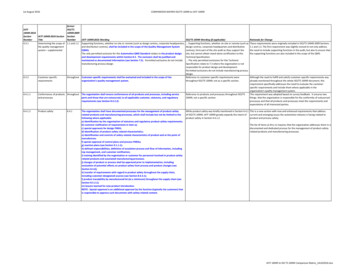
Transcription
1st August 2016IATF16949:2016SectionIATF 16949:2016 SectionNumberTitle4.3.1Determining the scope ofthe quality managementsystem – supplementalCOMPARISON MATRIX ISO/TS 16949 to IATF 16949formerISO/TS16949:2009SectionNumberIATF 16949:2016 Wording1.1 and 1.2 Supporting functions, whether on-site or remote (such as design centres, corporate headquarters,and distribution centres), shall be included in the scope of the Quality Management System(QMS).The only permitted exclusion for this Automotive QMS Standard relates to the product designand development requirements within Section 8.3. The exclusion shall be justified andmaintained as documented information (see Section 7.5). Permitted exclusions do not includemanufacturing process design.throughoutRationale for ChangeThese requirements were originally included in ISO/TS 16949:2009 Sections1.1 and 1.2. The first requirement was slightly revised to not only addressthe need to include supporting functions in the audit, but also to ensure thatthe supporting functions are also included in the scope of the rmance of products throughoutand processesThe organization shall ensure conformance of all products and processes, including serviceparts and those that are outsourced, to all applicable customer, statutory, and regulatoryrequirements (see Section 8.4.2.2).Reference to products and processes throughout ISO/TS16949, not a specific section.4.4.1.2Product safetyThe organization shall have documented processes for the management of product-safetyrelated products and manufacturing-processes, which shall include but not be limited to thefollowing where applicable:a) identification by the organization of statutory and regulatory product-safety requirements;b) customer notification of requirements in item a);c) special approvals for design FMEA;d) identification of product-safety related characteristics;e) identification and controls of safety related characteristics of product and at the point ofmanufacture;f) special approval of control plans and process FMEAs;g) reaction plans (see Section 9.1.1.1);h) defined responsibilities, definition of escalation process and flow of information, includingtop management, and customer notification;i) training identified by the organization or customer for personnel involved in product-safetyrelated products and associated manufacturing processes;j) changes of product or process shall be approved prior to implementation, includingevaluation of potential effects on product safety from process and product changes (seeSection 8.3.6);k) transfer of requirements with regard to product safety throughout the supply chain,including customer-designated sources (see Section 8.4.3.1);l) product traceability by manufactured lot (at a minimum) throughout the supply chain (seeSection 8.5.2.1);m) lessons learned for new product introduction.NOTE: Special approval is an additional approval by the function (typically the customer) thatis responsible to approve such documents with safety-related content.While product safety was briefly mentioned in Section 6.4.1 This is a new section with new and enhanced requirements that addressof ISO/TS 16949, IATF 16949 greatly expands the intent of current and emerging issues the automotive industry is facing related toproduct safety in Section 4.4.1.2.product and process safety.6.4.1Customer-specific requirements shall be evaluated and included in the scope of theorganization’s quality management system.ISO/TS 16949 Wording (if applicable). Supporting functions, whether on-site or remote (such asdesign centres, corporate headquarters and distributioncentres), form part of the site audit as they support thesite, but cannot obtain stand-alone certification to thisTechnical Specification. The only permitted exclusions for this TechnicalSpecification relate to 7.3 where the organization is notresponsible for product design and development.Permitted exclusions do not include manufacturing processdesign.Reference to customer-specific requirements werethroughout ISO/TS 16949, not as a specific section.Although the need to fulfill and satisfy customer-specific requirements wasalready mentioned throughout the whole ISO/TS 16949 document, thisrequirement specifically addresses the need to evaluate the customerspecific requirements and include them where applicable in theorganization's quality management system.This requirement was adopted based on survey feedback. It ensures twothings: that the organization is responsible for the conformity of outsourcedprocesses and that all products and processes meet the requirements andexpectations of all interested parties.The list of items a) thru n) requires that the organization addresses them in adocumented and dedicated process for the management of product-safetyrelated products and manufacturing processes.IATF 16949 to ISO TS 16949 Comparison Matrix 1AUG2016.xlsx
