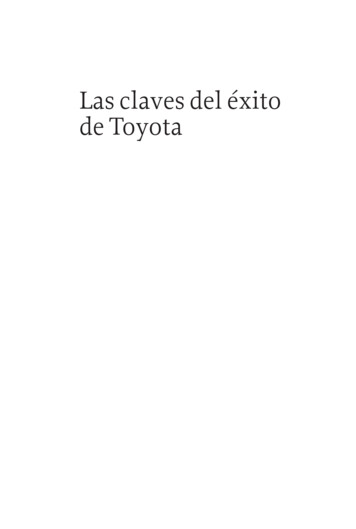
Transcription
Las claves del éxitode Toyota03.indd 314/4/20 4:01 PM
Jeffrey K. LikerLas claves del éxitode Toyota14 principios de gestióndel fabricante más grandedel mundo05.indd 514/4/20 4:05 PM
Obra editada en colaboración con Editorial Planeta - EspañaLa edición original de esta obra ha sido publicada en lengua inglesa porFree Press división de Simon & Schuster, Inc., Nueva York, con el títuloThe Toyota Way. 2006, Autor: Jeffrey L. Liker 2006, Traducción: Lluís Cuatrecasas 2004, McGraw-Hill 2010, Centro Libros PAPF, S.L.U. – Barcelona, EspañaDerechos reservados 2020, Ediciones Culturales Paidós, S.A. de C.V.Bajo el sello editorial PAIDÓS M.R.Avenida Presidente Masarik núm. 111,Piso 2, Polanco V Sección, Miguel HidalgoC.P. 11560, Ciudad de Primera edición impresa en España: septiembre de 2010ISBN: 978-84-9875-074-4Primera edición impresa en México: junio de 2020ISBN: 978-607-747-943-7No se permite la reproducción total o parcial de este libro ni su incorporación a un sistemainformático, ni su transmisión en cualquier forma o por cualquier medio, sea este electrónico, mecánico, por fotocopia, por grabación u otros métodos, sin el permiso previo y porescrito de los titulares del copyright.La infracción de los derechos mencionados puede ser constitutiva de delito contra lapropiedad intelectual (Arts. 229 y siguientes de la Ley Federal de Derechos de Autor yArts. 424 y siguientes del Código Penal).Si necesita fotocopiar o escanear algún fragmento de esta obra diríjase al CeMPro (Centro Mexicano de Protección y Fomento de los Derechos de Autor, http://www.cempro.org.mx).Impreso en los talleres de Litográfica Ingramex, S.A. de C.V.Centeno núm. 162, colonia Granjas Esmeralda, Ciudad de MéxicoImpreso en México - Printed in MexicoLEGAL Las claves del exito de Toyota.indd 619/5/20 6:29 PM
ÍndicePrólogo de Gary ConvisPrefacioIntroducción del InstitutoLean Management de España131523Primera parte.El poder de talla mundial del modelo Toyota271. El modelo Toyota: utilización de la excelencia operacionalcomo un arma estratégica292. Cómo Toyota se convirtió en el mejor fabricante del mundo:la historia de la familia Toyoda y del sistema de producción deToyota473. El corazón del sistema de producción de Toyota: eliminacióndel desperdicio654. Los 14 principios del modelo Toyota: un resumen ejecutivode la cultura detrás del TPS775. El modelo Toyota en acción: el desarrollo «sin compromisos»del Lexus876. El modelo Toyota en acción: nuevo siglo, nuevo combustible,nuevo diseño de proceso: el Prius101Segunda parte.Los principios empresariales del modelo ToyotaSección I. Filosofía a «largo plazo»7. Principio 1: Base sus decisiones de gestión en una filosofíaa largo plazo, a expensas de lo que suceda con los objetivosfinancieros a corto plazoG2000 claves toyota RM CTP v3.indd 912312512722/03/11 09:31
10 LAS CLAVES DEL ÉXITO DE TOYOTASección II. El proceso correcto producirá los resultados correctos8. Principio 2: Cree procesos en flujo continuo para hacerque los problemas salgan a la superficie9. Principio 3: Utilice sistemas pull para evitar produciren exceso10. Principio 4: Nivele la carga de trabajo (heijunka)11. Principio 5: Cree una cultura de parar a fin de resolverlos problemas, para lograr una buena calidad a la primera12. Principio 6: Las tareas estandarizadas son el fundamentode la mejora continua y de la autonomía del empleado13. Principio 7: Utilice el control visual de modo queno se oculten los problemas14. Principio 8: Utilice sólo tecnología fiable y absolutamenteprobada que dé servicio a su personal y a sus procesosSección III. Añada valor a la organización mediante el desarrollo de supersonal y de sus socios15. Principio 9: Haga crecer a líderes que