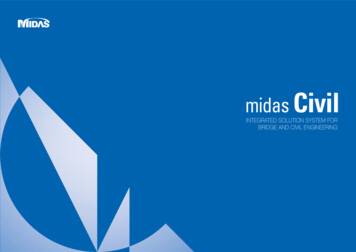
Transcription
midas CivilINTEGRATED SOLUTION SYSTEM FORBRIDGE AND CIVIL ENGINEERING
midas CivilIntegrated Solution Systemfor Bridge and Civil Engineering
0102Unique modelling toolsSpecialized on high-end analysisAdvanced bridge wizard such as Box Culvert, FCM,ILM, FSS, MSS, Grillage, Cable Stayed Bridge WizardSegmental post-tensioning including prestress lossesand camber resultsPowerful moving load optimizerCable force tuning in forward stage analysis andsuspension bridge analysis with geometric nonlinearityAuto-generation of rail track analysis modelsUniqueSpecializationAccurate seismic performancereflecting nonlinearpropertiesWhymidas CivilBridging Your Innovations to Realities0304Practical design featuresPractical modelling features such as SPC, TendonTemplate and Transverse Model WizardRC/Steel/PSC/Composite section design as perEurocodes, AASHTO and other standardsBridge load rating for PSC box and composite girderMaximized productivityPracticalProductivityUser-friendly GUI with high speed graphic enginePresenting input data in Works Tree and manipulatingthe data by Drag & DropExcel compatible input & output tablesAutomatic generation of analysis and design reports
03INTEGRATED SOLUTION SYSTEM FOR BRIDGE AND CIVIL ENGINEERING1. Innovative User InterfaceStretch your imagination & extend your ideas without restrictions.midas Civil will help you achieve the goals.Works TreeRibbon MenuIcon ToolbarsContext MenuFull graphical representationof all shapesTask PaneA new concept tool, which enables the user tofreely set optimal menu systemsDisplay of line & plane typesection shapesCombined analysis results &design displayA new concept menu system comprisingfrequently used menusProcedural sequence defined by the userfor maximum efficiencyLinks to corresponding dialogue boxesfor ease of checking input dataWalk Through ModeModel rendering provided in various view pointsHidden view processing ofa user-specified sectionEase of modelling in CivilData input via main menu ribbon interfaceQuick mouse access from context menuModelling by command inputTabular data entry directly from excelDynamic interaction between works treeand model windowCommand LineModelling function similar to autoCAD commandsModelling by one key commandsmidas CivilBridging Your Innovations to RealitiesOutput WindowTables
INTEGRATED SOLUTION SYSTEM FOR BRIDGE AND CIVIL ENGINEERING2. Optimal Solutions for BridgesDesign process for bridgesOne stop solution for practicing bridge engineersWith RC, steel, PSC and Composite designReinforced concrete design(beam / column)RC design as per Eurocode 2-2, AASHTO LRFD and other codesAnalysisDesignOptimal solution provided for analysis & designIterative analyses for calculating optimal sections & rebarsColumn checking for user-defined sectionsDesign check for maximum forces with corresponding force componentsIterative ProcessModellingAnalysisDesignRC Designs Beam / column section checks Irregular column section designs Auto-recognition of bracedconditions of columnsSteel Designs Stress calculations foruser-defined sectionsComposite SteelGirder DesignPSC DesignComposite PSC Designs Flexural Strength Checks Flexural strength checks Coming Soons Vertical Shear Resistance Checks Shear strength checks Combined stresses due toaxial & bending(all sections in database)s Lateral Torsional BucklingResistance checks Torsional strength checks To handle PSC -I and T girderswith concrete decks ofdifferent gradess Combined stresses due tobending & shear(all sections in database)s Design check with rebars,transverse and longitudinalstiffenerss Steel section Optimisations Fatigue strength checkOptimised Designs Reinforcing steel calculation& tendon checks Summary of constructionstage resultss Crack Width limit checkRC section check summary reportRC section check detail reportmidas CivilBridging Your Innovations to Realities04
05INTEGRATED SOLUTION SYSTEM FOR BRIDGE AND CIVIL ENGINEERING2. Optimal Solutions for BridgesSteel designDynamic report generatorSteel combined stress check as per Eurocode 3-2, AASHTO LRFD and other codesmidas Civil enables the user to auto-generate an MS Word report using analysis and design resultsStress checks for user-defined sectionsAll the input and output data can be plotted (ie. material properties, section properties, reactions, memberAutomatically searches for the optimized steel section with minimal section areaforces, displacements, stresses, section verification results, etc.) in a diagram, graph, text or table format(minimal weight) whilst satisfying the design strength checksThe report updates itself automatically when changes are made in the modelSection types in databaseUser-defined irregular sectionsReporting dynamic imagesMS Word reportReporting dynamic input/output tablesGraphical results of stress checksmidas CivilBridging Your Innovations to Realities
