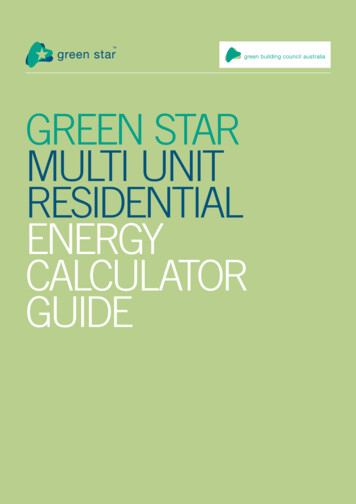
Transcription
Green StarMulti UnitResidentialEnergyCalculatorGuide1
EXECUTIVESUMMARYThe Green Star – Multi Unit Residential EnergyCalculator has been developed to predict the performanceof multi-unit residential buildings based on the totalgreenhouse gas emissions per person. The calculator comparesthe predicted greenhouse gas emissions to a set benchmark.Points are then awarded for a percentage reduction ingreenhouse gas emissions compared to the benchmark.To use the calculator, the predicted energy consumptionof the building is calculated. Important components suchas heating and cooling loads can be determined by using theNatHERS score or by computer modeling. For NSW buildings,the BASIX score can be used as an option to score Green Starpoints in lieu of the calculator.The predicted ancillary load energy consumption,such as that from lighting, mechanical ventilation and lifts,must also be calculated. This guide includes details on howto calculate these loads in such a way that they can be fairlycompared to the set benchmark.Finally, this guide includes information on how to enterthe simulation outputs and the ancillary load calculationsinto the Green Star – Multi Unit Residential Energy Calculator.The calculator compares the performance of the facilityrelative to the benchmarks. The Green Star – Multi UnitResidential Energy Calculator Benchmarking Methodologyreport provides further information on how these benchmarkswere determined.2
TABLE TIONGUIDELINES FOR SIMULATION OUTPUTSGUIDELINES FOR SIMULATIONINPUT PARAMETERSNatHERS MethodologyGeneral HVAC modelling parametersHVAC Internal LoadsA/C PumpingHVAC System SimulationsHVAC ControlsOTHER SERVICESCASE STUDYTwo Storey BuildingFour Storey BuildingEight Storey BuildingAPPENDIX A- SIMULATION BRIEF FOR ASSESSORSAPPENDIX B- SPACE TYPE DEFINITIONSAPPENDIX C– HVAC INTERNAL LOADS AND PROFILESAPPENDIX D:– HVAC INTERNAL LOADS AND PROFILESLIST OF FIGURESFigure One: How to enter the simulation outputsFigure Two: If there is a central HVAC SystemFigure Three: Screen shot of the Energy CalculatorFigure Four: If there is no central HVAC SystemFigure Five: Two storey residentialcalculator snap shotFigure Six: Four storey residentialcalculator snap shotFigure Seven: Eight storey residentialcalculator screen shotFigure Eight: Living space profileFigure Nine: First Bedroom profileFigure Ten: Additional bedrooms 2526273
1. IntroductioNThe Green Building Council of Australia (GBCA) hasdeveloped a suite of rating tools to assess the environmentalperformance of buildings in Australia. As part of the GreenStar – Multi Unit Residential rating tool, the Green Star – MultiUnit Residential Energy Calculator assesses the environmentalperformance of residential buildings with multiple dwellings bymeasuring their environmental impact.Part of this assessment of environmental performanceincludes determining the predicted energy consumptionof the multi-unit residential building. The Green Star– Multi Unit Residential Energy Calculator has been developedto compare this to a benchmark. More information on howthe benchmarks were set can be found in the Green Star– Multi Unit Residential Calculator BenchmarkingMethodology report.The building can be simulated using computer modellingsoftware in order to determine the predicted energyconsumption of its Heating, Ventilation and Cooling (HVAC)system. In place of this, NatHERS second generation heatingand cooling loads can be used for dwellings. In addition, thepredicted energy consumption of the ancillary loads in thebuilding must be calculated.The BASIX tool score for NSW buildings can be input intothe Green Star – Multi Unit Residential Energy Calculator as asubstitute to filling out the rest of the calculator to determinethe Green Star points awarded.This report has been written as a guide to the requiredGreen Star – Multi Unit Residential, and how they shouldbe entered into the Energy Calculator for comparison.4
2. Guidelines forsimulation outputsFigure 1 shows how to enter the simulation outputs intothe Green Star – Multi Unit Residential Energy Calculator.Information should be entered into the white cells.Continue to HVAC Energy Consumption 5
Figure 2: If there is a central HVAC system:Continue to HVAC Energy Consumption 6
