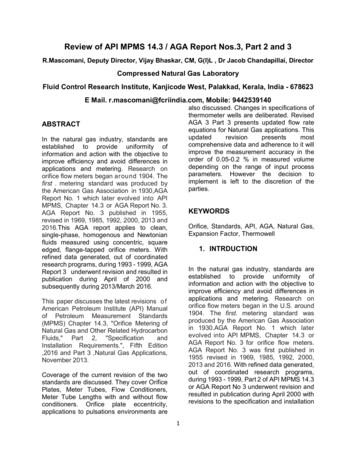
Transcription
Review of API MPMS 14.3 / AGA Report Nos.3, Part 2 and 3R.Mascomani, Deputy Director, Vijay Bhaskar, CM, G(I)L , Dr Jacob Chandapillai, DirectorCompressed Natural Gas LaboratoryFluid Control Research Institute, Kanjicode West, Palakkad, Kerala, India - 678623E Mail. r.mascomani@fcriindia.com, Mobile: 9442539140also discussed. Changes in specifications ofthermometer wells are deliberated. RevisedAGA 3 Part 3 presents updated flow rateequations for Natural Gas applications. Thisupdatedrevisionpresentsmostcomprehensive data and adherence to it willimprove the measurement accuracy in theorder of 0.05-0.2 % in measured volumedepending on the range of input processparameters. However the decision toimplement is left to the discretion of theparties.ABSTRACTIn the natural gas industry, standards areestablished to provide uniformity ofinformation and action with the objective toimprove efficiency and avoid differences inapplications and metering. Research onorifice flow meters began around 1904. Thefirst . metering standard was produced bythe American Gas Association in 1930,AGAReport No. 1 which later evolved into APIMPMS, Chapter 14.3 or AGA Report No. 3.AGA Report No. 3 published in 1955,revised in 1969, 1985, 1992, 2000, 2013 and2016.This AGA report applies to clean,single-phase, homogenous and Newtonianfluids measured using concentric, squareedged, flange-tapped orifice meters. Withrefined data generated, out of coordinatedresearch programs, during 1993 - 1999, AGAReport 3 underwent revision and resulted inpublication during April of 2000 andsubsequently during 2013/March 2016.KEYWORDSOrifice, Standards, API, AGA, Natural Gas,Expansion Factor, Thermowell1. INTRDUCTIONIn the natural gas industry, standards areestablished to provide uniformity ofinformation and action with the objective toimprove efficiency and avoid differences inapplications and metering. Research onorifice flow meters began in the U.S. around1904. The first. metering standard wasproduced by the American Gas Associationin 1930.AGA Report No. 1 which laterevolved into API MPMS, Chapter 14.3 orAGA Report No. 3 for orifice flow meters.AGA Report No. 3 was first published in1955 revised in 1969, 1985, 1992, 2000,2013 and 2016. With refined data generated,out of coordinated research programs,during 1993 - 1999, Part 2 of API MPMS 14.3or AGA Report No 3 underwent revision andresulted in publication during April 2000 withrevisions to the specification and installationThis paper discusses the latest revisions o fAmerican Petroleum Institute (API) Manualof Petroleum Measurement Standards(MPMS) Chapter 14.3, "Orifice Metering ofNatural Gas and Other Related HydrocarbonFluids," Part 2, "SpecificationandInstallation Requirements.", Fifth Edition,2016 and Part 3 ,Natural Gas Applications,November 2013.Coverage of the current revision of the twostandards are discussed. They cover OrificePlates, Meter Tubes, Flow Conditioners,Meter Tube Lengths with and without flowconditioners. Orifice plate eccentricity,applications to pulsations environments are1
requirements for orifice meterssubsequently during March 2016.andNormative ReferencesSymbols, Units, and TerminologyFlow Measurement EquationsFlow Equation Components RequiringAdditional ComputationGas PropertiesAnnex A Adjustments for InstrumentCalibrationAnnex B Factors ApproachAnnex C Flow Calculation ExamplesAnnex D Pipe Tap Orifice MeteringAnnex E SI ConversionsAnnex F Development of Constants for FlowEquationsAnnex G Buckingham and Bean EmpiricalExpansion Factor (Y) for Flange-tappedOrifice MetersThis paper discusses the latest orifice flowmetering standards - American PetroleumInstitute (API) Manual of PetroleumMeasurement Standards (MPMS) Chapter14.3, "Orifice Metering of Natural Gas andOther Related Hydrocarbon Fluids," Part 2,"SpecificationandInstallationRequirements." [1] and Part 3 “ Natural GasApplications [2]. These standards are alsoreferred as A m e r i c a n Gas Association(AGA) Report No. 3, Part 2 and Part 3More than 200 research papers of 30research programs during 1922-1999 isbriefly described Annex A of Part 2. Thisreport applies to fluids that are consideredto be clean, single-phase, homogenous andNewtonian measured using concentric,square edged, flange-tapped orifice meters.The requirements for orifice metering, flowrate calculations, as defined in thispublication, will be discussed in greaterdetail throughout this paper. Many authorshave reviewed the earlier version of thestandards published during 2000 in detail [35]For existing installations, the decision toupgrade to meet the requirements ofupdated standards is left to the discretion ofthe parties involved. The parties must beaware that if a meter installation is