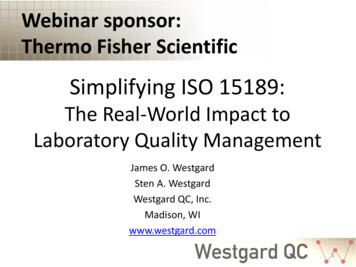
Transcription
Webinar sponsor:Thermo Fisher ScientificSimplifying ISO 15189:The Real-World Impact toLaboratory Quality ManagementJames O. WestgardSten A. WestgardWestgard QC, Inc.Madison, WIwww.westgard.com1
Need for improvements in qualityand patient safety Plebani M. Clin Chem Lab Med 2013;51:39-46.– A better analytical quality should be achieved by setting andimplementing evidence-based analytical quality specifications ineveryday practice;– If this will be done, rules for internal quality control and externalquality assessment procedures would be more appropriate.– Moreover, there is a compelling need for standardized programsimproving metrological traceability and correcting biases andsystematic errors.– Finally, more stringent metrics, such as Six Sigma, should belargely introduced in clinical laboratory to further improvecurrent analytical quality.2
Need for a “scientifically basedquality control process” Jassam N, et al. Clin Chem Lab Med 2013;51:1579-84– The implementation of national and internationalguidelines is beginning to standardize clinical practice.– There is an urgent need to ensure that differentlaboratories obtain the same analytical results on anysamples.– A scientifically based quality control process will be a prerequisite to provide this level of analytical performancewhich will support evidence-based guidelines andmovement of patients across boundaries whilemaintaining standardized outcomes.3
Purpose and Objectives Purpose: Understand ISO 15189 as a ScientificQuality Management System– Utilize Deming’s “Plan-Do-Check-Act” (PDCA)methodology as your “process”– Recognize that ISO 15189 requirements fit into thePDCA process model– Implement a Six Sigma Quality ManagementSystem (6σQMS) that provides tools and metricsfor scientific quality management4
Total Quality ManagementPerspective on Medical LabLaboratory Testing ProcessPre-analyticPhaseAnalyticPhasePost- analyticPhaseLaboratory Management5
ISO 15189 PerspectiveTechnical Requirements5.1 Personnel, 5.2 Accommodation & environmental conditions5.3 Laboratory equipment, reagents, and cess5.5-5.6PostexaminationProcess5.7-5.104.1 Organization and management responsibility4.2 Quality management system4.3 Document control; 4.4 Service agreements4.5 Examination by referral laboratories4.6 External services and supplies4.7 Advisory services; 4.8 Resolution of complaints4.9 Identification and control of nonconformities4.10 Corrective actions; 4.11 Preventive actions4.12 Continual improvement; 4.13 Control of records4.14 Evaluation and audits; 4.15 Management reviewISO 15189 Management Requirements6
ISO 15189 Requirements forQuality and Competence 2012 revision is 3rd edition Committee chaired by Dr. David Burnett andLucia Berte Burnett has also updated his book– “A Practical Guide to ISO 15189 in LaboratoryMedicine.” ACB Publications, 2013, 372 pages– Added information and guidance on Six Sigma,including selection of SQC procedures on basis ofsigma quality7
Simplifying ISO 15189Make it a PDCA process, not a list! Don’t think of ISO 15189 as a long list ofrequirements– Document isn’t organized and ordered to showthe “flow” of requirements into a process– Better to understand and organize thoserequirements for a process and system Think 1st about process for implementing QMS Think 2nd about a process for managing quality– Use Deming’s Plan-Do-Check-Act (PDCA) cycle8
Understanding QualityManagement Systems W. Edwards Deming described a system as aseries of functions or activities within anorganization that work together for the aim ofthe organization.”– Deming talked about “optimization of the system”as the role of management In the 1950s, Deming helped Japan rebuild theirindustries; In the 1980s-90s, Deming helped Americanindustry implement Total Quality Management (TQM)9
Developing a QMSDeming’s PDCA CyclePLANACTDOCHECKDeming’s PDCA describes the “Scientific Method” whichprovides the foundation for Quality Management Systems10
