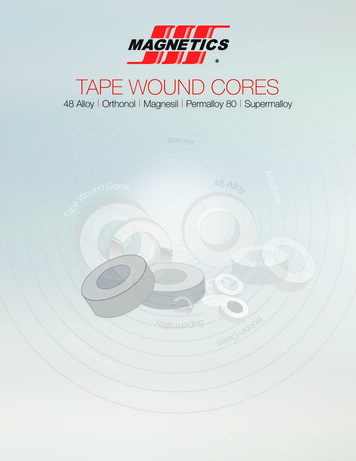
Transcription
TAPE WOUND CORES48 Alloy Orthonol Magnesil Permalloy 80 Supermalloy48 AlloyinbbBoresCond CoresouWilgnesMaTapeOrthonolSupermalloyPermalloy80
WEBSITESVisit Magnetics’ websites for a wealth of easy to access information on softmagnetic cores and materials All product specifications for Magnetics’ Ferrite Cores, Powder Cores and TapeWound Cores can be found quickly by using the menu driven product locator.Magnetics’ Digital Library contains all of the company’s technical bulletins, whitepapers and design manuals, which can be viewed on-screen or downloaded.HEADQUARTERSThe Software section of the website provides access to the Magnetics’ softwaredesign aids for designing Common Mode Filters, Current Transformers, Inductorsand MagAmps.Pittsburgh, PA 15238USA(p) NETICS INTERNATIONAL13/F 1-3 Chatham Road SouthTsim Sha TsuiKowloon, Hong Kong(p) 852.3102.9337 www.mag-inc.com.cn110 Delta Drive
CONTENTSHISTORY OF THESTRIP WOUND COREIndexMagnetics Pioneered Strip Wound Cores.HistoryMagnetics was established in 1949 when the commercial market for highpermeability magnetic materials was virtually non-existent and development in thisfield was just taking root. The new simplicity and reliability with which magneticcomponents could be used opened many doors in the field of electronics. Magneticswas quickly positioned as a leader in this field and has remained so ever since.The first tape cores were used in applications where they were superior to thefragile vacuum tubes. Tape wound core applications grew rapidly because thesenew magnetic components performed far better due to the inherent reliability androbustness of tape cores compared with vacuum tubes. They contained no parts towear or burn out; and the effects of shock, vibration and temperature were smallcompared to other components. Tape cores also made it possible to build circuits thatincluded electrical isolation or multiple-signal inputs whereas existing technologies atthe time could not.Today, Strip Wound Cores are used in magnetic amplifiers, reactors, regulators, staticmagnetic devices, current transformers, magnetometers, flux gates, oscillators, andinverters.ABOUT MAGNETICSMagnetics offers the confidence of over fifty yearsof expertise in the research, design, manufactureand support of high-quality magnetic materials andcomponents.A major supplier of the highest performance materials in the industry including:AmoFlux , XFlux , MPP, High Flux, Kool Mµ , power Ferrites, high permeabilityFerrites and Strip Wound Cores, Magnetics’ products set the standard for providingconsistent and reliable electrical properties for a comprehensive range of core materialsand geometries. Magnetics cores are the best choice for a variety of applicationsincluding switched mode power supplies for telecommunications equipment, servers,and computers; Uninterruptible Power Supplies for datacenters; and inverters forrenewable energy.Magnetics backs its products with unsurpassed technical expertise and support.Magnetics’ Sales Engineers offer the experience necessary to assist the designer fromthe initial design phase through prototype approval. Knowledgeable Sales Managersprovide dedicated account management. Skilled Customer Service Representativesare easily accessible to provide exceptional sales support. In addition, Magneticsoffers MyMagnetics, a self-service website, that provides 24-hour secure access toprice, inventory availability, tracking, account information, and online purchasing.This support, combined with a global presence via a worldwide distribution network,including a Hong Kong distribution center, makes Magnetics a superior supplier to theinternational electronics industry.History . . . . . . . . . . . . . . . . . . . . . . . . . . . . . 1Materials & ApplicationsMaterials & Applications . . . . . . . . . . . . . . . . 2-3Tape Wound CoresTape Wound Cores. . . . . . . . . . . . . . . . . . . . . 