Figure 3: Screen shot of the Energy Calculator7
Figure 4: If there is no central HVAC system(air conditioning is only provided individually to dwellings):Continue to Lighting Energy Consumption8
3. Guidelines forSimulation InputParametersThis section outlines the parametres used to simulate theHVAC energy consumption of a residential building. These arestandard criteria that must be adhered to in ordered to complywith the Green Star energy credit requirements. The outputsfrom this simulation will then be entered in the calculator, asoutlined in Section 2. Each typical dwelling must be assessed,as well as any common area which contains HVAC.The average dwelling load is based on an area weightedaverage of typical dwellings.If the BASIX tool is used, then only the BASIX score needsto be entered to be awarded the points and no other sectionsof the calculator need to be filled out. Second GenerationNatHERS heating and cooling loads can be used as analternative to the modelled heating and cooling loadsfor dwellings.9
3.1 NatHERS MethodologyTable 1: NatHERS parameters tableModelling ParameterRequirementsDocumentationNatHERS Demonstrate the average heatingand cooling loads.Verification Documents: NatHERS Certificate.HVAC Performance Demonstrate the co-efficientperformance of HVAC system.Give a brief description of the system.Verification Documents: Relevant pages of theHVAC Specification.3.2 General HVAC modelling parametersTable 2: Building envelope parameters Passed the BESTEST validation test; orSimulation PackageWeather DataOver shadowing The European Union draft standard EN13791July 2000; or Be certified in accordance with ANSI/ASHRAEStandard 140-2001.Please contact the GreenBuilding Council of Australia if none of the aboveoptions can be complied with. A Test Reference Year (TRY) if the building locationis within 50km of a TRY location; or In the absence of local TRY weather data,an actual year of recorded weather data froma location within 50km of the building location; or In the absence of TRY or actual weather datawithin 50km, interpolated data based upon3 points within 250km of the building location.Please contact the Green Building Council ofAustralia if none of the above options can becomplied with. Demonstrate that overshadowing from thesurrounding environment has been taken intoaccount in the model.Energy Report: Simulation brief for assessor(see Appendix A).Energy Report: Type of data (TRY / year / interpolated). Weather station location.Verification Documents: Relevant architectural drawings.Energy Report: Details of how overshadowing from theexternal environment has been representedin the model.1. The International Energy Agency, working with the U.S.National Renewable Energy Lab, has created a benchmarkfor building energy simulation programs. This benchmark is entitled“BESTEST – International Energy Agency Building Energy SimulationTest and Diagnostic Method”.10
Table 2: Building envelope parameters (continued)Building FormInsulationGlazingWindowsand SpandrelShadingOrientationInfiltration Demonstrate that the simulation model is anaccurate representation of the building’s shape; Demonstrate that all floors in the building aremodelled; and Show that there are limited simplifications tothe building form. Demonstrate that insulation in the walls, ceilingand floors has been accurately represented. Demonstrate that glazing is modelled using thefollowing parameters:- Visible light transmission;- Solar transmission;- Internal and external solar reflectance; and- Emissivity. Demonstrate that the sizes of windowsand spandrel are accurately represented. Demonstrate that all shading of windowsand external building fabric has beenaccurately represented. Demonstrate that the building orientation hasbeen included in the model. Demonstrate that infiltration has been modelledto reflect façade design specification. Typicaldefault values are 0.5 air changes per hour forperimeter zones and zero air changes per hourfor central zones.Verification Documents: Relevant architectural drawings.Energy Report: Details of how the building’s physical shapehas been represented in the model. Details of any simplifications in the modeland their effect.Verification Documents: Relevant architectural drawings. Materials