conventional blowers of up to 35%.The DBS series includes the same designfeatures as Kaeser's other screw blowerpackages, such as high efficiency motors,silencers, inlet filters, starters/drive, a fullenclosure, an onboard controller, and afull complement of sensors. These unitsKaeser's DBS screw blowers are up to 35% moreefficient than conventional blower designs.Howden Roots – Setting the Standard Since 1854Howden Roots is proud to continue building the Roots legacy, begunin 1854 by the Roots brothers, by manufacturing the world-renownedrotary positive displacement blowers and centrifugal compressors inConnersville, Indiana, U.S.A.Each Howden Roots rotary positive displacement blower, centrifugalcompressor and ExVel Turbo Fan is designed and fabricated to uniqueapplications within a wide array of industries such as: pneumaticconveying, gas separation, wastewater treatment, steam compression,and petrochemical production.Univeral RAIBi-lobe BlowerRGS-J GasCompressorTRI-NADO Tri-lobeExhausterEASYAIR X2 BlowerPackage SystemTo maintain optimized production levels,Howden Roots factory maintenance and repairservices are available around the world.CentrifugalCompressorFor further information contact Howden Roots 900 West Mount Street, Connersville, IN, U.S.A.Tel: 1-800–55-ROOTS (76687) Email: Connersville.CustomerCare@howden.com www.howdenroots.com Howden Group Ltd. All rights reserved. 2016blowervacuumbestpractices.com7
COLUMNS0 1 – 0 2 / 1 7RESOURCES FOR ENERGY ENGINEERSTECHNOLOGY PICKSare designed, built, and tested to meetinternational and domestic performanceand safety standards, and are available inboth STC (wye-delta start) and SFC (VariableFrequency Drive) versions.Models also come standard with SigmaControl 2 . In addition to monitoring allonboard sensors, Sigma Control 2 featuresexpanded communication features. With anEthernet port and built-in Web-server, SigmaControl 2 enables remote monitoring andemail notifications for service and alarms.Optional industrial communication interfacessuch as ModBus, Profibus, Profinet, andDevicenet are available to provide seamlessintegration into plant control/monitoringsystems such as Kaeser's Sigma Air Manager4.0 (SAM 4.0).About KaeserKaeser is a leader in reliable, energy efficientcompressed air equipment and system design.We offer a complete line of superior qualityindustrial air compressors as well as dryers,filters, SmartPipe , master controls, and othersystem accessories. Kaeser also offers blowers,vacuum pumps, and portable diesel screwcompressors. Our national service networkprovides installation, rentals, maintenance,repair, and system audits. Kaeser is an ENERGYSTAR Partner.For more information, visitwww.kaesernews.com/DBSTo be connected with yourrepresentative for additionalinformation, please call on K-Tron Introduces NewElectronic Pressure CompensationSystemCoperion K-Tron displayed, at the 2016Powder Show, the unique new ElectronicPressure Compensation (EPC) systemfor their high-accuracy loss-in-weightfeeders. The main advantages of the newsystem include improved accuracy andreliability as well as lower initial cost andeasier installation compared to traditionalmechanical pressure compensation systems.Retrofitting options for existing feeders areavailable. EPC can be installed on a majorityof Coperion K-Tron gravimetric feeders inalmost any application and all industries.In a closed feeding system, pressure buildup inside a feeder can significantly impairweighing accuracy. The commonly installedmechanical pressure compensation systemsare sensitive to structural factors andmachine alignment and therefore may beintricate or even unreliable. Coperion K-Tronhas now developed a clever but simpleelectronic solution for accurate and steadypressure compensation in feeder hoppers.The modular design incorporates pressuresensors and electronics tailored to interactsmoothly with Coperion K-Tron’s KCM feedercontrol system.About Coperion and Coperion K-TronCoperion K-Tron is a business unit ofCoperion and is a global leader and singlesource supplier of material handling andfeeding systems. Coperion K-Tron has definedthe leading edge of technology for materialhandling and feeding applications in theprocess industries.Coperion is the international market andtechnology leader in compounding systems,feeding technology, bulk materials handlingsystems and services. Coperion designs,develops, manufactures and maintainssystems, machines and components for theplastics, chemicals, pharmaceutical, food andminerals industries. Within its four divisions– Compounding & Extrusion, Equipment &Systems, Material Handling and Service –Coperion has 2,500 employees and nearly 40sales and service companies worldwide.For more information, visitwww.coperionktron.comBasic principle of EPC electronic pressure compensationapplied in gravimetric feeding system in a schematicpresentation; KCM: feeding control
