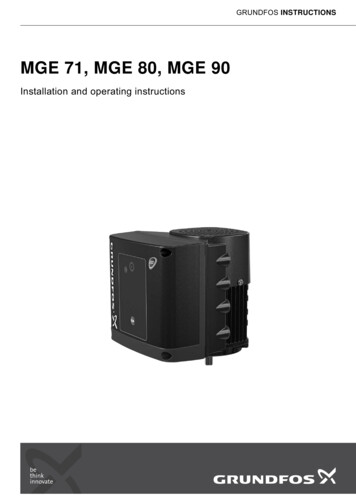
Transcription
GRUNDFOS INSTRUCTIONSMGE 71, MGE 80, MGE 90Installation and operating instructions
Declaration of conformityDeclaration of conformity1GB: EC declaration of conformityCN: EC 产品合格声明书We, Grundfos, declare under our sole responsibility that the productsMGE 71, MGE 80 and MGE 90, to which this declaration relates, are inconformity with these Council directives on the approximation of the lawsof the EC member states:— Low Voltage Directive (2006/95/EC).Standard used: EN 61800-5-1:2007.— EMC Directive (2004/108/EC).Standard used: EN 61800-3:2005.— R&TTE Directive (1999/5/EC).Standard used: ETSI EN 300 328 V1.7.1 (2006-10).This EC declaration of conformity is only valid when published as part ofthe Grundfos installation and operating instructions (publication number98418360 �明,产品 MGE 71, MGE 80 和MGE �理事会指令:— 低电压指令 (2006/95/EC)。所用标准 : EN 61800-5-1:2007。— 电磁兼容性指令 (2004/108/EC)。所用标准 : EN 61800-3:2005。— 线 设 和 信线端设 指令 (1999/5/EC)。所用标准 : ETSI EN 300 328 V1.7.1 富安装与操作指导手册 (出版号 , 6th March 2013Jan StrandgaardTechnical DirectorGrundfos Holding A/SPoul Due Jensens Vej 78850 Bjerringbro, DenmarkPerson authorised to compile technical file andempowered to sign the EC declaration of conformity.2
English (GB)English (GB) Installation and operating instructions1. Symbols used in this documentOriginal installation and operating instructions.CONTENTSWarningPageIf these safety instructions are not observed,it may result in personal injury.1.Symbols used in this document32.Abbreviations and definitions3Warning3.3.13.2General descriptionRadio communicationBattery444If these instructions are not observed, it may leadto electric shock with consequent risk of seriouspersonal injury or death.4.4.14.2IdentificationNameplateType key556Warning5.5.15.25.35.45.55.6Mechanical installationHandlingMountingCable entriesEnsuring motor coolingOutdoor installationDrain holes66667776.6.16.26.36.46.56.66.76.8Electrical installationProtection against electric shock, indirect contactCable requirementsMains supplyAdditional protectionFunctional modulesConnection terminals on functional modulesSignal cablesBus connection cable777899914147.7.17.27.37.47.5Operating conditionsMaximum number of starts and stopsAmbient temperatureInstallation altitudeAir humidityMotor cooling1414141414148.8.18.28.38.48.5User interfacesBasic control panelStandard control panelChanging the position of the control panelR100 remote controlGrundfos GO Remote151515171828FMFunctional module.9.9.19.2External setpoint signalClosed-loop operation (controlled)Open-loop operation (uncontrolled)292929GDSGrundfos Digital Sensor.Factory-fitted sensor in some Grundfospumps.10.Bus signal29GENIbusProprietary Grundfos fieldbus standard.11.Priority of settings29GFCIGround fault circuit interrupter.12.Grundfos Eye30GNDGround.13.Signal relays3114.MeggingGrundfos EyeStatus indicator light.32LIVELow voltage with the risk of electric shock ifthe terminals are touched.OCOpen collector:Configurable open-collector output.PEProtective earth.PELVProtective extra-low voltage.A voltage that cannot exceed ELV undernormal conditions and under single-faultconditions, except earth faults in othercircuits.SELVSafety extra-low voltage.A voltage that cannot exceed ELV undernormal conditions and under single-faultconditions, including earth faults in othercircuits.15. Technical data, single-phase motors15.1 Supply voltage15.2 Leakage current32323216. Technical data, three-phase motors16.1 Supply voltage16.2 Leakage current32323217.Inputs/outputs3218. Other technical data18.1 Sound pressure level333319.34DisposalWarningPrior to installation, read these installation andoperating instructions. Installation and operationmust comply with local regulations and acceptedcodes of good practice.The surface of the product may be so hot thatit may cause burns or personal injury.CautionIf these safety instructions are not observed,it may result in malfunction or damage to theequipment.NoteNotes or instructions that make the job easierand ensure safe operation.2. Abbreviations and definitionsAIAnalog input.ALAlarm, out of range at lower limit.AOAnalog output.AUAlarm, out of range at upper limit.CIMCommunication interface module.Current sinkingThe ability to draw current into the terminaland guide it towards GND in the internalcircuitry.Current sourcingThe ability to push current out of theterminal and into an external load whichmust return it to GND.DIDigital input.DODigital output.ELCBEarth leakage circuit breaker.3