notupgraded, measurement bias errors mayexist. Use of the calculation procedures andtechniques of API MPMS Ch.14.3.3/AGAReport No. 3, Part 3, with existing equipmentis recommended, since these representsignificant improvements over the previousmethods. The uncertainty levels for flowmeasurement using existing equipment maybe different from those quoted in earlierversions. This updated revision presentscomprehensive data and adherence to it willimprove the computational accuracy inmeasured volume depending on the range ofinput process parameters. The impact ofrevised expansion factor equation on flowrates for set of process conditions isevaluated. Flow rates calculated results inpositive bias. Orifice Plates, Meter Tubes,Flow Conditioners, Meter Tube Lengths withand without flow conditioners etc. arediscussed.Orifice plate eccentricity,applications to pulsations environments arealsodiscussed.Specificationsofthermometer wells are deliberated.Coverage of Part 2 incudesConstruction and Installation requirementsNormative referencesTerms, Definitions, symbolsOrifice Plate SpecificationsMeter Tube SpecificationsInstallation RequirementsAnnex A Research Projects and TestsAnnex B Orifice Meter Inspection GuidelineAnnex C Specific Installation CalibrationTestAnnex D Flow Conditioner PerformanceTestAnnex E Maximum Allowable Orifice PlateDifferential PressureFigures 1 - 6Tables 1- 8and Part 3 covers2
2. CONSTRUCTION ANDINSTALLATIONREQUIREMENTS(PART 3, SECTION 2) This section outlines the various designparameters for designing metering facilitiesusing orifice meters. The specifiedmechanical tolerances encompass a widerange of orifice diameter ratios for whichexperimental results are available. Use of thecalculation procedures and techniques ofAPI MPMS Ch.14.3.3/AGA Report No. 3,Part 3, with existing equipment isrecommended, since these representsignificant improvements over the previousmethods. The uncertainty levels may bedifferent from earlier versions. Though thestandard covers the diameter ratios (beta)0.1 - 0.75, , minimum uncertainty is achievedfor 0.2 - 0.6 with orifice diameters more than11.43 mm. It is advised to avoid extreme betaratio. Mid-diameter ratio (around 0.4) havethe highest probability of producing the bestmeasurement. A beta ratio of.75 could beused as the design criteria for new orificemeter installations. Achieving the best levelof measurement uncertainty depends onproper design, application of the meteringsystem, maintenance of the meters andadoption of latest equations. The symbols for orifice plate dimensionsare shown in Fig.1. Fig.2 illustrates theallowable departure. Deviations fromflatness shall be 1 % of dam height( )/2 i.e 0.010 in/in of dam heightunder no-flow conditions. Maximum )allowable departure is 0.005(and illustrated in Figs 2a-2c. The surfacesat upstream and downstream faces shallhave no abrasions, scratches visible to thenaked eye that exceed 50andmay be verified by using an electronicaveraging-type / other type surfaceroughness instrument with a cutoff value ofnot less than 0.03 inch.The standard recommends the plate shall beclean, free from accumulation of dirt, ice, grit,grease, oil, free liquid, and other extraneousmaterials. The upstream and downstreamedges of the orifice plate bore shall be freefrom defects visible to the naked eye, suchas flat spots, feathered texture, roughness,burrs, bumps, nicks, and notches. Thesurface of the plate bevel shall have nodefects visible to naked eye, such asgrooves, ridges, pits, or lumps. Regularinspection schedule depending on theservice conditions shall be practiced. Theupstream edge of the orifice plate bore shallbe square and sharp. An estimation ofsuitable sharpness can be made bycomparing the orifice plate bore edge withthe bore edge of a properly sharp referenceorifice plate of the same nominal diameter.The orifice plate bore edge being evaluatedshould feel and look the same as the edge ofthe reference orifice plate.3. TERMS, DEFINITIONS ANDSYMBOLS (PART 2, SECTION 3)The definitions are given to emphasize theparticular meaning of the terms as used inPart 2 such asdiameter ratio, differentialpressure, flow conditioner, meter tubes,orifice plate etc. Symbols and nomenclatureused in the standards are furnished.4. ORIFICESPECIFICATIONSSECTION 4)Orifice plate facesOrifice plate bore edgeOrifice plate bore diameter (dm) androundness (dr)Orifice plate bore thickness (e)Orifice plate thickness (E)Permanent Pressure DropOrifice plate bevel angle ( es f or t h e or if ic e p l at e d es ig na n d t h e key components of an orificeplate. Section covers3
