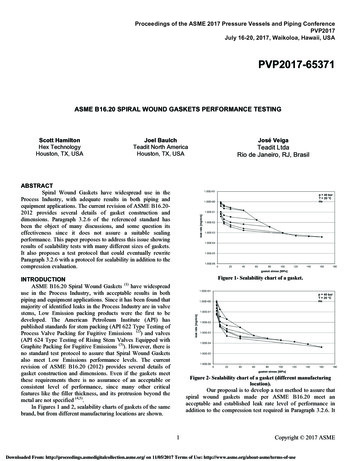
Transcription
Proceedings of the ASME 2017 Pressure Vessels and Piping ConferencePVP2017July 16-20, 2017, Waikoloa, Hawaii, USAPVP2017-65371ASME B16.20 SPIRAL WOUND GASKETS PERFORMANCE TESTINGScott HamiltonHex TechnologyHouston, TX, USAJoel BaulchTeadit North AmericaHouston, TX, USAJosé VeigaTeadit LtdaRio de Janeiro, RJ, BrasilABSTRACTSpiral Wound Gaskets have widespread use in theProcess Industry, with adequate results in both piping andequipment applications. The current revision of ASME B16.202012 provides several details of gasket construction anddimensions. Paragraph 3.2.6 of the referenced standard hasbeen the object of many discussions, and some question itseffectiveness since it does not assure a suitable sealingperformance. This paper proposes to address this issue showingresults of sealability tests with many different sizes of gaskets.It also proposes a test protocol that could eventually rewriteParagraph 3.2.6 with a protocol for sealability in addition to thecompression evaluation.Figure 1- Sealability chart of a gasket.INTRODUCTIONASME B16.20 Spiral Wound Gaskets (1) have widespreaduse in the Process Industry, with acceptable results in bothpiping and equipment applications. Since it has been found thatmajority of identified leaks in the Process Industry are in valvestems, Low Emission packing products were the first to bedeveloped. The American Petroleum Institute (API) haspublished standards for stem packing (API 622 Type Testing ofProcess Valve Packing for Fugitive Emissions (2)) and valves(API 624 Type Testing of Rising Stem Valves Equipped withGraphite Packing for Fugitive Emissions (3)). However, there isno standard test protocol to assure that Spiral Wound Gasketsalso meet Low Emissions performance levels. The currentrevision of ASME B16.20 (2012) provides several details ofgasket construction and dimensions. Even if the gaskets meetthese requirements there is no assurance of an acceptable orconsistent level of performance, since many other criticalfeatures like the filler thickness, and its protrusion beyond themetal are not specified (4,5).In Figures 1 and 2, sealability charts of gaskets of the samebrand, but from different manufacturing locations are shown.Figure 2- Sealability chart of a gasket (different manufacturinglocation).Our proposal is to develop a test method to assure thatspiral wound gaskets made per ASME B16.20 meet anacceptable and established leak rate level of performance inaddition to the compression test required in Paragraph 3.2.6. It1Copyright 2017 ASMEDownloaded From: http://proceedings.asmedigitalcollection.asme.org/ on 11/05/2017 Terms of Use: http://www.asme.org/about-asme/terms-of-use
considers the bolting capability of each flange class, with a lowYield Stress bolt per ASTM series. The test should be easy toimplement without any special tooling, and using equipmentavailable in the market.or𝑳𝑹𝒎 𝟕. 𝟔𝟕𝐄 𝟏𝟎Table 1 shows values for each NPS/Pressure Classcombination for ASME B16.20, adjusted for gasket outsidediameter, given that the leak rate per the API 624 level of 100ppmV is equivalent to 0.0137 mg/(s.m).NOMENCLATUREbar: pressure, 1 bar 14.50377 psiin: inchkg: kilogramksi: pressure, 1ksi 1000 psilb: pound weightLRm: mass leak ratem: metermg: milligramMpa: pressure, mega PascalNPS: nominal pipe sizep: pressureppmV: parts per million by volumepsi: pressure in pounds per square inchs: secondGOD: gasket winding outside diameterMW: gas molecular weightT: test temperature in KelvinTVA 2020 from Thermo Fisher Scientific Inc Flow rate 1liter pe rminutel: litermg: milligrams: secondm: meterin: inchR: universal gas constant in l.bar/K.molTable 1 – Gasket leak rate of 100ppmV.Concentration in ppmV per API 624 Level1/23/4150123154300123154Pressure 1851851 1/42352352352352351 1/222 8981310221231NPS 7968981310221231145315761798204422412659It is possible then to estimate the gasket emission levelin a given period of time, and determine whether the gasket isaccepted or rejected, in a quality control type operation whichcan be conducted typically at the manufacturer’s location. Thecalculation is performed multiplying the gasket perimeter bythe leak rate of 0.0137 mg/(s.m), and the time in seconds beingconsidered. It is further possible to even consider