English (GB)3. General descriptionGrundfos MGE 71, MGE 80 and MGE 90 arefrequency-controlled permanent-magnet motors for single-phaseor three-phase mains connection. The motors incorporate a PIcontroller.The motors can be connected to a signal from an external sensorand a setpoint signal enabling control in closed loop. The motorscan also be used for an open-loop system in which the setpointsignal is used as a speed control signal.The motors are only intended for machines with a square torquecharacteristic, such as ventilators and centrifugal pumps.The motors incorporate a control panel which is available invarious versions. See section 8. User interfaces for furtherinformation.Detailed motor settings are made with the wireless GrundfosR100 remote control or Grundfos GO Remote.Furthermore, important operating parameters can be read via theR100 or Grundfos GO Remote.The motors incorporate a functional module. The functionalmodule is available in various versions with different inputs andoutputs. See section 6.5 Functional modules for furtherinformation.As an accessory option, the motors can be fitted with a GrundfosCIM module. A CIM module is an add-on communication interfacemodule. The CIM module enables data transmission between themotor and an external system, for example a BMS or SCADAsystem. The CIM module communicates via fieldbus protocols.3.1 Radio communicationThis product incorporates a radio module for remote controlwhich is a class 1 device and can be used anywhere in the EUmember states without restrictions.For use in USA and Canada, see page 35.NoteSome variants of this product and products soldin China and Korea have no radio module.This product can communicate with the Grundfos GO Remoteand other MGE motors of the same type via the built-in radiomodule.In some cases, an external antenna may be required.Only Grundfos-approved external antennas may be connected tothis product, and only by a Grundfos-approved installer.3.2 BatteryA Li-ion battery is fitted in the FM 300 functional module.The Li-ion battery of the FM 300 module complies with theBattery Directive (2006/66/EC). The battery does not containmercury, lead and cadmium.4
English (GB)4. IdentificationThe motor can be identified by means of the nameplate on theterminal box.4.1 NameplateP.C. :Serial no :Env.Type :TEFCSF :CL:F PF:kg Tamb :INPUT:U in :f inI SF Amp:A I 1/1 :OUTPUTVARIANTP2Hp PB ::rpm FM :V n max::Hz EffHMI :ACIM :XxxxxxxxxxxType :P.N. :DE :NDE :Wgt :E.P. MotorThe motor nameplate is located on the side of the terminal box.See fig. 1, pos. A.Made in HungaryDK - 8850 Bjerringbro, DenmarkTM05 3489 3512AFig. 1Nameplate locationFigure 2 shows the nameplate. The position numbers refer to thetable below.Type :P.N. :DE :NDE :Wgt :28Fig. 2Pos.2-V34657P.C. :Serial no :Env.Type :IP:PF :CL:okg Tamb :C27262524INPUT:U in f inI 1/1 :23822910OUTPUTP2kW:V n max:rpm:Hz EffA:2120191211VARIANTPB :FM :HMI :CIM :1813Made in HungaryDK - 8850 Bjerringbro, Denmark17161514TM05 5246 35121Nameplate, MGE motorsDescriptionPos.Description1Type designation15Grundfos company address2Product number16Country of manufacture3Drive-end bearing17Human Machine Interface type4Version number18CIM module type5Environmental type19Motor efficiency6Production code (year and week)20Maximum motor speed [min-1]7Serial number21Maximum input current [A]8Supply voltage [V]22Mains frequency [Hz]9Rated power output [kW]23Enclosure class according to IEC 60034-510Power board24Insulation class according to IEC 6211411Functional module type25Maximum ambient temperature [ C]12CE mark and approvals26Power factor13Part number of nameplate27Weight [kg]14Grundfos logo28Non-drive-end bearing5