comprendanperfectamente el trabajo, vivan la filosofía y la enseñen a otros16. Principio 10: Desarrolle personas y equipos excepcionalesque sigan la filosofía de su empresa17. Principio 11: Respete su red extendida de sociosy proveedores, desafiándoles y ayudándoles a mejorarSección IV: La resolución continua de los problemas fundamentalesimpulsa el aprendizaje organizativo18. Principio 12: Vaya a verlo por sí mismo para comprender afondo la situación (genchi genbutsu)19. Principio 13: Tome decisiones por consenso lentamente,considerando concienzudamente todas las opciones;impleméntelas rápidamente20. Principio 14: Conviértase en una organización que aprendemediante la reflexión constante (hansei) y la mejora continua(kaizen)G2000 claves toyota RM CTP v3.indd 22/03/11 09:31
ÍNDICE 11Tercera parte.Aplicación del modelo Toyota en su organización21. Utilice el modelo Toyota para transformarlas organizaciones técnicas y de servicio22. Cree su propia empresa lean que aprende, asumiendoideas del modelo Toyota433AgradecimientosBibliografía. Referencias por capítulosBibliografía adicional recomendada465471477G2000 claves toyota RM CTP v3.indd 1140140322/03/11 09:31
Primera parteEl poder de talla mundialdel modelo ToyotaG2000 claves toyota RM CTP v3.indd 2722/03/11 09:31
1El modelo Toyota: utilizaciónde la excelencia operacionalcomo un arma estratégicaNosotros damos un gran valor a la implementacióninmediata y a pasar a la acción. Hay muchas cosas que noentendemos y, por consiguiente, nos preguntamos ¿porqué simplemente no avanzamos y pasamos a la acción yprobamos a hacer algo? Te das cuenta de lo poco que sabes,descubres tus propios fallos y puedes corregir simplementeesos fallos; y en un segundo intento, al hacerlo otra vezte das cuenta de otro fallo o de otra cosa que no te gusta ypuedes volverlo a hacer una vez más. Por eso, sólo con unamejora constante, o debería decir, con la mejora basadaen la acción, uno puede acceder a un nivel más alto depráctica y de conocimiento.FUJIO CHOPresidente de Toyota Motor Corporation, 2002Toyota captó por primera vez la atención mundial en los ochenta,cuando se intuía que había algo especial en la eficiencia y la calidadjaponesas. Los coches japoneses duraban más que los coches americanos y requerían muchas menos reparaciones. En los años noventase hizo evidente que había un plus (alguna cosa más especial) en Toyota comparada con los demás fabricantes de automóviles en Japón(Womack, Jones y Roos, 1991). No fueron los diseños atractivos o lasprestaciones, aunque el montaje fuera mas cuidado y los diseños mucho mas refinados. Era la forma en que Toyota diseñaba y fabricaba loscoches que los elevaba a una consistencia increíble en su proceso y suproducto. Toyota diseñaba coches más rápido, con más fiabilidad, aG2000 claves toyota RM CTP v3.indd 2922/03/11 09:31
30 LAS CLAVES DEL ÉXITO DE TOYOTAun coste competitivo y pagando los sueldos relativamente altos de lostrabajadores japoneses. Igualmente impresionante era que cada vezque Toyota mostraba una aparente debilidad y parecía vulnerable a suscompetidores, milagrosamente solucionaba el problema y continuabaaún con más fuerza. Es cierto que Toyota es el tercer fabricante decoches más grande en el mundo, detrás de General Motors y de Ford,con una venta global de 6 millones de vehículos por año en 170 países.Aunque de todos modos, Toyota es mucho más rentable que cualquierotro fabricante de automóviles. Los analistas del automóvil estimaronque Toyota superaría a Ford en el número global de vehículos vendidosen 2005, y si la tendencia continuaba, acabaría adelantando a GM paraconvertirse en el fabricante de automóviles más grande del mundo.Toda la industria del automóvil y muchos consumidores ya están familiarizados con