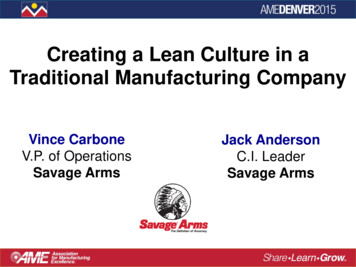
Transcription
Creating a Lean Culture in aTraditional Manufacturing CompanyVince CarboneV.P. of OperationsSavage ArmsJack AndersonC.I. LeaderSavage Arms
Agenda Savage Arms HistoryProducts, Customers, & InnovationsBurning Platform (a call to action)Our Lean Journey (changing course)Continuous Improvement in ActionLessons LearnedNext Steps
Our History . . .Arthur SavageThe Savage Arms Company was organized in 1894 by Arthur Savage inUtica, New York.He developed the Savage Halpine torpedo, became the Superintendent ofthe Utica Belt Line Railroad, and invented the first "hammerless" lever actionrifle .
1920AcquiredJ. Stevens Arms1894Savage ArmsCompanyfoundedby ArthurSavage1920-1930Became theworld’s largestfirearmsmanufacturerafter a seriesof acquisitionsEARLY YEARS(1890-1930)1919Received rightto use the“Indian” headlogo fromChief Lame DeerWorld War IManufactured thefirst wing-mountedmachine gunWorld War IIContributedmillions offirearms to thewar effort byconverting itsfactories toaccommodateheavy munitionsWORLD WAR II& AFTER(1940-1950”S)Post WWIIBegan producingalternateconsumerproductsincluding theworld’s first‘push-along’ and‘fly-mower’lawnmower1960sOperations movedto Westfield, MAand were acquiredby a largeconglomerate thatwas subsequentlyacquired by Black& Decker in 1971MULTIPLEQWNERSHIPCHANGES(1960-1988)1988Filed forbankruptcyprotectiondue to poormanagementand excessleverage afterbeing soldtwice duringthe hyrefocused onproducing highquality riflesnot availablefrom othermanufacturersat competitiveprices1994AcquiredLakefieldArms ge’spatentedrange systemsand bullettrapsdeveloped1989Acquired outof bankruptcyby Challenger Intl.;Ron Coburn named CEO2002Introduced theAccuTrigger 2007AcquiredPorta Target,maker oftargetsystems andshoothousesEnteredarcherymarket withtheacquisitionof BowTech2009IntroducedtheAccuStock ATKACQUISITION(2013-TODAY)PRIVATE OWNERSHIP(1995-2013)2000Introducedworld’s firstsmokelessmuzzleloader1995Acquiredthrough LBOby Ron Coburnand NauticPartners2013ATKpurchasesSavage Arms2010IntroducedSavage AXIS2004Long PointCapital andmanagementrecapitalizedthe businessTHE SAVAGE STORY2015ATK SportingGroup spins offand becomesVista Outdoor
Today . . .Savage ArmsWestfield, MATotal Area: 23.3 acres350,000 sq. ft.326 employees
Our Products . . . Model 10/110Introduced in 1958Over 1 Million Model 110’s produced Action design has become the blueprint & standard for accuracy in firearmsdesign throughout the industry Very strong & robust action: Able to handle high performance cartridgessuch as: .300 WM & .338 Lapua Very versatile design with 100’s of configurations
Savage#1 Centerfire rifle manufacturer#1 Bolt action rimfire rifle manufacturer
Innovative DesignTHE NEW INDUSTRY STANDARD: Savage ACCUTRIGGER User Adjustable trigger: (6oz – 6 lbs depending on model) No paying gunsmith to get a “trigger job” or purchasing an aftermarket trigger Very crisp with no creep Extremely Safe
Innovative DesignNew for 2015A17 Autoloader – 17 HMR
Our Customers . . .