4.2 Type keyEnglish (GB)CodeExampleMGE71[]BKType of motor unitComplete motor with terminal boxBasic motor unit without terminal boxKit for basic motor unit without terminal boxMGMotor GrundfosEElectronic control718090Frame size according to IEC (centre line height of motor shaft in mm, foot-mounted motor)MA2-14FT85-HASize of footNot defined for frame sizes 71 and 80SmallMediumLarge[]SMLLength ofstator coreABCD304560851234Maximum speed5900 min-14000 min-13600 min-12000 min-1Rated motor power, P2 [kW]1450-2000 min-12900-4000 min-14000-5900 mShaft end diameter [mm][]FTFFFlange versionFoot-mounted (B3)Tapped-hole flangeFree-hole flange[]Pitch circle diameter [mm], flange versionB3HIModel designationSingle-phaseThree-phaseAVersion designationFirst version5. Mechanical installationWarningInstallation and operation must comply with localregulations and accepted codes of good practice.5.1 Handling5.2 MountingThe motor must be secured to a solid foundation by bolts throughthe holes in the flange or the base plate.NoteIn order to maintain the UL mark, additionalinstallation procedures must be followed.See page 35.5.3 Cable entriesWarningObserve local regulations setting limits formanual lifting or handling.WarningBefore lifting the motor, pay attention to themotor weight stated on the nameplate.CautionDo not lift the motor by the terminal box.When lifting the motor, always use the eyebolts, if fitted.Alternatively, lift the motor with both hands.6The motor has four M20 screwed cable entries fitted with blindplugs from factory. Various cable glands can be ordered fromGrundfos as accessory kits.
NoteIn order to ensure sufficient cooling of the motor,the distance (D) between the end of the fan coverand a wall or other fixed objects must always beat least 50 mm, irrespective of motor size.See fig. 3.Carry out the electrical connection according to local regulations.Check that the supply voltage and frequency correspond to thevalues stated on the nameplate.WarningDo not make any connections in the terminal boxunless the power supply has been switched offfor at least 5 minutes.Make sure that the power supply cannot beaccidentally switched on.TM05 5236 3512The motor must be earthed and protected againstindirect contact in accordance with localregulations.DFig. 3Minimum distance (D) from the motor to a wall or otherfixed objectsIf the power supply cable is damaged, it must bereplaced by the manufacturer, the manufacturer’sservice partner or a similarly qualified person.Note6.1 Protection against electric shock, indirect contact5.5 Outdoor installationWhen installed outdoors, the motor must be provided with asuitable cover to avoid condensation on the electroniccomponents. See fig. 4.NoteThe user or the installer is responsible for theinstallation of correct earthing and protectionaccording to local regulations. All operationsmust be carried out by a qualified electrician.WarningWhen fitting a cover to the motor, observe theguideline in section 5.4 Ensuring motor cooling.The cover must be sufficiently large to ensure that the motor isnot exposed to direct sunlight, rain or snow. Grundfos does notsupply covers. We therefore recommend that you have a coverbuilt for the specific application. In areas with high air humidity,we recommend that you enable the built-in standstill heatingfunction. See section Standstill heating, page 27.The motor must be earthed and protected againstindirect contact in accordance with localregulations.Protective-earth conductors must always have a yellow/green(PE) or yellow/green/blue (PEN) colour marking.6.1.1 Protection against mains voltage transientsThe motor is protected against mains voltage transients inaccordance with EN 61800-3.6.1.2 Motor protectionTM05 3496 3512The motor requires no external motor protection. The motorincorporates thermal protection against slow overloading andblocking.Fig. 46.2 Cable requirements6.2.1 Cable sizeSingle-phase supply1.5 mm2 / 12-14 AWG.Examples of covers (not supplied by Grundfos)Three-phase supply5.6 Drain holes6-10 mm2 / 10-8 AWG.When the motor is installed in moist surroundings or areas withhigh air humidity, the bottom drain hole should be open.The enclosure class of the motor will then be lower. This helpsprevent condensation in the motor as it will make the motorself-venting and allow water and humid air to escape.6.2.2 ConductorsTypeStranded copper conductors only.The motor has a plugged drain hole on the drive side. The flangecan be turned 90 to both sides or 180 .B14Temperature rating for conductor insulation: 60 C (140 F).Temperature rating for outer cable sheath: 75 C (167 F).B5TM02 9037 1604B3Temperature ratingFig. 5Drain holes7English (GB)6. Electrical installation5.4 Ensuring motor cooling