el tremendo éxito de Toyota y su liderazgo en calidad: ; b X[d[\ Y e WdkWb Z[ JeoejW Wb \ dWb Z[ ik W e \ iYWb [d cWhpe Z[ 2003, fue de 8.130 millones de dólares –más que las gananciascombinadas de GM, Chrysler y Ford, y el mayor beneficio anualde cualquier fabricante de automóviles en al menos una década–.Su margen de beneficio neto también es grande, 3 veces mayorque la media de la industria. C [djhWi [b lWbeh Z[ c[hYWZe Z[ bei jh[i ]hWdZ[i \k[ YWo[dZe [d 2003, las acciones de Toyota se han incrementado un 24% durante2002. La capitalización de Toyota en el mercado (el valor total delas acciones de la compañía) fue de 105.000 millones de dólaresen 2003 –más que la combinación de capitalización de mercadode Ford, General Motors y Chrysler–. Ésta es una estadística asombrosa. Su retorno de inversión es ocho veces más alta que la mediade la industria. La compañía ha tenido beneficios todos los añosdurante los últimos 25 años y tiene entre 20.000 y 30.000 millonesde dólares en su muy consolidada caja. JeoejW W i Ze" ZkhWdj[ Z YWZWi" [b \WXh YWdj[ Z[ Wkjec l b[i número uno en Japón, aunque a un distante cuarto lugar detrásde los tres grandes fabricantes en Norteamérica. Pero en agosto de2003, por primera vez, Toyota vendió más vehículos en Nortea-G2000 claves toyota RM CTP v3.indd 3022/03/11 09:31
EL MODELO TOYOTA: UTILIZACIÓN DE LA EXCELENCIA OPERACIONAL COMO UN ARMA ESTRATÉGICA 31mérica que uno de los tres grandes (Chrysler). Parecía que Toyotapodría, aunque fuera provisionalmente, convertirse en miembropermanente de los tres grandes norteamericanos. (De los 1,8 millones de vehículos Toyota/Lexus vendidos en Norteamérica en2002, 1,2 millones fueron producidos en Norteamérica. Toyota estárápidamente incrementando su capacidad de producción en Estados Unidos, justo cuando los fabricantes estadounidenses estánestudiando cerrar plantas, reducir capacidad y llevarse la producción fuera del país.) ;d (&&) bW cWhYW JeoejW XW YWc de Z[ l[dZ[h c i l[ Ykbei [d Estados Unidos que cualquiera de las dos marcas que lideraban lasventas norteamericanas desde hacía 100 años (Ford y Chevrolet).El coche más vendido en Estados Unidos en 2003 y por quinto añoconsecutivo fue el Camry. El coche más vendido del segmentocompacto en todo el mundo fue el Corolla. JeoejW de WY[ ckY e [hW YedeY ZW feh \WXh YWh l[ Ykbei f[gk[ños y básicos, aunque en los últimos diez años se ha convertidotambién en un líder de los vehículos de lujo. Lexus empezó en1989 y en 2002, y por tercer año consecutivo, sobrepasó en ventasa BMW, Cadillac y Mercedes-Benz en Estados Unidos. JeoejW dl[dj bW ¼fheZkYY d lean» (también conocida como«el sistema de producción de Toyota» o «TPS»), lanzando durante la última década, a prácticamente toda la industria, a unatransformación global del sistema de fabricación y de la cadenade proveedores a la filosofía de Toyota y sus métodos. El sistema deproducción de Toyota es la base de docenas de libros sobre leanincluyendo a dos best sellers: La máquina que cambió el mundo: lahistoria de la producción lean (Womack, Jones, Roos, 1991) y LeanThinking (Womack, Jones, 1996). Los empleados de Toyota por suexperiencia son buscados por otras compañías en prácticamentecualquier industria en todo el mundo. JeoejW j [d[ [b fheY[ie Z[ Z[iWhhebbe Z[ fheZkYjei c i h f Ze del mundo. Para diseñar nuevos camiones necesitan tan sólo 12meses o incluso menos, mientras que los competidores normalmente requieren de dos a tres años.G2000 claves toyota RM CTP v3.indd 3122/03/11 09:31