IATF16949:2016SectionIATF 16949:2016 SectionNumberTitle5.1.1.1Corporate ordingnot included The organization shall define and implement corporate responsibility policies, including at aminimum an anti-bribery policy, an employee code of conduct, and an ethics escalation policy(“whistle-blowing policy”).Top management shall review the product realization processes and support processes toevaluate and improve their effectiveness and efficiency. The results of the process reviewactivities shall be included as input to the management review (see Section 9.3.2.1.).ISO/TS 16949 Wording (if applicable)Coporate responsibility was not included in ISO/TS 16949.Top management shall review the product realization processes and the support processes toassure their effectiveness and efficiency.Rationale for ChangeISO 9001:2015 expanded the ISO 9001:2009 concept of ManagementResponsibility and Commitment into a set of leadership behaviors to ensurean effective Quality Management System. The IATF supplemented the ISOrequirements by adopting a Corporate Responsibility requirement to addressincreasing market and governmental expectations for improved integrity insocial and environmental matters.The requirement to review the processes to ensure effectiveness andefficiency was covered in ISO/TS 16949, Section 5.1.1. Based on the IATFsurvey feedback, the IATF strengthened the requirement to ensure that theresults of the review are now to be included in the management review.5.1.1.2Process effectiveness and 5.1.1efficiency5.1.1.3Process ownersnot included Top management shall identify process owners who are responsible for managing theProcess owners were not called out in ISO/TS 16949.organization’s processes and related outputs. Process owners shall understand their roles andbe competent to perform those roles (see Section 7.2).ISO/TS 16949:2009 addressed management responsibility and authority, butit did not explicitly mention that management ensure process ownersunderstand their role and are competent. The IATF adopted thisrequirement to ensure that management understands this expectation.5.3.1Organizational roles,responsibilities, andauthorities –supplemental5.5.2.1Top management shall assign personnel with the responsibility and authority to ensure thatcustomer requirements are met. These assignments shall be documented. This includes, but isnot limited to, the selection of special characteristics, setting quality objectives and relatedtraining, corrective and preventive actions, product design and development, capacity analysis,logistics information, customer scorecards, and customer portals.Top management shall designate personnel with responsibility and authority to ensure thatcustomer requirements are addressed. This includes selection of special characteristics, settingquality objectives and related training, corrective and preventive actions, product design anddevelopment.5.3.2Responsibility andauthority for productrequirements andcorrective actions5.5.1.1Top management shall ensure that:a) personnel responsible for conformity to product requirements have the authority to stopshipment and stop production to correct quality problems;NOTE: Due to the process design in some industries, it might not always be possible to stopproduction immediately. In this case, the affected batch must be contained and shipmentprevented.b) personnel with authority and responsibility for corrective action are promptly informed ofproducts or processes that do not conform to requirements to ensure that non-conformingproduct is not shipped to the customer and that all potential non-conforming product isidentified and contained;c) production operations across all shifts are staffed with personnel in charge of, or delegatedresponsibility for, ensuring conformity to product requirements.Managers with responsibility and authority for corrective action shall be promptly informed ofproducts or processes which do not conform to requirements.Personnel responsible for conformity to product requirements shall have the authority to stopproduction to correct quality problems.Production operations across all shifts shall be staffed with personnel in charge of, or delegatedresponsibility for, ensuring conformity to product requirements.This requirement was already part of ISO/TS 16949:2009. However based onIATF survey feedback, the IATF adopted some modifications to therequirement to address the need to document assigned personnelresponsibilities and authorities. Additionally, clarifying that the goal is notjust to address customer requirements but to meet customer requirementsfully.The IATF adopted some enhancements to the requirement originallyincluded in ISO/TS 16949 based on IATF survey feedback to address the needto explicitly make Top Management responsible for ensuring conformity toproduct requirements and to corrective actions taken.
