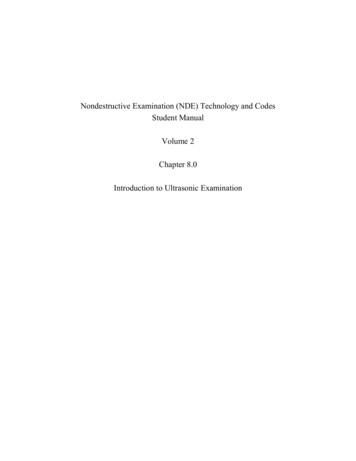
Transcription
Nondestructive Examination (NDE) Technology and CodesStudent ManualVolume 2Chapter 8.0Introduction to Ultrasonic Examination
NDE Technology and Codes Student ManualTable of ContentsTABLE OF CONTENTS8.0 INTRODUCTION TO ULTRASONIC EXAMINATION . 1Learning Objectives8.1 History. . . . . . . . . . . . . . . . . . . . . . . . . . . . . . . . . . . . . . . . . . . . . . . . . . . . . . . . . . . . . . . . . . . . 18.2 Personnel Qualification and Certification . 18.2.1ASME Section V . 18.2.2ASME Section XI . 28.3 Principles. . . . . . . . . . . . . . . . . . . . . . . . . . . . . . . . . . . . . . . . . . . . . . . . . . . . . . . . . . . . . . . . . . 48.3.1Frequency . . . . . . . . . . . . . . . . . . . . . . . . . . . . . . . . . . . . . . . . . . . . . . . . . . . . . . . . 48.3.2 Velocity 48.3.3Wavelength. 58.3.4Transmission/Reflection . 58.3.5Attenuation .68.3.6Instrumentation and Control . 68.3.7 Ultrasonic Wave Propagation . 68.3.7.1Acoustic Impedance . 78.3.7.2Reflection at Interfaces . 88.3.7.3Fresnel Zone . 88.3.7.4Fraunhofer Zone (Far Field) . 98.3.7.5Dead Zone. 98.3.8 Refraction. 98.3.8.1Snell’s Law . 98.3.8.2First and Second Critical Angles . 10USNRC Technical Training Center8 iRev 0409
NDE Technology and Codes Student ManualTable of Contents8.3.9 Ultrasonic Examination Variables . 118.3.9.1 Equipment . 118.3.9.2 Transducers . 128.3.9.3 Couplant. 138.3.9.4 Scanning Techniques . 138.3.9.5 Part Structure . 138.3.9.6 Surface Condition . 138.3.9.7 Part Geometry and Size . 138.3.9.8 Discontinuity Type, Shape, and Orientation . 148.4 Equipment . . 148.4.1 Ultrasonic Transducers . 148.4.1.1Types . 148.4.1.2Care of Transducers . 148.4.2 Base Pulse-Echo Instrumentation . 158.4.2.1Time base . 158.4.2.2Clock . 168.4.2.3Pulse Repetition Rate. 168.4.2.4Pulser-Receiver . 168.4.2.5Basic Controls. 168.4.2.6Gates . 178.5 Procedures. . 178.5.1 Application of the Various Wave Modes . 188.5.1.1Compressional Wave Applications . 188.5.1.2Shear Waves . 188.5.1.3Surface Waves . 188.5.1.4Lamb Waves . 188.5.2Immersion Testing . 188.5.2.1Immersion Tanks and System Components . 188.5.2.2Immersion Transducers . 198.5.3Data Display . 20USNRC Technical Training Center8 iiRev 0409
NDE Technology and Codes Student Manual8.5.3.18.5.3.28.5.3.3Table of ContentsA-Scan . 20B-Scan . 20C-Scan . 208.5.4 Calibration Techniques . 218.5.4.1Linearity. 218.5.4.2Distance Amplitude . 228.5.4.3Resolution . 238.5.4.4Beam Profile . 238.5.4.5Test Block Parameters . 238.5.5 Unacceptable Techniques . 238.5.5.1Scanning Problems . 238.5.5.2Interpretation Shortcomings . 238.5.5.3Report Format Problems . 238.6 Interpretation and Code Requirements . 248.6.1Weld Calibration Standards . 248.6.2Evaluation . 258.6.2.1False Indications . 258.6.2.2Nonrelevant Indications . 258.6.2.3Relevant Discontinuity Indications . 258.6.3Recording. 268.6.3.1Use of Examination Forms . 268.6.3.2Recording Techniques . 268.7 Advantages and Limitations of Ultrasonic Examination. 268.7.1 Advantages . 268.7.2Limitations . 26LIST OF TABLESUSNRC Technical Training Center8 iiiRev 0409
NDE Technology and Codes Student ManualTable of Contents8-1 Acoustic Properties of Materials . 28LIST OF FIGURES8-1 Wavelength 298-2 Reflection, Transmission at an Interface . 308-3 Block Diagram of a Typical Ultrasonic Instrument . 318-4 Particle Displacement by Longitudinal Waves . 328-5 Particle Displacement by Transverse Waves. 338-6 Surface or Rayleigh Wave Modes . 348-7 Plate or Lamb Wave Modes . 358-8 Constructive and Destructive Interference . 368-9 Near and Far Fields. 378-10 Near-to-Surface Reflector Within Dead Zone . 388-11 Dead Zone Check . 398-12 Angle Beam in Weld . 408-13 Angle Beam Transducer Assembly . 418-14 Refraction and Reflection of Incident Compressional Wave at an Interface . 428-15 Increasing Incident Angle in Probe Shoes (Wedges) With Second Medium ofHigher Velocity . 438-16 Transducer Coupled to Test Piece . 448-17 Immersion Test . 458-18 Normal Compressional Wave Probe . 468-19 Delay Line Probe . 478-20 Calibration of Timebase for Delay Line Probe . 488-21 Dual Element Probe (Pitch-Catch) . 498-22 Use of Reject . 508-23 Typical Ultrasonic Tank and Bridge/Manipulator. 518-24 Bridge/Manipulator . 528-25 Flat and Contour-Corrected Transducers . 538-26 Focused-Beam Shortening in Metal . 548-27 B-Scan Presentation . 558-28 C-Scan Presentation . 568-29 Typical C-Scan Recording. 578-30 Basic Calibration Block . 588-31 Distance Calibration . 59USNRC Technical Training Center8 ivRev 0409