“Out of the box accuracy”Darrell BuellDamascus, ORJohn WeilWelches, ORMonte MilanukWenatchee, WAStan PateMilwaukie, OR
Before Lean:Batch & Queue CultureOur Burning Platform Double digit defect rate23% Long lead time to the customerMonths Large batch sizes120 Multiple non-connected processes16 Days WIP Unreliable equipment/breakdownsNo TPM Command and control management style Could not keep up with Sales at 550 Guns/Day Dirty and Cluttered Production Environment BUT VERY SUCCESSFUL !!!
Kaizen EventsReceiver Department 5STPM, POUS, Pull SystemsSetup ReductionJourney BeginsMassMEP PartnershipLean 101 TrainingContinuous Flow Layout200320052004Leadership ChangesNew V.P. of OperationsLean Culture TractionLean 101 Training200720062008Value Stream MappingPull Systems5S InitiativeReceiver DepartmentBarrel DepartmentAssembly Department2 Bin SystemBalanced FlowlineLot Size ReductionSupplier Pull SystemEmployee TeamsVSM EventsLead TimeReductionsOur Lean Journey Begins . . .
Our 3 Main Value StreamsBarrelsReceiversAssembly
Creating a Lean Culture TOTAL SUPPORT from Top Management A Full Time Lean Expert at the top managementlevel Formal Top Level G&O’s / Use the LeanPlatform to drive the G&O’s Managers with Lean knowledge to manage theprocess Formal process of conducting Kaizen An adequate training room A need or crisis to change the culture
Lean tools available toChange the Culture Use the tools in your Lean Toolbox whereneeded Value Stream Mapping Start with quick wins like 6S Utilize TPM where the need to maintainequipment is crucial Use standard work as a compliment to 6S Train the Trainers
Lean tools available toChange the Culture Train everyone and keep the training going Celebrate all events Do not use excuses not to improve (month end,too busy, etc.) Try not to remove an employee from a Kaizendue to a production need Make the Kaizen no more than 5 days
Westfield OperationsAl KasperPresident/COOJack AndersonC.I. LeaderMike GreeneDirector of Machining Ops.Chris BezzinaDirector of OperationsVince CarboneV. P. of OperationsBob BrowningDirector of Supply ChainRoy ProvostDirector of Assembly Ops.Rick BonciDirector of Quality
FY2015 Operations Goals and Objectives 2400 Guns/Day (in a 5 day work week) Cost Reduction – 1MM through Continuous Improvement New Product Introduction - Meet all project milestones, costtargets and product introduction dates Quality / Rework Improvement Inventory Reductions Equipment and Process Enhancements (TPM, StandardWork) Factory Layout Training Programs
FY 2015 Goals and Objectives Execute the Quality Management System (QA, ENG, MFG) – Barrel, Receiver, Assembly and Finishing Cells Execute the Quality Management System SPP (QA, SCM, ENG) - Top Ten Vendors Reduce range rejects to less than 3% for Axis and less than 5% for all other (QA, MFG, ENG) Negotiate a new 3 year labor contract (HR Director, VP Operations, CFO Accounting) Improve communications within Salaried ranks (HR and Staff) Ensure complete compliance with OSHA regulations (HR, ENG, MFG) Lean – Engineering to lead one Kaizen per month, Manufacturing to lead one Kaizen per month, Maintenance to lead one TPM permonth (will depend on resources available). Service and Accounting/MIS one per quarter Cost reduction 1.0 M (MFG, SCM, QA, ENG) New Products – Hit production date, cost target and improve overall process (MFG, SCM, QA, ENG) Production run rate at 1800 guns per day to 2400 