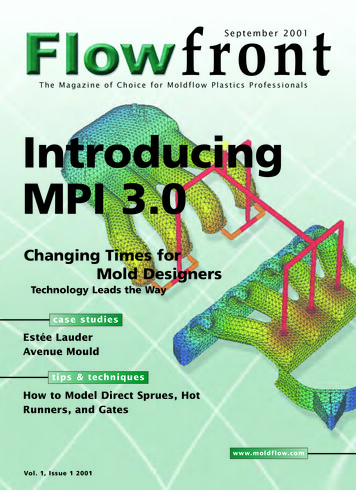
Transcription
frontSeptember 2001The Magazine of Choice for Moldflow Plastics ProfessionalsIntroducingMPI 3.0Changing Times forMold DesignersTechnology Leads the Waycase studiesEstée LauderAvenue Mouldtips & techniquesHow to Model Direct Sprues, HotRunners, and Gateswww.moldflow.comVol. 1, Issue 1 2001
contentsFEATURES5focus oncover story15Moldflow Manufacturing Solutions for the Automation, Controland Monitoring of the Injection Molding Process15 cover storyIntroducing MPI 3.0 - Moldflow Plastics Insight and C-MOLD2000 Work in SynergyCOLUMNS11 professional development 26 what’s newEnhancing Customer Education12real world successAvenue Moulds Wins TopHonors as Toolmaker of theYear22 the polymer pagesMoldflow Plastics Insight 3.0Thermoplastic MaterialsProperties Database23 learning curvesPlastics Engineering EducationExploring Moldflow PlasticsInsight 3.0 Finite-ElementMeshing CapabilitiesIntroducingMPI 3.0!28 design & moldingChanging Times for MoldDesigners - Technology Leadsthe Wayfocus on530 user reviewEstée Lauder Uses Moldflow PartAdviser to Design Sleek Shapesfor Cosmetic Linesat the University ofMassachusetts LowellDEPARTMENTS4 from the editor9 tips and techniques19 the executive view33 the analyst saysManufacturingSolutions forInjection MoldingFlow frontFor more information, contact us w.comEmail:flowfront@moldflow.comMail:430 Boston Post RoadWayland, MA 01778Editor:Laura CarrabineCopy Editor: Marcia SwanDesigner:Joanna KingHow to AdvertiseContact Marcia Swan at 607-257-4280, ext. 467for rates and availability, or go to our Web site atwww.moldflow.com and click on the FLOWfronticon, then click for advertisers. Here you candownload a PDF file that describes our insertionorder and rates. 2001 Moldflow Corporation. All rights reserved. Flowfront is a bi-yearly publication of Moldflow Corporation
Bob “The Conqueror” Carson: Assembly machineryHarry “Hercules” Adams: Ski equipmentSteve “Invincible” Thomas: Medical instrumentsNew SolidWorks Office.More than a great value, it gives youquite a powerful feeling.You can do it all. Now everything you need to beef-up your productivity and add moremuscle to your presentations is in your hands. You are the product designer with all the tools: SolidWorks 3D CAD software PhotoWorks SolidWorks Animator 3D Instant Website SolidWorks Toolbox FeatureWorks SolidWorks Utilities. You have all the power in one veryaffordable package. SolidWorks Office, the complete 3D CAD solution. Find out more, big guy.Log on to: www.solidworks.com/flowpower or call 1-800-693-9000 ext. 3556. 2001 SolidWorks Corporation. SolidWorks and the SolidWorks logo are registered trademarks and PhotoWorks is a trademark of SolidWorks Corporation.FeatureWorks is a registered trademark of Geometric Software Solutions Co. Limited. All other company and product names are trademarks of their respective owners.