NDE Technology and Codes Student e of ContentsDistance Amplitude Calibration . 60Linear Reflector . 61Distance Amplitude Correction Curves . 62Block A2 (IIW Block) . 63Block A7 . 64Checking Beam Index Point . 65Checking Beam Angle . 66Timebase Calibration for Shear Wave Probe Using A4 Block . 67Timebase Calibration for Shear Wave Probe Using A2 Block Modified with Slots . 68Timebase Calibration for Shear Wave Probe Using A2 Block Modified with 25 mmRadius . .69USNRC Technical Training Center8 vRev 0409
NDE Technology and CodesStudent Manual8.0 INTRODUCTIONEXAMINATIONChapter 8.0 Introduction toUltrasonic ExaminationTODevelopment of more advanced equipment inthe 1940's expanded the use of pulse-echo ultrasound, which derives information from the soundmaking round trips, and required access to onlyone side of the material. Another technique,resonance testing, depends on the resonant frequency of the material being examined.ULTRASONICLearning Objectives:To enable the student to:1. Understand the basic principles of the generation, transmission, and reflection ofultra-sound.8.2 Personnel Qualification and CertificationOf all the NDE methods, UT is the mostsubjective and therefore depends greatly on thequalifications and expertise of the examiner.2. Know the personnel qualification and certification requirements.3. Become familiar with the various techniquesused in ultrasonic examination (UT).8.2.1 ASME Section VThe 2007 Edition with 2008 Addenda of theASME Code Section V requires that NDE personnel be qualified in accordance with either:4. Understand the steps involved with calibration.5. Become familiar with the variables affectingUT.SNT-TC-1A (2006 Edition), orANSI/ASNT CP-189 (2006 Edition)ACCP6. Understand the common interpretation andcode requirements.Qualification in accordance with a prior editionof either SNT-TC-1A or CP-189 is consideredvalid until recertification. Recertification must bein accordance with SNT-TC-1A (2006 Edition),CP-189 (2006 Edition) or ACCP .7. Identify the advantages and limitation of UT.8.1 HistoryPractical use of ultrasound for NDE began inthe 1920's. Sokolov was a major pioneer, usingthe through-transmission technique whereby soundis transmitted through the material, to a receiver.Reduction in the received signal amplitudeindicated the possibility of discontinuities in thepath of the sound beam.USNRC Technical Training CenterA Level II Ultrasonic Examiner, who is a highschool graduate, must complete one of followingfor Section V and only the CP-189 requirementsfor Section XI.8 1Rev 0409
NDE Technology and CodesStudent ManualChapter 8.0 Introduction toUltrasonic Examinationexperience consists of the sum of the hoursrequired for NDT Levels I and II.3. The required minimum experience must bedocumented by method and by hour withsupervisor or NDT Level III approval.4. While fulfilling total NDT experiencerequirement, experience may be gained inmore than one (1) method.Minimumexperience hours must be met for eachmethod.The SNT-TC-1A requirements are:TrainingExperienceLevel I40 hours210* hrs /400**hrsLevel II40 hours630* hrs /1200 **hrsNOTES:1. To certify to Level II directly with no timeat Level I, the training and experience forLevel I and II shall be combined.2. Training hours may be reduced with additional engineering or science study beyondhigh school. Refer to Chapter 2 andSNT-TC-1A.3. There are no additional training requirements for Level III. Refer to Chapter 2 ofthis manual for Level III requirements.8.2.2 ASME Section XIUltrasonic examination is the most widely usedmethod for the detection and evaluation of pipingsystems’ flaws