guns per year by year end in a five day work schedule (MFG, SCM, QA, ENG) Standard Work (“Best Way”) (MFG, SCM, QA, ENG) Implement simultaneously in the Assembly, Finishing Department Processes and inMachining Training Create Job Breakdown Sheets and Training Timetables for Swing, Proof, Finishing, Ejector, Roll Stamp, Scope Mount, Build &Stock, Function, and Oil/Tag/Serialization Processes Employee Engagement (MFG, SCM, QA, ENG) Increase Employee Kaizen Participation (involve 2nd, and 3rd shift personnel)Employees involved in improving their processes, employ daily team huddlesEnhance communication, awareness, and teamwork between employees Maintenance Excellence (MFG, SCM, QA, ENG) TPM Events (identify critical equipment and schedule events accordingly)Improve machine safety, uptime, and create a renewed focus on energy conservation Problem Solving (MFG, SCM, QA, ENG) Utilize PDCA, and A3 Reports (data driven tool used as a plant wide problem solving tool)Continuous Flow (Assembly Department) (MFG, SCM, QA, ENG) Implement A Mag Rimfire Continuous Flowline (based on Axis Flowline)Create an Ejector/Roll Stamp/Scope Mount CellValue Stream Mapping (MFG, SCM, QA, ENG) Involve and train horizontal value stream process owners in VSM techniquesUtilize department VSM’s(Current & Future) to identify continuous improvements opportunitiesVisual Management/KPI’s (MFG, SCM, QA, ENG) Identify and track critical KPI’s to monitor in all departments (ex. Safety, Quality, Cost,Delivery, Training, 6S, Scrap)Plant Layout (MFG, SCM, QA, ENG) Implement 2013/2014 plant layout relocations in support of the approved 2015 Master Plan
LEAN TOOLBOX Pull Systems Value Stream Mapping Standard Work 6S SMED Heijunka TPM PDCA 8 Wastes 5 Whys Gemba Walks Poka Yoke Visual Controls Cellular Flow Takt Time Process Improvement OEE FIFO (first in first out) LSW VA / NVA Work KAIZEN Problem Solving(level loading)(mistake proofing)(one-piece flow)
2015 Lean/Continuous Improvement FocusMaintenance TPM / PMTPM Events – Machining DepartmentsMaintenance Excellence InitiativeEmployee Training / Employee EngagementStandard WorkJob InstructionProblem SolvingKaizen / BlitzesQuality / QMSDefect ReductionProcess AuditsGaging / CalibrationProcess Improvements / Continuous ImprovementAssembly DepartmentMachining DepartmentsValue Stream MappingVisual FactoryKPI’s / 6S InitiativeVisual Standards / Communication DisplaysEngineeringNew Product Introductions23
Lean DriversJack AndersonC. I. LeaderChris BezzinaDirector of OperationsDavid KronengoldDirector of EngineeringVince CarboneV. P. of OperationsWayne KratochvilComponents PlannerMike GreeneDirector of Machining Ops.Paul SmarrelliDirector of Customer ServiceRoy ProvostDirector of Assembly Ops.Don SkellyMaterials ManagerRick BonciDirector of Quality
Process ImprovementPacking ProcessShot Blast ProcessFinance ProcessesIncoming ReceivingTrain The TrainerWestfield & Lakefield5S Training withMassMEP FacilitatorLean 101 TrainingFluting SMED Kaizen200920112010Value Stream MappingBarrel DepartmentReceiver DepartmentAssembly DepartmentOrder Entry ProcessPlant Layout ChangesTPM /Kaizen EventsTPM TrainingRange ImprovementsOffice KaizenStandard Work201320122014Kaizen Events6S/Standard WorkProof & FunctionBarrel Bore FinishCustomer ServiceRTV ProcessSwing ReworkStandard Work VideosEmployee EngagementContinuous Flow FocusLean Training GrantOur Lean Journey Restart . . .