schedule.Energy Report: Details on how the insulation has beenrepresented in the model.Verification Documents: Relevant pages from the glazingor façade specification.Energy Report: Details of how glazing has been modelled.Verification Documents: Relevant architectural drawings.Energy Report: Details of the window and spandel sizesthat have been used in the model.Verification Documents: Relevant architectural drawings.Energy Report: Details of how window shadingand external building fabric are representedin the model.Verification Documents: Relevant architectural drawings.Energy Report: Details of how the orientation has beenrepresented in the model.Verification Documents: Relevant architectural drawings. Relevant pages from the façadespecification that show infiltrationor façade sealing characteristics.Energy Report: Details of how infiltration hasbeen modelled.11
3.2HVAC Internal LoadsTable 3: Internal loads parametersModelling ParameterLightingRequirements Demonstrate that lighting is calculated basedon space type. Demonstrate that the appropriate HVAC ModelOperational Profile (see Appendix C) has beenused in the HVAC Model.DocumentationVerification Documents: Area schedule. Reflected ceiling plans with base buildinglighting design. Relevant pages from electricalspecification showing occupancy sensors(if any), time clock (if any), lightsand light fittings.Energy Report: Details of space type areas using thedefinitions in Appendix B. Details of how the lighting power densitieshave been modelled. Details of how the operational profiles forthe building have been modelled.Verification Documents: Area schedule.Equipment Demonstrate that all equipment loadsis calculated based on space type. Demonstrate that the equipment loads aremodelled using the operational profilesas prescribed in Appendix C.Energy Report: Details of space type areas usingthe definitions in Appendix B. Details of how the equipment loaddensities have been calculated. Details of how the operational profiles havebeen modelled.Verification Documents: Bedroom schedule.Occupancy Demonstrate that all occupancies are calculatedbased bedroom quantities. Demonstrate that the occupancy profile usedis that prescribed for each space type inAppendices C.Energy Report: Details of space type areas usingthe definitions in Appendix B. Details on how the occupancy loadshave been modelled. Details on the profiles used for occupancy.Table 4: A/C pumping parametersModelling ParameterChilled waterHeating hot waterRequirements If central chiller water is supplied, demonstratethat chilled water pumping is calculated usingthe building cooling load, the static pressure ofthe chilled water pumps (typically 250kPa) andthe flow rate in L/s. If central heating hot water is supplied,demonstrate that the hot water pumpingis calculated using the building heating load,the static pressure of the hot water pumps(typically 250kPa) and the flow rate in L/s.DocumentationVerification Documents: Relevant pages from the hydraulicand mechanical specifications showingchilled water pump data – static pressureand flow rate in L/s.Energy Report: Calculation of chilled water pumping.Verification Documents: Relevant pages from the hydraulic andmechanical specifications showing hotwater pump data – static pressure and flowrate in L/s.Energy Report: Calculation of hot water pumping.12
3.4HVAC System SimulationsTable 5: HVAC system simulationModelling ParameterHVAC System designRequirements Demonstrate that the HVAC system modelledrepresents the system design for each partof the building.DocumentationVerification Documents: Relevant pages from mechanicalspecification and mechanical drawingswhich accurately and thoroughly describethe basic HVAC system design.Energy Report: Details of how the HVAC system has beenrepresented in the model.ZoningChiller plant and/orAC unitsBoiler plant Demonstrate that all air conditioning zonesrepresented in the thermal model accurately reflectsystem performance and zonal solar diversity. Demonstrate that the chiller plant size and for ACunits are accurately reflected in the model. Demonstrate that the actual efficiency curvesof the installed equipment are used in the model. Water cooled equipment: Demonstrate that datais specified under conditions that reflect