of water column depending on pipe size .Maximum allowable differential pressuresfor the recommended orifice platethicknesses in Table 3 are for operatingtemperatures not exceeding 150 F. The useof an orifice plate thickness other than therecommended thickness is acceptable ineither new or existing orifice plate holdingdevices as long as the thickness is withinthe maximum and minimum range; and theorifice plate eccentricity, bore thickness,differential pressure tap hole, andexpansion-factor pressure-ratio tolerancesand limits are satisfied.Additional guidanceon allowable differential pressure acrossthe orifice plate is provided in Annex E.Guidance is also provided for estimating thepermanent pressure loss across an orificeplate. Permanent pressure loss isapproximated to #(1 % ) . It rangesfrom 96-44 % for beta ratios of 0.2 - 0.75 forlisted maximum differential pressures ofTable 3The allowable tolerance for the orificeplate bevel angle, , is 45 15 . If a bevelis required, its minimum dimension, E-e,measured along the axis of the bore, shallnot be less than 0.0625 inch.The measured orifice bore diameteristhe mean of four or more evenly spaceddiameter measurements at the inlet edge.The roundness tolerances are given in Table1. During measurement, the temperatureshould be within 1 F ( 0.5 C). The orificeplate bore diameter at reference temperature [1 ( isdefinedas)].Linear coefficient of thermal expansionfor orifice plate material are given in Table 2.This edition has revised the coefficients.For SS 304 and 316 , separate values aregiven. The value for Monel 400 has beenrevised (3 %) . Metric Conversions has beenadded in the table. The applicable range oftemperature have been lowered to 32 – 212oF from -100 oF - 300 oF for stainless steeland for Monel, 68 oF – 212 oF. Maximumerror is 0.005 % in flow for SS over thetemperature range between old and newcoefficients.The minimum allowable bore thickness isspecified as 0.01 0.005”whichever is larger. The maximumallowable bore thickness is specified as 0.02 0.125whicheverissmaller; but e shall not be greater than themaximum allowable orifice plate thickness,E. When the orifice plate thickness (E)exceeds the orifice bore thickness (e), abevel is required on the downstream side ofthe orifice bore.Orifice plate bores thatdemonstrate any convergence from inlet tooutlet are unacceptable.5. METER TUBE SPECIFICATIONS(PART 2 SECTION 5)The meter tube consists t h e straightlength of pipe upstream of the orifice of thesame diameter, including the flowstraightener/conditioner, the orifice plateholder and the similar downstream pipebeyond the orifice plate. Allowabletolerances are provided for the meter tubesurface roughness. Guidance is alsoprovided on where to measure surfaceroughness along the meter tube. Metertubesurfacesthataretoohydrodynamically "smooth" or "rough" willresult in a flow measurement bias error.Allowable differential pressure limits variesand are function of beta ratio, pipe sizes,plate thickness, plate material, mechanicalstrength, acceptable expansion factor,uncertainty. Maximum acceptable permanentpressure loss and allowable differentialpressures a r e as high as 1000 “ WC.Theminimum,maximum,andrecommended values of orifice platethickness (E) for Types 304 and 316 SSorifice plates are given in Table 3. Themaximum allowable differential pressure isi n t h e r a n g e o f 1 8 0 - 1,000 inchesProper meter tube inside surfaceroughness is required to assure accuratemeasurement. The surface roughness4
requirement for meter tubes of 12” or less is300 μin Ra when βr 0.6, 250 μin Ra whenβr 0.6 and Minimum Ra is 0.34 μin.Thesurface roughness requirement for greaterthan 12 “ pipe is 600 μin Ra when β r 0.6, 500 μin Ra when β r 0.6 and MinimumRa is 0.34 μin. Irregularities such asgrooves, scoring, or ridges resulting fromseams, welding distortion, offsets, and thelike that affect the tolerance in excess ofthat allowed are not permitted. Theexistence of pits in the surface of the metertube, although undesirable, are allowedprovided their individual measurements donot exceed the surface roughness and/ordiameter tolerance requirements of themeter tube and do not compromise themeter tube’s pressure integrity. When thesetolerances are exceeded, the irregularitiesmust be corrected. The increase in themeter tube surface wall roughnessrequirement should not be interpreted asreducing the need to maintain clean metertubes. Due care shall be exercised to keepthe meter tube interior clean and free fromaccumulation of dirt, ice, grit, grease, oil,free liquid and o
AGA Report No. 3 published in 1955, revised in 1969, 1985, 1992, 2000, 2013 and 2016.This AGA report applies to clean, single-phase, homogenous and Newtonian fluids measured using concentric, square edged, flange-tapped orifice meters. With refined data generated, out of coordinated research programs, during 1993 - 1999, AGA Report 3 underwent revision and resulted inFile Size: 1MBPage Count: 14