during In-service Inspection (ISI)of nuclear power plants. However, due to thecomplexity of the method and the factors affectingthe examination, such as pipe geometry andmaterial type, the training and qualification ofexaminers have been problematic and underconstant evaluation since the early 1980's.The CP-189 requirements are:TrainingExperienceLevel I40 hours200*/400**Level II40 hours600*/1200**During the mid-seventies, boiling waterreactors (BWRs) were found to contain extensiveintergranular stress corrosion cracking (IGSCC) incertain stainless steel piping. The NRC called forincreased examinations and for plant owners toimprove the effectiveness of ultrasonic examinations. The Electric Power Research Institute(EPRI), NRC, and plant owners conducted anumber of studies on the effectiveness of ISIultrasonic examiners and their ability to detectIGSCC. The results showed qualified examinerswere missing critical discontinuities.Theindustry instituted special training and certificationexaminations given through EPRI to better qualifyexaminers to find IGSCC. It is critical to remem-*Hours in UT/** Total Hours in NDENOTES:1. Experience is based on the actual hoursworked in the specific method.2. A person may be qualified directly to NDTLevel II with no time as certified Level Iproviding the required training andUSNRC Technical Training Center8 2Rev 0409
NDE Technology and CodesStudent ManualChapter 8.0 Introduction toUltrasonic Examinationber that the requirements of CP-189 (1995 Editions) are minimum for Section XI. The specificand practical examinations must be directed at thespecific techniques an examiner will use in thefield. To have examiners spend 80 percent oftheir time doing erosion/corrosion (straight beam)examinations and then administer a simple anglebeam practical examination is not adequate for theperformance of ISI weld examinations.The requirements of Appendix VII are:ClassroomSection XI requires that personnel performingNDE be qualified and certified using a writtenpractice prepared in accordance with ANSI/ASNTCP-189 as amended by Section XI. IWA 2314states that the possession of an ASNT Level IIICertificate, which is required by CP-189, is notrequired by Section XI. Section XI also states thatcertifications to SNT-TC-1A or earlier editions ofCP-189 will remain valid until recertification atwhich time CP-189 (1995 Edition) must be met.ExperienceLevel I4040250 hoursLevel II4040800 hoursLevel III40-Options-see belowOption I - Graduate of a 4 year accreditedengineering or science college or university with adegree in engineering or science, plus 2 yearsexperience in NDE in an assignment comparable tothat of an NDE Level II in the ultrasonic examination method. At least 1 year of this experienceshall be in nuclear applications and shall includethe actual performance of examinations andevaluation of examination results. Also, it requires 4,200 hours of total experience with 2,100hours in nuclear applications.To assure that an examiner performing ISIultrasonic examinations is properly qualified,ASME Section XI has added extensive requirements above the minimums as outlined in CP-189.Specifically, Appendix VII was added to SectionXI. The following section outlines basic requirements for ASME Section XI. (Refer to ASMESection XI, Appendix VII for detailed information.)Option 2 - Completion with a passing grade ofat least the equivalent of 2 full years of engineering or science study at a university, college, ortechnical school, plus 3 years experience in anassignment comparable to that of a Level II in theultrasonic examination method. At least 2 yearsof this experience shall be in nuclear applicationsand shall include the actual performance ofexaminations and evaluation of examinationresults.Also, it requires 6,300 hours ofexperience with 4,200 hours in nuclearapplications.The 2007 edition with 2008 addenda of SectionXI, requires certification to CP-189 - 1995 asmodified in ASME Section XI MandatoryAppendix VII article VII 4000.USNRC Technical Training CenterLaboratory8 3Rev 0409