32 LAS CLAVES DEL ÉXITO DE TOYOTA J eoejW [i Yef WZW Yece be c[ eh [d ik YbWi[ feh iki Yecf[j Zeh[i en todo el mundo por su elevada calidad, alta productividad, rapidez en su fabricación y flexibilidad. Los automóviles de Toyotahan estado constantemente en los rankings más altos de calidadsegún J. D. Powers and Associates, Consumer Reports, y otras firmasdurante muchos años.Gran parte del éxito de Toyota proviene de su increíble reputaciónde calidad. Los consumidores saben que pueden confiar en su vehículoToyota para trabajar desde el primer día y durante tiempo, mientrasmuchas de las compañías norteamericanas y europeas de automóviles producen vehículos que funcionan bien cuando son nuevos,pero seguramente ya deberán pasar por el taller al cabo de un año.En 2003, en Estados Unidos, los vehículos Toyota tuvieron un 79%menos de problemas que los Ford, y un 92% menos que los Chrysler.Según un estudio de 2003 de Consumer Reports, una de las revistas másleídas por los consumidores de coches, 15 de los 38 modelos más fiables durante los últimos siete años estaban hechos por Toyota/Lexus.Ningún otro fabricante le seguía de cerca. GM, Mercedes y BMW notenían ningún coche en esa lista. Ningún Toyota se mencionaba enla lista de «vehículos a evitar» según Consumer Reports, mientras queun montón de Ford, al menos la mitad de los GM, y más de la mitadde Chrysler aparecían en dicha lista.He aquí otras estadísticas del informe anual de 2003 de ConsumerReports: ; d bW YWj[]eh W Z[ YeY [i YecfWYjei JeoejW 9ehebbW" ehZ ecus/Escort, GM Cavalier y Chrysler Neon), Toyota ganó durante los últimos tres años en fiabilidad global, como ya lo habíahecho anteriormente, y en fiabilidad futura para el modelo delaño 2003. ;d YkWdje W bei i[ZWd[i \Wc b Wh[i" [b JeoejW 9Wcho Z[iXWdY Wb Ford Taurus, al GM Malibu y al Dodge Intrepid, ganando en lostres últimos años, y presumiendo de fiabilidad para el modelodel año 2003.G2000 claves toyota RM CTP v3.indd 3222/03/11 09:31
EL MODELO TOYOTA: UTILIZACIÓN DE LA EXCELENCIA OPERACIONAL COMO UN ARMA ESTRATÉGICA 33 C i Z[ bW c jWZ Z[ bei JeoejW Z[ i[]kdZW cWde i[ l[dZ[d Yece «recomendación de compra», mientras esta cifra es menos del10% de Ford, el 5% de GM y ninguno de Chrysler. JeoejW%B[nki jWcX d W Zec dWZe bei hWda d]i Z[ ¼YWb ZWZ d cial» y durabilidad a largo plazo (de J. D. Powers) durante años.Lexus fue una vez más el coche número uno en fiabilidad, segúnun informe de calidad de 2003 de J. D. Powers, seguido por Porsche, BMW, y Honda.¿Cuál es el secreto del éxito de Toyota? La increíble consistencia delrendimiento de Toyota es el resultado directo de su excelencia operacional. Toyota ha convertido a su excelencia operacional en un armaestratégica. Esta excelencia operacional está basada en parte en herramientas y métodos de mejora de calidad, hechas famosas por Toyota enel mundo de la fabricación, como «just-in-time», «kaizen», «flujo piezaa pieza», «jidoka», y «heijunka». Estas técnicas han ayudado a expandirla revolución lean manufacturing. Pero las herramientas y las técnicasno son ningún arma secreta para transformar un negocio. El éxito deToyota al implementar estas herramientas proviene de la filosofía másprofunda del negocio basada en su comprensión y en la motivación dela gente. Su éxito está finalmente basado en su habilidad para cultivarel liderazgo, los equipos, y la cultura, para proyectar una estrategia,para construir relaciones con los proveedores y para mantener unaorganización del aprendizaje.Este libro, basado en mis 20 años de estudio de la compañía, describe los catorce principios que constituyen el modelo Toyota. Estoscatorce principios son también la base del sistema de producción deToyota (TPS) practicado en las plantas de Toyota de todo el mundo.Para su mejor comprensión he dividido estos principios en cuatrocategorías, todas con la inicial «P», Filosofía (del inglés Philosophy),Proceso, Gente (del inglés People/Partners) y resolución de Problemas(ver figura 1-1). (Para un resumen de los catorce principios del modeloToyota, ver capítulo 4.)En las mismas fechas que yo empezaba a escribir este libro, Toyota me mostró su propio documento interno del modelo Toyota paraG2000 claves toyota RM CTP v3.indd 3322/03/11 09:31