standardizedvalues characteristic to a group of gaskets.LEAKAGE CRITERIAThe API 624 standard has established the definition forLow Leak valves as 100 ppm, using Methane (CH4) as mediaand a Volatile Organic Compound Analyzer such us the typeTVA 2020 from Thermo Fisher Scientific Inc. (8). There is nodefinition for flanges. We propose to keep the 100-ppmVconcentration of Methane per EPA Method 21 (9) and API 622stem diameter as reference for the calculation of leakage.However, due to the range of the gasket outside diameters, it isnot feasible to have a single value (100 ppmV) as for valvestems. Our proposal is to convert it to a leak rate per millimeter(or inch) of a gasket outside diameter as shown in Annex A.Table 2 shows the leak in kilograms per gasket for aperiod of one year considering the API 624 level.If gaskets received in a plant meet the proposedcriteria, the total product loss due to emissions can be estimatedmultiplying the number of gaskets in the plant per the value inTable 2. If a tighter sealability level is established, the productloss savings due to this change can also be estimatedConsidering that the diameter of the test device stem perAPI 622 is 1 inch, we can establish the leak rate per millimeter(or inch) of stem perimeter. Per Annex A, the values forcalculating a gasket maximum leak rate equivalent to 100ppmV are as follows (metric and imperial values respectively):𝑳𝑹𝒎 𝟎. 𝒎2Copyright 2017 ASMEDownloaded From: http://proceedings.asmedigitalcollection.asme.org/ on 11/05/2017 Terms of Use: http://www.asme.org/about-asme/terms-of-use
Class 150: 5000 psiClass 300 and 400: 8000 psiClass 600 and above: 10000 psiTable 2 – Gasket leak in kilograms per yearLeak per gasket size for API 624 Level (kg/year)Pressure 0,0433/40,0540,0540,0540,0540,054Only one flange does not meet the proposed criteria:NPS 8 in – Class 150. It is well known that it is considered a“bad actor”.Table 3- Gasket stresses for 30 ksi bolt stress.40060090010,0650,0650,0650,0650,0651 1/40,0820,0820,0820,0820,0821 1/20,0950,0950,0950,0950,095Gasket Seating for 30 ksi Bolt Stress (psi)NPS(in.)Pressure Class20,1170,1170,1170,1170,117150300150025002 2410,2410,2411 ,2840,2840,2841 10,4310,4310,4310,4310,4312 223509245195SEATING STRESS CRITERIATo establish the minimum seating stress for eachflange size and pressure class, consider that all gaskets meetASME B16.20 dimensions.Current gasket research has shown that the ASMEB16.20 design requirement of Paragraph 3.2.6 to assemblegaskets to a constant bolt stress is out of step with the ASME –PCC-1-2013 Guidelines for Pressure Boundary Bolted FlangeJoint Assembly (10) technology because, per Appendix O, PCC1-2013 targets gasket stress instead of bolt stress.To establish the minimum gasket seating stressconsidering the value of 30 ksi for the bolt stress, we havecalculated the gasket stresses shown in Table 3. This value iscalculated the Yield Strength of ASTM A193 B8 Class 1Stainless Steel bolt, a weak material in the ASTM series.The chosen gasket seating stresses are intentionallyselected on the “low end” because, ideally, we want a gasket tohold a seal at a very low stress, to account for relaxation, flangestiffness, assembly inconsistencies, etc.400600900It is a common practice in the industry to use an “idealseating stress”. With this in consideration we propose a test at15 ksi for Class 150 and at 25 ksi for higher classes and anadditional test at an intermediate gasket stress so we can have achart of sealability versus gasket stress. The sealability tests arethen performed at the following gasket stresses:-For Class 150: 5000, 10000 and 15000 psi.For Class 300 and 400: 8000, 15000 and 25000 psiFor Class 600 and higher: 10000, 15000 and 25000 psiTo assure that the raised portion of the flange does not hitthe guide ring, the winding compressed thickness is recorded ateach seating stress, and compared with the guide ring thickness.To assure that there is no “guide ring seal”, the winding shall bedetermined to be thicker than the guide ring.Analyzing Table 3, we can propose the followingminimum seating stress for each pressure class:3Copyright 2017 ASMEDownloaded From: http://proceedings.asmedigitalcollection.asme.org/ on 11/05/2017 Terms of Use: http://www.asme.org/about-asme/terms-of-use