NDE Technology and CodesStudent ManualChapter 8.0 Introduction toUltrasonic Examination"hertz" units as follows:Option 3 - High school graduate, or equivalent, plus 4 years experience in an assignmentcomparable to that of a Level II in the ultrasonicexamination method. Also, it requires 8,400hours of experience with 4,200 hours in nuclearapplications. Appendix VII also addresses NDE InstructorQualification, Annual Training (minimum of 10hours per year), Examinations (with much emphasis on performance demonstration), andQualification Records.The audible range, which is the range of humanhearing, is 20 Hz to 20 KHz. Ultrasoundencompasses all frequencies higher than 20 KHz.UT utilizes only a portion of the ultrasonic range.Most commercial UT is performed within therange of 100 KHz to 25 MHz; a few applicationsare performed both above and below thisfrequency band. Actual examination frequencydepends on the frequency of the transducerselected.Appendix VII Supplement 1 contains theminimum content for initial training courses.8.3 PrinciplesSound is the transmission of mechanicalenergy, in the form of vibrations, through a material. Although sound can be propagated in allthree states of matter; solids, liquids, and gases,factors such as type of sound wave, materialcomposition, and wavelength can make propagation difficult or impossible in a given situation.8.3.18.3.2 VelocityVelocity is the speed at which sound travels.It is expressed as distance traveled per unit time.The most common units of time in UT are thesecond and microsecond (μsec). A microsecondis one millionth of a second.FrequencyThe velocity of sound depends upon:Frequency is the rate of vibration or the number of vibrations per second. Because soundwaves are in motion, frequency can also be viewedas the number of complete waves which pass agiven point during 1 second. One complete unitof vibration is called a cycle. A cycle isgraphically represented by a sine curve andconsists of two opposing motions, such as forwardand backward, or up and down. The rate ofvibration, or cycles per second, is expressed inUSNRC Technical Training CenterHertz (Hz) cycles per second,Kilohertz (KHz) one thousand cycles persecond, andMegahertz (MHz) one million cycles persecond. Density and elasticity of the material throughwhich sound is traveling, Wave mode (the manner in which materialparticles vibrate as sound travels through thematerial), and Material temperature, which has a minor effecton sound velocity for temperatures greater than150 F.8 4Rev 0409
NDE Technology and CodesStudent ManualChapter 8.0 Introduction toUltrasonic Examinationmaterial offers to the passage of sound. It is theproduct of the material's velocity and density. Asthe impedance ratio increases between theinterfaces of two materials the greater the soundreflection at this interface boundary and hence lesssound is transmitted into the second material. Thepercentage of sound reflected from an interface,where Z1 is the acoustic impedance of the mediumthrough which the sound is initially traveling, andZ2 is the acoustic impedance of the medium thatthe sound meets at the interface and is reflected, iscalculated as follows:Several formulas used in UT employ materialvelocity as a variable. The most convenient unitfor calculating these formulas is kilometers persecond (km/sec), although inches per second andcentimeters per microsecond are sometimesencountered.8.3.3 WavelengthA vibration in motion is often called a soundwave. A series of sound waves sent into an objectis often called a pulse.