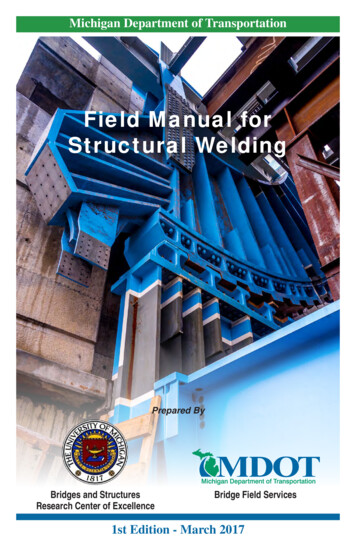
Transcription
Michigan Department of TransportationField Manual forStructural WeldingPrepared ByBridges and StructuresResearch Center of ExcellenceBridge Field Services1st Edition - March 2017
Field Manual for Structural Welding
Table of ContentsGlossary.6Acknowledgement.10Introduction and Purpose.11Governing Specifications.11Arc Welding Processes.13Shielded Metal Arc Welding (SMAW).13Gas Metal Arc Welding (GMAW).14Flux Cored Arc Welding (FCAW).14Submerged Arc Welding (SAW).15Process Selection.16Welded Structural Connections.16Joint Types.17Weld Types.17Groove Welds.17Terminology for Groove Welds.18CJP Groove Weld.19PJP Groove Welds.21Fillet Welds.22Minimum Fillet Weld Size.23Maximum Fillet Weld Size.23End Returns (Boxing).23Fillet Weld Termination.24Fillet Weld Considerations.24Plug and Slot Welds.24Plug and Slot Weld Considerations.25Field Manual for Structural Welding1
General Weld Considerations and Terminology.25Weld Tabs.25Weld Access Holes.26Filler Metal Strength.26Filler Metal Considerations.27Welds and Bolts in Same Connection.27Filler Plates.27Prohibited Joint Types and Welds.28Hydrogen Embrittlement.28MDOT Requirements for Electrodes.29Discontinuities.29Planar Discontinuities.30Volumetric Discontinuities.31Special Considerations for Lap Joints.33Special Considerations for Butt Joints.34Special Considerations for T-Joints.34Special Considerations for Corner Joints.35Weld Cracking.35Types of Weld Cracking.35Shrinkage and Restraint.36Practices to Reduce Shrinkage Stresses.36Practices to Reduce Restraint.37Centerline Cracking.37Segregation-Induced Cracking.37Bead Shape-Induced Cracking.38Surface Profile-Induced Cracking.38Heat-Affected Zone Cracking.38Transverse Cracking.39Limiting Transverse Cracking.39Lamellar Tearing.40Field Manual for Structural Welding2
Distortion.40Angular Distortion.41Transverse Shrinkage .41Longitudinal Shortening.42Twisting.42Longitudinal Sweep or Camber.42Buckling and Warping .43Rotational Distortion.43General Distortion Control Measures .43Specialized Distortion Control Measures.44AWS Distortion and Shrinkage Requirements.44Allowable Dimensional Tolerances.45Fatigue.45Special Fabrication Requirements for Fatigue Resistance.46Galvanized Steel.47Hot-Dipped Galvanized (HDG) Structural Elements.47General Welding Requirements.48Base Metal Preparation.48Assembly.49Fillet Welds.49Plug, Slot and Butt Joints.49Groove Welds.49Peening.50Field Manual for Structural Welding3
Shop Welding.51Requirements for Shop Welding.52Welding Procedure Specification (WPS).52Procedure Qualification Test Record (PQR).54Shop Welded Plate Girders and Rolled Beams.54Shop Splices.55Weld Conditions.55Shop Weld Nondestructive Testing.56Nondestructive Testing – Groove Welds.56Nondestructive Testing – Fillet Welds.57Defective Welds.57Field Welding.58Requirements for Field Welding.58Field Welding Surface Requirements .58Field Weld Nondestructive Testing.59Defective Field Welds.60Special Field Welding Cases.60Weld Positions.61Welder Certification and Endorsement.62AWS Welder Endorsements.62AWS Welder Certification (AWS QC7-93).62AWS Performance Test.63MDOT Welder Endorsements.63MDOT Welder Certification Program (WCP).63MDOT WCP Guidelines.64MDOT Welder Qualification Program (WQP).64Field Manual for Structural Welding4
Economic Welding Practices.65Considerations Based on Weld Types.66CJP Groove Welds.66PJP Versus Fillet Welds.66Mixed PJP-Fillet Welds.66Other Welding Considerations.67CJP Groove Welds.67PJP Groove Welds.67Flare Groove Welds.67Fillet Welds.67Welding Inspection.67Visual Testing (VT).68Penetrant Testing (PT).69Magnetic Particle Testing (MT).70Radiographic Testing (RT).70Ultrasonic Testing (UT).71Weld Repair.72Weld Symbols.72MDOT Bridge Field Services – Contact Information.Back CoverField Manual for Structural Welding5
