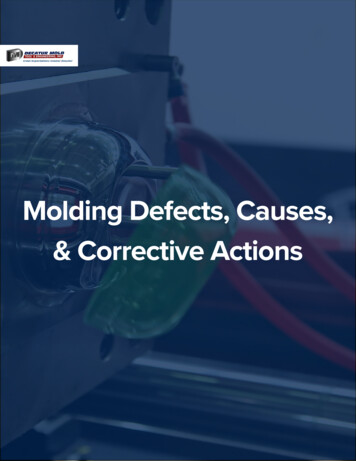
Transcription
Rapid Prototyping 101Possible iveActionBlister, BlisteringUnintended raised orlayered area on thesurface of the partTool is running toohot or the heater ismalfunctioningTest tool heat andeliminate any externalsources contributing toheat on the tool, checkcooling in area of toolDescriptionDefectCausesCorrectiveActionBurn Marks,Gas Burn, Air BurnBlack or browndiscoloration onmaterial farthestfrom the mold gateInjection speed ofmaterial is too highand/or the tool venting is not sufficientSlow down the injectionspeed and/or testventing of tool toachieve proper shotspeed and temperaturePossible iveActionColor Streaks,StreakingUndesired colorchange in areasof the materialDesired colorant isn’tmixing properly withgranules or has runlow, revealing naturalcolorCheck proper mixturerate for colorant andensure colorant level insystem feed is correctPossible MoldingDefectsMolding Defects, Causes,& Corrective Actions
Molding Defects, Causes, & Corrective ActionsPossible iveActionBlister, BlisteringUnintended raised orlayered area on thesurface of the partTool is running toohot or the heater ismalfunctioningTest tool heat andeliminate any externalsources contributing toheat on the tool, checkcooling in area of toolPossible iveActionBurn Marks,Gas Burn, Air BurnBlack or browndiscoloration onmaterial farthestfrom the mold gateInjection speed ofmaterial is too highand/or the tool venting is not sufficientSlow down the injectionspeed and/or testventing of tool toachieve proper shotspeed and temperaturePossible iveActionColor Streaks,StreakingUndesired colorchange in areasof the materialDesired colorant isn’tmixing properly withgranules or has runlow, revealing naturalcolorCheck proper mixturerate for colorant andensure colorant level insystem feed is correct3330 N. State Road 7, North Vernon, IN 47265Telephone: (812) 346-5188 Fax: (812) 346-7357 2Email: websales@decaturmold.com
Molding Defects, Causes, & Corrective ActionsPossible iveActionDelaminationPart walls are not solidand form layers ofmaterial instead of onesolid pieceDangerous situationthat creates parts withvery little strength,usually due to materialcontaminationCheck material stock forcontamination, try withnew material sourcePossible iveActionFlash, BurrsMaterial flows outsideof the mold cavityInsufficient clampingforce, debris on toolmating surfaces, ortool damageInspect tool for damage,clean mating surfacesof molds, and ensureproper clamping forceon the moldPossible iveActionEmbedded Contaminates, EmbeddedParticulatesUndesired colorchange in areasof the materialDesired colorant isn’tmixing properly withgranules or has runlow, revealing naturalcolorClean the tool surfaceand cavity, inspect thebarrel/hopper/feedersystem for contaminants,check shear heat3330 N. State Road 7, North Vernon, IN 47265Telephone: (812) 346-5188 Fax: (812) 346-7357 3Email: websales@decaturmold.com
Molding Defects, Causes, & Corrective ActionsPossible iveActionFlow Marks,Flow LinesMaterial flow createsmultiple visible linesand patterns onfinished partInjection speed ofmaterial is too slowand cooling tooquicklyIncrease injectionspeed of materialPossible iveActionJettingTurbulent flowof material fromgate causes partdeformationInjection speed istoo high, poor overall tool design, poorplacement of gateor runnerCheck material injectionspeed, review designof toolPossible iveActionPolymer DegradationMaterial compositionfailure in tensilestrength, color, shape,etc.Exposure of granulesto excessive light,heat, water, orchemicalsDiscard poor material,check storage andfeeder system forcontaminant issuesDEGRADATION3330 N. State Road 7, North Vernon, IN 47265Telephone: (812) 346-5188 Fax: (812) 346-7357 4Email: websales@decaturmold.com