COLUMNS0 1 – 0 2 / 1 7 TECHNOLOGY PICKSNew Robuschi ROBOX CompressorsHelp an Italian WWTPFPZ Regenerative Blowers MeetNew Motor Efficiency StandardsRobuschi, a Gardner Denver brand, hasdeveloped a new screw compressor calledROBOX Energy that improves energyefficiency and reduces operating costs.The compressor has immense flexibilityand combines the unique characteristicsof the screw compressor with theinnovative permanent magnet motor. Moreinformation is available in a case study thatdescribes how Robuschi’s ROBOX Energycompressors helped Italy’s Iren Group withthe restructuring of one of its wastewatertreatment systems. The case study alsoprovides useful information on the technologyused and how facilities can reduce costs andbecome more energy efficient.FPZ, Inc. announced their regenerativeblowers meet new federal energy efficiencyrequirements for commercial and Industrialelectric motors under the U.S. Energy PolicyAct (e-pact 431 subpart B/X), affecting3-phase, 1 HP or greater motors.These high-efficiency motors are nowstandard across the FPZ product line andavailable ex stock from their Saukville(Milwaukee), Wisconsin facility.The blowers feature clean, oil-free andmaintenance-free operation, with flows to over1400 scfm and pressure differentialsto 10.8 psig / 14.7 hg.FPZ’s premium efficient blowers meet the DOE’s motorefficiency requirements outlined in Nema table 12-12.FPZ, Inc. sells on a “factory-direct” basis andall blowers come with a 3-year warranty.For more information visitwww.fpz.com, email: usa@fpz.com,tel: 262-268-0180Click here to access the case yatworkHigh Quality Blowers at an Excellent ValueEurus Blower is a 100 million corporation with 50 years of experience building high quality positive displacement blowers.Don’t be fooled into paying more. Receive the same qualityand performance while profiting from significant savings.ZG Series Tri-lobedBlowersZZ Series Drop-inReplacement BlowersBulkmaster 6800 SeriesTruck BlowersBi-lobed MB SeriesBlower PackagesFlows from 30 to 5000 cfm. / Pressures to 15 psi. / Vacuums to 15” Hg.For more information contact Eurus Blower, PO Box 4588, Wheaton, Illinois 60189tel: 630-221-8282 / email: sales@eurusblower.com / www.eurusblower.comblowervacuumbestpractices.com9
INDUSTRIAL VACUUM & BLOWER SYSTEMS0 1 – 0 2 / 1 7Optimizing Five LiquidRing Vacuum PumpsON A PAPER MACHINEBy Tim Dugan, P.E., President,Compression Engineering Corporationc Industrial process operating loads andoptimal set points are not usually accuratelyknown at the time of design, so often thereis significant mismatch between equipmentand the process it serves. To overcome thisuncertainty, designers typically oversizeequipment. Over time, process changes andequipment efficiencies decline, so equipmentmight be operating less efficiently than at startup. Or, equipment can be undersized, therebyhampering the entire system and causing otherinefficiencies to compensate. For instance,too much steam usage in the dryer sectionof a paper machine can occur because ofinadequate vacuum at the wet end.Proper tuning and commissioning rarelyhappens, so it is not known if the system isoperating per the intent of the original design.Typically, there is insufficient monitoring datato even know if the system is still operatingat its commissioned level. Finally, systemset points usually change over time, and thevacuum system design is usually not set upproperly to be able to be adjusted easily andefficiently.For all these reasons, some vacuumsystems need a complete retrofit to meetcurrent and future standards and processrequirements. However, most vacuumsystems can be improved quite a bit justby being “re-commissioned.” The easiestre-commissioning is to tweak the vacuum pumpspeeds (assuming they are belt-driven). As an“Industrial process operating loads and optimal set points are notusually accurately known at the time of design, so often there issignificant mismatch between equipment and the process it serves.”— Tim Dugan, P.E., President, Compression Engineering Corporation10blowervacuumbestpractices.com
INDUSTRIAL VACUUM & BLOWER SYSTEMS0 1 – 0 2 / 1 7 Proudly Presenting the 2017 Expert Webinar Seriesexample, a paper machine vacuum system will be used to illustratehow constant flow vacuum systems work. The example also illustratesone simple way to optimize a constant flow vacuum system—speedadjustment. Any constant flow process can do the same.The principles I will use in this article are summarized as follows:1. The “system curve” needs to be known.2. The vacuum “pump curve” needs to be known.3. The system curve and pump curve cross at the “operatingpoint,” and should be as close as possible to the bestoperating point for the system and for the pump.Principle 1: The System Curve Needs to be KnownA “system curve” is the relationship between vacuum (pressuredifferential, really) and flow. It tells you how the system “behaves.”How much flow do you need to “feed” it to keep it satisfied, atevery potential desired operating point? It’s a bit tricky in a vacuumsystem, especially if the reader is familiar with the standard liquidsystem curve (pressure drop is proportional to flow squared). Withgas flow at low pressures, pressure differential is proportional tothe square of mass flow, and inversely proportional to density—anddensity changes a lot. So how do you find the system curve in yourreal process?First, you need to make some measurements. Trend logging isalways better, but if all you have are spot measurements, it can stillwork. Assuming there is only one operating point for a constantflow system (or subsystem), you only need to measure at that onepoint. The following measurements are