from the editorWelcomeDear Readers,Welcome to the first edition of the new format of Flowfront. Flowfront begins its life cycle as a semi-annualpublication with an issue targeted for spring and fall of each year. Each issue contains a myriad of compellingarticles that are focused on technology, academic and R&D breakthroughs, and industry trends and issues. Thisnew magazine format allows us to get more in depth on each topic we cover.Flowfront, unlike other publications that briefly touch on issues important to injection molding professionals, will explore these topicsmore deeply and help our readers find solutions to the problems they face every day. For this to happen, we need contributions from ourreaders. We are always on the lookout for interesting application stories, topics of industry interest, and articles discussing technology andautomation. If you feel that you have a topic or story to contribute, we encourage you to contact us.Moldflow product line manager Dean Piepiora explains Moldflow's exciting new Synergy technology inside Moldflow Plastics Insight3.0. Synergy is a powerful new pre- and post-processor for model preparation and cleanup, as well as for viewing and manipulatinganalysis results. The technological breakthrough integrates the best features of Moldflow Plastics Insight (MPI) andC-MOLD 2000 (CM2K) products into a single, merged product family. Also in this issue, product line manager Peter Rucinski offersinsight to Moldflow's Manufacturing Solutions for automating, controlling, and monitoring injection-molding processes. He gives full,updated descriptions of Moldflow Plastics Xpert, Moldflow Shotscope, and Moldflow EZ Track manufacturing software solutions.Each edition of Flowfront will feature innovative commentary authored by Moldflow customers and partners, as well as Moldflowresources. In fact, each month guest author and Gartner Group research director Marc Halpern, Ph.D., will offer his overviews ofCAD/CAM/CAE, plastics engineering, e-commerce, and the supply chain. In this issue, he addresses the need for manufacturers andsuppliers to develop collaborative product commerce (CPC) networks.As you will see in this issue, Moldflow customers Avenue Mould (Sligo, Ireland) and Estée Lauder (New York, NY) offer insights as tohow these world class manufacturers are using Moldflow products to reduce product development lead times, enhance product quality,and win industry awards! Each Flowfront edition will contain exclusive customer success stories from applications around the world. Ifyou would like your application featured in an upcoming issue of Flowfront, please contact me at laura carrabine@moldflow.com.Also in this issue, Barr Klaus, vice-president of technology at Milacron, Inc., comments about how Milacron is responding to the globalenergy crisis in the Executive Spotlight. This column is a forum for senior management to discuss industry trends, solutions to problems,and what's on the horizon in terms of new technology. In his commentary, Mr. Klaus explains how all-electric injection molding machinescan help save manufacturers millions of dollars in terms of conserving energy and why the benefits of converting to all-electric faroutweigh the costs of retaining inefficient equipment.Professor Robert Malloy of the Plastics Engineering Program at the University of Massachusetts Lowell provides an interesting historicaloverview of the Plastics Engineering Program at the school. From its humble beginnings in 1895, the program today is rich in technologyand resources. Support and endowments from outside sources such as Moldflow and Milacron are testament to the program's success.This issue of Flowfront also provides tips and techniques for using Moldflow Plastics Advisers (MPA) 5.0 design-for-manufacture analysissoftware from product line manager Murali Anna-Reddy. Using MPA tools, designers can test every part and mold concept formanufacturing feasibility before the tool is cut, when the cost of change is minimal.ProMold's sales and engineering manager, Scott Peters, tells us how the role of mold designer has changed over the course of his career. Fromoverpaid draftspeople to valued team members, Scott says that technically savvy mold designers today are key to a manufacturer's success.Soon, Moldflow will open its Center for Professional Development. Stephen Thompson, Moldflow's global training manager, explainswhy the facility came to be and how it will be used. The Center is a corporate university that is being developed for Moldflow customersto help empower their Moldflow users.Enjoy this first issue. We are excited to bring you the latest news and technology via this format. We welcome reader input and encourageyou to submit article ideas, suggestions, and comments about what you like and don't like about the publication. If you have softwaretips and/or techniques that you would like to share, please do. Send your feedback to laura carrabine@moldflow.com.Laura CarrabineEditorF l o w f r o n t Vo l . 1 I s s u e 1w w w. m o l d f l o w. c o m4