theintended condenser water temperature controls. Air cooled equipment: Demonstrate that the COPprofiles have been accurately modelled with regardto loading and ambient conditions If there is a boiler plant, demonstrate that theboiler plant size, thermal efficiency and distributionefficiency are accurately reflected in the model.Supply Air and ReliefFans Demonstrate that fan performance curvesare accurately represented in the model. Demonstrate that index run pressure drops areaccurately represented to include the total staticinclusive of filters, coils and diffusers.Cooling Tower andCondenser WaterPumping If there are cooling towers, demonstrate thatallowance for energy consumption from coolingtower and condenser water pumping has beenmade, based upon the annual cooling loadof the building.Energy Report: Details of how the air conditioning zoneshave been represented in the model, andhow these zones accurately represent themechanical design drawingsand specification.Verification Documents: Relevant pages from the mechanicalspecification showing the chiller plant sizeand any condenser water operation. Documentation from chiller supplier givingpart load curves (and condenser watertemperatures where applicable).Energy Report: Details of how the chiller plant size hasbeen represented in the model. Details of how the actual efficiency curveshave been used in the model. Details of how the chiller data is relevantto the intended condenser watertemperature controls.Verification Documents: Relevant pages from the mechanicalspecification which show details of theboiler plant size, thermal efficiencyand distribution efficiency.Energy Report: Details of how the boiler has beenmodelled.Verification Documents: Pages from the mechanical specificationshowing fan performance curvesand fan size.Energy Report: Details of how the index run pressuredrops have been calculated. Details of how these have been modelled.Energy Report: Details of how the cooling towerand condenser water pumping havebeen modelled.13
3.5 HVAC ControlsTable 6: HVAC Controls parametersModelling ParameterOutside AirEconomy CyclePrimary duct temperature controlAirflow ControlMinimum turndownChiller stagingTemperature controlbandsRequirements Demonstrate that outdoor air flows have beenmodelled as documented in the mechanical designdrawings and specifications, and in compliancewith the appropriate standards. Demonstrate that economy cycles have beenmodelled to reflect system specification notingany enthalpy/temperature cut-off and controlpoint. Constant Volume Systems: Demonstrate thatmodelling has allowed supply air temperaturesto vary to meet loads in the space. Variable Volume Systems: Demonstrate thatmodelling has allowed supply air volumes to varyto meet loads in the space. Demonstrate that set points have beenrescheduled as specified. Note that simplificationsmay be made to consider average zonetemperature in lieu of high/low select. Demonstrate that control logic describing theoperation of the dampers to control outside andre-circulated airflow is inherent in the modeland accurately reflects the airflow characteristicsof the system. Demonstrate, where relevant, that the minimumturndown airflow of each air supply is accuratelyreflected in the model. Demonstrate that for systems that employ multiplechillers with a chiller staging strategy, the correctcontrols are modelled to reflect the actualrelationship between the chillers. Demonstrate that the temperature control bandsof the system accurately reflect the thermal model.DocumentationVerification Documents: Relevant pages from mechanicalspecification giving details on the correctminimum outside air flow.Energy Report: Detail of how outside air flow has beenrepresented in the system.Verification Documents: Relevant pages from mechanicalspecification giving details on the economycycle of the system.Energy Report: Details of how the economy cycle hasbeen modelled.Verification Documents: Relevant pages from mechanicalspecification giving details of the designtemperature and HVAC coolingand heating set points.Energy Report: Detail of how design temperaturesand set points have been modelled.Verification Documents: Relevant pages from the mechanicalspecification giving details of theoperation of the dampers to