Burnett’s “Process Model”for ISO 15189Organization/Management4.1 Organization & Management Responsibility4.4 Service agreements4.15 Management review4.2 Quality Management System4.3 Document control4.13 Control of recordsEvaluation & Improvement4.8 Resolution of complaints4.9 Identification & control non-conformities4.10 Corrective action4.12 Continual improvement4.14 Evaluation and internal audit5.6 Ensuring quality of results (in part)Resource Management5.1 Personnel5.2 Accommodations, environmental conditions5.3 Equipment, reagents, consumables5.9 Laboratory information management4.6 External service and suppliesExamination Processes4.5 Examination by referral laboratories4.7 Advisory services5.4 Pre-examination processes5.2 Examination processes5.6 Ensuring quality of examinations5.7 Post examination processes5.8 Reporting of results11
Introduced at 2014 AACCMeeting, Chicago1st half considersImplementation ofISO 15189 Managementand Technical Requirements2nd half focuses on Six SigmaQMS for Analytical QualityManagementIntroduces 2 new tools“Westgard Sigma Rules”and “Proficiency AssessmentChart”290 pages12
Simplifying ISO 15189Implementation Strategies Select a Quality Manager to guide process– Coordinate development and implementation Assemble a “Management Planning Team”– Focus on management requirements– Perform a Gap analysis to prioritize neededchanges and improvements Appoint a “Technical Planning Team”– Focus on technical requirements– Develop Six Sigma QMS (6σQMS)13
Simplifying ISO 15189Management Planning Team (MPT)Develop QMS Plan (PLAN)Implement Plan (DO)1. Commit to QMS2. Select a quality manager3. Formulate a quality policy4. Establish Man. Plan. Team5. Provide initial training6. Define Q goals, objectives7. Review ISO 151898. Perform “gap analysis”9. Prioritize improvements10. Develop action plan1. Start a quality manual2. Establish a documentcontrol system3. Assign individual tasks4. Assign MPT projects5. Assign project teams6. Expand quality training7. Document policies,processes, procedures,forms for recordsManagement review (ACT)1.2.3.4.5.Review quality manualSelect accreditorReview application processPerform pre-assessmentIdentify/prioritize needs forimprovement (go to P10)Monitor Progress (CHECK)1.2.3.4.Monitor tasks/projectsSelect quality indicatorsMonitor non-conformitiesFormalize internal auditprocesses , procedures,and reports14
Simplifying ISO 15189Divide up the work!Action Plan for QMSImplementation ofManagement RequirementsMPT rt qualitymanualPrepareorganization chartDescribe extent ofservices .1.2.3.4.5.Establishdocument controlsystemFormulatemanagementpoliciesExpand qualitytrainingMonitor quality &performance .Project TeamAssignments1. Flowchart processesfor preexamination,examination, andpost –examination2. Implement qualityindicators3. .15
Simplifying ISO 15189Technical Planning Team (TPT)Action Plan for QMSImplementation ofTechnical RequirementsTPT AssignmentsPolices and Processes1. Identify customers2. Flowchart total testing process3. Define policies and processesfor determining customerrequirements4. Standardize policies andprocesses for methodverification & validation5. Select quality indicators6. Define policies and processesfor design of QC procedures,selection of indicators,determination of measurementuncertaintyProject Assignments.Procedures and Forms1. Flowchart pre-examination,examination, and postexaminations processes2. Review/standardize SOPs3. Implement verification andvalidation protocols4. Implement SQC design5. Implement quality indicatorsincluding measurementuncertainty16