6.3.2 Three-phase supply voltage6.3.1 Single-phase supply voltage 3 x 380-500 V - 10 %/ 10 %, 50/60 Hz, PE.Single-phase motors are available for the voltages below: 1 x 200-240 V - 10 %/ 10 %, 50/60 Hz, PE 1 x 90-240 V - 10 %/ 10 %, 50/60 Hz, PE or 30-300 VDC(power supply from a renewable-energy source).CautionCheck that the supply voltage and frequency correspond to thevalues stated on the nameplate.NoteNoteIf the motor is supplied through an IT network, adedicated IT network motor should be used.Contact Grundfos.The wires in the motor terminal box must be as short as possible.Excepted from this is the separated earth conductor which mustbe so long that it is the last one to be disconnected in case thecable is inadvertently pulled out of the cable entry.For maximum backup fuse, see section 15.1 Supply voltage.MGE 71 and MGE 80In order to avoid loose connections, ensure thatthe terminal block for L1, L2 and L3 is pressedhome in its socket when the supply cable hasbeen connected.Corner grounding is not allowed for supplyvoltages above 3 x 480 V, 50/60 Hz.Check that the supply voltage and frequency correspond to thevalues stated on the nameplate.NoteIf the motor is supplied through an IT network, adedicated IT network motor should be used.Contact Grundfos.The wires in the motor terminal box must be as short as possible.Excepted from this is the separated earth conductor which mustbe so long that it is the last one to be disconnected in case thecable is inadvertently pulled out of the cable entry.For maximum backup fuse, see section 16.1 Supply voltage.MGE 90L1L2L1ELCB(GFCI)L2L3Example of a mains-connected motor with mainsswitch, backup fuse and additional protectionL3PEMGE 71 and MGE 80Fig. 8TM05 3942 1812Fig. 6TM05 4034 1912ELCB(GFCI)Example of a mains-connected motor with mainsswitch, backup fuses and additional protectionMGE 90Fig. 7TM05 3495 1512TM05 3494 1512English (GB)6.3 Mains supplyMains connection, single-phase motorsFig. 98Mains connection, three-phase motors
6.4 Additional protection6.4.1 Single-phase motorsIf the motor is connected to an electric installation where an earthleakage circuit breaker (ELCB) or ground fault circuit interrupter(GFCI) is used as additional protection, this circuit breaker orinterrupter must be marked with the following symbol:ELCB(GFCI)NoteWhen an earth leakage circuit breaker or groundfault circuit interrupter is selected, the totalleakage current of all the electrical equipment inthe installation must be taken into account.The motor must be connected to a power supply with a qualitycorresponding to IEC 60146-1-1, class C, to ensure correct motoroperation at phase unbalance.This also ensures long life of the components.6.5 Functional modulesVarious functional modules are available for this product.The selection of module depends on the application and therequired number of inputs and outputs.Possible functional modules: Basic functional module (FM 100) Standard functional module (FM 200)The leakage current of the motor can be found in section15.2 Leakage current. Advanced functional module (FM 300).6.4.2 Motors supplied from a renewable-energy sourceThe descriptions and terminal overviews in this section apply toboth single- and three-phase motors.This section only applies to motor variants designed for supplyfrom a renewable-energy source (1 x 90-240 V - 10 %/ 10 %,50/60 Hz, PE or 30-300 VDC).Overvoltage and undervoltage protectionOvervoltage and undervoltage may occur in case of unstablepower supply or a faulty installation. The motor will be stopped ifthe voltage falls outside the permissible voltage range. The motorwill automatically be restarted when the voltage is again withinthe permissible voltage range. Therefore, no additional protectionrelay is required.NoteThe motor is protected against transients fromthe power supply according to EN 61800-3.In areas with high lightning intensity, werecommend external lightning protection.6.6 Connection terminals on functional modulesFor maximum tightening torques, see section Torques, page 33.6.6.1 Basic functional module (FM 100)The FM 100 has only the most necessary inputs for closed- andopen-loop operation. The module also enables communicationvia a GENIbus connection.The FM 100 has these connections: analog