controloutside and re-circulated air.Energy Report: Details of how these have beenrepresented in the model.Verification Documents: Relevant pages from the mechanicalspecification giving details of the minimumturndown airflow of each air supply.Energy Report: Details of how the minimum turndownis modelled for each air supply.Verification Documents: Relevant pages from the mechanicalspecification giving details of the chillerstaging strategy.Energy Report: Details of how chiller staging hasbeen modelled.Verification Documents: Relevant pages from the mechanicalspecification giving details of the designspecification for the thermal model.Energy Report: Details of how the temperature controlbands have been modelled.14
4. OtherServicesIn addition to the building’s air conditioning system,the following items must also be accounted forin the energy consumption assessment: Lighting;Mechanical exhaust;Lifts, escalators and travelators;Domestic hot water supply; andPool, spa and sauna.These items will be entered separately into the calculator.Domestic water pumping can be ignored. Any other normalor extraordinary energy item that would reasonably beconsidered significant in an energy model must also beincluded and the calculation or simulation methodology mustbe adequately adjusted. This shall include, but not be limitedto, groundwater or water recycling treatment plants.15
Table 7: Other services parametersModelling ParameterLightingMechanicalexhaust systemsLift loadsEscalatorand travelator loadsRequirementsDocumentation Demonstrate that lighting is calculated basedon floor area. Demonstrate that the appropriate Lighting EnergyConsumption Profile in Appendix D has been used.Verification Documents: Area schedule. Reflected ceiling plans with base buildinglighting design. Relevant pages from electricalspecification showing occupancy sensors(if any), time clock (if any), lightsand light fittings.The lighting profile can be adjusted if the followingare installed: Occupancy sensors: Lighting must followthe appropriate lighting profile whenever theappropriate occupancy profile is greater than 0. Time Clocks: If lighting operates on a time clockthen common area lighting must follow theappropriate lighting profile when specified as “on”by the electrical specification. This must operatefor no less time than described for theprevious point. Daylight dimming: Details on this system mustbe provided. Demonstrate that the energy requirements formechanical exhaust systems (such as thoseinstalled for toilets, kitchens and any other purposespecific systems such as car parks and amenitiesexhausts). Each exhaust system is calculated asoperating for 0.5 hr/ day. Lift loads are to be calculated using the methodoutlined in Appendix D. Escalator and travelator loads are to be calculatedusing the method outlined in Appendix D.Energy Report: Details of space type areas using thedefinitions in Appendix B. Details of how the lighting power densitieshave been modelled. Details of how the operational profilesfor the building have been modelled. Details of the lighting control systemsand how they have been modelled.Verification Documents: Relevant pages from the mechanicalspecification showing details of mechanicalexhaust systems.Energy Report: Details of how the energy requirements formechanical exhaust systems are calculated.Verification Documents: Area schedule. Specification of lift systems.Energy Report: Details of how the lift energy requirementis calculated in accordance with Appendix D.Verification Documents: Area schedule. Specification of escalatorand travelator systems.Energy Report: Details of how the escalator and travelatorenergy requirement is calculated.Domestic hotwater loadsPools, Spaand Sauna’s Domestic hot water loads (to showers and washhand basins) are to be calculated using the methodoutlined in Appendix D. Note that any other hot water supply (such as forlaundries) is not to be included. Note that the contribution from any solar hotwater source is to be calculated and subtractedfrom the hot water energy consumption. Demonstrate the energy requirements for pools,spas and sauna’sVerification Documents: Area schedule. Specification of domestic hotwater systems. Specification of solar hot water systems.Energy Report:Details of how the domestic hot waterheating energy requirement is calculatedin accordance with Appendix D.Verification Documents: Specification of pool volume,heating system and cover. Specification of spa volume, heatingsystem and cover. Specification of sauna volume, heatingsystem and ventilation system.Energy Report: Details of how the energy requirementsfor the pool, spa and sauna werecalculated.16