Simplifying ISO 15189Adopt PDCA for Scientific 6σQMSPLANDO1. Define goals for intended use basedon reg/accred requirements andclinical and medical applications2. Select analytic measurementprocedure; consider traceability andmanufacturer’s reference methodsand materials3. Validate method performance orverify manufacturer’s claims4. Implement method and analyticsystem and address pre-analyticand post-analytic requirements; 4a.Train analysts and operators in newanalytic systemACTCHECK10. Measure quality and performancewith EQA/PT and MU.11. Monitor failures with qualityindicators12. Prioritize problems/issues and planimprovements5.6.7.8.9.Formulate Sigma QC strategySelect/design SQCDevelop QC PlanImplement QC PlanVerify attainment of intended qualityof test results17
6σQMS(1a) Regulatory &Accred .Requirements(1) Define Goals forIntended Use (TEa, Dint)(1b) Clinical andMedical Applications(2a) Traceability &Harmonization(2) Select AnalyticMeasurement Procedure(2b) Manufacturer’sRef Methods & Materials(4b) Pre- and Post-analyticRequirements(12) Improve Quality,TQC Plan [CQI, CAPA](3) Validate MethodPerformance (CV,bias)(3a) Manufacturer’sClaims(4) Implement Methodand Analytic System(4a) Manufacturer’sInstallation/Training(5) Formulate“Total QC Strategy”(5a) Sigma[(TEa-Bias)/CV](6) Select/DesignSQC (rules, N)(6a) SigmaQC Selection Tool(11) Monitor FailuresFRACAS. Quality Indicators(7) DevelopTotal QC Plan(7a) Risk Analysis(10) Measure Quality &Performance (EQA, PT, MU)(8) ImplementAnalytic TQC Plan(8a) QC Tools(9) Verify Attainment ofIntended Quality18
6σQMS(1a) Regulatory &Accred .Requirements(2a) Traceability &Harmonization(4b) Pre- and Post-analyticRequirements(12) Improve Quality,TQC Plan [CQI, CAPA](1) Define Goals forIntended Use (TEa, Dint)(1b) Clinical andMedical Applications(2) Select AnalyticMeasurement Procedure(2b) Manufacturer’sRef Methods & MaterialsPlan(3) Validate MethodPerformance (CV,bias)(3a) Manufacturer’sClaims(4) Implement Methodand Analytic System(4a) Manufacturer’sInstallation/Training(5) Formulate“Total QC Strategy”(5a) Sigma[(TEa-Bias)/CV](6) Select/DesignSQC (rules, N)(6a) SigmaQC Selection Tool(11) Monitor FailuresFRACAS. Quality Indicators(7) DevelopTotal QC Plan(7a) Risk Analysis(10) Measure Quality &Performance (EQA, PT, MU)(8) ImplementAnalytic TQC Plan(8a) QC Tools(9) Verify Attainment ofIntended Quality19
6σQMS(1a) Regulatory &Accred .Requirements(2a) Traceability &Harmonization(4b) Pre- and Post-analyticRequirements(12) Improve Quality,TQC Plan [CQI, CAPA](1) Define Goals forIntended Use (TEa, Dint)(1b) Clinical andMedical Applications(2) Select AnalyticMeasurement Procedure(2b) Manufacturer’sRef Methods & MaterialsPlan(3) Validate MethodPerformance (CV,bias)(3a) Manufacturer’sClaims(4) Implement Methodand Analytic System(4a) Manufacturer’sInstallation/Training(5) Formulate“Total QC Strategy”(5a) Sigma[(TEa-Bias)/CV](6) Select/DesignSQC (rules, N)(6a) SigmaQC Selection ToolDo(11) Monitor FailuresFRACAS. Quality Indicators(7) DevelopTotal QC Plan(7a) Risk Analysis(10) Measure Quality &Performance (EQA, PT, MU)(8) ImplementAnalytic TQC Plan(8a) QC Tools(9) Verify Attainment ofIntended Quality20
6σQMS(1a) Regulatory &Accred .Requirements(2a) Traceability &Harmonization(4b) Pre- and Post-analyticRequirements(12) Improve Quality,TQC Plan [CQI, CAPA](1) Define Goals forIntended Use (TEa, Dint)(1b) Clinical andMedical Applications(2) Select AnalyticMeasurement Procedure(2b) Manufacturer’sRef Methods & MaterialsPlan(3) Validate MethodPerformance (CV,bias)(3a) Manufacturer’sClaims(4) Implement Methodand Analytic System(4a) Manufacturer’sInstallation/Training(5) Formulate“Total QC Strategy”(5a) Sigma[(TEa-Bias)/CV](6) Select/DesignSQC (rules, N)(6a) SigmaQC Selection ToolDoCheck(11) Monitor FailuresFRACAS. Quality Indicators(7) DevelopTotal QC Plan(7a) Risk Analysis(10) Measure Quality &Performance (EQA, PT, MU)(8) ImplementAnalytic TQC Plan(8a) QC Tools(9) Verify Attainment ofIntended Quality21