INTEGRATED SOLUTION SYSTEM FOR BRIDGE AND CIVIL ENGINEERING3. Composite Girder Bridge DesignComposite action withconstruction stage analysisProcedure and main features forsteel composite girder bridge designComposite action withconstruction stage analysisMain Girder CheckStiffener CheckShear ConnectorCheckCross Frame /Bracing CheckDesign ReportAutomatic generation of steel composite girder bridge model- Straight, curved and skewed bridge- 3D bridge model with piers, abutments and cross frames- Automatic generation of construction sequence with composite action- Easy generation of non-prismatic tapered sections over the entire or partial spansAutomatic calculation of effective width for composite sectionCracked section option to ignore concrete deck stiffness in negative flexure region3D Cross frame modeling for accurate designAutomatic calculation of member forces and stresses separately for steel girder and concrete deckStage-wise stress check during composite constructionAutomated check of composite girder bridges with concrete deck as per Eurocode 4-2 and AASHTO LRFD- Steel I-girder, tub and box girder bridges- Checks for uniform and hybrid steel girder- Composite girder checks for main girders, longitudinal stiffeners, transverse stiffeners andshear connectors- Steel code checks for cross frame / bracing- Cross section proportion limits, constructability, service limit state, strength limit state, stiffeners andshear connectorsBridge load rating for existing bridges as per AASHTO LRFR- Standard vehicles, user defined vehicles, legal vehicles and permit vehiclesDetailed calculation report for analysis, design and ratingBuilt-in composite section dataEffective width scale factorComposite section for construction stage tosimulate composite action with 1-D elementReinforcement andlongitudinal stiffener dataApplicable functions can be changed upon design codemidas CivilBridging Your Innovations to Realities06
07INTEGRATED SOLUTION SYSTEM FOR BRIDGE AND CIVIL ENGINEERING3. Composite Girder Bridge DesignSteel & PC Composite Girder bridge wizardFast modelling of steel I, box, tub and PC composite bridges using wizardEasy generation of tapered girder4 types of model generationDefinition for transverse deck element spacing by number of division per span or distance- All plate modelX bracing, V bracing, inverted V bracing and single beam cross frame- All frame modelDead load before composite and after composite action with quick generation of live load- Deck as plate & girder as frameEasy generation of tendon using tendon template- Deck & web as plate, flanges as frameAutomatic generation of construction stage considering deck pouring sequenceMulti-curve and different skew angle by support positionsLong term effect by applying 3n in elastic modulus after composite actionInclination in bridge deckResultant forces at every 10 points per spanPier and abutment modellingFE model of steel I composite girder bridgeAll frame model of steel I composite girder bridgeDead and live load definitionDefining bridge layout with spaninformation and bearing dataAll frame model of PC I composite girder bridgemidas CivilBridging Your Innovations to Realities
INTEGRATED SOLUTION SYSTEM FOR BRIDGE AND CIVIL ENGINEERING3. Composite Girder Bridge DesignUseful features suited forcomposite girder bridge designResultant forces for 3D FE modelGeneration of irregular shape composite sectionCalculation of resultant forces on a selected region in beam, plate and solid elementsGeneration of general shape composite section using SPCResultant forces for unstructured meshesComposite tapered section with general shape is supportedTable and text format output by load cases / combinationsConstruction stage analysis to simulate composite action by partsSPC (Section Property Calculator)Resultant forces in the table and text formatBefore composite actionAfter composite actionmidas CivilBridging Your Innovations to Realities08
09INTEGRATED SOLUTION SYSTEM FOR BRIDGE AND CIVIL ENGINEERING3. Composite Girder Bridge DesignSteel composite girder checkSteel composite girder ratingAutomatic steel composite girder checkAutomatic steel composite girder ratingComposite girder check as per Eurocode 4-2, AASHTO LRFD and other specificationsAutomatic generation of load combinationsConstructability, strength, service and fatigue limit state checksMain girders, longitudinal stiffeners, transverse stiffeners, shear connectors, braces and cross framesExcel format calculation report, spreadsheet format table and design result diagrammidas CivilBridging Your Innovations to RealitiesSteel composite bridge load rating as per AASHTO LRFRStrength, service and fatigue limit state ratingDesign live load, legal load and permit load evaluationAdjustment factor resulting from the comparison of measured test behavior with the analytical modelMember resistances and allowable stresses in accordance with AASHTO LRFDExcel format calculation report and spreadsheet format table