BatchingThe Old Receiver Manufacturingprocesses that consisted of:Ten CellsMill Line 1Mill Line 2Trigger slotAuto DrillMill Line 3Safety SlotMill Line 4Hand File2007WashThreadingTwenty four Machines
2015
LEAN TOOLBOX Pull Systems Value Stream Mapping Standard Work 6S SMED Heijunka TPM PDCA 8 Wastes 5 Whys Gemba Walks Poka Yoke Visual Controls Cellular Flow Takt Time Process Improvement OEE FIFO (first in first out) LSW VA / NVA Work KAIZEN Problem Solving(level loading)(mistake proofing)(one-piece flow)
Value Stream MappingValue Stream Mapping – Current State
Value Stream MappingValue Stream Mapping – Future State
Value Stream MappingSuggested KaizenBenefitSponsorTeam LeaderStartDateGun Drill TPMImprove Uptime, Avoid Delays,Increase CapacityMike GreeneKeith Albee / JackAndersonAprilGun Drill SMED Set UpReductionImprove Uptime, Avoid Delays,Increase CapacityMike GreeneRon VishawayAprilScrap / Rework ReportingSystemPerformance Metric, Process Control,Improvement OpportunitiesRick BonciMike GreeneAprilWash / Polish / Oil & Bag CellReduce Distance Traveled, AvoidParts Transportation / Travel WasteMike GibbsDean PeatmanJuneGun Drill ToolingImprove Uptime, Avoid Delays,Increase CapacityMike GreeneFrank DarcyMayTWI Job Instruction Training/Cross TrainingEmployee Development, WorkforceFlexibility, Job SatisfactionVince CarboneJack AndersonJulyCut Off SupermarketImprove Synchronization, AvoidOverproduction, Reduce WIPMike GreeneWayne Kratochvil/ Mike GreeneMarchTurning & Chambering 6SKaizen EventsOrganize work areas for greater flowand less wastesMike GreenePatrick KenneyMayVSM Improvement Plan
Our Improvement tScheduleC. I. Improvement FlowmapKaizenEvent
Kaizen EventsContinuous Improvement – Employee Driven
Kaizen EventsContinuous Improvement – Employee Driven
Day OneKaizen AgendaKaizen Lean TrainingObserve & Document Current ProcessDay TwoIdentify Problems & BarriersBrainstorm Improvement IdeasDay ThreeDevelop Action PlansImplement Action PlansDay FourContinue ImprovementsDocument & Train to New Standard WorkDay FiveKaizen Presentation
6SLIFE BEFORE 6SWorkplace Organization
Pull SystemsPurchasingKanban CardSupplierA basic pull replenishment system starts with the demand for parts or material. With the needfor replenishment, a SIGNAL is sent back to Purchasing to supply more parts or material.
TPM (Total Productive Maintenance)TPM requires the involvementof all people in the organization.MaintenanceOperatorsManagement
Standard WorkInvolve the people that do the work and help develop the“Best Way” to do the process as you know it today,then keep improving it.Standard Work ChartStandard Work Video
Continuous FlowFirst in First Out Lanes
Visual FactoryVISUAL FACTORY(13) digital signage stationsKPI’sCompany InformationSafety AlertsKaizen EventsNew Product ReleasesEmployee ProfilesHealth & Wellness
2-Year Training Grant2013/2015 - 8 modulesLean 101Value Stream MappingStandardized WorkLean Expert CertificationChampion TrainingInspector Technician CertificationSupervisory SkillsLean Supply Chain Certification––––––––400 employees33 employees33 employees30 employees16 employees24 employees25 employees13 employees
Lean 101 Training
Lean 101 Training
Employee Training
Lean ChampionsJack AndersonC. I. LeaderChris BezzinaDirector of OperationsDavid KronengoldDirector of EngineeringVince CarboneV. P. of OperationsWayne KratochvilComponents PlannerMike GreeneDirector of Machining Ops.Paul SmarrelliDirector of Customer ServiceRoy ProvostDirector of Assembly Ops.Don SkellyMaterials ManagerRick BonciDirector of Quality