GlossaryArc Welding – A welding process that produces a coalescence of metalsby heating them with an electric arc.Arc Welding Electrode – A part of the welding system that conductscurrent and ends at the arc.Back Gouging – The removal of weld and base metal from the other sideof a partially welded joint. The objective is to assure complete penetrationupon subsequent welding from that side.Backing – A piece of material placed at the root of a weld joint for thepurpose of supporting molten weld metal.Base Metal – The metal to be welded.Bevel – An angled edge preparation.Butt Joint – A joint between two members lying in the same plane.Complete Fusion – Fusion over the entire fusion faces and between alladjoining weld beads.Complete Joint Penetration – A groove weld condition in which weldmetal extends through the joint thickness.Defect – A discontinuity or discontinuities that, by nature or accumulatedeffect (for example, total crack length or amount of porosity), renders apart or product unable to meet minimum applicable acceptance standardsor specifications.Depth of Fusion – The distance that fusion extends into the base metalor previous bead from the surface melted during welding.Facing Surface – The surfaces of materials in contact with each otherand joined or about to be joined together.Filler Material – The material to be added in making a welded, brazed, orsoldered joint.Fillet Weld – A weld of approximately triangular cross section that joinstwo surfaces approximately at right angles to each other in a lap joint,T-joint, or corner joint.Field Manual for Structural Welding6
Flat Welding Position – A welding position where the weld axis isapproximately horizontal and the weld face lies in an approximatelyhorizontal plane.Flux – Material used to prevent, dissolve, or facilitate removal of oxidesand other undesirable surface substances.Flux Cored Arc Welding (FCAW) – An arc welding process thatproduces coalescence of metals by means of a tubular electrode.Shielding gas may or may not be used.Fusion – The melting together of filler metal and base metal, or of basemetal only, to produce a weld.Gas Metal Arc Welding (GMAW) – An arc welding process where the arcis between a continuous filler metal electrode and the weld pool. Shieldingfrom an externally supplied gas source is required.Gas Tungsten Arc Welding (GTAW) – An arc welding process where thearc is between a tungsten electrode (non-consumable) and the weld pool.The process is used with an externally supplied shielding gas.Groove Weld – A weld made in a groove between two members.Heat-Affected Zone (HAZ) – That section of the base metal, generallyadjacent to the weld zone, whose mechanical properties or microstructurehave been altered by the heat of welding.Hot Crack – A crack formed at temperatures near the completion ofweld solidification.Incomplete Fusion – A weld discontinuity where fusion did not occurbetween weld metal and the joint or adjoining weld beads.Incomplete Joint Penetration – A condition in a groove weld where weldmetal does not extend through the joint thickness.Interpass Temperature – In a multi-pass weld, the temperature of theweld area between p
The purpose of this Field Manual for Structural Welding is to summarize basic definitions, concepts and procedures for welded joints. The manual addresses general considerations for welding, welder certification and inspection procedures. The intent of the manual is to assist engineers,