voltage input two digital inputs or one digital input and one open-collectoroutput GENIbus connection.See fig. 10.NoteDigital input 1 is factory-set to be start/stop inputwhere open circuit will result in stop. A jumperhas been factory-fitted between terminals 2 and6. Remove the jumper if digital input 1 is to beused as external start/stop or any other externalfunction.NoteAs a precaution, the wires to be connected to theconnection groups below must be separatedfrom each other by reinforced insulation in theirentire lengths.Overload protectionIf the upper load limit is exceeded, the motor will automaticallycompensate for this by reducing the speed and stop if theoverload condition persists.The motor will remain stopped for 8 seconds. After this period,the motor will automatically attempt to restart. The overloadprotection prevents damage to the motor. Consequently, noadditional motor protection is required.Overtemperature protectionThe electronic unit has a built-in temperature sensor as anadditional protection. When the temperature rises above a certainlevel, the motor will automatically compensate for this byreducing the speed and stop if the temperature keeps rising.The motor will remain stopped for 8 seconds. After this period,the motor will automatically attempt to restart. Inputs and outputThe inputs and output are internally separated from themains-conducting parts by reinforced insulation andgalvanically separated from other circuits.All control terminals are supplied by safety extra-low voltage(SELV), thus ensuring protection against electric shock.6.4.3 Three-phase motors If the motor is connected to an electric installation where an earthleakage circuit breaker (ELCB) or ground fault circuit interrupter(GFCI) is used as additional protection, this circuit breaker orinterrupter must be of the following type:A galvanically safe separation must fulfil the requirements forreinforced insulation including creepage distances andclearances specified in EN 61800-5-1. It must be suitable for handling leakage currents and cutting-inwith short pulse-shaped leakage. It must trips out when alternating fault currents and faultcurrents with DC content, i.e. pulsating DC and smooth DCfault currents, occur.Mains supply (terminals N, PE, L or L1, L2, L3, PE).For these motors an earth leakage circuit breaker or ground faultcircuit interrupter, type B, must be used.This circuit breaker or interrupter must be marked with thefollowing symbols:ELCB(GFCI)NoteWhen an earth leakage circuit breaker or groundfault circuit interrupter is selected, the totalleakage current of all the electrical equipment inthe installation must be taken into account.The leakage current of the motor can be found in section16.2 Leakage current.9English (GB)Protection against phase unbalance
6.6.2 Standard functional module (FM 200)English (GB)The FM 200 has more inputs and outputs than the FM 100 and issuitable for even more demanding applications.The FM 200 has these connections: two analog inputs two digital inputs or one digital input and one open-collectoroutput Grundfos Digital Sensor input and output two signal relay outputs GENIbus connection.See fig. 11.OC 24 V*/5 V* 10 DI3/OC1 4AI12DI15 5 V6GNDAGENIbus AYGENIbus YBGENIbus B* If an external supply source is used, there must be aconnection to GND. NoteAs a precaution, the wires to be connected to theconnection groups below must be separatedfrom each other by reinforced insulation in theirentire lengths.TypeFunction10DI3/OC1Digital input/output,configurable.Open collector: Max. 24 Vresistive or inductive.4AI1Analog input:0.5 - 3.5 V / 0-5 V / 0-10 V2DI1Digital input, configurable5 5 VSupply to potentiometer andsensor6GNDGroundAGENIbus, AGENIbus, A ( )YGENIbus, YGENIbus, GNDBGENIbus, BGENIbus, B (-)Inputs and outputsAll inputs and outputs are internally separated from themains-conducting parts by reinforced insulation andgalvanically separated from other circuits.All control terminals are supplied by safety extra-low voltage(SELV), thus ensuring protection against electric shock.Fig. 10 Connection terminals, FM 100TerminalNoteDigital input 1 is factory-set to be start/stop inputwhere open circuit will result in stop. A jumperhas been factory-fitted between terminals 2 and6. Remove the jumper if digital input 1 is to beused as external start/stop or any other externalfunction.DIGNDTM05 3511 1512 24 V* Signal relay outputs– Signal relay 1:LIVE:Mains supply voltages up to 250 VAC can be connected tothis output.SELV:The output is galvanically separated from other circuits.Therefore, the supply voltage or safety extra-low voltagecan be connected to the output as desired.