IATF16949:2016SectionIATF 16949:2016 SectionNumberTitle6.1.2.1Risk 7.2.2.2The organization shall include in its risk analysis, at a minimum, lessons learned from productrecalls, product audits, field returns and repairs, complaints, scrap, and rework. Theorganization shall retain documented information as evidence of the results of risk analysis.ISO/TS 16949 Wording (if applicable)Reference to risk analysis was in Section 7.2.2.2 of ISO/TS 16949, however, risk analysis was not aspecific section.Preventive action was in the ISO 9001:2008 portion of ISO/TS 16949. The organization shalldetermine action to eliminate the causes of potential nonconformities in order to prevent theiroccurrence. Preventive actions shall be appropriate to the effects of the potential problems.A documented procedure shall be established to define requirements fora) determining potential nonconformities and their causes,b) evaluating the need for action to prevent occurrence of nonconformities,c) determining and implementing action needed,d) records of results of action taken (see 4.2.4), ande) reviewing the effectiveness of the preventive action taken.Rationale for ChangeThe need to identify, analyze, and consider actual and potential risks wasalready covered in various areas of ISO/TS 16949. The IATF adopted theadditional requirements for risk analysis recognizing the continual need toanalyze and respond to risk and to have organizations consider specific risksassociated with the automotive industry.The IATF enhanced the requirement found in ISO/TS 16949 bycomprehending what is considered to be best practice in the automotiveindustry.6.1.2.2Preventive action8.5.3The organization shall determine and implement action(s) to eliminate the causes of potentialnonconformities in order to prevent their occurrence. Preventive actions shall be appropriate tothe severity of the potential issues.The organization shall establish a process to lessen the impact of negative effects of riskincluding the following:a) determining potential nonconformities and their causes;b) evaluating the need for action to prevent occurrence of nonconformities;c) determining and implementing action needed;d) documented information of action taken;e) reviewing the effectiveness of the preventive action taken;f) utilizing lessons learned to prevent reoccurrence in similar processes (see Section 7.1.6).6.1.2.3Contingency plans6.3.2The organization shall:The organization shall prepare contingency plans to satisfy customer requirements in the event ofa) identify and evaluate internal and external risks to all manufacturing processes andan emergency such as utility interruptions, labour shortages, key equipment failure and fieldinfrastructure equipment essential to maintain production output and to ensure that customer returns.requirements are met;b) define contingency plans according to risk and impact to the customer;c) prepare contingency plans for continuity of supply in the event of any of the following: keyequipment failures (also see Section 8.5.6.1.1); interruption from externally provided products,processes, and services; recurring natural disasters; fire; utility interruptions; labour shortages;or infrastructure disruptions;d) include, as a supplement to the contingency plans, a notification process to the customerand other interested parties for the extent and duration of any situation impacting customeroperations;e) periodically test the contingency plans for effectiveness (e.g., simulations, as appropriate);f) conduct contingency plan reviews (at a minimum annually) using a multidisciplinary teamincluding top management, and update as required;g) document the contingency plans and retain documented information describing anyrevision(s), including the person(s) who authorized the change(s).The contingency plans shall include provisions to validate that the manufactured productcontinues to meet customer specifications after the re-start of production following anemergency in which production was stopped and if the regular shutdown processes were notfollowed.The IATF enhanced the requirement found in ISO/TS 16949 bycomprehending what is considered to be best practice in the automotiveindustry. The expanded requirement ensures the organization defines andprepares contingency plans along with a notification process to the customeror other interested parties.6.2.2.1Quality objectives and5.4.1.1planning to achieve them– supplementalTop management shall ensure quality objectives to meet customer requirements are defined,established, and maintained for relevant functions, processes, and levels throughout theorganization.The results of the organization’s review regarding interested parties and their relevantrequirements shall be considered when the organization establishes its annual (at a minimum)quality objectives and related performance targets (internal and external).ISO/TS 16949 included the importance of addressing customer expectationsin the NOTE to Section 5.4.1.1. The IATF decided to enhance therequirement by including the NOTE in Section 6.2.2.1 and to require that itbe done at all levels throughout the organization.Top management shall define quality objectives and measurements that shall be included in thebusiness plan and used to deploy the quality policy.NOTE Quality objectives should address customer expectations and be achievable within a definedtime period.
