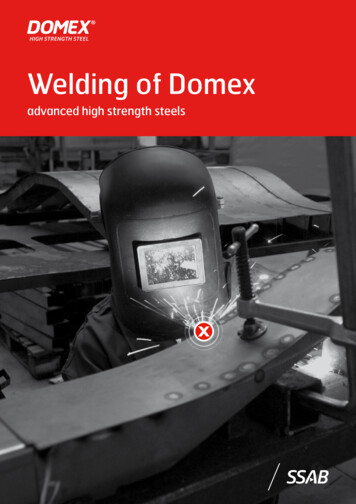
Transcription
Welding of Domexadvanced high strength steels
2
IntroductionFor many years, fusion welding has been employed for the welding of DomexAdvanced High Strength Steels. Compared with the fusion welding of mildsteels, the process does not differ significantly. However, in order to maximizethe benefits of these high strength steels, the welding process must still becontrolled in a suitable manner. The following pages offer useful informationabout welding with Domex from SSAB. The advice and information here canhelp you to achieve optimal welding results, which allow you to experiencethe full potential of your choice in Domex from SSAB.ContentsDomexJoint preparationWeldingWelding methods for DomexHot cracks and lamellar tearingHydrogen crackingCarbon equivalentEN 1011-2Filler metals for DomexStatic Strength of welded jointsHeat inputInterpass temperatureSoft zonesResults of mechanical testingImpact toughness of welded jointRecommendations in order to minimize distortionStress relief annealingHot straightening4677788891111111213141415153
Domex120011001000Yield strength, N/mm2Domex is the brand name for hot-rolled sheet steelsfrom SSAB. These steels are supplied in the thicknessrange 2–16 mm, and due to their exceptional formabilityin a cold state, they are also known as cold-forming steels.Domex steels are characterized by high yield strength,excellent formability and good weldability. These qualitiesmake them optimal for use in the transportation industry(trailers, trucks, tippers, automotive, trains and cranes).Domex steels are available in the yield strength levelsshown in figure 1. Their mechanical properties and chemicalcomposition can be seen in tables 1 and 2.900800700600500400460500355300Figure 1 Strength of Domex.4550MC600650700
Table 1 Mechanical properties of Domex.Mechanical PropertiesSteel gradeDomex 355 MCYield strengt Reh(MPa)Tensile strengthRm (MPa)Elongation Min. (%)Bending radius, minimum in 90 bend.minimumminimumA80 t 3A5 t 3t 33 t 6t 6355430–55019230.2 x t0.3 x t0.5 x tDomex 420 MC420480–62016200.4 x t0.5 x t0.8 x tDomex 460 MC460520–67015190.5 x t0.7 x t0.9 x tDomex 500 MC500550–70014180.6 x t0.8 x t1.0 x tDomex 550 MC550600–76014170.6 x t1.0 x t1.2 x tDomex 600 MC600650–82013160.7 x t1.1 x t1.4 x tDomex 650 MC650 *700–88012140.8 x t1.2 x t1.5 x tDomex 700 MC700 *750–95010120.8 x t1.2 x t1.6 x tDomex 550 W550600181.0 x t1.5 x tDomex 700 W700750122.0 x t* For thickness above 8 mm the minimum yield strength may be 20 MPa lower.Table 2 Chemical composition of Domex.Chemical compositionSteel gradeC (%)maximumSi (%)maximumMn (%)maximumP (%)maximumS (%)maximumAl (%)minimumCEVTypicalCETTypicalDomex 355 MC0.100.031.500.0250.0100.0150.260.18Domex 420 MC0.100.031.500.0250.0100.0150.300.20Domex 460 MC0.100.101.500.0250.0100.0150.310.20Domex 500 MC0.100.101.600.0250.0100.0150.320.22Domex 550 MC0.120.101.800.0250.0100.0150.320.16Domex 600 MC0.120.101.900.0250.0100.0150.340.21Domex 650 MC0.120.102.000.0250.0100.0150.370.23Domex 700 MC0.120.102.100.0250.0100.0150.390.25Domex 550 W0.100.151.500.120.0100.0500.370.19Domex 700 W0.120.602.100.0300.0100.0500.480.26The sum of Nb, V and Ti is max. 0.22 %, Mo is max 0.5 %, and B is 0.005 % max.5
Joint preparationAll conventional methods for joint preparation can readilybe used with these steels. However, the most commonmethods are: Machining Thermal cuttingMilling and thermal cutting (gas, plasma or laser cutting)are the most common methods used for joint preparation.Joint preparation for Domex Advanced High Strength Steelsis as easy to perform as it is on mild steels. No preheating isneeded for thermal cutting, however, it is important to notethat a thin oxide film may form on the joint surface produced6by thermal cutting. It is recommended to remove this filmbefore welding.If plasma cutting is used for joint preparation, it is recommended that oxygen be used as the plasma gas. If nitrogen isused, it can be absorbed at the cut surfaces of the steel, whichmay cause porosity in the weld metal. The solution lies inusing oxygen as the plasma gas, or by grinding down the cutsurfaces by at least an approximate 0.2 mm before welding.If thin sheet steel parts are to be weldedtogether, ordinary shearing can be used as joint preparation.