TEST MEDIA AND PRESSUREThe API 622/624 standards specify Methane (CH4) astest media and a pressure of 41.4 bar (600 psi) as the maximumtest pressure for valves. This value can be used for all flangeClasses 300 and higher. For Class 150, the maximum pressureat room temperature per ASME B16.5 is 19.6 bar (285 psi).For reference, EN 13555 specifies 40 bar for all sizes.-Our proposal is then:For Class 150: 20 bar (290 psi)For Class 300 and higher: 40 bar (580 psi)Figure 3 – AMTEC Temes fl.ai1.Testing Flexible Graphite gaskets with CH4 has to bedone with proper care for safety reasons. In addition, if thegasket is not seated properly or the leak rate is too high, it takesa long time to “decontaminate” the gasket (11,12,13,14). This mayshow as a high leak rate however, it is just the FlexibleGraphite impregnated by the CH4. The EN 13555 protocol ofincreasing and reducing the gasket stress to evaluate the leakrate at each step may not be feasible with CH4 due to thecontamination issue. For this reason our proposal does notaddress the gasket characteristics determination for ASMEBoiler and Pressure Vessel Code, Section VIII (15) calculations.TEST PROTOCOLSThe EN 13555 standard is well known and will not bedescribed in this paper.The Methane test protocol determined duringpreliminary evaluations that is necessary to seal the gasket asclose as possible to the winding outside diameter. Otherwisethe CH4 will concentrate and reach the VOC inlet probe inbursts. Tests were also performed in standard ASME B16.5flanges and the same effect was found; the concentration inppmV was not stable, but oscillating, making it impossible toevaluate the actual gasket leak.GASKET SAMPLESAll gaskets samples used for the development of thistest protocol included:- Dimensions and other features like welding and wrapsper ASME B16.20-2012- Winding metal: Stainless Steel type AISI 304- Filler: Flexible Graphite- Outer Ring: Carbon Steel- Inner Ring: Stainless Steel type AISI 304TEST RIGSTwo test rigs were used in this research. An AMTECTemes fl.ai1 Multifunctional Test Rig (16) (Figure 3) equippedwith an Oerlikon Phoenix L300i Mass Spectrometer (17) for theHelium EN 13555 leak tests. And, a 50-ton Hydraulic Presswith a Volatile Organic Compound Analyzer TVA 2020 (13) asshown in Figure 4 for the Methane leak tests.Figure 4 -50-ton Hydraulic Press with a Volatile OrganicCompound Analyzer TVA 2020.A simple fix was developed sealing the gap betweenplatens with a 5mm thick rubber O-ring fitted around the GuideRing OD. The O-ring has two locations of double “V cuts”, 180degrees apart, one for the VOC probe and the other for the airinlet. The double “V cut” is one cut facing up, the other cutfacing down. This way, any leak is directed to the probe of themeasuring instrument. The Methane inlet is through a hole inthe center of one of the platens. This set up is shown in Figures5 through 7.4Copyright 2017 ASMEDownloaded From: http://proceedings.asmedigitalcollection.asme.org/ on 11/05/2017 Terms of Use: http://www.asme.org/about-asme/terms-of-use
11 – Change the force on press to the second step in Table 4and repeat steps 7,8, 9 and 10.11 – Change the force on press to the third step in Table 4 andrepeat steps 7,8, 9 and 10.12. – Finish test, remove the gasket and record the winding fullthickness.13 – Report the ppmV concentration and the gap betweenplatens for each step, the winding initial and final thickness andthe inner and guide ring thickness.Figure 5 – Platens schematics.Table 6 - Gasket seating stress steps.MediaPressurePressureClassFigure 6 – Double “V cuts” O-ring.20 bar150#300# and400#40 bar600# 00215000325000110000215000325000TEST VALIDATIONFigure 7- Test Schematics.To validate the proposed procedure, several tests wereperformed with both Helium and Methane. The Helium testswere performed following the EN 13555 protocol. Since this isa well-known and proven test procedure, a correlation with itwould be desirable. Gaskets acquired in the market fromseveral manufac
ASME B16.20 Spiral Wound Gaskets (1)have widespread use in the Process Industry, with acceptable results in both piping and equipment applications. Since it has been found that majority of identified leaks in the Process Industry are in valve stems, Low Emission packing products were the first to be developed.