4Mag Amp Cores. . . . . . . . . . . . . . . . . . . . . . . 4Core Case Selection. . . . . . . . . . . . . . . . . . . . 5Testing Parameters. . . . . . . . . . . . . . . . . . . . . 6Typical Hysteresis Loops48 Alloy and Orthonol. . . . . . . . . . . . . . . . . . . 7Magnesil . . . . . . . . . . . . . . . . . . . . . . . . . . . . 8Square Permalloy 80 and Supermalloy . . . . . . 9Core Loss vs. Induction LevelCore Loss vs. Induction Level. . . . . . . . . . 10-12NotesIntentionally Left Blank . . . . . . . . . . . . . . . . . 13Tape Wound Core SizesTape Wound Core Sizes . . . . . . . . . . . . . . . 14-15Tape Core DesignTape Core Design. . . . . . . . . . . . . . . . . . . . . 16Bobbin CoresBobbin Cores . . . . . . . . . . . . . . . . . . . . . . . . 17Bobbin Core Sizes . . . . . . . . . . . . . . . . . . 18-19Bobbin Core Design . . . . . . . . . . . . . . . . . . . 20Bobbin Core Testing. . . . . . . . . . . . . . . . . . . 21Wire TableWire Table. . . . . . . . . . . . . . . . . . . . . . . . . . . 22Other Magnetics ProductsPowder Cores & Ferrites. . . . . . . . . . . . . . . . 23Custom Components & Prototyping . . . . . . . 24Warranty. . . . . . . . . . . . . . . . . . . . . . . . . . . . 241
MATERIALS AND APPLICATIONSMagnetics offers soft magnetic core materials for saturating devices and high sensitivity magnetic circuits for all applications. Thesematerials are especially selected and processed to meet exacting magnetic circuit requirements, and are manufactured to tight guaranteedtolerances according to IEEE test procedures or other common industry test methods.SQUARE ORTHONOL48 ALLOYThis material, a grain-oriented 50% nickel-iron alloy, is manufactured to meet exacting circuitrequirements for very high squareness and high core gain, and is usually used in saturablereactors, high gain magnetic amplifiers, bistable switching devices, and power inverterconverter applications. Other applications such as time delays, flux counters and transductorsdemanding extremely square hysteresis loops require selection of Square Orthonol.This material, a 50% nickel-iron alloy, has a round B-H loop and exhibits lower saturationflux density, squareness, coercive force, and core gain than the Orthonol types. It is usefulin devices requiring lower coercive force such as special transformers, saturable reactors, andproportioning magnetic amplifiers. AC core losses are lower than with Orthonol.(MATERIAL CODE A)SQUARE PERMALLOY 80(MATERIAL CODE D)(MATERIAL CODE H)MAGNESIL(MATERIAL CODE K)This material, a non-oriented 80% nickel-iron alloy, is manufactured to meet the highsquareness and high core gain requirements of magnetic preamplifiers and modulators. Itis especially useful in converters and inverters where high voltage at low power levels isrequired, but where circuit losses must be kept to a minimum. Square Permalloy 80 has asaturation flux density approximately one-half that of the Orthonol’s, but has coercive forcevalues one-fifth to one-seventh that of the 50% oriented nickel-iron alloys.This material, a grain-oriented 3% silicon-iron alloy, is processed and annealed to develop highsquareness and low core loss. It is usually used in high quality toroidal power transformers,current transformers and high power saturable reactors and magnetic amplifiers. It exhibitshigh saturation flux density with high squareness but has comparatively high coercive forceand core loss. With its high Curie temperature, it is quite useful in magnetic devices whichare to be exposed to temperatures between 200ºC (392ºF) and 500ºC (932ºF). At highertemperatures, only uncased cores should be used due to case temperature limitations.SUPERMALLOYROUND PERMALLOY 80This material is a specially processed 80% nickel-iron alloy. It is manufactured to developthe ultimate in high initial permeability and low losses. Initial permeability ranges from40,000 to 100,000 while the coercive force is about one-third that of Square Permalloy 80.Supermalloy is very useful