WeldingWelding methods for DomexAll common fusion welding methods can be employedfor welding Domex Advanced High Strength Steels.Examples of welding methods that can be used are: MAG-welding (Metal Active Gas), (GMAW) MMA-welding (Manual Metal Arc), (SMAW) TIG-welding (Tungsten Intert Gas), (GTAW) Plasma welding Submerged arc welding Laser weldingDomexSteel with high slag contentFigure 2 Lamellar tearing. Difference between a steel with high slaginclusions and Domex steels.Welding methods other than those mentioned above may alsobe used. However, of the methods mentioned, MAG-weldingis the most commonly used welding method in the industrytoday. One of the reasons for this is because MAG-welding isvery easy to automate (high productivity).Hot cracks and lamellar tearingSince Domex steels have a very low content of alloying elements and a low amount of inclusions, there is a low risk fordefects such as hot cracks and lamellar tearing. These defectscan sometimes occur in steels with a higher content of nonmetallic inclusions. Good sulphide shape control for Domexsteels enhances the properties in the thickness directioncompared to steels with a high content of solid inclusions,see figure 2.When a T joint (see figure 3) is welded close to the edge ofDomex steel with a yield strength 600 MPa, and a thicknessof 8 mm, it is important that there are no sharp defects atthe edge. Stresses that occur in the thickness direction duringwelding can give rise to cracking of the sheet. Since shearingcan produce sharp stress raisers in the edge, it is preferable touse thermal cutting to produce an edge with a better surfacequality.Edge produced by thermal cutting.Figure 3 It is recommended to use thermal cut edges in T-jointswith welds close to the cut edge.7
Hydrogen crackingThe risk of hydrogen cracking (cold cracking) occurring inDomex is very low. The reason for this is due to: Very lean steel composition and thin sheets (slow cooling),which reduce the occurrence of brittle structures; The avoidance of high stresses, since thin sheet joints areless stiff than thick plate joints; Lower hydrogen contents, since hydrogen can diffuse morereadily from the sheet.Carbon equivalentThe risk of hydrogen cracking during welding is linked to theamount of alloying elements in the steel. Different variants ofcarbon equivalent formulas are used to describe the amountof alloying elements in conjunction with fusion welding. Thetwo most common are CEV or CET.CEV C Mn Cr Mo V Cu Ni 6515CET C Mn Mo Cr Cu Ni 1020400.500.45Carbon equiva. CEV (%) S235JR S275JR S355J2These steels, according to EN 10025-2:2004 are very common,have long been used in welded structures, and are very easy toweld. There is a low risk of hydrogen cracking in thin sheetsof these steels. Although the yield strength of cold formingsteels is well above that of steels in EN 10025-2:2004, the CEVvalues are not much higher. In other words, this means thatthe risk of hydrogen cracking of Domex cold forming steels isno higher than that of the conventional weldable steels in EN10025-2:2004.EN 1011-2EN 1011-2 (recommendations for welding of metallic materials) is a standard partly used for accessing the risk for hydrogen cracks occurring in the welded joint during fusion welding. The standard specifies the working temperature neededto avoid cold cracking. The input data used for the evaluationare; the sheet thickness, type of weld (e.g. fillet weld), heatinput, and hydrogen content of the weld metal.For example, according to EN 1011-2, a very high hydrogencontent ( 15 ml/100 g weld metal) of the weld metal and anextremely low heat input ( 0.5 kJ/mm), together with a combined thickness of 30 mm for Domex 700 MC are requiredto promote these types of cracks to occur. If electrodes thatproduce low hydrogen contents ( 10 ml/100 g weld metal) areused, which is recommended by SSAB for these steels, no coldcracking problems will arise. No preheating is necessary evenfor the thickest dimensions of Domex.It is of course important to follow the general recommendations to avoid an increased risk for the occurrence ofhydrogen cracks, including:CARBON EQUIVALENT VS YIELD STRENGTH.TYPICAL VALUES FOR T 5 mm.0.400.350.300.250.20EN 10025-2:2004Domex MC0.150.10200300400500600700Yield strength (MPa)800900Figure 4 Relationship between carbon equivalent (CEV) and yieldstrength (MPa of Domex compared to the conventionalsteels in EN 10025-2:2004 (thickness 5 mm).8Figure 4 shows the relationship between the carbon equivalent CEV and the yield strength of Domex and the standardized steels of the European Standard EN 10025-2:2004.Examples of conventional steels according to EN 10025-2:2004are: Good welding circumstances. Keep the welded joint freefrom moisture, rust, oil, etc. Make sure that there is no ice/white frost or condensationin the joint Handle the filler metal in accordance with the supplier’srecommendations.
