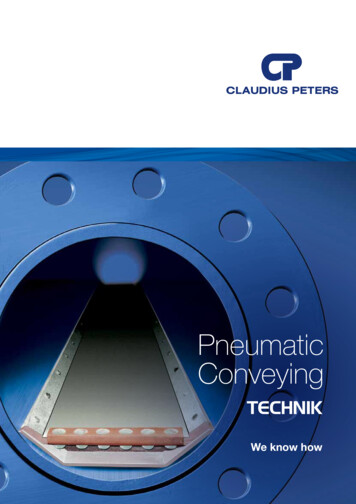
Transcription
PneumaticConveyingTECHNIKWe know how
pneumatic conveying technikAboutSince its founding in 1906, Claudius Peters has become one of the world’smost respected engineering houses and an innovative world leader. Its GermanContentsTechnikum3engineering excellence continues to set benchmarks for the design, manufacturePlant design4and commissioning of materials handling and processing systems for theFLUIDCON6gypsum, cement, coal, alumina, steel and bulk-handling industries.Type 1: Pressurevessel conveyorFrom conception and installation through to commissioning and after-sales8Type 2: X-Pump10Type 3: Airlift12Type 4: Rotary feeder TWA 14Type 5: Jet feeder15support, Claudius Peters provides world-class service to the world’s biggestbulk materials producers.The Claudius Peters Group GmbH is headquartered in Buxtehude near Hamburg,Germany, with regional offices in the Americas, Asia and Europe.Claudius Peters is one of the world’s leadingsuppliers of pneumatic systems for the conveyingof dry bulk materials.With experience in the handling and analysis ofover 13,000 different types of bulk solid, ClaudiusPeters can determine the precise conveyingprocedure for any requirement.Claudius Peters’ service includes delivery of acomplete plant, from examination of bulk solidsthrough selection of conveying system withauxiliary components to installation and plantClaudius Peters’ headquarters, Buxtehude, Germany.commissioning.Design of required pneumatic equipment (including bulk solid feeders, air supply equipment,conveying pipelines and the air/solid classifiers)can come from a client’s specification or fromClaudius Peters’ own material sample analysis.2
TechnikumThe Claudius Peters Technikum (Technical Center) offers clients a laboratorywith facility to test all bulk solid conveying systems.Extensive testing, backed by years of experienceEach material is measured for deaeration time,enables Claudius Peters to design and producedensity, humidity and wall friction angle, withconveying systems which combine high reliabilitydata documented in a test report supported bywith minimal power consumption.EDP and used to ensure optimal plant design.State-of-the-arttechnology to meetevery conveyingrequirementWith conveying lines up to 5km long and a widerange of pipe diameters, the laboratory enablesthe design and supply of systems which havebeen calculated for optimal process, cost andoperating parameters.In the Technikum, conveying procedures canbe tested for any load, gas velocity, conveyingpressure and conveying distance.Claudius Peters Technikum.Customer enquiryMaterial known?YesTest reportNoYesNoConveying tests are runMaterial characteristicsAnglePressureParticle densityBulk densityMaterial behaviour: Sticky Abrasive AlkalineSpec, surface etc.Already been conveyed?WeightpercentageA test report is elaboratedDiameterGrain size distributionDetermination ofconveying procedureLean phaseVelocityTimeVenting onsumptionhighhighlowlowDimension of conveying routeNoLean phase conveyanceDefinition of solids feederStrand conveyanceOptimun configuration?Dune conveyanceYesDesign completedThe Claudius Peters, DIN EN ISO 9001 certified working procedure.Dense phasePlug conveyance3
plant designDetermining the conveying processThorough testingdelivers optimalpower efficiencyCharacteristics of bulk materials, determined from sample analysis, are usedin configuration of the plant.A typical plant consists of a bulk solids feeder,The appropriate conveying procedure isa pressure generator, conveying pipe anddetermined by results from the bulk solids testa separator.and the conveying tests, along with thecustomer’s basic conveyance data. OnceThe Geldart diagram (below) shows howthis is determined, the plant can be designedClaudius Peters classifies bulk solids, with greyfor optimal power efficiency. The requiredareas showing materials which can easily betask and the bulk solid’s behaviour will thenconveyed in a dense phase mode.determine selection of the conveying mode.Density difference particle - gas (kg/m3)10,000DB1,000AC10010100Medium particle size (μm)4Geldart diagram.1,00010,000