– Signal relay 2:SELV:The output is galvanically separated from other circuits.Therefore, the supply voltage or safety extra-low voltagecan be connected to the output as desired. Mains supply (terminals N, PE, L or L1, L2, L3, PE).A galvanically safe separation must fulfil the requirements forreinforced insulation including creepage distances andclearances specified in EN 61800-5-1.10
TypeNCNormally closedcontactC1CommonNONormally opencontactNCNormally closedcontactC2CommonNONormally opencontactNCC1NO 24 V* 24 V*OCDIGND 24 V*/5 V*DI3/OC14AI1Analog input:0-20 mA / 4-20 mA0.5 - 3.5 V / 0-5 V / 0-10 V2DI1Digital input, configurable 5 5 VSupply to potentiometer andsensor10 DI3/OC1 4AI12DI15 5 V6GNDAGENIbus AYGENIbus YB36GNDGroundAGENIbus, AGENIbus, A ( )GENIbus BYGENIbus, YGENIbus, GNDGNDBGENIbus, BGENIbus, B (-)15 24 V3GNDGround26 5 V15 24 VSupply23 GND8 24 VSupply26 5 VSupply to potentiometer andsensor23GNDGround25GDS TXGrundfos Digital Sensoroutput24GDS RXGrundfos Digital Sensor input7AI2Analog input:0-20 mA / 4-20 mA0.5 - 3.5 V / 0-5 V / 0-10 V 24 V*/5 V*25 GDS TX 24 V* 24 V24 GDS RX 5 V*7AI2* If an external supply source is used, there must be aconnection to GND.Fig. 11 Connection terminals, FM 200TM05 3510 35128 24 V*Signal relay 2(SELV only)10C2 24 V*Signal relay 1(LIVE or SELV)Digital input/output,configurable.Open collector: Max. 24 Vresistive or inductive.NCNOFunctionEnglish (GB)Terminal11
6.6.3 Advanced functional module (FM 300)English (GB)The FM 300 has a number of inputs and outputs enabling themotor to be used in advanced applications where many inputsand outputs are required.The FM 300 has these connections: three analog inputs one analog output two dedicated digital inputs two configurable digital inputs or open-collector outputs Grundfos Digital Sensor input and output two Pt100/1000 inputs LiqTec sensor inputs two signal relay outputs GENIbus connection.See fig. 12. NoteDigital input 1 is factory-set to be start/stop inputwhere open circuit will result in stop. A jumperhas been factory-fitted between terminals 2 and6. Remove the jumper if digital input 1 is to beused as external start/stop or any other externalfunction.NoteAs a precaution, the wires to be connected to theconnection groups below must be separatedfrom each other by reinforced insulation in theirentire lengths.Inputs and outputsAll inputs and outputs are internally separated from themains-conducting parts by reinforced insulation andgalvanically separated from other circuits.All control terminals are supplied by safety extra-low voltage(SELV), thus ensuring protection against electric shock. Signal relay outputs– Signal relay 1:LIVE:Mains supply voltages up to 250 VAC can be connected tothis output.SELV:The output is galvanically separated from other circuits.Therefore, the supply voltage or safety extra-low voltagecan be connected to the output as desired.– Signal relay 2:SELV:The output is galvanically separated from other circuits.Therefore, the supply voltage or safety extra-low voltagecan be connected to the output as desired. Mains supply (terminals N, PE, L or L1, L2, L3, PE).A galvanically safe separation must fulfil the requirements forreinforced insulation including creepage distances andclearances specified in EN 61800-5-1.12
TypeNCNormally closedcontactC1CommonNONormally opencontactNCNormally closedcontactC2CommonNONormally opencontact18GNDGround11DI4/OC2Digital input/output,configurable.Open collector: Max. 24 Vresistive or inductive.NO19Pt100/1000 input 2Pt100/1000 sensor input18 GND17Pt100/1000 input 1Pt100/1000 sensor input12AOAnalog output:0-20 mA / 4-20 mA0-10 V9GNDGround14AI3Analog input:0-20 mA / 4-20 mA0-10 V1DI2Digital input, configurable21LiqTec sensor input 1LiqTec sensor input(white conductor)20GNDGround(brown and blackconductors)22LiqTec sensor input 2LiqTec sensor input(blue conductor)10DI3/OC1Digital input/output,configurable.Open collector: Max. 24 Vresistive or