IATF16949:2016SectionNumberIATF 16949:2016 Section Title7.1.3.1Plant, facility, and erWording6.3.1The organization shall use a multidisciplinary approach including risk identification and riskmitigation methods for developing and improving plant, facility, and equipment plans. Indesigning plant layouts, the organization shall:a) optimize material flow, material handling, and value-added use of floor space including controlof non-conforming product, andb) facilitate synchronous material flow, as applicable.Methods shall be developed and implemented to evaluate manufacturing feasibility for newproduct or new operations. Manufacturing feasibility assessments shall include capacityplanning. These methods shall also be applicable for evaluating proposed changes to existingoperations.The organization shall maintain process effectiveness, including periodic re-evaluation relativeto risk, to incorporate any changes made during process approval, control plan maintenance(see Section 8.5.1.1), and verification of job set-ups (see Section 8.5.1.3).Assessments of manufacturing feasibility and evaluation of capacity planning shall be inputs tomanagement reviews (see Section 9.3).NOTE 1 These requirements should include the application of lean manufacturing principles.NOTE 2 These requirements should apply to on-site supplier activities, as applicable.ISO/TS 16949 Wording (if applicable)Rationale for ChangeThe organization shall use a multidisciplinary approach (see 7.3.1.1) for developing plant, facilityIncreased focus on risk identification and risk mitigation; evaluating manufacturing feasibility; re-evaluation of changesand equipment plans. Plant layouts shall optimize material travel, handling and value-added use of in processes; and inclusion of on-site supplier activities.floor space, and shall facilitate synchronous material flow. Methods shall be developed andimplemented to evaluate and monitor the effectiveness of existing operations.NOTE These requirements should focus on lean manufacturing principles and the link to theeffectiveness of the quality management system.7.1.4.1Environment for the operation ofprocesses – supplemental6.4.2The organization shall maintain its premises in a state of order, cleanliness, and repair that isconsistent with the product and manufacturing process needs.The organization shall maintain its premises in a state of order, cleanliness and repair consistentwith the product and manufacturing process needs.Requirement maintained from ISO/TS 16949 to IATF 16949, moved to Section 7.1.4.1.7.1.5.1.1Measurement system analysis7.6.1Statistical studies shall be conducted to analyse the variation present in the results of each type ofinspection, measurement, and test equipment system identified in the control plan. Theanalytical methods and acceptance criteria used shall conform to those in reference manuals onmeasurement systems analysis. Other analytical methods and acceptance criteria may be used ifapproved by the customer.Records of customer acceptance of alternative methods shall be retained along with resultsfrom alternative measurement systems analysis (see Section 9.1.1.1).NOTE Prioritization of MSA studies should focus on critical or special product or processcharacteristics.Statistical studies shall be conducted to analyse the variation present in the results of each type of Records are now required for customer acceptance of alternative methods. See Annex B, which contains IATFmeasuring and test equipment system. This requirement shall apply to measurement systemsrecommended tools for implementation.referenced in the control plan. The analytical methods and acceptance criteria used shall conformto those in customer reference manuals on measurement systems analysis. Other analyticalmethods and acceptance criteria may be used if approved by the customer.7.1.5.2.1Calibration/verification records7.6.2The organization shall have a documented process for managing calibration/verificationrecords. Records of the calibration/verification activity for all gauges and measuring and testequipment (including employee-owned equipment relevant for measuring, customer-ownedequipment, or on-site supplier-owned equipment) needed to provide evidence of conformity tointernal requirements, legislative, and