needed:pp Ambient pressurepp Vacuum, at the pump inlet, after any throttlingvalvesAeration BlowerTurndown EfficiencyVariationsJoin Keynote Speaker, Tom Jenkins,President of JenTech Inc., to reviewvariations in aeration blower turndownefficiencies, across different operatingranges, for different blower technologies.According to the U.S. EnvironmentalProtection Agency (EPA), wastewatertreatment plants consume 56 billion kWhtotaling nearly 3 billion per year – equal toalmost 3 percent of total power usage in theUnited States. Aeration blowers, in a typicalbiological wastewater treatment plant, canaccount for 50 to 70 percent of the facility’senergy use. This webinar will reviewthe aeration blower turndown efficiencyvariations, across operating ranges, ofdifferent technologies.Tom Jenkins hasover 30 years ofexperience withaeration blowersand blowercontrols.Receive 1.0 PDH Credit.pp Vacuum, at the system “exit” point, but beforeany throttling valvespp Flow or flow proxyIdeally, you need to measure with an orifice plate at the inlet ordischarge of the vacuum pump, wherever it is practical to have ameter run. Some vacuum systems have these flanges and taps alreadyinstalled, because the system was flow tested at initial commissioning.The rigorous approach is to use the ASME 9 or 10 procedure,depending on whether it is positive displacement or centrifugal, andRegister for Free Today ebruary 23, 2017 – 2:00 PM ESTblowervacuumbestpractices.com11
INDUSTRIAL VACUUM & BLOWER SYSTEMS0 1 – 0 2 / 1 7OPTIMIZING FIVE LIQUID RING VACUUM PUMPS ON A PAPER MACHINEthe ASME 19.5 method for flow measurement(See References 1 through 3). Or, flow proxiescan be made. Your vacuum pump vendor or anoutside consultant should know how to do that.A few alternate methods include:a differential pressure (DP).This is essentially a crudeflow meter. You really needone DP transmitter, and thenuse the piping friction tablesto estimate flow.pp Use pump curve, Amps andvacuum. This is the leastdesirable, since you shouldalways question the validityof any curve.Analysispp Use a straight run of pipe andConvert flow to icfm at the system outlet(before the regulating valve, if there is one).Calculate alternate flows for other vacuumlevels, in 1"Hg increments.See Table 1 and Figure 1 for an examplesystem curve and estimate of optimal powerat each system curve point.pp Use process instrumentationor test data, correlated withvacuum.Principle 2: The Vacuum Pump CurveNeeds to be KnownPositive displacement vacuum pump curvesall tend to look similar, pretty flat flow forall vacuum levels, except at the extremities.Centrifugal exhauster curves look more likea centrifugal pump curve, with flow reducingas head (vacuum) increases, and viceversa. This example is for pulp and paperdewatering, so we are using a curve of aliquid ring vacuum pump.In reality, no pump matches the curve exactly.If the above flow measurement method canFigure 1: Example Vacuum System CurveTABLE 1: EXAMPLE SYSTEM CALCULATIONSPRESSURE DIFFERENTIAL(VACUUM), "HGABS PRESS, "HGMASS FLOW, LB/MINNORMALIZED FLOW, SCFMINLET VOLUME FLOWREQUIRED, ICFMAPPX VACUUM PUMPPOWER REQ'DPERCENT OF HP AT14.5"HG 554834%Assumptions:1 System equivalent orifice is not changed2 DP is proportional to Qm 2 / density3 Qm is proportional to (density x DP) 0.54 Power is proportional to icfm and vacuum5 Pamb 29.92 "Hg12blowervacuumbestpractices.com
FREE SUBSCRIPTIONDIGITAL EDITION FREE WORLDWIDE PRINT EDITION FREE TO U.S. SUBSCRIBERS2017 FOCUS INDUSTRIES!Poultry & Meat Packaging Pharmaceutical & Labs Food Processing Wastewater AerationSustainable Energy Savings withBlower & Vacuum Best PracticesFrom WWTP Aeration Blowers to CentralizedVacuum SystemsBlower & Vacuum Best Practices is a technical magazine dedicatedto discovering Energy Savings in industrial blower and vacuum systemsand in municipal wastewater aeration blower systems. Our editorialfocus is on case studies and technical articles where application andsystem knowledge drives technology selection, creating energy savingsin projects delivering excellent ROI’s.Our readers have embraced energy management practices as the nextstep. Our diverse key subscribers work at multi-factory manufacturingorganizations and are targets to consider options such as VSD vacuumpumps in newly centralized systems. On the municipal side, over 1,000 operators at wastewater treatment plants (WWTP’s) and blower saleschannels receive the magazine. Lastly, a growing group of industrialblower and vacuum OEM design engineers are looking for technologiesable to improve their machines.“A more recent innovation is to control the aeration blowersoff of total air flow instead of header pressure.”– Julia Gass, P.E., Black & Veatch (September 2016 Issue)“Busch designed a customized central vacuum system for thefurniture manufacturer, consisting of eight identical Mink clawvacuum pumps, each equipped with a suction capacity of 300 m3/h.”– Uli Merkle, Busch Vacuum Pumps and Systems (feature article in July 2016 Issue)“Our engineering optimizes blower packages for each field –identifying, for example, the optimal conveying velocitiesfor over 50 types of wheat flour!”– Todd Smith, General Manager, Coperion K-Tron(Powder Show Report in a 2016 Issue)To subscribe visit blowervacuumbestpractices.comSubscribe Now!