34 LAS CLAVES DEL ÉXITO DE TOYOTAsus propósitos de formación. Este documento tuvo influencia en miplanteamiento sobre estos catorce principios y, consecuentemente, lohe incorporado en estos cuatro niveles de este documento (Genchi,Genbutsu, Kaizen, Respeto y trabajo en equipo y desafío) y los relaciono con mis cuatro categorías de principios: Filosofía, Proceso, Gente yresolución de Problemas (ver figura 1-1).El modelo Toyota y el sistema de producción de Toyota (el métodode fabricación de Toyota) son la doble hélice del ADN de Toyota; definió su estilo directivo y lo que hace única a esta compañía. En estelibro espero explicar y demostrar que este modelo de Toyota puede seraplicado en cualquier organización, para mejorar su negocio, desdelas ventas al desarrollo de producto, marketing, logística y dirección.Para ayudarle en ese viaje ofrezco numerosos ejemplos de cómo Toyotamantiene este alto nivel de lóbulos, también exploraremos compañíasde una gran variedad de industrias y servicios que han aplicado deuna manera eficaz los principios de Toyota.Figura 1-1. La pirámide «4P» del modelo Toyota.gegen nchitbutsuTérminosToyotakaize2ES nPETOYENEQU TRABAJOIPOResoluciónde problemas(mejora continuay aprendizaje)s !PRENDIZAJE CONTINUO A TRAVÏS DE kaizen.s 6E Y OBSERVA POR TI MISMO PARA COMPRENDER AL COMPLETO LASITUACIØN (genchi genbutsu).s 4OMA DECISIONES DETENIDAMENTE DE FORMA CONSENSUADACONTEMPLANDO TODAS LAS OPCIONES POSIBLES IMPLEMENTArápidamente.Gente y socios RESPETO RETOSY CONTINUA EVOLUCIØN2ETOProceso ELIMINACIØN DE LOS DESPERDICIOSG2000 claves toyota RM CTP v3.indd 34Filosofía PENSAMIENTO A LARGO PLAZOs &ORMA A LÓDERES QUE VIVAN LA FILOSOFÓA s 2ESPETA HAZ EVOLUCIONAR Y RETA A TU GENTE Y A TUSEQUIPOS s 2ESPETA HAZ EVOLUCIONAR Y AYUDA A TUS PROVEEDORES s #REAR iFLUJOw EN LOS PROCESOS PARA QUE APAREZCAN LOSPROBLEMAS s 5TILIZAR SISTEMAS pull PARA EVITAR SOBREPRODUCCIØN s .IVELAR LA CARGA DE TRABAJO (heijunka).s 0ARAR CUANDO APARECE UN PROBLEMA DE CALIDAD (jidoka).s %STANDARIZAR TAREAS PARA PODER MEJORAR CONTINUAMENTE s 5TILIZAR CONTROLES VISUALES CON EL OBJETIVO DE QUE LOSPROBLEMAS NO QUEDEN ESCONDIDOS s 5TILIZAR TECNOLOGÓA FIABLE QUE HAYA SIDO PROBADA s "ASA TUS DECISIONES DE GESTIØN EN UNAFILOSOFÓA A LARGO PLAZO A EXPENSAS DE LOQUE SUCEDA CON LAS METAS A CORTOPLAZO 22/03/11 09:31
EL MODELO TOYOTA: UTILIZACIÓN DE LA EXCELENCIA OPERACIONAL COMO UN ARMA ESTRATÉGICA 35El sistema de producción de Toyota (TPS) y el leanproductionEl sistema de producción de Toyota es una aproximación única a laproducción. Es la base de gran parte del movimiento lean productionque ha dominado las tendencias de producción (juntamente con seissigma) durante los últimos diez años. A pesar de la gran influenciadel movimiento lean, espero mostrar en este libro que muchos de losintentos de implementar lean han sido bastante superficiales. La razónes que muchas compañías se concentran demasiado en herramientascomo las «5S» y el JIT, sin entender el lean como un sistema completoque debe incorporar también una organización cultural. En muchascompañías donde el lean se ha implementado, la dirección no estabainvolucrada en el día a día ni en la mejora continua que forman partedel lean. La realidad de Toyota es muy diferente.