FocusonMoldflow ManufacturingSolutions for the Automation,Control, and Monitoring of theInjection Molding ProcessBy Peter Rucinski, Moldflow CorporationMolders today are constantly in the search for waysto squeeze inefficiencies out of every step in themanufacturing process. The pressure to reducedowntime and scrap, leverage the know-how ofexperienced die-setters, and implement systemsthat maximize the productivity of every machineand every operator at every site, regardless oflocation, is constant. Increasingly, this industry isturning to technology to provide the solution totheir problems.Custom and captive injection molders wanted a suite of products from one global supplier that would provide injection moldingmanufacturing personnel with all the tools necessary for scheduling, setup, optimization, control, and reporting of the injection moldingprocess. Specifically, customers pointed out that existing molding practices often resulted in: Inefficient scheduling of mold, machine, and laborresources. Unacceptable production scrap rates. Long process setup times and associated scrap. Lack of part traceability. Non-optimized cycle times. Lack of manufacturing management information. Poor or inconsistent control of the molding process. Unacceptable molded part quality.Moldflow's Manufacturing Solutions products address all of these problems with scalable solutions that will work for small, custominjection molders, and large, multi-national corporations.Plastic injection moldingThe plastic injection molding process is integral to many of today's mainstream manufacturing processes. Industries such astelecommunications, consumer electronics, medical devices, computers, and automotive all have large, constantly increasing demands forinjection molded plastic parts. In addition, these industries continually must decrease time-to-market as product life cycles are beingcompressed.While demand for injection molded plastic parts is increasing, the problems associated with the process often can cause significant timedelays and cost increases. This is because the injection molding process is a complex mix of machine variables, mold complexity, operatorskills, and plastic material properties. In addition, there are constant pressures to reduce mold setup times and scrap, improve part quality,and maximize the productivity of every injection molding machine. Due to these pressures, it is becoming increasingly important to havesystems in place to allow the molding process to be scheduled, set up, optimized, controlled, and monitored using an intuitive, systematic,documentable, and globally supported methodology.Intuitive — so machine operators can maximize productivity by not having to be experts on every machine/mold combination they areresponsible for running.Systematic — so the process of setting up and optimizing the molding process can be done with a scientific method that does not relysolely on the skills of the machine operator.Documentable — to meet the strict quality control reporting requirements that are commonplace today.Globally Supported — so that large, multi-national corporations can source these solutions from one supplier and implementcompany-wide standards across their enterprises.In response to market feedback regarding these pressures and existing plastics manufacturing practices Moldflow Corporation hasdeveloped a complete suite of Manufacturing Solutions for the automation, control, and monitoring of the injection molding. Theseproducts consist of:Moldflow Plastics Xpert — a process automation and control system that decreases mold setup time, cycle time, and scrap; andimproves molded part quality and labor productivity.5F l o w f r o n t Vo l . 1 I s s u e 1w w w. m o l d f l o w. c o m
Shotscope — a process monitoring andanalysis system that collects critical data inreal time from the injection moldingmachine and then records, analyzes, andreports on that data.EZ-Track — a real time productionmonitoring and reporting system that canbe attached to virtually any cyclicmanufacturing equipment.Moldflow Plastics XpertThroughout the injection moldingindustry today, the number of molds thatmust be set up and optimized for highvolume part production is far outpacingthe number of process engineers ortrained technicians qualified to do so. It isnot uncommon for a molding operationto have a small number of individuals whohave the education or experience to set upthe injection molding process. And, eventhose who can set up the process often donot have time to optimize it due toproduction pressures. This scenario resultsin problems such as long process setuptimes and associated scrap, non-optimizedcycle times, unacceptable molded partquality, unacceptable production scraprates, and poor or inconsistent control ofthe molding process.molded part with no defects. A user moldsa part, then provides feedback to the MPXsystem regarding molded part quality.MPX processes this feedback along withdata being collected from the machineand (if necessary) determines a processchange that will improve the result.After completing Setup Xpert anddetermining a combination of processingparameters that results in a single,satisfactorily molded part, the user stilldoes not know if these parameters arewithin a robust processing window. Forexample, any process parameter drift orvariation could easily result in parts ofunacceptable quality. In the injectionmolding process, variation is inherent.Whether the material, machine, process,operator, or environment causes it, therewill always be some variation. Thisvariation may or may not result in theproduction of bad parts. The variation isnormal, so the processing window mustbe robust enough to compensate for itwithout producing bad parts.Design of experiments (DOE) is a usefultool in determining a robust processingwindow. The process window is defined