(8-2)% Sound reflected (Z1-Z2)2/(Z1 Z2)2 x 100Wavelength is an important variable in UT andis defined as the distance from one point on anultrasonic wave train to the next identical point(e.g., from trough to trough or peak to peak)(Figure 8-1).Material discontinuities reflect sound becausethey have an acoustic impedance different from thematerial being examined (Figure 8-2). In additionto acoustic impedance, a number of other factorsreduce the amplitude of the echo that thetransducer receives from a discontinuity. Thesize, shape, and orientation of the reflector allaffect its echo response. Position of a reflector isparticularly important due to the effects of soundbeam geometry and material properties. Themore the sound beam has spread at the point ofreflector interception, the less will be the reflectedsound pressure per unit area. In addition, assound travels through test material, increasedscattering and absorption of the sound by thematerial's own structure is experienced. Whenexamining thick sections, some type ofdistance/amplitude correction (DAC) must beconsidered to compensate for amplitude lossescaused by the sound beam and test material.It is also defined as the distance sound travelswithin the duration of one complete cycle.Wavelength (represented by λ, the Greek letterlambda) is calculated by dividing velocity (V) byfrequency (f), as follows:λ(8-1)(mm) V(km/sec)/f8.3.4Transmission/Reflection(MHz).Sound reflects when it strikes a surface calledan acoustic interface. An echo is thereforedefined as a reflection from an acoustic interface.An acoustic interface is the boundary between twomaterials with different acoustic impedances.Acoustic impedance is defined as the opposition aUSNRC Technical Training Center8 5Rev 0409
NDE Technology and CodesStudent ManualChapter 8.0 Introduction toUltrasonic Examination8.3.5 Attenuation8.3.7 Ultrasonic Wave PropagationSound amplitude decreases (as it propagates inthe material) are called sound attenuation. Attenuation is due to several factors:Sound waves travel through materials bydisplacing tiny particles of the material, generallyat the molecular level. Depending on the mannerin which vibrations are introduced, the particledisplacements exhibit certain behaviors, calledwave modes, as the vibrations travel.Absorption - Sound is absorbed by the brakingeffect on the particle motion. Lost energy isconverted to heat.There are two basic wave modes, which differfrom each other depending on how materialparticles move relative to the direction oftransmitted energy. Longitudinal waves (alsoknown as compressional waves) are characterizedby the particle motion being parallel to thedirection of wave travel (Figure 8-4). Transversewaves (also known as shear waves), are defined byparticle motion perpendicular to wave travel(Figure 8-5). The difference in wave motion causesthese wave modes to also differ from each other intheir relative velocity as well as in their ability topropagate in the various states of matter.Scatter - Grain boundaries of the materialcause the sound to scatter.The amount of sound attenuation within amaterial is governed by the density, elasticity,grain size, and grain structure of the material.These factors are affected by alloying, heattreatment, working, etc.8.3.6Instrumentation and ControlFigure 8-3 shows a block diagram of a typicalultrasonic flaw detection instrument. The pulsegenerator (trigger, clock) transmits an electricalpulse simultaneously to the transducer (searchunit) and the time base of the cathode ray tube(CRT). The transducer converts the electrical pulseinto sound which is transmitted into the material.The time base (sweep generator) generates the Xsweep across the CRT. When the sound pulse isreflected back to the transducer, it is convertedback into an electrical pulse and is amplifiedbefore being fed to the Y axis of the CRT. Thispulse deflects the time base vertically and producesa peak.USNRC Technical Training CenterUltrasonic energy propagates throughmaterials in several different ways depending uponthe manner in which the particles within thecarrying medium move relative to the direction ofwave propagation.There are four forms of wave propagationthrough materials:8 6 Compression (or longitudinal), Shear (or transverse), Surface (or Rayleigh), and Plate (or Lamb).Rev 0409
NDE Technology a
Student Manual Ultrasonic Examination USNRC Technical Training Center Rev 04098 1 8.0 INTRODUCTION TO ULTRASONIC EXAMINATION Learning Objectives: To enable the student to: 1. Understand the basic principles of the genera-tion, transmission, and reflection of ultra-sound. 2. Know the pe