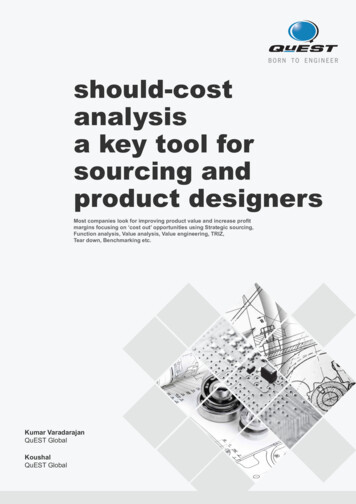
Transcription
should-costanalysisa key tool forsourcing andproduct designersMost companies look for improving product value and increase profitmargins focusing on ‘cost out’ opportunities using Strategic sourcing,Function analysis, Value analysis, Value engineering, TRIZ,Tear down, Benchmarking etc.Kumar VaradarajanQuEST GlobalKoushalQuEST Global
contents1.0Abstract032.0Background033.0Should-Cost Overview044.0Process of Should-Cost Analysis04-055.0What would it cost to make my Design Concepts?05-066.0A Simple Cost Model of Machined Part067.0Significance of Should-Cost Analysis078.0Importance of Should-Cost in NPD9.0Concurrent Costing-An Integration of ShouldCosting and Concurrent r Profile13About QuEST Global07-0809-1010 2013, QuEST Global Services
White Paper Should-Cost AnalysisAbstractMost companies look for improving product value andincrease profit margins focusing on ‘cost out’opportunities using Strategic sourcing, Functionanalysis, Value analysis, Value engineering, TRIZ, Teardown, Benchmarking etc. These have become vitalelements of any discipline to analyse and reduce cost ascustomers are forced to develop products with stringentcost targets. In the mid 20th century, companies followedtraditional cost analysis to estimate the product cost.Sometimes, this fails to supply the scope and detailsrequired to evaluate a supplier's cost proposal credibly.Today, we have significantly progressed in terms oftechnology, that we have many software to carry out astructured way of cost modeling to estimate the productcost. Also, there are opportunities to identify andoptimise the uneconomical and unproductive costs. Inthis context, Should-cost analysis is an approach thatdetermines what the product or a system ought to cost,assuming applicable economic and physical attributes inline with the requirements. The objective of Should-costanalysis is to provide the sourcing team with acceptableand justifiable information for judicious price negotiation.Apart from this, designers are benefited in costestimation of the product cost at the early stage ofproduct development to achieve their targeted costs.Should-cost analysis assists the designer to optimise theproduct and process design that drives the cost. Thispaper includes the process of Should Cost analysis, itssignificance, its importance in New ProductDevelopment (NPD) and concurrent costing.BackgroundMost companies use strategic sourcing to reduce cost ofgoods sold, reduce spend drivers, improve processperformance, identify unproductive services andpromote healthy competition to have an edge in theirprice negotiations. Sourcing is done from low costcountries such as, China, India, Brazil, Russia, Mexicoetc. and the objective behind this strategy is to obtain thekey cost differences between various geographies anddevelop strategic sourcing competence. This approachworks well provided the business volumes arepotentially high. Obviously, there are engineeringproducts and systems that are more complex andpurchased in very low volumes. In such scenario,sourcing team has a challenge in getting competitivebids from suppliers as there could be very few to cater tosuch specific process and engineering services. Tomake a choice or trade off on the vendor with minimalparameters to assess their estimate would be tough.3In order to get reasonable quotes, the sourcing team isforced to grapple with unique and sole suppliers. Inspecific businesses like, Oil and Gas, Energy,Aerospace, these categories of spends for uniqueproducts and processes could be significant. Mostbuyers look for a reasonable decrease in outlay toachieve their set targets, but what the product shouldactually cost is not envisaged. Buyers are usually notfamiliar with the specific manufacturing processesfollowed by suppliers and also not aware of the processoptimisation done over the period to bring down theproduct cost. One solution to this problem is a techniqueknown as Should-cost analysis that allows the companyto have a better insight in to the cost drivers of theirproducts and provide valuable information to thesourcing team to facilitate judicious price negotiations. 2013, QuEST Global Services