asthe maximum amount of allowable processvariation — allowable, because it will notresult in the production of bad parts.While demand for injection molded plasticparts is increasing, the problems associatedwith the process can often cause significanttime delays and cost increases.Moldflow Plastics Xpert (MPX) processautomation and control technologyprovides machine operators with an easyto-learn and easy-to-use tool for the setup,optimization, and control of the injectionmolding process. MPX allows a lessexperienced operator to set up molds,optimize the process, and controlproduction.MPX functionality isarranged into threemodulesI: The Setup Xpert module allows users toperform a variety of injection-velocity andpressure-phase-related setup routines tofix certain defects, such as short shots,flash, burn marks, sink marks, etc.Setup Xpert helps users achieve one goodF l o w f r o n t Vo l . 1 I s s u e 1However, the historical perception of DOEis that it can be complicated, resulting inextensive training requirements and costsfor those responsible for running it. DOEis also time consuming, thus increasing thetime required to put a given mold intoproduction.II: Optimize Xpert is an automated designFocusonofexperiments(DOE) thatcan be runquickly andeasily. Thesoftware does not requireany special training in statistical processcontrol. The goal of using Optimize Xpertis to obtain a robust processing windowthat will compensate for normal processvariation and ensure that acceptablequality parts are produced consistently.While the Optimize Xpert DOE isautomated, easy to use, and relatively fastto complete, it is far from simple. Thereare five process parameters that can beused as DOE factors: packing pressure,mean (or average) injection velocity,velocity stroke, packing time, and coolingtime. In addition, there are a number ofmolding defects that can be used tomeasure part quality criteria, includingshort shots, flash, sink marks, burn marks,poor weld line appearance, weight,dimension, and warpage problems.Assuming a robust processing window isdetermined using the Optimize Xpert,control mechanisms are still required tomake sure that the process stays within itsspecified limits.III: Production Xpert is a comprehensiveprocess control system that maintains theoptimizedprocessingconditionsdetermined with Optimize Xpert.Production Xpert allows the user tomaintain the production processconsistently, resulting in reduced rejectrates, higher part quality, and moreefficient use of machine time. If desired,Production Xpert will correct the processautomatically should it drift or go out ofcontrol.There are still many functions required ina manufacturing operation, includingproductionscheduling,processmonitoring, statistical process control(SPC), statistical quality control (SQC),scrap tracking, production monitoringand reporting, preventive maintenancescheduling, and more.Moldflow ShotscopeThe Moldflow Shotscope processmonitoring and analysis system is acomprehensive product suite that collectscritical data in real time from moldingmachines on the factory floor. Thesoftware then records, analyzes, reports,and allows access to the information forw w w. m o l d f l o w. c o m6
Focusonuse in criticaldecision making.Ad d i t i o n a l l y,the product canbe used forbothplasticinjection molding and metaldie casting operations.Shotscope allows molders to maximize theirproductivity by providing necessary tools toschedule mold and machine resourcesefficiently. The software also monitors thestatus and efficiency of any mold/machinecombination. By monitoring the efficiencyof a given mold/machine combination,molders can schedule jobs based on anumber of criteria, including minimumcycle times, highest production yields, andso on. Users also can define periodicmaintenance schedules for molds andmachines, and, after a pre-determinednumber of cycles or operating hours,Shotscope will signal that preventativemaintenance is required.Shotscope also maintains and displaysstatistical process control (SPC) data in avariety of formats, including trend charts,X-bar and R charts, histograms, andscatter diagrams. This informationprovides molders with the knowledge thattheir processes are in control, and, shouldthey go out of control, Shotscope can alertto an out-of-control condition and divertsuspect-quality parts. Furthermore,because the Shotscope system can measureand archive up to 50 process parameters(such as pressures, temperatures, times,etc.) for every shot monitored, theprocessing "fingerprint" for any part canbe stored and retrieved at any time in thefuture. This functionality is extremelyimportant to any manufacturersconcerned with the potential failure of amolded part in its end-use application (forexample, a medical device).Shotscope7maintainsareportingF l o w f r o n t Vo l . 