Lean ExpertsJack AndersonC.I. LeaderBen LewisQuality EngineerFrank DarcyManufacturing SupervisorSandy MolloyGroup Leader – Sub-AssemblyHector TorresMaterial CoordinatorJessica HenryStaff AccountantDon SkellyMaterials ManagerMaryanne GignacCustomer ServiceIsrael MaldonadoGroup Leader - BarrelsKristin OlbrysMRO BuyerVitaliy BlishchikGroup Leader - ReceiversJames VassalloBuilder/ShooterCraig PriestCNC OperatorJoslin HawleyGroup Leader - ReceiversRon VishawayManufacturing SupervisorKate GihonC.I. SpecialistReid LavalleeManufacturing SupervisorWayne KratochvilComponents PlannerChristian SavariaQuality InspectorEric BerriosGroup Leader - Barrels
Barrel CutoffChamberingGun DrillRiflingStraightenWashReamTurnComponents1,230 total feetBarrel ManufacturingJune 2014
PolishWashChamberingComponentsStraightenTurn590 total feetRiflingReamMaster PlanBarrel ManufacturingFuture StateGun DrillCutoff
CutoffHand FileTumbleHeat TreatPickleTurnGun DrillBroachOkuma A-B1,400 total feetReceiver ManufacturingJune 2014
Heat TreatHand FileComponentsOkuma A-B780 total feetBroachMaster PlanTurnGun DrillCutoffReceiver ManufacturingFuture State
PassivateShot BlastBlack OxideSwing1,150 total feetEjectorRoll StampScope MountRifle ProductionCurrent State June 2014AssemblyFinished GoodsPackingRangeSerialization
PassivateShot BlastSwingBlack OxideRange925 total feetMaster PlanRifle ProductionFuture StatePackingTo Finish GoodsWarehouseBoresightSerialization
Factory of the FutureNew Manufacturing Plant Layout“Creating a clean, safe, and productive work environment”Summer 2014
Factory of the FutureMoved 75 machines since the July Shutdownto enhance flow and reduce lead time
New Manufacturing Plant LayoutJuly 2014toDecember 201475 machinesrelocatedBarrelsReceivers
Next StepsUpcoming Employee TrainingApril 2015Team Involvement Problem Solving (TIPS)Leader Effectiveness Training (L.E.T)
HOW ARE WE GOING TO CONTINUE TO DO IT?EMPLOYEEENGAGEMENTGreat People Make Savage! #1 Rifle Sales High Quality Product Industry Leading Innovation Tremendous Value
Safety (SQDEC)Lean Safety Gemba WalksFocus on Safety
Quality (SQDEC)
Delivery (SQDEC)181616 daysreduced down to3 days 2AssemblyLead Time Reduction (days of WIP)2014
Delivery (SQDEC)140120120 per lot100reduced down to20 per lot806040200201020122013Barrel Lot Size Reduction2014
Employee Engagement (SQDEC)AutonomyMasteryPurpose
Cost (SQDEC)Lean Cost Saving Program Annualized2008 Total 1,054,6342009 Total 2,461,4392010 Total 897,9612011 Total 1,078,7612012 Total 1,285,3302013 Total 230,822 (4 months switched to ATK fiscal year)2014 Total 2,270,8502015 Total 1,019,387Eight Year Total 10,299,184
Value Added (EBITDA) per Associate
Lessons Learned Top Management needs to be totally committed Easy to fall back to old habits – “sustain the gains” Use Value Stream Mapping to chart the course Provide Lean training for all associates Create Lean Experts and Champions
Lessons Learned Select the right Lean tool for the right application Involve and show Respect for People Utilize Standard Work and keep on improving Go and See the process – Gemba Walks
Thank You!A link to the full conference survey willbe emailed to you Tuesday afternoon.Session Code: VS-3Creating a Lean Culture in a TraditionalManufacturing CompanyVince CarboneJack AndersonSavage m
Kaizen Events Receiver Department 5S TPM, POUS, Pull Systems Setup Reduction Value Stream Mapping Receiver Department Barrel Department Assembly Department Pull Systems 2 Bin System Balanced Flowline Lot Size Reduction Supplier Pull System 5S Initiative Employee Teams VSM