in ultra sensitive transformers, especially pulse transformers, andultra sensitive magnetic amplifiers where low loss is mandatory.This material, a non-oriented 80% nickel-iron alloy, is processed to develop high initialpermeability and low coercive force. It has lower squareness and core gain than the squaretype, as these characteristics are sacrificed to produce the high initial permeability and lowcoercive force properties. Round Permalloy 80 is especially useful in designing highly sensitiveinput and inter-stage transformers where signals are extremely low and DC currents are notpresent. It is also useful in current transformers where losses must be kept to a minimumand high accuracy is a necessity. The initial permeability of this material is usually between20,000 and 50,000.(MATERIAL CODE F)2(MATERIAL CODE R)
MATERIALS AND APPLICATIONSTable 1TYPICAL PROPERTIES OFMAGNETIC ALLOYSPROPERTY3% Si-FeAlloys(K)50% Ni-FeAlloys(A, H)80% Ni-FeAlloys(R, D, F)% Iron975017% Nickel .5079% Silicon3 . . . .4Density (gms/cm )7.658.28.7Melting Point (ºC)1,4751,4251,425Curie Temperature (ºC)750500460Specific Heat (Cal./ºCgm)0.120.120.118Resistivity (μ Ω -cm)504557CTE (x10 /ºC)125.812.9Rockwell HardnessB-84B-90B-95% Molybdenum3-6Table 2MAGNETIC CHARACTERISTICS COMPARISON*MaterialCodeMaterialFlux DensityCoercive ForceBr/Bm(kG)(Teslas)14.2 - 15.81.42 - 1.58400 Hertz CCFR **OerstedsA/M0.88 up0.15 - 0.2511.9 - 19.9ASquare OrthonolDSquare Permalloy 806.6 - 8.20.66 - 0.820.80 up0.022 - 0.0441.75 - 3.50FSupermalloy6.5 - 8.20.65 - 0.820.40 - 0.700.004 - 0.0150.32 - 1.19H48 Alloy11.5 - 14.01.15 - 1.400.80 - 0.920.08 - 0.156.4 - 12.0KMagnesil15.0 - 18.01.5 - 1.80.85 up0.45 - 0.6535.8 - 51.7RRound Permalloy 806.6 - 8.20.66 - 0.820.45 - 0.800.008 - 0.0320.64 - 2.55* The values listed are typical of 0.002" thick materials of the types shown. For guaranteed characteristics on all thicknesses of alloys available, contact Magnetics Sales Engineering Department.** 400 Hertz CCFR Coercive Force is defined as the H1 reset characteristic described by the Constant Current Flux Reset Test Method in IEEE Std. #393.mag-inc.com3
MATERIALSTAPEWOUNDANDCORESAPPLICATIONSMAGNETICS Tape Wound Cores are made from high permeability magnetic strip alloys of nickel-iron (80% or 50% nickel), and silicon-iron.Tape Wound Cores are produced with ODs ranging from 0.438" to 3" in many sizes.Additional and custom box sizes are available.APPLICATIONSHOW TO ORDERMagnetics Tape Wound Cores are often key components of:Each core is coded by a part number that describes it in detail. A typical part number is: Aerospace Power Supplies Radar Installations Current Transformers015 1 0 2 9 2 AMaterial Code Jet Engine ControlsGauge CodeCore SizeCase/Coating Code01 - Single core or 02 - 03 - 04 matched setsBelow is a quick reference for available combinations of materials, cases, and *0.0005"(Gauge Code 5)0.001"(Gauge Code 1)0.002"(Gauge Code 2)0.004"(Gauge Code 4)ASquare Orthonol50, 51, 52XXXXDSquare Permalloy 8050, 51, 52XXXXFSupermalloy50, 51, 52XXXXHAlloy 4850, 51, 52XXXXKMagnesil50, 51, 52, 53, 54XXRRound Permalloy 80XX50, 51, 52*Cases/Coatings (Specifications on page 5)50 series – cores in non-metallic cases (phenolic or nylon depending on availability)51 series – cores in aluminum cases52 series – cores in aluminum cases with epoxy coating53 series – uncased/bare cores54 series – encapsulated cores (red epoxy)4Gauges (Thickness)XFive sizes of cores have been designed specifically to be used as magnetic amplifier cores.Mag Amp cores have been designed to serve as a regulator in the control loop or the secondaryoutputs of the switch-mode power supply.Magnetics website, www.mag-inc.com, provides a software program to assist the designerwith Mag-Amp design. Using the values of output current, secondary voltage, frequency, dutycycle and head room, the program software will select the appropriate core and calculate thelosses and temperature rise of the Mag Amp design.
