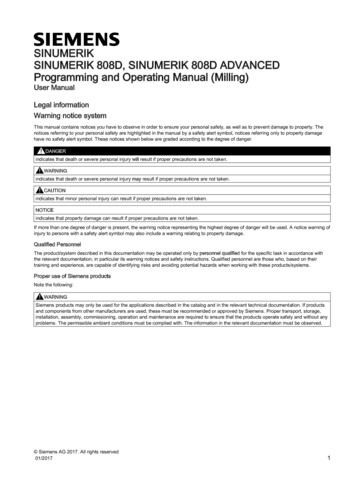
Transcription
SINUMERIKSINUMERIK 808D, SINUMERIK 808D ADVANCEDProgramming and Operating Manual (Milling)User ManualLegal informationWarning notice systemThis manual contains notices you have to observe in order to ensure your personal safety, as well as to prevent damage to property. Thenotices referring to your personal safety are highlighted in the manual by a safety alert symbol, notices referring only to property damagehave no safety alert symbol. These notices shown below are graded according to the degree of danger.DANGERindicates that death or severe personal injury will result if proper precautions are not taken.WARNINGindicates that death or severe personal injury may result if proper precautions are not taken.CAUTIONindicates that minor personal injury can result if proper precautions are not taken.NOTICEindicates that property damage can result if proper precautions are not taken.If more than one degree of danger is present, the warning notice representing the highest degree of danger will be used. A notice warning ofinjury to persons with a safety alert symbol may also include a warning relating to property damage.Qualified PersonnelThe product/system described in this documentation may be operated only by personnel qualified for the specific task in accordance withthe relevant documentation, in particular its warning notices and safety instructions. Qualified personnel are those who, based on theirtraining and experience, are capable of identifying risks and avoiding potential hazards when working with these products/systems.Proper use of Siemens productsNote the following:WARNINGSiemens products may only be used for the applications described in the catalog and in the relevant technical documentation. If productsand components from other manufacturers are used, these must be recommended or approved by Siemens. Proper transport, storage,installation, assembly, commissioning, operation and maintenance are required to ensure that the products operate safely and without anyproblems. The permissible ambient conditions must be complied with. The information in the relevant documentation must be observed. Siemens AG 2017. All rights reserved01/20171
PrefaceApplicable productsThis manual is valid for the following control systems:Control systemSoftware versionSINUMERIK 808D ADVANCED M (Milling)V4.7.4: PPU161.3/PPU160.2 with spindle/feed servo systemSINUMERIK 808D (Milling)V4.7.4: PPU141.2 with feed servo systemDocumentation components and target audienceEnd-user documentationTarget audienceProgramming and Operating Manual (Turning)Programmers and operators of turning machinesProgramming and Operating Manual (Milling)Programmers and operators of milling machinesProgramming and Operating Manual (ISO Turning/Milling)Programmers and operators of turning/milling machinesProgramming and Operating Manual (Manual Machine Plus (MM ), Turning)Programmers and operators of turning machinesDiagnostics ManualMechanical and electrical designers, commissioning engineers,machine operators, and service and maintenance personnelManufacturer/service documentationTarget audienceCommissioning ManualInstallation personnel, commissioning engineers, and service andmaintenance personnelFunction ManualMechanical and electrical designers, technical professionalsParameter ManualMechanical and electrical designers, technical professionalsService ManualMechanical and electrical designers, technical professionals, commissioning engineers, and service and maintenance personnelReadme fileThird-party software - Licensing terms and copyright informationMy Documentation Manager (MDM)Under the following link you will find information to individually compile your documentation based on the Siemens content:www.siemens.com/mdmStandard scopeThis manual only describes the functionality of the standard version. Extensions or changes made by the machine toolmanufacturer are documented by the machine tool manufacturer.Technical supportCountryHotline 1)Germany 49 911 895 7222China 86 400 810 4288Further service contact information: Worldwide Web site: ese Web site:http://www.siemens.com.cn/808D1)You can find more hotline information at the worldwide Web site given above.EC Declaration of ConformityThe EC Declaration of Conformity for the EMC Directive can be found on the Internet t.Here, enter the number "67385845" as the search term or contact your local Siemens office.2Programming and Operating Manual (Milling)01/2017
Table of contentsPreface. 212Fundamental safety instructions . 71.1General safety instructions . 71.2Industrial security . 8Introduction. 92.12.1.12.1.22.1.3Panel Processing Units (PPUs) . 9PPU versions . 9PPU control elements . 9Screen layout . 112.22.2.12.2.2Machine Control Panels (MCPs) . 12MCP versions . 12MCP control elements . 122.3Coordinate systems . 152.4Protection levels . 173Common notices for machining operations . 194Switching on and referencing . 195Setting the user interface language . 206Setting up tools . 207896.1Creating a tool . 206.2Creating/changing a cutting edge . 216.3Activating the tool and the spindle . 226.46.4.16.4.2Assigning the handwheel. 23Assigning the handwheel through the MCP. 23Assigning the handwheel through the PPU . 246.5Measuring the tool manually. 256.6Verifying the tool offset result . 27Creating part programs . 287.1Creating a part program . 2.3.57.2.3.67.2.3.77.2.3.87.2.3.9Editing the part program . 30Using a standard program structure . 30Editing a part program . 30Understanding frequently used programming instructions. 33Inch or metric dimensions (G70/G71) . 33Definition of work offset (G54 to G59, G500, G90/G91) . 34Rapid traverse (G00) . 35Tool and traverse (T, D, M6, F, G94/G95, S, M3/M4, G01) . 35Tool radius compensation (G40, G41/G42) . 36Milling circles and arcs (G02/G03). 37Fixed point approach (G74/G75) . 38Spindle control . 38Setting dwell time in the program (G04) . 38Program simulation . 398.1Simulation prior to machining of the workpiece . 398.2Simultaneous recording prior to machining of the workpiece . 41Machining the workpiece . 429.1Executing a part program . 42Programming and Operating Manual (Milling)01/20173