Feeder selectionClaudius Peters delivers positive pressure conveying systems.The diagram (below) illustrates the structure of aTypes of feeders for plant configurationpositive pressure conveying system, whereThe chart (bottom) shows the variety andquantities of bulk solids are introduced into thefeatures of available feeders along with theirconveyor pipe against the conveying pressure,standardized range of applications. Claudiusresulting in no air leakage losses. Claudius PetersPeters can also supply solutions for ranges notoffers a complete range of feeder types.included in the chart.A feeder typefor everypossible systemMaterials conveyedSolids feederConveying pipePressureaggregateGas-solidsSeparatorConveying gasMaterial conveyedPressure vesselX-PumpAll non-adhesivematerialsWide particlesize distributionwith fine sharesAirliftRotary feederJet feederFluidisablematerialsCoarse andfine materialslow abrasionAll materialsMax.throughput[ m3/h ]150 (single)300 (twin)640100077010Max. conveyingdistance[m]35001500120vertical30075Max. pressuredifference inconveyor pipe[ bar ]302,50,6vertical0,70,25
FLUIDCONPneumaticconveying, withconsiderablylower powerconsumptionThe Claudius Peters FLUIDCON system offers the advantages of pneumaticconveying with considerably lower energy requirements owing to it’s uniqueaeroslide transportation principle within the transport pipe.Additionally, FLUIDCON provides a dense phaseTo transport the material, transport air travelssystem with increased bulk material load andperpendicular to the fluidized air and passes incan be used to convey all fine bulk solids thatan axial direction. The pressure loss of thecan be fluidized with low air velocities, expandingtransport air flow substitutes for the inclinationhomogeneously during the process. Dependingof the aeroslide. The aeroslide principle turnson the transport pipe routing chosen, it canthe bulk solids into a fluid state with minimalinternal friction and ensures that it remainssubstantially reduce power consumptionfluidized away from the bottom of the pipe andAbout FLUIDCONin the gas flow. These optimum conveyingFLUIDCON is a conveyor pipe that canconditions allow the transportation of solidspartially or completely fluidize material overwith lowest axial driving gas velocities in thethe horizontal length of the pipe (the aeroslidefeed point and acceleration section of the pipe.principle). The air is used to fluidize but notIt is therefore possible to convey materials withtransport the material.the FLUIDCON system using minimal differentialpressure through uphill inclines of up to 30 .Detail of FLUIDCON pipe.100P (pneumatic) / P (belt)Advantages of FLUIDCONConventionalConveyance32n R educed operating costs. Substantiallyless energy consumption. Compared toconventional pneumatic nveying distance [ m ]Schematic of FLUIDCON transport.68001000n H igh availability. The system is easilystarted or restarted even when solidsremain in the conveying linen G entle material handling. This is due tolower conveying velocities starting atapproximately 2-3m/s and ending atapproximately 5-10m/sn A lternative feed systems. With areduction in the conveying pressure,Claudius Peters X-pumps (screw pumps)can be installed instead of conventionalpressure vessels to ensure savings inheight and capital costs
The Claudius Peters FLUIDCON System hasproven to be a valuable alternative in bulkn Lower investment costmaterials handling applications.n Lower gas and solids velocitiesAdditionally this type of system can be utilized inash removal plants where it is particularlysuitable for the removal of fly ash from an Lower conveying pressuren Reduced wearn Lower power requirementbaghouse or ESP. The fly ash discharge pointsn Lower installation heightare connected to a common FLUIDCONn Simplified material feedingconveying pipe and the ash is continuouslyFLUIDCON pipe feeder.removed and can be conveyed long distances.The application of the FLUIDCON system forconveying dust beneath filter installations offersa number of advantages compared to otherconveying technologies.Conveyance of 150t/h fly ash at the Trianel Power Plant Lünen.Schematic of power plant fly ash handling.Rotary Feeder with FLUIDCON.M7
type 1: pressure vessel conveyorConveying solutions for distances up to 3,500 mFully customized,highly efficientThe main features of pressure vesselconveying are:n High availabilityn Low maintenance requirementsn Partial load operationn Suitable for dense phase conveyancen Appropriate for all types of bulk solidsn Available in sizes up to 50m3n Conveying distances up to 3,500mn Conveying pressures up to 30 barn S uitable for systems with top orbottom dischargePressure vessel transport system.The main principlesof pressure vesselconveyance are:1. Filling2. Pressurizing3. Conveying4. Venting8Schematic of transport cycle.
