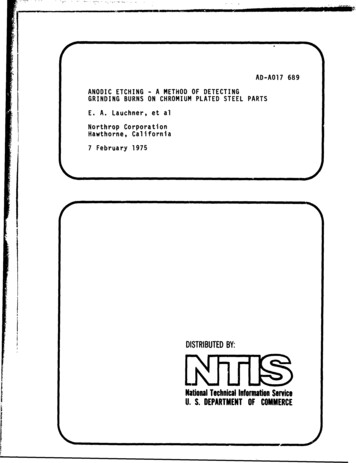
Transcription
AD-AO17 689ANODIC ETCHING - A METHOD OF DETECTINGGRINDING BURNS ON CHROMIUM PLATED STEEL PARTSE. A. Lauchner,et alNorthrop CorporationHawthorne, Califo1n9a.7 February 1975I'DISTRIBUTED BY:National Technical Informaton ServiceU.S.DEPARTMENT OF COMMERCE
33510O04iii1pprr;',"2 or public relokNORTHROP- R.p,.du,.d bV NATIONAL TECHNICALSERVICE:INFORMATIONUS Depaflment of Com- trc.Spo-yl,eld. VA 2 21 1
Northrop CorporationAircraft DivisionNOR-75-33ANODIC ETCHING - A METHOD OFDETECTING GRINDING BURNS ON CHROMIUMPLATED STEEL PARTS7 February 1975PREPARED BYE. A. LauchnerMetallurgical EngineeringG. A. AndrewsQuality Technical SupportAPPROVED BYL.o!!.bu'i(-, U-1,1';F. NGEIDATEORIGINATING DEPARTMENTPAGSS AFFECTED OR REMARKS
NORTHROPAirafat DivisionNOR-75-337 February 1975.ABSTRA",Anodic etching, a method for "atect'ing abusive grindingdamage on chromium plated steel p its, is evaluated.Anodic etching procedure foý, inspecting chromium platedsteel pins wag studied and the i-1 ianism of the anodic etch burnindication is discussed.In adWi'ion, the results of magneticparticle and penetrant inspect'. niof the pins is presented.The results indicate thai "busive grinding of chromiumplate can cause cracks or burns in the plate or base metal thatare not detected by conventional inspection techniques.etching is a useful technique for determining ifhas been burned by abusive grinding.Anodicchromium plateIf the plate is burned,further investigation is required to determine whether the basemetal is burned or cracked.ii
NORTHROPAircraft ivisonNOR-75-327 February 1973CONTENTS"PAGEABSTRACT .iCONTENTS .iii.LIST OF TABLES .ivLIST OF ILLUSTRATIONS .iv1.INTRODUCTION .12.OBJECTIVE .33. CONCLUSIONS.34.RECOMMENDATIONS5.PROCEDURE .6.5.1Initial Inspection5.25.3Anodic EtchingInspectionRESULTS AND DISCUSSION .6.16.26.3448Initial InspectionAnodic EtchingInspection7. REFERENCES .APPENDIX A .iii14AI-A6
s4NORTHROPAerftfSNOR-75-337 February 1975LIST OF TABLESPAGETABLE1MATERIAL REMOVED BY ANODIC ETCHING .152SURFACE FINISH OF CHROMIUM PLATE ANODICETCHED .15RESIDUAL STRESS MEASUREMENTS .163LIST OF ILLUSTRATIONSPAGEFIGURE1CHROMIUM PLATED MAIN WING ATTACH PIN USEDFOR TEST PROGRAM .17INDICATIONS REVEALED BY MAGNETIC PAkTICLEINSPECTION ON THREE DIFFERENT CHROMIUMPLATED PINS .183GRINDING DAMAGE ON CHROMIUM PLATE REVEALED BY19ANODIC ETCHING .4MUD CRACK PATTERN IN DAMAGED AREA OF CHROMIUMPLATE REVEALED BY ANODIC ETCHING .5SURFACE OF NORMAL CHROMIUM PLATE AFTER ANODICETCHING . .621SEM PPOTOGRAPHS OF CHROMIUM PLATED SURFACEAFTER ANODIC ETCHING .72022PHOTOMICROGRAPHS OF CHROMIUM PLATED STEELAFTER ANODIC ETCHING .(CONTINUED)iv237ivi.
