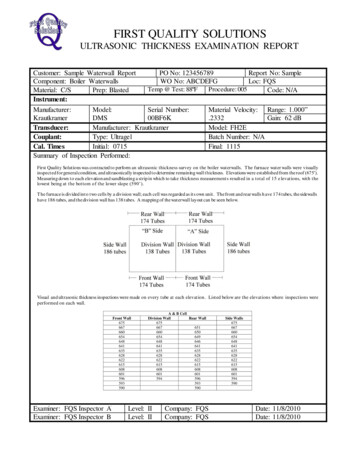
Transcription
FIRST QUALITY SOLUTIONSULTRASONIC THICKNESS EXAMINATION REPORTCustomer: Sample Waterwall ReportPO No: 123456789Report No: SampleComponent: Boiler WaterwallsWO No: ABCDEFGLoc: FQSTemp @ Test: 88ºFProcedure: 005Material: C/SPrep: BlastedCode: N/AInstrument:Manufacturer:Model:Serial Number:Material Velocity: Range: 1.000”KrautkramerDMS00BF6K.2332Gain: 62 dBTransducer:Manufacturer: KrautkramerModel: FH2ECouplant:Type: UltragelBatch Number: N/ACal. TimesInitial: 0715Final: 1115Summary of Inspection Performed:First Quality Solutions was contracted to perform an ultrasonic thickness survey on the boiler waterwalls. T he furnace water walls were visuallyinspected for general condition, and ultrasonically inspected to determine remaining wall thickness. Elevations were established from the roof (675’).Measuring down to each elevation and sandblasting a strip in which to take thickness measurements resulted in a total of 15 e levations, with thelowest being at the bottom of the lower slope (590’).T he furnace is divided into two cells by a division wall; each cell was regarded as its own unit. The front and rear walls h ave 174 tubes, the sidewallshave 186 tubes, and the division wall has 138 tubes. A mapping of the waterwall layout can be seen below.Visual and ultrasonic thickness inspections were made on every tube at each elevation. Listed below are the elevations where inspections wereperformed on each wall.Front xaminer: FQS Inspector AExaminer: FQS Inspector BA & B CellDivision WallRear 22622615615608608601601594596593590Level: IILevel: IICompany: FQSCompany: FQSSide e: 11/8/2010Date: 11/8/2010
The results of the visual and ultrasonic thickness inspections can be seen as follows, and in addition,attached are visual representations of the inspection with colored maps of the test results.Recommendations: Perform ultrasonic thickness testing at approximately the same elevations as this outage duringthe next scheduled maintenance outage.Restore all areas where walls have been bowed.Replace all tubes where pad welds were found from past repairs.Visual Inspection1. Elev. 675, cracking on the front wall header tube stub at the front wall header, tube # 29.2. Elev. 675, division wall tube # 75 bent out of plain.
Sample Waterwall ReportFurnace Waterwall Ultrasonic Thickness InspectionNov 2010 Outage“A” Side Front 359011020Thickness0.999 - 0.1500.149 - 0.1200.119 - 0.1000.099 - 0.001No Data304050Coding60708090100110120130140150160170
Sample Waterwall ReportFurnace Waterwall Ultrasonic Thickness InspectionNovember 2010 Outage"A" Side Front 90.1600.1370.1430.1530.1620.161-Thickness0.999 - 0.1500.149 - 0.1200.119 - 0.1000.099 - 0.001No DataMAX 0.229MIN 0.107AVG 0.1660.1760.1710.1610.1550.1630.1780.1620.168-Tube Number1011120.167 0.169 0.1720.170 0.177 0.1780.164 0.169 0.1690.171 0.175 0.1720.172 0.171 0.1720.157 0.158 0.1570.163 0.157 0.1670.161 0.168 0.1590.167 0.175 0.1630.165 0.169 0.1670.162 0.167 0.1630.208 0.2000.171 0.1700.166 0.1670.143 20.1840.1610.1700.151
Sample Waterwall ReportFurnace Waterwall Visual InspectionNov 2010 Outage"A" SideWall675FrontAir leakage at front upperdistribution header at the sidewall and division wall, crackingon front wall tube stubs atfront wall header tubes # 2125,29,35,39,49,51,57,73,85,89,93, 95,99,101,105,109,113,115,155 and 159Picture # 1 - Tube 29DivisionTubes # 74,75,77and 78 bentout of plain667660RightPicture # 2 - Tube 75Tubes # 74,75,77and 78 bentout of plainOld attachment weld left ontube # 172RearTubes # 74,75,77and 78 bentout of plainSee Section 5: Pendant SectionElev.Pad weld on tube # 126Flattening on tubes #127 (0.161),128 (0.154), 129 (0.157)Picture # 3 - Tube # 126Bowing tubes # 108,125,126146, 147 (1/8 to 1/4 tube diam.)Tube #126 bulged and crackinglongitudinally.
Sample Waterwall ReportFurnace Waterwall Visual InspectionNov 2010 Outage"A" SideWallFrontAir leakage at front upper675654Pad weld on tube # 168Picture # 4648Soot blower damage,seesoot blower reportCirc. Cracking on tube #174641DivisionTubes#74,75,77andbentPad welds on tubes # 7867,156Corrosion on tube # 67 in doghouseCrack weld tubes # 68,69,84,85Erosion above pad weld tube#98,99,100Tubes # 85 and 86 bent outof plainStitch weld broken at tubes #68 & 69.Tubes # 85 & 86, 115 & 116, and121 & 122 bowed 1 tube diam.RearRightSee Section 5: PendantSectionSee Section 5: Pendant SectionElev.Stitch welds cracked tubes # 68, Erosion above weld overlay right69and left sides ,also soot blowerTubes #115 - 116, and 120 - 121 damage , see soot blower reportbowed 1 tube diameterTubes #2 & 3 gougedBroken stitch welds at tubes #1& 2.Circ. Cracking in a 1 ft. area ontube # 1.Pad weld on tube # 136
Sample Waterwall ReportFurnace Waterwall Visual InspectionNov 2010 Outage"A" SideWallFrontAirleakagefront upperPad welds on attubes#61 & 62Tube #107 bowed 1/2 tube diam.DivisionTubes#74,75,77and78tubesbentStitch welds cracked on# 68,69,123 and124675635RightTube #82 - 0.114"Tube #83 - 0.110"Tube #86 - 0.093"Tube #130 - the 1 ft. membranenear the tubes has cracks.Stitch weld cracked on tube # 68and # 69628Stitch weld cracked on tube # 68and # 69622RearCorrosion/erosion noted on tube#79 through 107.See Section 5: Pendant SectionElev.Pad weld noted on tube # 108
The results of the visual and ultrasonic thickness inspections can be seen as follows, and in addition, attached are visual representations of the inspection with colored maps of the test results. Recommendations: Perform ultrasonic thickness testing a