White Paper Should-Cost AnalysisShould-Cost OverviewShould-Cost modeling is the process of determining,what a product must cost based upon the drivers likecomponent’s raw material costs, manufacturing costs,process overheads, and an added rational profitpercentage. Many a times, the engineering teams do notevaluate the cost of the product themselves and instead,rely on the sourcing for the cost information. Thesourcing team negotiates with their suppliers with limitedinformation provided by the designers and without theshould-cost models. If the cost model is in place, it wouldbe helpful for the engineering team to evaluate thevarious design concepts focusing on the target costduring the development phase and also accomplisheffective sourcing.Integration of strategic sourcing along with engineeringteam in making the cost model will result in an effectiveshould-cost model, which enables the sourcing team tohave a better leverage while negotiating with theirsuppliers.Should-cost modeling is quite essential for the Supplychain and Engineering team during the new productdevelopment stage. Moreover, it also helps to analyseand optimise product cost, to establish and sustain in themarket.Significant changes in demand, lack of resources andinflation have resulted in an increase in the productioncost and procurement cost. This has, in turn, ledcompanies to analyse cost accurately and vigilantlyevaluate the supplier cost proposals.Should-costanalysis will help in giving the big picture on the overallcost breakup in terms of material cost, process cost,setup, rejects, labor, overheads, packing and transit.From the results, one can identify the potential cost-outopportunities and revisit on minimising the costs.Process of Should-Cost AnalysisShould cost analysis: There are certain prerequisites forShould-cost analysis and based on these availableinformation, one can make an accurate estimation. Tostart with, one should have a good understanding of theproduct and the processes required to produce the partor assembly from the raw material stage, adhering toquality and compliance requirements. The level ofaccuracy depends on the skill and knowledge of theindividual who builds the cost model. This activity is quitechallenging for a buyer but relatively easier for anInput Study Drawings 3D Models Engineeringspecifications Testing andQualification Assemblyprocedures4Processprerequisite Analyzeprimary /Secondaryprocess Processplanning AnalyzeCompliancerequirements Material cost IdentifyMachineriesandEquipments Manufacturinglocations Process,Labor,Overheadscost Annul usageengineer as he is the brain behind the product’s design.However, engineers may not have the detailed costingknowledge of various secondary processes like heattreatment, plating, welding, which probably areoutsourced. This is the area where Should-costmodeling software will help designers/engineers toestimate the complete cost of the product with end toend costing. The chart below depicts the Should-costapproach, which has to be followed to make an accurateestimation of the product cost.Cost ModelingOutputsReport out Annualvolumes /Batch quantity/ Unit ofmeasurement Define Partgeometry Select Process/ Material Defaultselection ofprocess andmodeling Manualselection ofprocess andmodeling Define costparameterswith respect togeographicallocations Cost drivermodels Costparameterswith respect tobreak down ofprocess Process timewith respect toindividualprocess Cost graphrepresentingkey costdrivers Break evencost withrespect tovolumes Excel basedcost summary Break up ofProcess,Material,Setup, Rejects,and processtime Piece part costand NRI costestimation andamortizationcost 2013, QuEST Global Services
White Paper Should-Cost AnalysisShould-cost analysis works on feature based costing. Towell describe a product, it is built based on a number offeatures, each of which has a particular function toperform. Based on the number of features in the part, theprocessing time and costs are estimated. Each productor part is characterised by a set of physical attributes:the materials it can be made from, the viablemanufacturing process, precision, complexity, size andgeometry.Economic attributes also contribute to the product’s costwhich is reflected in the cost model. It is essential tohave the information on the annual volumes and batchsize which in turn, help with “make or buy” decisionsbased on the bill of materials. These attributes andfeatures are quite essential to build the cost model asshown below. Designer can make a trade-off based onthe cost behavior of individual features and optimise thedesign based on the feature’s criticality.Today, there are a number of cost-modeling toolsavailable for the customers to study and reduce cal and statistical tools used to analyse thecost behavior of the part or assembly. The software’slibrary, which is built based on cutting-edgetechnologies, processes, machineries, labor ratesaccording to distinct geographies, setup rates,overheads and time are tagged to the variables relatedto product and process characteristics. The compilationof the mathematical model in a set algorithm will result inthe observation of process variables that significantlycontribute in driving the cost of the product. Thesesoftwares