4NORTHROP--Aircraft DivisionNOR- 75-337 February 1975LIST OF ILLUSTRATIONS (Continued)PAGE"FIGURE8INDICATIONS REVEALED AFTER ANODIC ETCHINGOF THREE DIFFERENT CHROMIUM PLATED PINS91024.MAGNETIC PARTICLE INSPECTIOI ON PIN AFTERVARIOUS OPERATIONS .25BURNS REVEALED BY NITAL ETCHING OF BARESTEEL AFTER STRIPPING CHROMIUM PLATE .264-V4
NORTHROPArcmft D sWNOR-75-337 February 1975*1. INTRODUCTIONThe aircraft industry has been plagued with the problem ofburning high strength steel parts by abusive machining orgrinding.Burns on steel parts degrede the fatigue propertiesof the base material, and many service failures have beenattributed to this type of burning.Nital etching has been usedas a method to detect burns on steel surfaces.However, abu-sive grinding of chromium plated steel parts can also cause.burns beneath the plate on the steel surface (Ref.1 and 2).Abusive grinding of chromium plate results from an exces-Ssive rate of metal removal or inadequate cooling of the workpiece during the grinding operation.Friction generated betweenthe grinding wheel and the chromium plate causes heat to buildup locelly to very high levels.Since chromium and steel havelow thermal conductivity, the heat is not conducted away adequately.The heat builds up in the plate and the steel, causingretempering or rehardeninR burns in the steel.The industry has tried to exercise close control overgrinding of chromium plate, and therefore to minimize thetendency to produce chermal damage.Precise manufacturing andprocess controls have been imposed to control the feeds,and coolants used when grinding chromium plate.are necessary.speedsThese controlsHowever, the controls are not entirely adequateas damage can still occur due to improper grinding.There
[VNORTHROPA tftvDihkNOR-75-337 February 19751. INTRODUCTION (Continued)has been no adequate nondestructive inspection techniqueavailable'to determine if burns exist on the surface of thesteel part beneath the chromium plate.Current techniques for inspection, such as the magneticparticle method, are only effective in detecting large grindingchecks (indications of base metal. cracks evident through thechromium plate).Chromium plate in thicknesses above 0.0007inch reduces the crack detection capability of magnetic particleinspection (Ref. 3).3The loss of detection is more pronouncedabove 0.003 inch of plate.Regardless of plating thickness,small fine cracks beneath the chromium plate are usually notdetected.Itis important to repeat that magnetic particleinspection will not detect damage that has not caused cracksbeneath the chromium plate.A new process for detecting abusive grinding damage onchromium plate has recently been developed (Ref. 4).Theprocess, called "Anodic Etching", utilizes an alkaline solutionand a high current density to etch (strip) the smearedchromium from the plated surface.Initial evaluations haveshown anodic etching to be a practical way of detecting thermaldamage on chromium plate caused by abusive grinding.If theplate is damaged, further investigation of the base metal is9indicated.2
NO'ROPrcraft DMo7 February 19752.OBJECTIVEThe object of this program was to determine ifthe anodicetching technique will detect burns on steel through the chroviiumplate.The fundamental mechanism of the technique was cvalua:ed,and the processing requirements necessary to implement the inspection procedure into.production were determined.Also,thecapabilities of magnetic particle and penetrant inspection wereevaluuted as aids in inspecting chromium plated steel parts forcracks.'3.COr:LUSIONS1. The present practice of plating parts oversiop and grindingto final dimensions is unsatisfactory.Abusive grinding cancause cracks and burns in the base metal that are usually notdetected by conventional inspection procedures.2.Anodic etching of ground chromium plated steel parts is auseful technique for de.armining whether or not the chromium"plate has been damaged.If the plate is damaged, furtherinvestigation is required t6 determine whether the basemetal is burned or crac)ked.3.Fluorescent magnetic particle .Uiis more sensitivethan the black oxide method for detecting grinding checkson chromium plated parts.3
NORTHROP,Akd.ftoiSIoNOR- 75-337 February 1975-3.4.CONCLUSIONS (Continued)High intensity magnetic particle inspection will not detectbase metal cracks through chromium plate any better thannormal magnetic particle inspection.4.RECOMMENDATIONSThere are two alternatives to the present procedure of finishgrinding parts chromium plated oversize to reduce the danger ofgrinding burn damage:1.Anodic etch inspection should be implemented on partschromium plated and ground, or2.Parts should be chromium platad to size to eliminatethe grinding.5.5.1PROCEDUREINITIAL INSPECTIONFour steel pins were selected for evaluation that werescrapped due to.evidence of grinding checks on the chromiumplate.These pins were made from 300M bar ana were heattreated to 280 to 300 ksi ultimate strength.They werechromium plated on the 1.75 inch diameter to a thickness of0.003 inch 0.0001. A typical pin isshown in Figure 1.of the pins were identified as 1,2,3,or 44Eachby vibratory etching