6σQMS(1a) Regulatory &Accred .Requirements(2a) Traceability &Harmonization(4b) Pre- and Post-analyticRequirementsAct(12) Improve Quality,TQC Plan [CQI, CAPA](1) Define Goals forIntended Use (TEa, Dint)(1b) Clinical andMedical Applications(2) Select AnalyticMeasurement Procedure(2b) Manufacturer’sRef Methods & MaterialsPlan(3) Validate MethodPerformance (CV,bias)(3a) Manufacturer’sClaims(4) Implement Methodand Analytic System(4a) Manufacturer’sInstallation/Training(5) Formulate“Total QC Strategy”(5a) Sigma[(TEa-Bias)/CV](6) Select/DesignSQC (rules, N)(6a) SigmaQC Selection ToolDoCheck(11) Monitor FailuresFRACAS. Quality Indicators(7) DevelopTotal QC Plan(7a) Risk Analysis(10) Measure Quality &Performance (EQA, PT, MU)(8) ImplementAnalytic TQC Plan(8a) QC Tools(9) Verify Attainment ofIntended Quality22
Simplifying ISO 15189Define Policies, Processes, Procedures The laboratory should define policies,processes, and procedures in a QualityManual to document the implementation ofits Quality Management System– Policies: Describes what is to be achieved– Processes: Describes activities to implement apolicy– Procedures: Provides step by step directions foractivities23
ISO 15189Intended Use, Intended Quality 5.5.1.1 Selection, Validation– The laboratory shall select examination procedures whichhave been validated for their intended use.– The specified requirements (performance specifications)for each examination procedure shall relate to theintended use of that examination. 5.6.2.1 Quality Control– The laboratory shall design quality control procedures thatverify the attainment of the intended quality of results.24
Example ApplicationQuality Required for Intended Use Policy - Quality requirement shall be defined for each test toidentify critical performance characteristics that must beachieved to satisfy the intended clinical use of each laboratorytest. Process – Analytical goals shall be established for each testbased on an assessment of specific clinical diagnostic andtreatment requirements for the test, goals based on biologicvariability, criteria for performance in PT and EQA programs,and “state of the art” performance Procedure – Select specific analytical goal, or qualityrequirement, by comparison of different quality requirementsusing an error grid.25
Example – Quality Goals for HbA1cComparison of CAP, NGSP, ADAHbA1c Error Grid10.00NGSP HiNew Method Value (%Hb)9.00CAP PT-Hi8.00Y X7.00CAP PT-LoNGSP 0Reference Method Value (%Hb)CAP NGSP 6%, as demanding as ADA clinicaldiagnostic and treatment criteria26
ISO 15189Validation of Examination Procedures Section 5.5.– The laboratory shall select examination procedures whichhave been validated for their intended use – The specified requirements (performance specifications)for each examination shall relate to the intended use ofthat examination– The independent verification by the laboratory shallconfirm through obtaining objective evidence that theperformance characteristics for the examination procedureare met.27
Validation of Examination Procedures Policy - The laboratory shall validate the performancecharacteristics to ensure the quality required for intended useis achieved. Process - The laboratory shall employ an evaluation studythat includes experiments for analytic range, replication,comparison of methods, confirmation of reference ranges,and when appropriate, detection limit, interference, andrecovery. Experimental results should be analyzed graphicallyand statistically and the sigma-metric determined to judge theacceptability for the intended use.28
Validation of Examination Procedures Procedure - Preparation of a Method Decision Chart todetermine quality on the sigma scale and assess theacceptability of precision and accuracy for intended use.1.2.3.4.5.6.7.Define the quality requirement for the test in the TEa format.Scale the y-axis from 0 to TEa and the x-axis from 0 to TEa/2.Draw “sigma lines” for 2, 3, 4, 5, and 6σ, e.g., 2σ line has y-intercept ofTEa and x-intercept of TEa/2; 3σ y-int of Tea, x-int of TEa/3; 4σ y-int TEa, x-int TEa/4; 5σ y-int TEa, x-int TEa/5; 6σ Y-int TEa, x-int TEa/6.Obtain %CV from the replication experiment.Obtain %Bias from the comparison of methods experiment.Plot an “operating point” that has %Bias as the y-coordinate and %CV asthe x-coordinate.Assess sigma-quality from location of the operating point.29