LIC CASESUNCASED/BARE CORESFor superior electrical properties, improved wearing qualities, and high strength, non-metalliccases are widely used as protection for the core material against winding stresses andpressures. Both phenolic and nylon types meet a minimum voltage breakdown of 2000volts wire-to-wire. The glass-filled nylon types can withstand temperatures to 200ºC (392ºF)without softening, while the phenolic materials will withstand temperatures up to 125ºC(257ºF).Uncased cores offer a maximum window area. They also offer a slightly smaller package andlower cost where slight deterioration of properties after winding can be tolerated.ALUMINUM CASESENCAPSULATED (RED EPOXY) CORESAluminum core cases have great structural strength. A glass epoxy insert, to which thealuminum case is mechanically bonded, forms an airtight seal. These core cases will withstandtemperatures to 200ºC (392ºF), a critical factor in designing for extreme environmentalconditions.Encapsulated cores have a guaranteed minimum voltage breakdown of 1000 volts from coreto winding. The temperature rating of this finish is 125ºC (257ºF).(CASE/COATING CODE 50)(CASE/COATING CODE 51)(CASE/COATING CODE 53)Because of the extreme sensitivity of nickel-iron cores to winding stresses and pressures, suchcores are not available in an uncased state. Magnesil cores are not as susceptible to thesepressures and are available without cases.(CASE/COATING CODE 54)Only Magnesil cores are available in encapsulated form. This protection is a tough, hard epoxywhich adheres rigidly to the core, allowing the winder to wind directly over the core withoutprior taping. A smooth radius prevents wire insulation from damage.ALUMINUM CASEWITH GVB EPOXY PAINT(CASE/COATING CODE 52)This case is the same basic construction as the aluminum box, but in addition it has a thin,epoxy-type, protective coating surrounding the case. This finish adds no more than 0.015"to the OD, subtracts no more than 0.015" from the ID, nor adds more than 0.020" to theheight.GVB epoxy paint finish offers a guaranteed minimum voltage breakdown of 2000 volts wireto-wire. This coating will withstand temperatures as high as 200ºC (392ºF) and as low as-65ºC (-85ºF) with an operating life of greater than 20,000 hours.5
TESTING PARAMETERSTape Core Testing ParametersSQUARE B-H LOOP TAPE CORESSquare loop materials include oriented silicon iron, Magnesil, oriented 50% nickel, Orthonol, and 80% nickel, Permalloy, with a square loop anneal. These cores are tested by the Constant-CurrentFlux-Reset test method as defined by IEEE Standard #393 which measures 4 points on the BH loop as shown in Figure 1.Bmax – The saturation flux density is the flux density swing from the origin of the BH loop to the saturation in one direction.Bm - Br is the difference between the maximum flux density (Bm) and the residual flux density (Br). The lower this number, the lower the permeability in saturation and the lower the switching lossesfor a given core material.Br/Bm – Br residual flux density / Bm, (squareness) is calculated.H1 – The third parameter measured is the width of the hysteresis loop. The core is reset 1/3 of the way down the loop from positive saturation to negative saturation. The loop width at this point is theH1/3 point, given in Oersteds. The narrower the B/H loop, the lower will be the corresponding core losses.Delta H – The last parameter that this test measures is Delta H, or the additional amount of DC current or ampereturns required to set the core from BH1/3 down the loop to – BH2/3. H is read inOersteds and cores normally have a maximum Delta H limit.B (Kilogauss) 8BM - BRBR 4 BMBR H.08H1/3 2.04.04H(Oersteds).08-2H2/3-4-6-8Figure 1. Standard DC Reset Tester Measurements86-BM
Typical Hysteresis Loops for 48 Alloy and OronotholMATERIALSAND APPLICATIONSTYPICAL HYSTERESISLOOPSTypical Hysteresis Loops for 48 Alloy and OrthonolB (Kilogauss) 1.6 16Orthonol 1.4 1.2 1248 Alloy 1.0 .8 8 .6 .4 4 .2B (Tesla)H-.6-.4-.2 .2 .4 -70-60-50-40-30-20-100H (A/m) 10 20 30 40 50 60 7079
Typical Hysteresis Loops for Magnesil and SupermendurTYPICAL HYSTERESIS LOOPSTypical Hysteresis Loop for Magnesil(Kilogauss) 2.0 1.6B 20 16Magnesil 12 .8 8 .4 4B (Tesla) 1.2H0-1.6-1.2-.8-.4 .4 .8 1.2 120-100-80-60-40-200H (A/m) 20 40 60 80 100 120 140
Typical Hysteresis Loops for Sq Permalloy 80 & SupermalloyMATERIALSAND APPLICATIONSTYPICAL HYSTERESISLOOPSTypical Hysteresis Loops for Square Permalloy 80 and SupermalloyB (Kilogauss) 8 8Square Permalloy 80Supermalloy 6 6 .4 4 .2 2B (Tesla)H-.16-.12-.08-.04 .04-.2-2-.4-4-6-6-8-8-14-12-10-8-6-4-20H (A/m) 2 4 .08 6 8 .12 .16(Oersteds) 10 12 149
CORE LOSS vs. INDUCTION LEVEL2 mil Square Orthonol (code 2A)2 mil 48 Alloy (code 02.2.01.11/2 mil Square Orthonol (code 00020001000900800700600500400300200100Flux Density 50403060KHz60100Core Loss (Watts/Pound)600Flux Density (Gauss)400H10008001001K1 mil Square Orthonol (code 0700600500400300Flux Density 0020001000900800700600500400300200100Flux Density z.386K.41000Core Loss (Watts/Pound)Core Loss (Watts/Pound).610Core Loss (Watts/Pound).8
COREMATERIALSLOSS vs.ANDINDUCTIONAPPLICATIONSLEVEL2 mil Square Permalloy 80 (code 2D)1 mil Square Permalloy 80 (code x Density 3z43.6KH615Core Loss (Watts/Pound)80100KHz50KHzzKHz2 mil Supermalloy (code 2F)10Core Loss (Watts/Pound)20K10K9000800070006000500040001/2 mil Square Permalloy 80 (code 5D)Flux Density (Gauss)3000Flux Density 500400300200100Flux Density 350.4.36KHz.6100Core Loss (Watts/Pound)615Core Loss (Watts/Pound)811
CORE LOSS vs. INDUCTION LEVEL1 mil Supermalloy (code 1F)1/2 mil Supermalloy (code 06060404030302020101088Core Loss Core Loss (Watts/Pound)20K10K9000800070006000500040002 mil Magnesil (code 2K)100.23000Flux Density (Gauss)4 mil Magnesil (code 300200100Flux Density 0436KHz6100Core Loss (Watts/Pound)10080Core Loss ux Density 50040030020010012Flux Density (Gauss)
notes13
TAPE WOUND CORE SIZESTape Wound Core Sizes (By Effective Core Area)CORE PARTNUMBER5040250107503565015350B12 Mag Amp501545005650B11 Mag Amp50057501555000050B
CONTENTS 1 HISTORY OF THE STRIP WOUND CORE Magnetics Pioneered Strip Wound Cores. Magnetics wa