NORTHROP .po,iVonNOR-75-337 February 1975,.5.PROCEDURE (Continued)on the head end.The pins were vapor degreased and cleaned.They werefluorescent magretic particle inspected using boch head and coiltechniques at 1800 and 6000 amperes current respectively.The pins were aemagnetized and solvent cleaned, after inspection.Pins 1, 2, and 3 were magnetic particle inspected usingboth fluorescent and black oxide particles.taken of the indications produced.Photographs wereHigh intensity magneticcurrents of 2800, 4000, and 5000 amperes were also evaluated.Penetrant inspection was attempted on all four pins.lHowever, no indications of cracks could be detected throughthe chromium plate.Residual stress measurements on pin number four were takenon four different areas on the chromium plate using the RigakuStrain Flex machine.5.2ANODIC ETVHINGAll four pins were anodic etched.Limpositions were evaluated.Two different bathOne contained sodium hyiroxideand potassium pyrophosphate; the other contained sodium carbonate and sodium hydrcxide.Preliminary tests showed that bothsolutions etched the chromium plate equaliy well.cause of difficulty in mixing the ,yrophospiate,However, bethe higher so-lution content of chemicals required, and the higher cost, all5
NORTHROPAircraft DivisionNOR-75-337 February 1975.5.subsequent testsPROCEDURE (Continued)are performed using the carboiiate and hydrox-ide solution.Various times for etching such as 45, 90, 130, 450 secondswere evaluated initially.However, 45 seconds appeared to givean adequate etch, and longer times tended to remove excessivechromium plate.Subsequent etching on the four pins was per-formed using a 45 second etch time.The anodic etching solution control parameters are asfollows:"Sodium Carbonate-Sodium HydroxideCurrent density-9 to 20 ounces per gallon5 to 10 ounces per gallon2.5 to 3.5 amperes perBath temperatureEtching time-square inch65 to 110 F-45 to 60 secondsAlkalinity-pH 11-12, 20-300 BaumeThe procedure for anodic etching consisted of the following:1. Vapor degrease or solvent wipe pins.2.Attach electrical contacts made of braided copper wire.3.Mask all areas not requiring etching with peelableLnaskant or tape.4.Hand clean chromium plated area using cheesecloth and1 to 5 micron aluminum oxide abrasive cleaner.5.Water rinse.Check for water breaks.6
NORTHROPAircraft DivisionNOR-75-337 February 19755.6.PROCEDURE (Continued)Immerse in alkaline cleaner at 130 to 180 F for 3minutes.7.Hot water rinse.Inspect pins for a water-break-freesurface.8.Immerse pins in anodic etching solution.9.Electrolyze pins for 45 to 60 seconds at a currentdensity of 2.5 to 3.5 amperes per square inch of exposed chromium plate using the pins as an anode.10.Remove part from etchant and remove masking materials.ii.Rinse in hot water.12.Inspect pins for adequate etch and for evidenceDry thoroughly.,fgrinding burns.5.3INSPECTIONThe diameter of pin number one was measured after variousetching times before and after etc.iing.In addition the surfacefinish of the pin was evaiu.:t:cd both before and after etching.Pins 1, 2, and 3 were inspected after anodic etching bythe magnetic particle and penetrant nitthods.taken.Photographs wereThree pins were penetrant inspected using WP-167 fluor-escent penetrant.The pins were soaked for 5 minutes, washed,examined tinder an ultraviolet light, dried, lightly coated withnonaqueous developer and examined again.A special techniquewas also used of washing under the ultraviolet light until allindication of penetrant was removed, wiped dry, and then7
NORTHROPtp,,NORTROPAircraft,0rDivisionNOR-75-337 February 19755.PROCEDURE (Continued)examined.Photographs were also taken of the indications revealedby anodic etching.Pin numder four was stripped of chromium plate after etching using an alkaline stripper.particle inspected.The pin was then magneticIn addition, the pin was nital etch in-spected to reveal burns on the steel surface.Photographswere taken.Residual stress measurements were taken on pin number four,after stripping of chromium, in the same areas measured before,except, the Fastress machine was used.6.6.1RESULTS AND DISCUSSIONINITIAL INSPECTIONCrack inuications revealed by fluorescent and black oxidemagnetic particle inspection are shown in Figure 2.There isa significant difference in crack indications revealed by theblack oxide versus fluorescent techniques.The indicationsshown by the fluorescent method are more distinct and easierto evaluate due to the inherent color contcast.The high intensity magnetic current inspection techniquesevaluated were not successful in detecting any additional cracks,8
NORTHROPAircraft Division7 February1975NOR-75-33S 6.RESULTS AND DISCUSSION (Continued)The high intensity currents caused excessive background (nonrelevant) indications.Therefore, no further gain in true in-dications could be certain.Penetranl inspection on the chromium plated pins was alsoinvestigated.Excessive penetrant bleedout caused jy inherentchromium plate porosity, and grinding smears on the platecaused unsatisfactory results for this inspection technique.6.2ANODIC ETCHINGThe appearance of pin number four after anodic etching isshown in Figure 3.The removal of the smeared chromium plate,caused by the grinding of the pin, leaves a dull matte finishon the chromium plate.If the chromium plate is damaged, itnormally evident immediately after anodic etching.isIf a burndoes exist on the plate, the burn can be seen due to d
The procedure for anodic etching consisted of the following: 1. Vapor degrease or solvent wipe pins. 2. Attach electrical contacts made of braided copper wire. 3. Mask all areas not requiring etching with peelable Lnaskant or tape. 4. Hand clean chromium plated area using cheesecloth andAuthor: E A Lauchner, G A AndrewsPublish Year: 1975