5. Case Study5.1 Two Storey BuildingThis case study illustrates how a two storey building canachieve one point. This building has two studio/1 bedroomapartments, and two 2 bedroom apartments giving a totalof four dwellings in the building. These apartments 80m²and 120m² respectively as set by the benchmark (see GreenStar – Multi Unit Residential Energy Calculator BenchmarkingMethodology Report). Foyers are 20m² per apartmentand one car space per apartment is provided also as perthe benchmark.Firstly, the space type areas are calculated using the definitionsin Appendix B.Table 8: Two Storey Space AreasAll lighting and extras energy consumption were calculatedas specified in section 4 and also to meet the benchmark(see Green Star – Multi Unit Residential Energy CalculatorBenchmarking Methodology Report).Table 10: Two Storey Lighting Energy ConsumptionSpace TypeTotal CalculatedLighting EnergyConsumption(kWh/yr)Dwellings3,236Foyers, lobbies, hallwaysand corridors350Space TypeSpace Area (m²)Amenities0Foyers, lobbies, hallwaysand corridors400Back of House0Amenities40Car park0Back of House0External lighting1,577Indoor car park0External car park0Dwellings120Next, the HVAC consumption of electricity and gas iscalculated using Section 3 of this guide. NatHERS secondgeneration heating and cooling loads were used in place ofa central HVAC system with 100% of all dwellings havingair-conditioning. There was no modelled non-dwelling HVACenergy consumption in this case study.Table 9: Two Storey HVAC NatHERS inputsAverage load of buildingdwellings MJ/m²/yr35Coefficient of Performance (COP)of AC system3.3Table 11: Two Storey Extras Energy ConsumptionExtrasTotal CalculatedEnergy Consumption(kWh/yr)Dwellings Exhaust Systems730Amenities, Back of House & Mechanical Ventilation0Car park Ventilation0Lifts0Domestic Hot Water GAS MJ/yr30,44117
Figure 5: Two storey residential calculator snap shot (right).No energy generation was used in this case study.The results of this case study were as follows:Table 12: Two Storey Case Study ResultsTotal Benchmark Emissions(kgCO2/yr)17,415Total Benchmark Emissions(kgCO2/pers)1,741Actual Facility Emissions (kgCO2/yr)9,975Actual Facility Emissions(kgCO2/pers/yr)998Greenhouse Gas Savings(Difference in greenhouse gasemissions between benchmarkand facility (kgCO2/yr))Number of Points Achieved42.7%1For an equivalent building, a BASIX score of 40%is required to achieve a comparative Green Star point.This information is entered into the calculatoras detailed in Figure 5.18
5.2 Four Storey BuildingTable 15: Four Storey Lighting Energy ConsumptionThis case study illustrates how a four storey building canachieve one point. This building has four studio/1 bedroomdwellings and four 2 bedroom dwellings and four 3 bedroomdwelling giving a total of 12 dwellings. These dwellings havean area of 80m², 120m², 160m² respectively as defined by thebenchmark (see Green Star – Multi Unit Residential EnergyCalculator Benchmarking Methodology Report). Foyers,lobbies, hallways and corridors have been set at 10m² perdwelling as per the benchmark. However, only five car spacesare provided.Firstly, the space type areas are calculated using the definitionsin Appendix B.Table 13: Four Storey Space AreasSpace TypeSpace Area (m²)Dwellings1,440Foyers, lobbies, hallwaysand corridors120Amenities0Space TypeTotal CalculatedLighting EnergyConsumption(kWh/yr)Dwellings11,647Foyers, lobbies, hallwaysand corridors1,051Amenities0Back of House526Car park1,971External lighting0No energy generation was used in this case study.The results of this case study were as follows:Table 17: Four Storey Case Study ResultsTotal CalculatedEnergy Consumption(kWh/yr)Back of House30ExtrasIndoor car park15074,229External car park0Total Benchmark Emissions(kgCO2/yr)Total Benchmark Emissions(kgCO2/pers)2,062Actual Facility Emissions (kgCO2/yr)47,305Actual Facility