¿Qué es exactamente una empresa lean? Se podría decir que es elresultado final de aplicar el sistema de producción de Toyota a todaslas áreas del negocio. En su excelente libro Lean Thinking, James Womack y Daniel Jones definen el lean manufacturing como un proceso decinco pasos: definir el valor del cliente, definir el flujo de valor, hacerlo«fluir», tirarlo (pull) desde el final (cliente) y perseguir la excelencia.Para una producción lean se requiere una mentalidad que enfoque larealización del flujo de producto a través de procesos de valor añadido,sin interrupción (flujo pieza a pieza), con un sistema pull que avanzadesde el final a partir de la demanda del cliente completando sólolo que la siguiente operación necesita o se ha llevado, en intervaloscortos, y en una cultura en que cada uno está continuamente persiguiendo la mejora.Taiichi Ohno, fundador del TPS, lo dijo de forma más sucinta:Lo que todos controlamos es la cronología desde el momento del pedido del cliente hastaque cobramos. Durante el proceso todos estamos reduciendo ese tiempo y eliminandoel desperdicio que no añade valor (Ohno, 1988).Como veremos con más detalle en el segundo capítulo, Toyota desarrolló su sistema de producción después de la segunda guerra mundial,G2000 claves toyota RM CTP v3.indd 3522/03/11 09:31
36 LAS CLAVES DEL ÉXITO DE TOYOTAen una situación y frente a unas condiciones de negocio muy diferentes de las de Ford y GM. Mientras que Ford y GM usaban la producciónen masa, las economías de escala y las grandes máquinas para producirel mayor número de piezas y lo más económicas posible, el mercadode Toyota en la posguerra japonesa era pequeño. Toyota además debíafabricar una gran variedad de productos en la misma línea de montajepara satisfacer a sus clientes. Por eso, la clave de sus operaciones fue laflexibilidad. Esto ayudó a Toyota a hacer un descubrimiento crítico:cuando los tiempos totales (lead time) se reducen y el interés se centraen flexibilizar las líneas de producción, se consigue una calidad másalta, una mejor respuesta al cliente, una mejor productividad y unamejor utilización de la maquinaria y del espacio. Mientras la tradicional producción en masa de Ford parece buena cuando se mide elcoste por pieza en la máquina individualmente, lo que los clientesquieren es una mayor variedad de elección de la que puede ofreceresta fabricación tradicional de manera efectiva en cuanto al coste.El objetivo de Toyota en los años cuarenta y cincuenta de eliminarel tiempo y el material desperdiciado en cada uno de los pasos delproceso de producción –desde la materia prima al producto terminado– estaba diseñado para hacer frente a las mismas condiciones quese encuentran muchas empresas hoy en día: la necesidad de procesosmás rápidos y flexibles, haciendo lo que quieren los clientes, cuandolo quieren, con la mejor calidad y a un coste competitivo.El interés en el «flujo» ha continuado como una de las bases deléxito global de Toyota en el siglo XXI. Compañías como Dell tambiénse han convertido en famosas por usar lead times cortos, con alta rotación de inventarios, que son pagados rápidamente, para tambiénrápidamente desarrollar una compañía de crecimiento rápido. Peroincluso Dell está tan solo iniciando el camino para poder convertirseen la sofisticada «empresa lean» que Toyota ha desarrollado durantedécadas de aprendizaje y de duro trabajo.Desafortunadamente, muchas compañías aún están usando las técnicas de producción en masa que funcionaron tan bien para Henry Forden los años veinte, cuando la flexibilidad y la posibilidad de elección delcliente no eran tan importantes. El interés en la eficiencia de los pro-G2000 claves toyota RM CTP v3.indd 3622/03/11 09:31