INDUSTRIAL VACUUM & BLOWER SYSTEMS0 1 – 0 2 / 1 7OPTIMIZING FIVE LIQUID RING VACUUM PUMPS ON A PAPER MACHINEFigure 2: Typical Paper MachinePrinciple 3: Optimize Vacuum PumpPerformance for an Alternate SpeedIf the vacuum level is too high, the pump is“pulling too hard” on the system. If you reducethe speed, the vacuum will drop along thesystem curve, as described above. Power willalso drop. Savings can be significant. I willexplain that for one of the five pumps in theexample project. It can be done as follows:pp Adjust vacuum pump speedto move the operating pointas close as possible to theneeded vacuum level. Forbelt-driven vacuum pumps,this is simple. For directdrive, it would require a VFD.pp Stay within the pump curvespeed range limits.Figure 3: Typical Uhle Box of a Paper Machine (Vacuum Connection on Back Side)be accomplished for the system curve, youcan generate the vacuum pump curve with notrouble, as follows:pp Install data logging for pumppp Vary flow higher by a falsebleed-in.inlet vacuum (not systemvacuum) and Amps (orpower).pp Vary flow lower by throttlingpp If flow can be trend logged,pp Correlate flow with vacuumgreat. Otherwise, make a spot14calculation of flow at eachoperating point.blowervacuumbestpractices.comthe vacuum pump intake/isolation valve.and power with vacuum.Example Paper Machine Project withFive Vacuum PumpsPaper machines use vacuum in the forming,press, and drying sections, as can be seenin Figure 2. In forming, the largest flowrequirement exists. Vacuum and gravity pulla large amount of water out from liquidstock (starting at only 4 percent solids inthe “headbox”). This is known as sheetformation, where the fibers start to spread
INDUSTRIAL VACUUM & BLOWER SYSTEMSand consolidate into a thin mat. It looks likea white fleece in this section. The web of wetpaper is then lifted from the wire mesh andsqueezed between a series of presses whereits water content is lowered to about 50percent by squeezing between rollers. It thenpasses around a series of cast-iron cylindersin the drying section, heated to temperaturesin excess of 200 F, where drying takes place.Here, the water content is lowered to between5 and 8 percent—its final level.The vacuum process evaluated in this articleis in the press section. In this part of the papermachine, air is sucked through the web inlong slots on the top of a box called an “Uhlebox” (Refer to Figure 3). The press section hasseveral Uhle boxes, each designed with exactlythe right slot geometry and vacuum level toremove water step by step.The example project’s vacuum system servedthe press section of a paper machine, and0 1 – 0 2 / 1 7it is shown in Figure 4. It uses positivedisplacement vacuum pumps called liquid ringvacuum pumps, that use a “liquid ring” forthe cylinder wall and a rotor that is immersedin the ring, as shown in Figure 5. They canhandle high condensable loads, and they arecommon in wet applications like pulp andpaper. Centrifugal exhausters are startingto make inroads into pulp and p
including Tuthill's PD Plus, CP Series or Qx models, open or closed package design with field retrofittable enclosure option, and high endurance and Tuthill reliability. The MPAK 2000 blower package provides CFM up to 2200, pressure up to 18 PSI, and vacuum down to 17" Hg. MPAK blower packages are manufactured at the Tuthill Vacuum & Blower