regulatory requirements, and customer definedrequirements shall be retained.The organization shall ensure that calibration/verification activities and records shall includethe following details:a) revisions following engineering changes that impact measurement systems;b) any out-of-specification readings as received for calibration/verification;c) an assessment of the risk of the intended use of the product caused by the out-of-specificationcondition;d) when a piece of inspection measurement and test equipment is found to be out ofcalibration or defective during its planned verification or calibration or during its use,documented information on the validity of previous measurement results obtained with thispiece of inspection measurement and test equipment shall be retained, including theassociated standard's last calibration date and the next due date on the calibration report;e) notification to the customer if suspect product or material has been shipped;f) statements of conformity to specification after calibration/verification;g) verification that software version used for product and process control is as specified;h) records of the calibration and maintenance activities for all gauging, (including employeeowned equipment, customer-owned equipment, or on-site supplier owned equipment);i) production related software verification used for product and process control (includingsoftware installed on employee-owned equipment, customer-owned equipment, or on-sitesupplier owned equipment).Records of the calibration/verification activity for all gauges, measuring and test equipment,needed to provide evidence of conformity of product to determined requirements, includingemployee- and customer-owned equipment, shall include- equipment identification, including the measurement standard against which the equipment iscalibrated,- revisions following engineering changes,- any out-of-specification readings as received for calibration/verification,- an assessment of the impact of out-of-specification condition,- statements of conformity to specification after calibration/verification, and- notification to the customer if suspect product or material has been shipped.7.1.5.3.1Internal laboratory7.6.3.1An organization's internal laboratory facility shall have a defined scope that includes its capabilityto perform the required inspection, test, or calibration services. This laboratory scope shall beincluded in the quality management system documentation. The laboratory shall specify andimplement, as a minimum, requirements for:a) adequacy of the laboratory technical procedures;b) competency of the laboratory personnel;c) testing of the product;d) capability to perform these services correctly, traceable to the relevant process standard (suchas ASTM, EN, etc.); when no national or international standard(s) is available, the organizationshall define and implement a methodology to verify measurement system capability;e) customer requirements, if any;f) review of the related records.NOTE Third-party accreditation to ISO/IEC 17025 (or equivalent) may be used to demonstratethe organization's in-house laboratory conformity to this requirement.An organization's internal laboratory facility shall have a defined scope that includes its capability Added requirement to have the organization (client) define a methodology to verify measurement system capability ifto perform the required inspection, test or calibration services. This laboratory scope shall beno national or international standard(s) exist.included in the quality management system documentation. The laboratory shall specify andimplement, as a minimum, technical requirements for- adequacy of the laboratory procedures,- competency of the laboratory personnel,- testing of the product,- capability to perform these services correctly, traceable to the relevant process standard (such asASTM, EN, etc.), and- review of the related records.NOTE Accreditation to ISO/IEC 17025 may be used to demonstrate the organization's in-houselaboratory conformity to this requirement but is not mandatory.Ensuring that customer requirements are met, enhanced calibration/ verification record retention requirements,including software installed on employee-owned or customer-owned equipment.