EL MODELO TOYOTA: UTILIZACIÓN DE LA EXCELENCIA OPERACIONAL COMO UN ARMA ESTRATÉGICA 37cesos individuales de la producción en masa nos devuelve a FrederickTaylor y a su «dirección científica» de principios del siglo XX. Al igualque los creadores del sistema de producción de Toyota, Taylor intentóeliminar el desperdicio de los procesos de producción. Él observó a lostrabajadores y trató de eliminar cualquier segundo de movimiento ineficiente. Los ideólogos de la producción en masa comprendieron mástarde que los paros de las máquinas también eran otro desperdicio sinvalor añadido: una máquina apagada por reparaciones no hace piezasque podrían dar dinero. Pero considere las siguientes anti-intuitivasverdades acerca del desperdicio sin valor añadido en la filosofía del TPS: M uchas veces lo mejor que se puede hacer es parar una máquina y dejarde producir piezas. Esto se hace para evitar la sobreproducción, undesperdicio fundamental en el TPS. A menudo es mejor construir un inventario de piezas acabadas parapoder nivelar una producción programada, que producir acorde con unademanda fluctuante de órdenes de clientes. Nivelar la programación(heijunka) es fundamental para el flujo, los sistemas pull y paraminimizar el inventario en la cadena de suministros. (Nivelar laproducción significa amortiguar el volumen de mezcla de referencias producidas para que haya sólo una pequeña variación enla producción de un día a otro.) A menudo es mejor sustituir selectivamente gastos generales por trabajadores directos. Cuando nos hemos liberado del desperdicio denuestros trabajadores con valor añadido, es necesario proveerlesde apoyo de alta calidad del mismo modo que nos gustaría ayudara un cirujano en una operación complicada. N o ha de ser una prioridad principal mantener a los trabajadores ocupados haciendo piezas tan rápido como sea posible. Se deberán producir piezas al mismo ritmo de la demanda. Trabajar más rápidosolamente por el gusto de sacar el máximo provecho de los trabajadores es otra manera de sobreproducción y eso nos conducea emplear más gente de la necesaria. C onviene usar selectivamente la informática, y a menudo es mejor utilizar procesos manuales en lugar de posibles automatizaciones, aunqueG2000 claves toyota RM CTP v3.indd 3722/03/11 09:31
38 LAS CLAVES DEL ÉXITO DE TOYOTAparezca justificarse su coste por la reducción en mano de obra. Lagente constituye el recurso más flexible del que se dispone. Sino se ha trabajado de manera eficiente en el proceso manual, noestará claro donde es necesaria la automatización para ayudaren el proceso.En otras palabras, las soluciones de Toyota a los problemas particulares a menudo parecen añadir más desperdicio en lugar de eliminarlo. La razón para esta paradoja es que Ohno aprendió de susexperiencias de taller un significado muy peculiar del desperdicio devalor añadido: se puede hacer poco con operarios ocupados y equipos que trabajan al máximo, y mucho con la forma de transformarla materia prima en un bien vendible. Para Ohno, la finalidad de sus«excursiones» por la planta es identificar las actividades que deberíandar valor a la materia prima, y deshacerse de todo lo demás. Aprendióa hacer un mapa del flujo de valor de la materia prima que se transforma en un producto acabado por el que el cliente desearía pagar.Este método era radicalmente diferente del sistema de producciónen masa de simplemente identificar, enumerar y eliminar el tiempodesperdiciado y centrar los esfuerzos en los procesos de producciónexistentes.Si hacemos «la excursión», como Ohno, en nuestra propia organización para mirar los procesos veremos materiales, facturas, llamadasde servicio y piezas de prototipos en I D (y así podría añadir todos losprocesos de su negocio) que son transformados en algo que el clientequiere. Pero una inspección más minuciosa delatará que a menudohay materiales que son desviados a un rincón, a algún lugar dondese acumulan y esperan largos períodos de tiempo, hasta que los mueven al siguiente proceso o transformación. Ciertamente, a la genteno le gusta ser desviada de su trayecto o sus propósitos y tener queesperarse en largas colas. Ohno veía a los materiales como si tuvieranel mismo nivel de impaciencia. ¿Por qué? Si cualquiera de los largoslotes de material son producidos y después aparcados a la espera deser procesados, si las llamadas de servicio son archivadas, si el I Drecibe piezas de prototipos y no tienen tiempo para inspeccionarlas,G2000 claves toyota RM CTP v3.indd 3822/03/11 09:31
