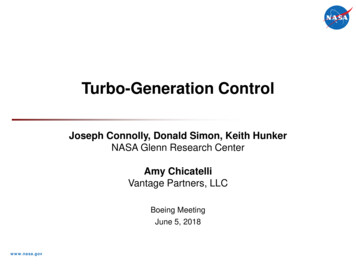
Transcription
Turbo-Generation ControlJoseph Connolly, Donald Simon, Keith HunkerNASA Glenn Research CenterAmy ChicatelliVantage Partners, LLCBoeing MeetingJune 5, 2018www.nasa.gov
Overview: NEAT Turbine Transient Assessment & ControlProblemElectrified Aircraft Propulsion (EAP) power systems are being studied at theNASA Electric Aircraft Testbed (NEAT) facility. The electric motors at NEAT havethe capability to dynamically respond to commands that would be unrealisticwhen integrated with turbomachinery. There is a need to provide more realisticturbine transients for future system performance studies.STARC-ABL Aircraft ConceptObjectiveWork with the NEAT analysis team to help develop a method to physics basedsimulations to allow electric motors to provide more realistic turbine transients.NEATApproachA dynamic Numeric Propulsion System Simulation (NPSS) generic model of aTurbofan and Tail Fan are combined to be representative of the STARC-ABLconfiguration. The NPSS models are integrated in MATLAB/Simulink using an Sfunction with pseudo-real time blocks to allow the simulation to reflect thecomputer clock. A short flight profile is used that contains altitude, Mach number,fuel flow, and power requirements. The computer is then integrated on the NEATEthernet network using User Datagram Protocol (UDP) blocks to pass motorspeeds and torques to emulate Turbofan shafts and power extraction.NPSS Turbofan and Tail Fan models used tocontrol the operation of the NEAT Testbed.ResultsThe NEAT electric power system has been controlled using a generic NPSSmodel that is representative of the STARC-ABL configuration. The NPSS modelwas shown to operate stably during a short flight profile without violating voltageor current limits. Lessons learned have been compiled for future improvementsto enable performance and design studies.SignificanceThis demonstrates the capability to run turbomachinery models on a networkedcomputer to control the operation of the NEAT electric motors to be morerepresentative of the dynamic response of the system during flight like conditionsof takeoff, cruise, and descent.NPSS scaled power input and the resultingNPSS Tail fan shaft speed commanded toelectric motor for emulated response.POC: Joseph Connolly, NASA GRC
NEAT STARC-ABL Control DiagramWing Turbofan RightTail FanTorqueAltitudeMachTorqueto PowerNPSSThrottleSpeedTorqueMotor 2torqueCmdTorqueMotor 3TorqueAltitudeThrottleNPSSCmdTorquePrevious Single String TestMachAltitudeMachSpeedMotor 6PowerTorqueMotor 4Motor 8Motor 7TorqueΣNPSSSpeedMotor 5CmdTorqueMotor 1input from PCmechanical shaftWing Turbofan LeftTorque3
Flight Profile for Transient Turbine Assessment The flight profile used for thistest is a simple takeoff, cruise,and descent, that was limitedto about 17min for rapid checkout testing.– Future studies that will befocused on performancemetrics will transition to theN 3 design referencemissions After the large fuel flowtransient for takeoff, the fuelflow is held constant to ensurechanges in power extractionare reflected in the NPSSresponse and NEAT hardware– The power extraction used issimply for demonstratingcorrect communication tohardware and stability4
NEAT Hardware Results The power to the NPSS Tail Fan motor isshown, starting from zero power at flight idleto the expected 3500 hp at top of climb.Variation in the delivered power is theresults of the power extracted from the wingturbofansThe NPSS model provides a rotationalspeed to motor 7 that emulates the tail fanshaft.– The electric motor track the NPSS commandwell. There is a slight delay that will need tobe understood and possibly filtered whendoing future performance studies. The current control of the motors appears tobehave reasonably in terms of the responsefollowing the resulting current commandsgenerated from the NPSS inputs.5