also enable the user to customise uniquematerials and process parameters that are not includedin the library. The resulting feature based cost model canbe used by the end user (buyer, engineer) to infer andmeasure the amount of uneconomical and inefficientprocesses followed.The product designer can probably study the costbehavior of various design iterations. To be moreprecise, if the user wishes to choose an alternatematerial or process, the cost model can be duplicatedand framed according to their area of interest for designchange. The statistical graphs enable the user tocompare and analyse the cost behavior for the variousiterations in terms of process, material, overheads, andproduction volumes.What would it cost to make my Design ngSheet metalMaterialPPAAluminumSS 304SS 304Annual Volume1500150015001500Batch Size200200200200 2013, QuEST Global Services
White Paper Should-Cost Analysisbuyer wishes to study and compare the cost model andmanufacturing process plan of the supplier, could inferthem and identify the potential tweaks and modifyaccordingly. Should cost gives a detailed breakdown ofcost and time study of the various manufacturingoperations carried out that contribute to the part’s cost.This will help the sourcing team to make judiciousnegotiations.A Simple Cost Model of Machined Part6 2013, QuEST Global Services
White Paper Should-Cost AnalysisSignificance of Should-Cost Analysis Should-cost analysis provides a better insight for thesourcing team to identify the supplier’s profit marginsand grab the purchasing power from the supplier It helps them in identifying the key cost drivers of theproduct and helps in “make or buy” decisions Infer price comparisons of the part, assembly, ifoutsourced to different geographical locations For any strategic sourcing, should-cost analysis wouldbe an ideal tool for making profitable negotiations It also aids new product development team toevaluate the product cost in the early stage ofdevelopment. Engineers will have a better insight ofcost implication on the design and revisit on designto- cost Analyse viable alternate material or process to studythe cost behavior and make necessary tradeoff Identify the apt materials and processes in the earlystages and avoid design iterations in the later stage Should-cost results will help in understanding thesupplier quotient and their strengthsImportance of Should-Cost in NPDNew product development is the key driver of businesssustenance. Once a product is launched in to themarket, it has its own rivals to kill it. However it will onlysustain based on the cost and technological impact thatdifferentiates itself from the rest. In order to establish atargeted cost for the product, cost management is quiteessential and has to be initiated from the design stage inthe product life cycle to achieve the target cost. Mostcompanies neglect the cost impact in the developmentof their new products and accept their returns oninvestment at small margins without knowing the bigpicture. The lack of awareness brings bigger surprises inthe fag-end of development stage resulting in greatercost overrun than the estimated budget. This may lead tovarious tradeoffs on the design and in turn reduce theproduct’s quality. Such flaws may affect the product’ssuccess and lead to a catastrophic loss for theorganization as enormous time and cost is spent on thedesign research and product development.Target costing emphasizes on cost reduction at earlystages in product development and ensures that totalcosts are minimised for both the producer and thecustomer. Successful target costing analyses thecomplete life-cycle cost of the product. Usually, it isobserved in new product development that designersusually overdesign for functionality and high productreliability without considering cost implications. This7would result in sluggish growth in market. The majordrawback is that, the purchasing and manufacturingteams are not involved with the design team to do thefeasibility analysis and at the later stage, value analysisis done to bring down the product cost.In the early stages of product life cycle, the productioncost is very high, which are later optimised by findingalternate processes and materials. This process provesa lot more costly and laborious as it involves redesignand validation. However, this does n
Excel based cost summary Break up of Process, Material, Setup, Rejects, and process time . based on the bill of materials. These attributes and features are quite essential to build the cost model as shown below. Designer can make a trade-off based on the cost behavior of individual features and optimise the design based on the feature’s criticality. Today, there are a number of cost .