Simplifying Method ValidationUse a Method Decision ChartMethod Decision Chart TEa 6.0%Accuracy - observed %Bias652-sigma3 sigma4 sigma5 sigma6 sigmaRegion 511.522.53Precision - observed %CV30
Goal is Six Sigma Quality!- Tolerance TargetSpecification-6 SDsshould fitinto spec ToleranceSpecification 6 SDsshould fitinto spec-6s -5s -4s -3s -2s -1s 0s 1s 2s 3s 4s 5s 6s31
Minimum Acceptable Quality is 3σ!- Tolerance TargetSpecification-3s-2s-1s0s ToleranceSpecification1s2s3s32
Simplifying Method ValidationCalculate a oleranceLimitBias TEaSigma TEa-BiasSDSD-6s -5s -4s -3s -2s -1s 0s 1s 2s 3s 4s 5s 6s33
Simplifying Method ValidationCalculate a Sigma-metric Sigma (TEa – Bias)/SD– TEa, allowable Total Error– Bias, inaccuracy of the method Initially from comparison of methods exp. Ongoing from PT/EQA survey or Peer Comparisonprogram– SD or CV, imprecision of the method Initially from replication experiment On-going from routine SQC data– All terms in either % or concentration units34
Example Calculations of Sigma Sigma (TEa – Bias)/CV Glucose, TEa 10%– Bias 1.0, CV 1.5%– Sigma (10.0-1.0)/1.5 6.0 HbA1c, TEa 6.0%– Bias 1.0%, CV 1.5%– Sigma (6.0-1.0%)/1.5% 3.3335
ISO 15189Quality Control 5.6.2.1– The laboratory shall design quality controlprocedures that verify the attainment of theintended quality of results. Must have defined “intended quality” Must have QC selection/design process that relates thequality required with the precision and accuracy of theexamination procedure and the rejection characteristicsof different control rules and different numbers ofcontrol measurements36
Simplifying QC DesignUse quality-planning tools Select SQC procedures on basis of observedsigma quality of examination procedures– Sigma QC Selection tool Described in CLSI C24A3– Charts of Operating Specifications Available from Westgard QC publications, website– “Westgard Sigma Rules” graphic tool Available from Thermo Fisher Scientific– http://thermoscientific.com/westgard-poster37
Westgard Sigma RulesTM2 Levels of ControlsDataQCReport ResultsNo13sNo22sYesR4sYesN 2R 1NoYesN 2R 1No8X41sYesN 4R 1NoYesN 2R 2N 4R 2N 2R 4Take Corrective Action6σ5σ4σ3σSigma Scale (%TEa-%Bias)/%CV38
Westgard Sigma RulesTM2 Levels of ControlsDataQCReport ResultsNo13sNo22sYesR4sYesN 2R 1NoYesN 2R 1No8X41sYesN 4R 1NoYesN 2R 2N 4R 2N 2R 4Take Corrective Action6σ5σ4σ3σSigma Scale (%TEa-%Bias)/%CV39
HbA1c: TEa 6.0%, Bias 1.0%,CV 1.0%, Sigma (6-1)/1 5DataQCReport ResultsNo13sNo22sYesR4sYesN 2R 1NoYesN 2R 1No8X41sYesN 4R 1NoYesN 2R 2N 4R 2N 2R 4Take Corrective Action6σ5σ4σ3σSigma Scale (%TEa-%Bias)/%CV40
HbA1c: TEa 6.0%, Bias 1.0%,CV 1.0%, Sigma (6-1)/1 5DataQCReport ResultsNo13sNo22sYesYesN 4R 1No8XYesLocate SigmaN 2R 1No41sR4sYesN 2R 1NoYesN 2R 2N 4R 2N 2R 4Take Corrective Action6σ5σ4σ3σSigma Scale (%TEa-%Bias)/%CV41
HbA1c: TEa 6.0%, Bias 1.0%,CV 1.0%, Sigma (6-1)/1 5DataQCReport ResultsNo13sNo22sYesYesN 4R 1No8XYesLocate SigmaN 2R 1No41sR4sYesN 2R 1NoYesN 2R 2N 4R 2N 2R 4Take Corrective Action6σ5σ4σ3σSigma Scale (%TEa-%Bias)/%CV42
Glucose: TEa 10.0%, Bias 1.0%,CV 1.5%, Sigma (10-1)/1.5 6DataQCReport ResultsNo13sNo22sYesR4sYesN 2R 1NoYesN 2R 1No8X41sYesN 4R 1NoYesN 2R 2N 4R 2N 2R 4Take Corrective Action6σ5σ4σ3σSigma Scale (%TEa-%Bias)/%CV43
Glucose: TEa 10.0%, Bias 1.0%,CV 1.5%, Sigma (10-1)/1.5 6DataQCReport ResultsNo13s22sYesNoR4sYesLocate SigmaN 2R 16σNoYesN 2R 1No8X41sYesN 4R 1NoYesN 2R 2N 4R 2N 2R 4Take Corrective Action5σ4σ3σSigma Scale (%TEa-%Bias)/%CV44
Why a low sigma is bad!Sigma-metric 3.0DataQCReport ResultsNo13sNo22sYesR4sYesYesN 2R 1No8X41sYesN 4R 1NoYesN 2R 2N 4 N 2R 2 R 4Take Corrective Action6σ5σ4σ3σLocate SigmaN 2R 1NoSigma Scale (%TEa-%Bias)/%CV45
ISO 15189Measurement Uncertainty (MU) 5.5.1.4– The laboratory shall define the performancerequirements for the measurement uncertainty ofeach measurement procedure and regularlyreview estimates of measurement uncertainty.– The laboratory shall consider measurementuncertainty when interpreting measured quantityvalues.– Upon request, the laboratory shall make itsestimates available to laboratory users.46