1 I s s u e 1mechanism that communicates all thedata collected and entered into the systemacross a manufacturing enterprise. As aresult, informed decisions can be made.Users can generate production, scrap,downtime, efficiency, and job summaryreports, any of which also can be used asdocumentation that accompanies partshipments.automatically and can be classified into anunlimited number of causes. Onceproduction data is collected, there is anextensive set of Web-based reports that canincorporate trend charts, tabular reports,pie charts, and Pareto charts. It is possibleto interface the EZ-Track system toERP/MRP systems via an advanced SQLdatabase that is open, fully documented,and ODBC-compliant.Moldflow EZ-TrackMoldflow EZ-Track is software for realtime, plant-wide production monitoringand reporting. The EZ-Track system canbe attached to virtually any cyclicmanufacturing equipment and machinery,such as ultrasonic welders, assemblymachines, packaging equipment, etc., inaddition to injection molding machines.The EZ-Track system provides a scalablesolution for production monitoring,which can be used by small, custommolders with fewer than 10 machines orby large, multi-national corporations withdistributed injection molding andmanufacturing operations around theworld. There are extensive setupcapabilities that allow complete definitionof resources and flexible customization ofmost displays and reports.The EZ-Track system collects data oncycle times, cycle/part counts, and numberof rejects, and it uses this data as thefoundation to perform powerfulscheduling tasks. The EZ-Track schedulercan check for mold conflicts and machinefeasibility and highlight any problems.The product continuously updatesestimates of job completion times basedon actual cycle time, downtime, rejects,and cavitation. In addition, the schedulersupports family molds.EZ-Track monitors machine status,downtime, scrap, raw material usage, andlabor activity. The product can also beused to track machine efficiencies andcompute yield efficiencies. Labor, time,and attendance can be tracked byemployee and associated with machines,jobs, and activities. In this way,manufacturing managers can determinewhat jobs, machines, or activities requiremore labor resources than others require.This capability can allow managers toinvestigate areas where more efficiency,possibly in the form of processautomation, could be introduced intotheir manufacturing operations.EZ-Track can be used to count good parts,diverted parts, packed cases, and othervariables. Downtime is measuredThere are many companies today across abroad range of industries for which plasticinjection molding and related upstreamand downstream manufacturing processesare on the critical path to achievingsuccessful and profitable productlaunches. These companies face a varietyof issues that make it difficult to remaincompetitive: Product life cycles are decreasingwhile short-term volumerequirements are increasingexponentially. Customers continue to demandincreased quality at lower costs. There is a shortage of skilled laborto run ever-more-sophisticatedinjection molding equipment. Inefficiencies in the scheduling,monitoring, and reporting ofproduction do not allow for efficientmanufacturing management. Molded part process documentationand traceability increasingly arebecoming a standard requirement.Competitive companies require tools thatare intuitive, systematic, documentable,and globally supported, such as theMoldflow Manufacturing Solutionsproducts, to remain globally successful.For the latest information on MoldflowManufacturing Solutions products, visitwww.moldflow.com.w w w. m o l d f l o w. c o m
FREE ReportReveals the Best Kept Secretsof In-Plant TrainingIf you’re considering the implementation of an inplant training program, one thing matters. Will itimprove your bottom line by giving you a competitiveadvantage now as well as in the future?Recent breakthroughs in training technology aremaking this possible like never before. This newtechnology, developed by A. Routsis Associates, takesfull advantage of multimedia while using the latest inlearning technology. Utilizing this powerfulcombination results in shorter training times and higheremployee retention rates.Over 100 Interactive Training titles, including moldmaking and mold design, injection molding technology& plastic part design.For a FREE copy of The Best Kept Secrets of InHouse Training and the latest issue of Plastics TrainingReview contact:A. Routsis Associates, Inc.275 Donohue Rd, Suite 14 Dracut, MA 01826Tel:(978) 957-0700 Fax:(978) 957-1860www.traininteractive.com
tips & techniquesUsing Moldflow Plastics Advisers 5.0By Murali Anna-Reddy, Moldflow CorporationTechnique to model adirect sprue gate or hotsprueFor cylindrical or symmetricalshaped parts (boxes, cups, helmets,etc.) that are molded in singlecavity molds, a sprue gate ispreferred. Here, the part is gateddirectly from the sprue. If the sprueis cold, then there is no gate andthe sprue directly connects to thepart. However, with a hot sprue asmall gate is used to facilitateautomaticdegating.Whenmodeling these types of gates, thekey is to understand that MoldAdviser requires a sprue and a gateas the minimum for a feed system.Since there is no gate in the case ofa cold sprue, you will need to modela portion of the sprue as gateentity. Say, for example, that yourcold sprue is three inches long.Then, you could model 2.5 inch asSprue and the remaining 0.5 inch asa Gate. Use the taper angle tocalculate the starting and endingdiameters of the Sprue and theGate. Here is a step by stepprocedure to model these twogates.1. Import the part model and set the model type to Single Cavity.2. Orient the part such that the sprue is in the positive Z-axis. Next, selectthe injection location.3. Select Parting Planeand position the parting plane a smalldistance above the injection point. The distance between the partingplane and the injection point will be the length of your gate.4. Select Specify Mold dimensionsthe length of the sprue.5. Select Edit Runner Defaultsgate. Set the 'A