Molding Defects, Causes, & Corrective ActionsPossible iveActionSink MarksDepression created inthicker material zonesCooling time is too short,holding time post-injectionis too short, or pressureduring holding is too lowTest cooling and holdingtimes post-molding,review proper pressureduring moldingPossible iveActionShort Shot, Non-FillMold, Short MoldIncompletemolded partNot enough material entering the mold, injectionspeed of material is tooslow, or tool pressureis too low to dispersematerial correctlyIncrease injectionspeed of material andtest pressure on partduring moldingPossible iveActionSplay Marks, SplashMark, Silver StreaksPart has circular patternin material at gateHot gas generated bymoisture in the granulesdue to impropermaterial dryingprocedure or techniqueUse dry material, reviewmaterial drying process,review material storagefor contamination issues3330 N. State Road 7, North Vernon, IN 47265Telephone: (812) 346-5188 Fax: (812) 346-7357 5Email: websales@decaturmold.com
Molding Defects, Causes, & Corrective ActionsPossible iveActionStringiness, StringingMaterial from previousshot remains in mold,resulting in string-likeappearance in partMaterial temperatureat nozzle is too high,gate can’t completeshot cleanlyReduce materialtemperature at nozzlePossible iveActionVoidsFormation ofunintended air pocketin molded partHolding pressure isincorrect or mold is notcorrectly centered duringforming, causing differentwall thicknessesCorrect holding pressureduring material coolingPossible iveActionWeld Line, Knit Line,Meld LineLine on completedpart where materialflow meetsMaterial is moving tooslowly and cooling toorapidly, forming a linewhen it meetsIncrease temperature ofmaterial and/or mold toachieve appropriate flowSTRINGING3330 N. State Road 7, North Vernon, IN 47265Telephone: (812) 346-5188 Fax: (812) 346-7357 6Email: websales@decaturmold.com
Molding Defects, Causes, & Corrective ActionsPossible iveActionWarping, Twisting PartPart is deformed anddistortedMaterial is too hot and/or cooling time is tooshort, lack of coolingaround the toolCorrect coolingtime and materialtemperature,investigate coolingof toolWant to learn more?Download the Molding Tolerances Chart to findthe recommended tolerances for your mold toprevent part failure and performance loss.Want to learn more?Access the Injection Molding Glossary andexplore the different injection moldingterminology to inform your next project.* Defect photos courtesy of www.plastictroubleshooter.com3330 N. State Road 7, North Vernon, IN 47265Telephone: (812) 346-5188 Fax: (812) 346-7357 7Email: websales@decaturmold.com
Molding Defects, Causes, & Corrective ActionsPossible MoldingDefectsDefectDescriptionAbout Decatur MoldCorrectiveActionDefectCausesIn 1966, Decatur Mold was a five man shop with a 2,400 square foot facility, an excellent work ethic,and a desire to provide the best service and quality the industry had to offer. That commitment hasproven successful and now Decatur Mold has grown to a world class facility with 100 employeesand more than 87,000 sq ft.Test tool heat andTool is running tooBlister, BlisteringUnintended raised orDecatur Mold continues to incorporateof the art equipmenttechnologythroughouteliminate any externalhot or the andheaterislayered areastateon theour production process Technologyandsources contributingtomalfunctioningsurface of the partconcepts have changed since 1966, but our commitment to our customers, our quality,andourheat on the tool, checkemployees has not.cooling in area of toolDescriptionContact usDefectCausesCorrectiveActionBurn Marks,Gas Burn, Air BurnBlack or browndiscoloration onmaterial farthestfrom the mold gateInjection speed ofmaterial is too highand/or the tool venting is not sufficientSlow down the injectionspeed and/or testventing of tool toachieve proper shotspeed and temperaturePossible iveActionLearnMorePossibleMoldingDefectsCheck proper mixtureDesired colorant isn’trate for colorant andmixing properly withensure colorant level ingranules or has runsystem feed is correctlow, revealing naturalcolor3330 N. State Road 7, NorthVernon, IN 47265Telephone: (812) 346-5188 Fax: (812) 346-7357 Email: websales@decaturmold.comColor Streaks,StreakingUndesired colorchange in areasof the material3330 N. State Road 7, North Vernon, IN 47265Telephone: (812) 346-5188 Fax: (812) 346-7357 8Email: websales@decaturmold.com
Splay Marks, Splash Mark, Silver Streaks Part has circular pattern in material at gate Hot gas generated by moisture in the granules due to improper . Access the Injection Molding Glossary and explore the different injection molding terminology to inform your next project. Want to le