Emissions(kgCO2/pers/yr)1,314Next, the HVAC consumption of electricity and gas iscalculated using Section 3 of this guide. NatHERS secondgeneration heating and cooling loads were used in place ofa central HVAC system with 100% of all dwellings havingair-conditioning. There was no modelled non-dwelling HVACenergy consumption in this case study.Table 14: Four Storey NatHERS inputsAverage load of buildingdwellings MJ/m²/yr35Coefficient of Performance(COP) of AC system3.3All lighting and extras energy consumption werecalculated as specified in Section 4 to meet the benchmark(see Green Star – Multi Unit Residential Energy CalculatorBenchmarking Methodology report)Greenhouse Gas Savings(Difference in greenhouse gasemissions between benchmark andfacility (kgCO2/yr))Number of Points Achieved36.3%1For an equivalent building a BASIX score of 33% is requiredto achieve a comparative Green Star point.This information is entered into the calculatoras detailed in Figure 6.19
Figure 6: Four storey residential calculator snap shot (right)20
5.3Eight Storey BuildingThis case study illustrates how an eight storey building canachieve one point. This building has eight studio/1 bedroom,sixteen 2 bedroom and eight 3 bedroom dwellings giving atotal of 32 dwellings in the building. Dwelling areas have beendefined according to the number and type of dwellings as perthe benchmark. All other space areas have been defined as perthe benchmark (see Green Star – Multi Unit Residential EnergyCalculator Benchmarking Methodology Report).Firstly, the space type areas are calculated using the definitionsin Appendix B.Table 18: Eight Storey Space AreasAll lighting and extras energy consumption were calculatedas specified in Section 4 to meet the benchmark (see GreenStar – Multi Unit Residential Energy Calculator BenchmarkingMethodology)Table 20: Eight Storey Lighting Energy ConsumptionSpace TypeTotal CalculatedLighting EnergyConsumption(kWh/yr)Dwellings31,059Foyers, lobbies, hallwaysand corridors2,803Amenities2,243Back of House1,121Space TypeSpace Area (m²)Dwellings3,840Foyers, lobbies, hallwaysand corridors320Car park16,614Amenities64External lighting0Back of House64Indoor car park960External car park0Next, the HVAC consumption of electricity and gas iscalculated using Section 3 of this guide. NatHERS secondgeneration heating and cooling loads were used in place ofa central HVAC system with 100% of all dwellings havingair-conditioning. There was no modelled non-dwelling HVACenergy consumption in this case study.Table 19: Eight Storey NatHERS inputsAverage load of buildingdwellings MJ/m²/yr35Coefficient of Performance(COP) of AC system3.3Table 21: Eight Storey Extras Energy ConsumptionExtrasTotal CalculatedEnergy Consumption(kWh/yr)Dwellings Exhaust Systems5,840Amenities, Back of House& Mechanical Ventilation0Car park Ventilation40,640Lifts32,850Domestic Hot Water GAS MJ/yr292,20221
No energy generation was used in this case study.The results of this case study were as follows:Table 22: Eight Storey Case Study ResultsTotal Benchmark Emissions(kgCO2/yr)249,224Total Benchmark Emissions(kgCO2/pers)2,596Actual Facility Emissions (kgCO2/yr)177,563Actual Facility Emissions(kgCO2/pers/yr)1,850Greenhouse Gas Savings(Difference in greenhouse gasemissions between benchmarkand facility (kgCO2/yr))Number of Points Achieved28.7%1For an equivalent building, a BASIX score of 30%is required to achieve a comparative Green Star pointThis information is entered into the calculatoras detailed in Figure 7.Figure 7: Eight storey residential calculator screen shot (right)22
APPENDIX ASIMULATION BRIEFFOR ASSESSORSIn order to assess the validity of the final results, it is criticalthat the assessor and the simulator understand the limitationsof the simulation package which has been used. The simulatormust provide the assessor with a briefing of the simulationpackage and model used which shows that the followingrequirements have been met: The simul
the Green Star - Multi Unit Residential Energy Calculator as a substitute to filling out the rest of the calculator to determine the Green Star points awarded. This report has been written as a guide to the required Green Star - Multi Unit Residential, and how they should be entered into the Energy Calculator for comparison. 1. introduCtion