Simplifying MUUse “Intermediate” QC data 5.5.1.4 Note 2– Measurement uncertainties may be calculatedusing quantity values obtained by themeasurement of quality control materials underintermediate precision conditions that include asmany routine changes as reasonably possible inthe standard operation of a measurementprocedure, e.g., changes of reagent and calibratorbatches, different operators, scheduled instrumentmaintenance.47
Intermediate Precision Conditions Should be long enough time period to includechanges of calibration, calibrator lots, reagentlots, different operators, instrumentmaintenance Recommend at least 100 data points– Confidence interval for SD is about 10%– Approximately 3 to 4 months data would be theminimum time period48
Simplifying Measurement Uncertainty Policy - The laboratory shall evaluate theuncertainty of measurement for eachexamination procedure where precision dataare available from stable control materials. Process - The laboratory shall determinestandard measurement uncertainty from SQCdata obtained under intermediate precisionconditions.49
ISO 15189Review of Estimates of MU 5.5.1.4 The laboratory shall define the performancerequirements for the measurement uncertainty ofeach measurement procedure and regularly reviewestimates of measurement uncertainty. Process - The laboratory shall compare estimates ofstandard measurement uncertainty to theperformance required for intended use of theexamination procedure by determination of sigmametrics.50
Simplifying MUCalculate Sigma-metric Procedure - Define TEa, estimate SD fromintermediate QC data Sigma (%TEa)/%CV– Where %TEa is PT or EQA requirement foracceptable performance– %CV is determined from laboratory’s intermediateterm SQC data51
ISO 15189External Quality Assessment 5.6.3.1 Interlaboratory comparison– The laboratory shall participate in anintralaboratory comparison programme [PT, EQA]appropriate to the examination andinterpretations of examination results.– The laboratory shall monitor the results andparticipate in the implementation of correctiveactions when predetermined performance criteriaare not fulfilled.52
CAP 2014 HbA1c 6.97 %Hb53
Sigma Proficiency AssessmentCAP 2014 GH2-02 6.97%Hb6.0Observed Inaccuracy 4.0-5.0-6.00.0 0.5 1.0 1.5 2.0 2.5 3.0 3.5 4.0 4.5 5.0 5.5 6.0Observed Imprecision (%CV)54
Summary: Simplifying ISO 15189Development/Implementation Select Quality Manager Assemble Management Planning Team– Adopt PDCA for management requirements– Define policies, processes, procedures Appoint Technical Planning Team– Adopt PDCA for scientific technical requirements– Integrate Six Sigma concepts and tools Method Decision Chart, calculation of sigma-metrics QC Planning tools, such as “Westgard Sigma Rules”55
Summary: Simplifying ISO 15189Plan and DO Stages of 6σQMS Define quality requirements in form of TEa Select examination procedures with attentionto traceability Validate examination performance by– Use Method Decision Chart– Calculate sigma-metric Implement examination procedures– Training for use of SOPs56
Summary: Simplifying ISO 15189Check and Act Stages of 6σQMS Select/design SQC procedures for the sigmaquality achieved by the method Estimate Measurement Uncertainty fromintermediate QC data Assess acceptability of MU by calculation ofsigma-metric Assess acceptability of bias from PT/EQA bycalculation of sigma-metric57
Thank you for your kind attention!58
Any Questions?MUCH, MUCH MORECan be found onlineAt www.westgard.com59
Simplifying ISO 15189 Make it a PDCA process, not a list! Don't think of ISO 15189 as a long list of requirements -Document isn't organized and ordered to show the "flow" of requirements into a process -Better to understand and organize those requirements for a process and system Think 1st about process for implementing QMS