Filler metals for DomexThe filler metals recommended for Domex are listed infigure 5.If the stresses acting on the weld are very high and thetensile strength of the weld is required to be equal or close tothe requirements of the parent material, we recommend usingmatching filler metals. Under-matched filler metal can oftenalso be used for Domex in the following typical cases: When the weld is in a low-stress areaFor fillet welds (compensate by larger throat thickness)For welding to an ordinary mild steelIf the weld reinforcement is not removedIn most joints subjected to fatigue loadsIf lower hardness of the weld metal is desired(easier milling of weld metal).Yield Strength (MPa)700AWS: A5.28 ER100S-XAWS: A5.28 ER110S-XEN 16834(-A) 69XAWS: A5.29 E11XT-XEN 18276(-A) T69XAWS: A5.28 ER100S-XAWS: A5.28 ER110S-XEN 16834(-A) G 62X600AWS: A5.5 E11018EN757 E69XAWS: A5.23 F11XEN 26304(-A) S69XAWS: A5.5 E11018EN757 E62XAWS: A5.23 F11XEN 26304(-A) S62XAWS: A5.28 ER100S-XAWS: A5.28 ER90S-XEN 16834(-A) G 55XAWS: A5.29 E10XT-XAWS: A5.29 E9XT-XEN 18276(-A) T55XEN 16834(-A) T50XAWS: A5.5 E100XEN757 E55XEN 2560 E50XAWS A5.23 F10XEN 26304(-A) S55XEN 756 S50XAWS: A5.23 F9XAWS: A5.28 ER80S-XEN 14341(-A) 50XEN 14341(-A) G 46XAWS: A5.29 E8XT-XEN 16834(-A) T46XEN 16834(-A) T42XAWS: A5.5 E80XEN 2560(-A) E46XEN 2560(-A) E42XAWS: A5.23 F8XEN 756 S46XEN 756 S42XAWS: A5.23 F7X500400Domex 700 MCDomex 650 MCDomex 600 MCDomex 550 MCDomex 500 MCDomex 460 MCDomex 420 MC300Domex 355 MCAWS: A5.28 ER70S-XEN 14341(-A) G 42XMAG WeldingSolid wireAWS: A5.5 E70XMAG WeldingCored wireMMA WeldingCoated electrodeSubmergedarc weldingFIGURE 5 Recommended filler metals for Domex.9
A large number of solid wires for MAG-welding of Domexare available on the market, in yield strengths ranging from355 to 700 MPa.If cored wires are intended to be used, rutile cored wiresare recommended. Rutile cored wires are easier to weld andthey normally provide a much better surface appearance thanbasic cored wires. Basic cored wires are primarily used if theimpact toughness requirements on the product are very high.Basic electrodes are recommended for MMA-welding ofDomex. The risk of cold cracking (caused by hydrogen embrittlement) in the HAZ (heat affected zone) is then very low,even for Domex with the highest yield strength. Preheating isnot necessary.If submerged arc welding is used for Domex, it is recommended that a basic flux should be used together with a wirethat provides the required mechanical properties.It is very important to follow the storage recommendationssupplied by the filler metal manufacturer in order to minimizethe risks of weld defects and to achieve the required mechanical properties. Electrodes that, for example, have been storedwithout protection in the workshop, can absorb moisture fromthe air, which can lead to high hydrogen contents in the weldmetal, with increased risk for hydrogen cracking. SSAB recommends electrodes/filler metals that give maximum hydrogencontent in the weld metal according to table 3.10table 3 Recommended max. hydrogen content of the weld metal.Steel gradeMaximum hydrogen content ml/100 g weld metalDomex 355 MC30Domex 420 MC30Domex 460 MC10Domex 500 MC10Domex 550 MC10Domex 600 MC10Domex 650 MC10Domex 700 MC10Domex 550 W10Domex 700 W10
Static strength of welded jointsIn order to reach the required tensile strength of the weldedjoint, both the weld metal and the HAZ must have sufficientstrength. Several factors affect the strength of the welded jointe.g. filler metal used (matched or under-matched), chemical composition, heat input, interpass temperature etc. Thestrength of the weld metal (MPa) is mainly determined by thefiller metal used whereas the strength of the HAZ is more orless determined by the cooling cycle (Δ t8/5).Heat inputThe heat input in fusion welding is the amount of heat supplied to the material during welding. The following formulais generally used for calculating the heat input:E U I 60kJ/mmv 1 000Where: U voltage (V)I current (A)v welding speed (mm/min)Since the energy input to the material is of most interest, allenergy inputs given in this brochure will be Q (i.e. taking thearc efficiency factor into account).Q k EWhere: k arc efficiencyThe approximate values of k for different welding methodsare as follows, see table 4.table 4 Arc efficiency for different welding methods.Welding methodkMAG0.8MMA0.8Submerged arc welding1.0TIG0.6By using the SSAB software WeldCalc, one can easily calculatethe heat input for the specific joint type, taken into accountthe material and weld method.Interpass temperatureMultipass welding may cause the temperature in the weldedjoint to rise to a level that is harmful to the material, which inturn causes the stren
Domex steel with a yield strength 600 MPa, and a thickness of 8 mm, it is important that there are no sharp defects at the edge. Stresses that occur in the thickness direction during welding can give rise to cracking of the sheet. Since shearing can produce sharp stress raisers in the edge, it is preferable to use thermal cutting to produce an edge with a better surface quality .File Size: 1MBPage Count: 16