101149.2Executing specified blocks . 439.3Correcting a part program . 449.4Simultaneous recording during machining of the workpiece . 449.5Entering the tool wear offsets . 45Other common operations rogram control functions . 48Program test . 48Dry run feedrate . 48Conditional stop . 49Skip block. 49Single block mode . 49Rapid traverse override . 49Auxiliary function lock. 4910.2Calibrating the tool probe . 5010.3Measuring the tool with a probe (auto) . 5110.410.4.110.4.2Setting up the workpiece . 52Measuring the workpiece . 52Entering/modifying workpiece offsets . 5510.5Entering/modifying the setting data . 5510.6Setting R parameters . 5910.7Setting user data . 6010.8Setting the date and time . ing/transferring a part program from external . 61Executing/transferring through the USB interface . 61Executing from external (through USB interface) . 61Transferring from external (through USB interface) . 62Executing/transferring through the Ethernet connection . 62Configuring the network drive . 62Executing from external (through Ethernet connection) . 65Transferring from external (through Ethernet connection). 65Executing/transferring through the RS232 interface (PPU160.2 only) . 66Configuring RS232 communication . 66Executing from external (through RS232 interface) . 67Transferring from external (through RS232 interface) . 68Configuring the firewall. 6910.10Extending/deactivating the CNC lock function . 7010.1110.11.110.11.210.11.2.110.11.2.2Data backup . 72Internal data backup. 72External data backup . 73External data backup in a data archive . 73External data backup of separate files . 7410.12Pocket calculator . 76Programming principles .7711.111.1.111.1.2Fundamentals of programming . 77Program names . 77Program structure . .2.811.2.9Programming instructions . 78Programming dimensions . 78Plane selection: G17 to G19 . 79Absolute/incremental dimensioning: G90, G91, AC, IC. 80Dimensions in metric units and inches: G71, G70, G710, G700 . 81Polar coordinates, pole definition: G110, G111, G112 . 81Programmable work offset: TRANS, ATRANS . 83Programmable rotation: ROT, AROT . 84Programmable scale factor: SCALE, ASCALE . 85Programmable mirroring: MIRROR, AMIRROR . 86Programming and Operating Manual (Milling)01/2017
11.2.1011.2.11Workpiece coordinate system - settable work offset: G54 to G59, G500, G53, G153 . 87NC block compression (COMPON, COMPCURV, COMPCAD) . 8811.311.3.111.3.211.3.3Linear interpolation . 90Linear interpolation with rapid traverse: G0 . 90Feedrate F . 91Linear interpolation with feedrate: G1 . 9111.411.4.111.4.211.4.311.4.411.4.5Circular interpolation. 92Circular interpolation: G2, G3 . 92Circular interpolation via intermediate point: CIP. 97Circle with tangential transition: CT . 98Helix interpolation: G2/G3, TURN. 98Feedrate override for circles: CFTCP, CFC. 9911.511.5.111.5.211.5.3Thread cutting . 100Thread cutting with constant lead: G33 . 100Tapping with compensating chuck: G63 . 101Thread interpolation: G331, G332 . 10211.611.6.111.6.2Fixed point approach . 103Fixed point approach: G75 . 103Reference point approach: G74 . 10411.711.7.111.7.211.7.3Acceleration control and exact stop/continuous path . 104Acceleration pattern: BRISK, SOFT . 104Exact stop/continuous-path control mode: G9, G60, G64 . 105Dwell time: G4 . 10711.811.8.111.8.211.8.3Spindle movements . 108Gear stages . 108Spindle speed S, directions of rotation . 108Spindle positioning: SPOS . 10811.911.9.111.9.2Contour programming support. 109Contour definition programming . 109Rounding, chamfer . 11.10.711.10.8Tool and tool offset . 113General Information . 113Tool T . 114Tool compensation number D . 115Selecting the tool radius compensation: G41, G42 . 117Corner behavior: G450, G451 . 119Tool radius compensation OFF: G40. 120Special cases of the tool radius compensation. 121Example of tool radius compensation . 12311.11Miscellaneous function M . 12411.12H function . 12411.1311.13.111.13.211.13.3Arithmetic parameters, LUD and PLC variables . 125Arithmetic parameter R. 125Local User Data (LUD) . 126Reading and writing PLC variables . 12711.1411.14.111.14.211.14.311.14.4Program jumps . 128Unconditional program jumps . 128Conditional program jumps. 129Program example for jumps . 130Jump destination for program jumps . 13111.1511.15.111.15.211.15.311.15.4Subroutine technique. 131General information . 131Calling machining cycles . 133Modal subroutine call. 133Executing internal and external subroutines (CALL, EXTCALL). 13411.1611.16.111.16.2Timers and workpiece counters . 135Runtime timer . 135Workpiece counter. 137Programming and Operating Manual (Milling)01/20175
1213A611.17Smooth approach and retraction . 13811.18Cylinder surface transformation (TRACYL) . 143Cycles . 15012.1Overview of cycles . 15012.2Programming cycles. 15112.3Graphical cycle programming in the program editor. 2.4.812.4.9Drilling cycles . 153General information. 153Requirements . 154Drilling, centering - CYCLE81 .
Programming and Operating Manual (Milling) 2 01/2017 Preface Applicable products This manual is valid for the following control systems: Control system Software version SINUMERIK 808D ADVANCED M (Milling) V4.7.4: PPU161.3/PPU160.2 with spindle/feed servo system SINUMER