Turbofan Engine Controls Development The T-MATS STARC-ABL dynamic systemsimulation with power flow electricalcomponent modeling was executed at 726operating points encompassing the full flightenvelope.– The controller was able to provide the a risetime of less than five seconds meeting theFAA requirement– Further analysis is being conducted foroperability changes with newly availableelectrical machines The turbomachinery controller is required toprovide two critical operations– It must be able to go from an idle condition to95% of power within 5 seconds to simulate anemergency takeoff– It must be able to operate through out theoperational envelope without encountering astall event that results in a rapid loss of thrust.6
Transient Performance for Flight MissionOperability Study The N 3 expected 900 nmiflight mission profile is providedbelow, the cruise portiontruncated for the interest oftime, but the main transientfeatures remainKey operability parameters forthe STARC-ABL system areshown for a healthy system,end of life, and optimizedpower split for lower TSFCFlight MissionIt can be seen that none of the main operability limitsare violated for the nominal mission throughout theexpected system life cycleThe LPC stall margin is currently the closest to aviolation at idle conditions. In general, taking slightlyless power form the turbofan improves their operabilitymargins and reduced TSFC by about 0.5%7
Summary Analysis conducted on N 3 STARC-ABL concept for transient operationand control– The simple power flow electrical component modeling neglects the electricaldynamics of switching, but provides a tool for more rapid control systemdevelopment, A transient assessment of the NEAT facility was conducted for a shortduration flight profile with the focus on providing realistic transient responsesfrom STARC-ABL representative turbomachinery models to interact withelectric motors and generators.– A method similar to the the previous single string test of using NPSSMATLAB/Simulink S-function operation with UDP blocks to send and receive dataacross an Ethernet connection to the 8 electric motors was used.– The NPSS models of the STARC-ABL provided the expected transient behavior,however being generic models the performance metrics of the turbomachinerydoes not reflect the designed STARC-ABL turbomachinery A near term goal is to develop and demonstrate critical technologies for hybridgas-turbine electric propulsion by 2025 to impact the next generation of singleaisle aircraft8
References1.2.3.4.5.6.7.8.9.Bradley, M.K., and Bradley, D.K., “Subsonic Ultra Green Aircraft Research: Phase II – Volume II –Hybrid Electric Design Exploration,” NASA CR–2015-218704/Volume II, April, 2015.Ashcraft, S.W., Padron, A.S., Pascioni, K.A, Stout Jr., G.W., and Huff, D.L., “Review of PropulsionTechnologies for N 3 Subsonic Vehicle Concepts,” NASA TM 2011-217239, October, 2011.Welstead, J. and Felder, J. L., “Conceptual Design of a Single-Aisle Turboelectric CommercialTransport with Fuselage Boundary Layer Ingestion” AIAA 2016-1027Dyson, R., “NASA Electric Aircraft Test Bed (NEAT) Development Plan,” 2016, NASA TM 2016-219085Thole, K., Whitlow, W. & et al., “Commercial Aircraft Propulsion and Energy Systems Research:Reducing Global Carob Emissions,” The National Academies Press, 2016Bowman, C. “Visions of the Future: Hybrid Electric Aircraft Propulsion”, AIAA Propulsion and Energy,2016Shin, J. & et. al. “NASA Aeronautics: Strategic Implementation Plan 2017 Update”, 2017Esker, B. Wahls, R. and et. Al., “ARMD Strategic Thrust 4: Transition to Low-Carbon Propulsion” May,2016.Thole, K., Whitlow, W. & et al., “Commercial Aircraft Propulsion and Energy Systems Research:Reducing Global Carob Emissions,” The National Academies Press, 20169
Acknowledgments This work was funded by the NASA Advanced Air TransportTechnologies (AATT) project10
Ethernet network using User Datagram Protocol (UDP) blocks to pass motor speeds and torques to emulate Turbofan shafts and power extraction. . Summary Analysis conducted on . N 3 STARC-ABL concept for transient operation . B. Wahls, R. and et. Al., “ARMD Strat