7.1.5.3.2External laboratory7.6.3.2External/commercial/independent laboratory facilities used for inspection, test, or calibrationservices by the organization shall have a defined laboratory scope that includes the capability toperform the required inspection, test, or calibration, and either:— the laboratory shall be accredited to ISO/IEC 17025 or national equivalent and include therelevant inspection, test, or calibration service in the scope of the accreditation (certificate);the certificate of calibration or test report shall include the mark of a national accreditationbody, or— there shall be evidence that the external laboratory is acceptable to the customer.NOTE Such evidence may be demonstrated by customer assessment, for example, or bycustomer-approved second-party assessment that the laboratory meets the intent of ISO/IEC17025 or national equivalent. The second-party assessment may be the organization assessingthe laboratory using a customer-approved method of assessment.Calibration services may be performed by the equipment manufacturer when a qualifiedlaboratory is not available for a given piece of equipment. In such cases, the organization shallensure that the requirements listed in Section 7.1.5.3.1 have been met. Use of calibrationservices, other than by qualified (or customer accepted) laboratories, may be subject togovernment regulatory confirmation, if required.The organization shall establish and maintain a documented process(es) for identifying trainingneeds including awareness (see Section 7.3.1) and achieving competence of all personnelperforming activities affecting conformity to product and process requirements. Personnelperforming specific assigned tasks shall be qualified, as required, with particular attention to thesatisfaction of customer requirements.External/commercial/independent laboratory facilities used for inspection, test or calibrationAllows the organization to conduct second-party assessments of laboratory facilities; however, requires customerservices by the organization shall have a defined laboratory scope that includes the capability toapproval of assessment method. Added government regulatory confirmation, if required.perform the required inspection, test or calibration, and either- there shall be evidence that the external laboratory is acceptable to the customer, or- the laboratory shall be accredited to ISO/IEC 17025 or national equivalent.NOTE 1 Such evidence may be demonstrated by customer assessment, for example, or bycustomer-approved second-party assessment that the laboratory meets the intent of ISO/IEC17025 or national equivalent.NOTE 2 When a qualified laboratory is not available for a given piece of equipment, calibrationservices may be performed by the equipment manufacturer. In such cases, the organization shouldensure that the requirements listed in 7.6.3.1 have been met.7.2.1Competence - supplemental6.2.2.2The organization shall establish and maintain documented procedures for identifying trainingneeds and achieving competence of all personnel performing activities affecting conformity toproduct requirements. Personnel performing specific assigned tasks shall be qualified, as required,with particular attention to the satisfaction of customer requirements.NOTE 1 This applies to all employees having an effect on quality at all levels of the organization.NOTE 2 An example of the customer-specific requirements is the application of digitizedmathematically based data.Adds requirement of “awareness,” which includes knowledge of organization’s (client’s) quality policy, qualityobjectives, personnel contribution to the QMS, benefits of improved performance, and implications of not conformingwith QMS requirements. Also, further emphasizes the customer requirements for OJT (on-the-job) training, not justquality requirements.7.2.2Competence - on-the-job training6.2.2.3The organization shall provide on-the-job training (which shall include customer requirementstraining) for personnel in any new or modified responsibilities affecting conformity to qualityrequirements, internal requirements, regulatory or legislative requirements; this shall includecontract or agency personnel. The level of detail required for on-the-job training shall becommensurate with the level of education the personnel possess and the complexity of thetask(s) they are required to perform for their daily work. Persons whose work can affect qualityshall be informed about the consequences of nonconformity to customer requirements.The organization shall provide on-the-job training for personnel in any new or modified jobaffecting conformity to product requirements, including contract or agency personnel. Personnelwhose work can affect quality shall be informed about the consequences to the customer ofnonconformity to quality requirements.Enhanced emphasis of on-the-job training and its importance in meeting customer requirements, including otherinterested parties.7.2.3Internal auditor competency8.2.2.5The organization shall have a documented process(es) to verify that internal auditors arecompetent, taking into account any customer-specific requirements. For additional guidanceon auditor competencies, refer to ISO 19011. The organization shall maintain a list of qualifiedinternal auditors.Quality management system auditors, manufacturing process auditors, and product auditorsshall all be able to demonstrate the following minimum competencies:a) understanding of the automotive process approach for auditing, including risk-basedthinking;b) understanding of applicable customer-specific requirements;c) understanding of applicable ISO 9001 and IATF 16949 requirements related to the scope ofthe audit;d) understanding of applicable core tool requirements related to the scope of the audit;e) understanding how to plan, conduct, report, and close out audit findings.The organization shall have internal auditors who are qualified to audit the requirements of thisTechnical Specification (see 6.2.2.2).Enhanced re
of ISO/TS 16949, IATF 16949 greatly expands the intent of product safety in Section 4.4.1.2. This is a new section with new and enhanced requirements that address current and emerging issues the automotive