Plate' thickness to. Set the dimensions of the sprue and6. Select Sprue Location. Click on the middle of the injectionlocation, and click OK. This will create the sprue directly above theinjection location7. On the Runner Generation dialog, select Generate Sprue and Gates,and click OK.This should complete the creation of the direct sprue gate or the hotsprue. Examples of each are shown below.Sprue Gate (Cold Sprue)Sprue Gate (Hot Sprue)Technique to model a hot drop runner systemThe process of modeling a hot drop runner system is outlined below using a simple example of a single-cavity mold.However, the same procedure can be applied to multi-cavity and family molds, as well as to modeling 3-plate cold runnersystems.1. Import part model and set the model type to SingleCavity.2. Orient the part such that the sprue is in the positiveZ-axis. Next, select the injection location.3. Select Parting Planeand position the partingplane a small distance above the injection point. The9F l o w f r o n t Vo l . 1 I s s u e 1distance between the parting plane and the injectionpoint will be the length of your gate. Typically, with hotdrops and 3-plate cold runner molds, a restricted gatecalled a Pin Point Gate is used for automatic degatingpurposes. The gate dimensions are typically very smallcompared to other types of gates.continued on page 10w w w. m o l d f l o w. c o m
tips & techniques4. Select Specify Mold dimensions. Set the APlate thickness to the length of the sprue. Turn on theFloating Plate, and set its thickness to the length of thehot drop.5. Select Edit Runner Defaults. Set thedimensions of the sprue, runner and gate.6. Select Sprue Location. Click on the middle ofthe injection location, and click OK. This will create thesprue directly above the injection location.7. On the Runner Generation dialog, select GenerateSprue, and click OK.8. Select Design Runners. This will allow you tocreate runners and gates manually. Click the bottom ofthe sprue. The Runner Creation dialog pops up. SelectCreate Drop and the hot drop will be createdautomatically using the dimensions specified earlier.9. Only the gate is left to be created. Select DisplayBeam Elementsto display the runner as a beamelement. This is quite useful, especially if the runner islarge and obstructs the view. Similarly, select DisplayCavitiesto turn off the display of the cavities. Thistoo can be helpful during the modeling of gates.10. Now select Design Runnersagain and click onthe end of the hot drop and then on the injection cone.The gate will be created automatically between the hotrunner and the injection point.This will complete the creation of a single-cavity moldwith a hot runner system. An example of such a modelis shown below. As mentioned earlier, the sameprocedure could be applied for creating hot runners formulti-cavity and family molds as well as 3-plate coldrunner systems. Examples of such molds are shownbelow.Single-cavity moldwith a hot runnersystemFamily mold with ahot runner systemSingle-cavity mold witha 3-plate cold runnersystemTechniques to model fan, film, ring, or diaphram gatesUsing the geometry tools provided in the Moldflow Mold Adviser module, you can very easily model tunnel, cashew, andtab gates. However, when it comes to modeling fan, film, ring, and diaphram gates, the geometry modeling tools fallshort. The limitations arise from being unable either to accurately represent the volume of plastic in the gate region orto accurately model the flow of the plastic from the gate into the cavity. The common aspect of all these types of gatesis that the gates are very wide (sometimes extending the entire width or circumference of the part). The larger gatewidth spreads and slows the melt as it enters the cavity. If your object is to simulate only the effect of the gate on theplastic flow, you can do so by modeling several injection points along the edge where the gate connects to the part. Inthis case, you need not model the runners and gate, and the analysis would be done in the Part Only mode.On the other hand, if you would like to design the entire sprue, runner, and gate system, then our suggestion is to modelthese types of gates in your CAD system. The STL file you would export from the CAD system should contain both thepart and the gate geometry. The sprue and runners would later be added inside the Mold Adviser.The example shown below features a part model with a fan gate. The two modeling scenarios explained above areshown in the accompanying images.Several injection pointsused to represent plasticflow through the fan gateF l o w f r o n t Vo l . 1 I s s u e 1Model with the part andfan gate designed in theCAD systemSprue and runner added tothe fan gate model tocomplete the runner systemw w w. m o l d f l o w. c o m10
professional developmentEnhancing Customer EducationBy Stephen Thompson, Moldflow CorporationSavvy software providers offer flexible, innovative trainingprograms that help customers learn to quickly and efficientlybecome proficient using their software products. The initialchallenge for organizations such as Moldflow is to developeffective met
Soon, Moldflow will open its Center for Professional Development. Stephen Thompson, Moldflow's global training manager, explains why the facility came to be and how it will be used. The Center is a corporate university that is being developed for Moldflow customers to help empower their Moldflow users. Enjoy this first issue. We are excited to .