EL MODELO TOYOTA: UTILIZACIÓN DE LA EXCELENCIA OPERACIONAL COMO UN ARMA ESTRATÉGICA 39entonces este paro y la espera para la siguiente operación se convierte endesperdicio. El resultado es que tanto los clientes internos como losexternos se acaban impacientando. Por esta razón el TPS empieza porpreguntar al cliente: «¿Qué valor le estamos añadiendo al productosegún su perspectiva?». Porque el único indicativo de valor en cualquier tipode proceso –sea en la fabricación, marketing o desarrollo de procesos– es latransformación física o de información de un producto, servicio o actividadesen algo que el cliente desea.Por qué las compañías a menudo piensan que sonlean, pero no lo sonCuando empecé a descubrir el TPS, estaba admirado por el flujo ydel poder que tiene el flujo pieza a pieza. Cuanto más aprendía delos beneficios del flujo y del pull de piezas cuando se necesitan, enlugar de producir y crear inventario, más deseaba experimentaren primera línea la transformación de procesos de producción enmasa a procesos lean. Aprendí que todas las herramientas de apoyodel lean, como son: equipamiento rápido de cambios de preparación,trabajo estandarizado, sistemas pull y sistemas anti-error poka-yoke,eran todas necesarias para crear flujo. Pero mientras avanzaba en miapredizaje, líderes experimentados de Toyota me advertían que esasherramientas y técnicas no eran la clave del TPS. Más allá del poderdel TPS, hay detrás además un compromiso directivo de una compañíade invertir constantemente en su gente y promover la cultura de lamejora continua. Creía saber de qué me estaban hablando y continuéestudiando cómo calcular sistemas kanban y construir células de flujopieza a pieza. Fue después de estudiar Toyota durante casi 20 años yobservar cómo finalmente se hundían otras compañías a pesar desus esfuerzos aplicando fabricación lean, que comprendí lo que esosmaestros de Toyota (llamados «sensei») querían decir. La intenciónde este libro es demostrar que el modelo Toyota consiste en algo másque un conjunto de herramientas del lean, como el just-in-time.Pongamos por ejemplo que usted compra un libro de cómo crearcélulas de flujo pieza a pieza, o que quizás usted va a clases de formación, o quizás ha contratado un consultor lean. Usted escoge unG2000 claves toyota RM CTP v3.indd 3922/03/11 09:31
40 LAS CLAVES DEL ÉXITO DE TOYOTAproceso y desarrolla un proyecto de mejora lean. Una revisión del proceso ya revela montones de «desperdicio» o «muda», término queutiliza Toyota para designar cualquier cosa que lleva tiempo peroque no añade valor a su cliente. Se da cuenta de que está desorganizadoy el sitio es un desorden. Entonces usted lo limpia y endereza el flujodel proceso. Todo empieza a fluir más rápido. Tiene mejor controlsobre el proceso. La calidad también mejora. Esto es estimulante y seanima a desarrollarlo en otras partes de la planta. Entonces, ¿dóndeestá la dificultad?He visitado centenares de organizaciones que se proclaman avanzadas en la práctica de métodos lean. Muestran orgullosas su pequeñoproyecto lean. Y, sin duda, han
Las claves del éxito de Toyota 14 principios de gestión del fabricante más grande del mundo G2000 claves toyota RM CTP v3.indd 5 22/03/11 09:31 . LEGAL Las claves del exito de Toyota.indd 6 19/5/20 6:29 PM. Índice Prólogo de Gary Convis 13 Prefacio 15