inductive.4AI1Analog input:0-20 mA / 4-20 mA0.5 - 3.5 V / 0-5 V / 0-10 V2DI1Digital input, configurable5 5 VSupply to potentiometerand sensorNCC1NONCC2 24 V*OCDI11 DI4/OC219 Pt100/100017 Pt100/1000 24 V*/5 V* 24 V* 24 V* 5 V*12AO9GND14 AI31DI221 LiqTec20 GND22 LiqTec 24 V* 24 V* 24 V*OCDIGND 24 V*/5 V* 10 DI3/OC1 4AI12DI15 5 V6GNDAGENIbus AYGENIbus YBGENIbus B3GND15 24 V 24 V23 GND 24 V*/5 V*25 GDS TX 24 V*24 GDS RX 5 V*7AI2* If an external supply source is used, there must be aconnection to GND.Fig. 12 Connection terminals, FM 300TM05 3509 3512826 5 V 24 V*FunctionEnglish (GB)TerminalSignal relay 1(LIVE or SELV)Signal relay 2(SELV only)6GNDGroundAGENIbus, AGENIbus, A ( )YGENIbus, YGENIbus, GNDBGENIbus, BGENIbus, B (-)3GNDGround15 24 VSupply8 24 VSupply26 5 VSupply to potentiometerand sensor23GNDGround25GDS TXGrundfos Digital Sensoroutput24GDS RXGrundfos Digital Sensorinput7AI2Analog input:0-20 mA / 4-20 mA0.5 - 3.5 V / 0-5 V / 0-10 V13
7. Operating conditions6.7 Signal cablesUse screened cables with a cross-sectional area of min.0.5 mm2 and max. 1.5 mm2 for external on/off switch, digitalinputs, setpoint and sensor signals. 7.1 Maximum number of starts and stopsConnect the screens of the cables to frame at both ends withgood connection. The screens must be as close as possible tothe terminals. See fig. 13.The number of starts and stops via the power supply must notexceed four times per hour.When switched on via the power supply, the motor will start afterapprox. 5 seconds.If a higher number of starts and stops is desired, use the input forexternal start/stop when starting/stopping the motor.When started via an external on/off switch, the motor will startimmediately.TM02 1325 44027.2 Ambient temperature Screws for frame connections must always be tightenedwhether a cable is fitted or not. The wires in the motor terminal box must be as short aspossible.7.2.1 Ambient temperature during storage and transportationMinimum -30 CMaximum 60 C.7.2.2 Ambient temperature during operationMinimum -20 CFig. 13 Stripped cable with screen and wire connectionsMaximum 50 C.The motor can operate with the rated power output (P2) at 50 C,but continuous operation at higher temperatures will reduce theexpected product life. If the motor is to operate at ambienttemperatures between 50 and 60 C, an oversized motor must beselected. Contact Grundfos for further information.6.8 Bus connection cable7.3 Installation altitude6.8.1 New installationsFor the bus connection, use a screened 3-core cable with across-sectional area of min. 0.5 mm2 and max. 1.5 mm2.Caution If the motor is connected to a unit with a cable clamp which isidentical to the one on the motor, connect the screen to thiscable clamp. If the unit has no cable clamp as shown in fig. 14, leave thescreen unconnected at this end. Motors installed up to 1000 metres above sea level can beloaded 100 %. Motors installed more than 1000 metres above sea level mustnot be fully loaded due to the low density and consequent lowcooling effect of the air. See fig. 16.A2Y31BBP2[%]TM05 3973 1812A 1Y 23The motor must not be installed more than2000 metres above sea level.Installation altitude is the height above sea level of the installationsite.Motor1008060406.8.2 Replacing an existing motor 20If a screened 2-core cable is used in the existing installation,connect it as shown in fig. 15.00MotorAY12B12141000150020002500Altitude [m]Fig. 16 Derating of motor output (P2) in relation to altitudeabove sea level7.4 Air humidityAYBFig. 15 Connection with screened 2-core cable 500TM05 5243 3512Fig. 14 Connection with screened 3-core cableTM02 8842 0904English (GB) If a screened 3-core cable is used in the existing installation,follow the instructions in section 6.8.1 New installations.Maximum air humidity: 95 %.If the air humidity is constantly high and above 85 %, the drainholes in the drive-end flange should be open.See section 5.6 Drain holes.7.5 Motor coolingTo ensure cooling of m
The ability to draw current into the terminal and guide it towards GND in the internal circuitry. Current sourcing The ability to push current out of the terminal and into an external load which must return it to GND. DI Digital input. DO Digital output. ELCB Earth leakage circuit breaker. FM Functional module. GDS Grundfos Digital Sensor.