Solids can be conveyed by single, twin ordouble-storey vessels as required.A range of flexibleexpansion optionsSingle pressure vessel conveyance:n Batch conveyancen Maximum capacity 150m3/hn Fully automaticn Simple, low costsTwin pressure vessel conveyance:n Quasi-continuous conveyancen Maximum capacity 300m3/hn Fully automaticn 50% reserve in case of vessel failurePressure vessel system.Throughput for single pressure vessel (for example cement).Double-storey vessel conveyance:120n Continuous conveyancen Fully automaticThroughput [t/h]n Maximum capacity 150m3/h10080Δp 3 barL 200 m3ss 1000 kg/mwear class 16040200Special applications0,511,522,5As well as conveying vessels, Claudius PetersDesign parameters for thistype of application:also offers injection vessels, which are designedn Standard sizes: 0.2m3 to 20m3to inject substances against high counterpressures. If required, injection vessels mayincorporate distribution devices within theconveying pipe to divide the material flow, suchas when feeding coal into a blast furnace atseparate points.33,54Net volume [m3]68121520n Customized sizes to 35m3 are in operationn T hroughputs to 300m3/h arepresently operatingn Distances to 3,500mn Customized solutionsn M odern control techniques with valvessuiting the specific bulks9
type 2: X-PumpProven technologyfor dense phaseconveyanceThe Claudius Peters X-Pump is a high-speed screw feeder, installed as afeeding unit in front of a pneumatic conveying pipeline. This system can bedesigned as a conventional pneumatic pipeline or as a Claudius PetersFLUIDCON pipeline system.The task of the X-Pump is designed to feed adefined solids mass flow into a conveying gasflow against the overpressure within the conveyorpipe. At the same time it seals the system on-contact between screw / housing leadsn Nto less wear and high operation reliabilityoverpressure against the surroundings or then End wings can be replaced separatelyupstream sections of the plant, minimizing gasn F lexible partial load operation due totwo-sided bearing systemleakage through the feeder.This sealing is realized by forming a plug of bulksolids of defined length at the end of the screw.Conveying pressures up to approx. 2.5 baroverpressure (in special cases even higher)areachieved as well as conveying distances of upn No balancing of screw neededn H igh sealing effect due to small gapbetween screw and wear bushingn N on-contact labyrinth sealing ideal forhigher screw speedsto approx. 1000 m and throughput capacities ofn Low maintenance costs and down timeup to 640m3/h. With this system it is possible ton D esigned for non-explosive or explosiveand bulk materials like coal dustconvey pulverized bulk solids as well as coarsermaterials with grain sizes up to 10 mm. TheX-Pump can be used as a feeder for dense-phaseVariable design and power transmission.Advantages of X-Pumpn 1 00% ATEX conformity for explosivebulk materialsas well as for lean-phase conveyance.Highest flexibility in design of outlet points (example: left hand outlet).10Cross section of X-Pump. For 3D animation go to www.claudiuspeters.com
1Main Components of X-Pump:2A reliable feeder fordense-phaseand lean-phaseconveying 1. Material inlet2. Surge bin with dedusting socket3. Conveying and compressing screw344. Material discharge area55. Double sided sealing and bearing system6786. Material / Gas mixing chamber7. Conveying gas inlet8. Conveying pipe connectionThe Claudius Peters solid X-Pump is a verycompact unit due to its two-sided bearing.The machinery runs extremely quietly and ischaracterized by very low power consumptionas well as reduced pulsation during operation.800The wear parts can be easily replaced and the640pump is suitable for a wide range of applications600Special features:n Variable arrangement of the pump outletn Different screw geometries and end flightsn E asy assembly – wear parts can bereplaced with minimal dismantlingn Screw supported at both ends of the shaftThroughput [m3/h]and -350Sizen I ndividual screw geometry for eachbulk solidn Check flap with integrated damper425400X-Pump capacities.n Pulsation free conveyance11
type 3: AirliftVertical liftcapabilitywith a lowinvestment costThe Claudius Peters Airlift: a pneumatic lift that can convey solids vertically to amaximum capacity of 1000t/h.Features of the AirliftThe Airlift offers the advantages of low investment costs, low power consumption and highavailability, alongside continuous operation andeasy partial load operation. It can handle all fluidbulk solids, conveying loads up to 12-25kg solidsper m3 of conveying gas, with conveying heightsup to 120m and capacities up to 1000t/h.Airlift – rapid transport of largequantities of material using airThe Airlift feeds bulk solids continuously into theAirlift pot, whilst conveying air is fe
feeding unit in front of a pneumatic conveying pipeline. This system can be designed as a conventional pneumatic pipeline or as a Claudius Peters FLUIDCON pipeline system. Highest flexibility in design of outlet points (example: left hand outlet). Cross section of X-Pump. For 3D animation go to www.claudiuspeters.com