INTEGRATED SOLUTION SYSTEM FOR BRIDGE AND CIVIL ENGINEERING3. Composite Girder Bridge DesignMain features forPC composite girder bridge designUK and Italy PSC section database for composite sectionsQuick generation for PSC general shape composite section in Section Property CalculatorEasy and fast generation of strands/tendons using Tendon TemplateConsidering longitudinal rebars and tendons in section stiffness calculationConstruction sequence with time dependent behaviour of concreteAutomatic calculation of member forces and stresses separately for PC girder and concrete deckStage-wise stress check during composite constructionImmediate and time-dependent prestress losses by tendons (Graph & Tables)PSC composite girder design as per Eurocode 2-2 and AASHTO LRFDDetailed calculation report for analysis and designTendon template wizardQuick generation of PSC composite sectionPSC composite girder designmidas CivilBridging Your Innovations to Realities10
11INTEGRATED SOLUTION SYSTEM FOR BRIDGE AND CIVIL ENGINEERINGIntegrated solution for practical PSC bridge design(Longitudinal & transverse direction analysis and strength checks)4. PSC Bridge DesignProcedure and main features forPSC bridge designGlobal analysisalong the spansTransverseanalysisStrength checkAutomatic generation oftransverse analysis modelIntegrated solutionfor PSC bridge designGlobalanalysis alongthe f model dataEndof designRC designConstruction stage analysis reflecting change in elements, boundary conditions & loadingsAuto generation of transverse analysis models through global analysis modelsCreep & shrinkage calculation based on codesTransverse analysis model generation wizard & auto generation of loading and boundary conditionsTime dependent steel relaxation (CEB-FIP, Eurocode, Magura & IRC112)(transverse tendon assignment)Irregular sections displayed to true shapesAutomatic placement of live load for transverse analysisAutomatic positioning of loadings for plate analysis3D/2D tendon placement assignment(lumped representative tendon analysis)Section check using RC / PSC design functionStrength check to Eurocode, AASHTO LRFD and other codesConfinement effect of rebars considered for creepBCM BridgeAuto-calculation of section propertiesconsidering effective widthEasy generation of non-prismatic tapered sectionsover the entire or partial spansBeam stress check for PSC bridgesDefining positions for transverse analysisTransverse analysis model wizardAutomatic reaction summary at specific supports throughstaged launching in ILM bridgesGeneration & analysisof a transverse modelCompression-only element provided for modellingtemporary supports & precasting platformCompleted state analysis reflecting effective width byconstruction stagesSpecial type of PSC bridge analysis (extradosed bridge)Automatic generation of transverse analysis modelRC design of irregularly shaped columnsmidas CivilBridging Your Innovations to RealitiesExtradosed BridgeRC Design Result TableText Design ReportDetail Design Calculation Sheet
INTEGRATED SOLUTION SYSTEM FOR BRIDGE AND CIVIL ENGINEERING4. PSC Bridge DesignModelling features suited forpractical designModelling PSC bridges of irregular sections using Section Property CalculatorConvenient auto generation of tapered sections (change in thicknesses of top/bottom flanges andPSC bridge wizards (BCM, ILM, MSS & FSM): user-defined tendons & sections possibleweb separately considered)Construction stage analysis and completed state analysis reflecting auto calculated effective widthExact 3D tendon and simplified 2D tendon placementsDisplay and design of irregular sectionsAuto generation of non-prismatictapered sectionsAutomatic calculationof effective widthIrregular section defined by user using SPCPSC wizard reflecting design practiceAuto generation oftapered sectionsbased on bridge spansAutomatic calculation ofeffective width for PSC bridgesSchedule-based input of rebarsLumped representative tendon analysisTendon profile input and real-time display3D tendon profile placement2D placement of tendons usingthe representative tendon functionmidas CivilBridging Your Innovations to Realities12
13INTEGRATED SOLUTION SYSTEM FOR BRIDGE AND CIVIL ENGINEERING4. PSC Bridge DesignAutomatic strength checkVarious analysis results forpractical designEurocode 2-2, AASHTO LRFD and other specificationsSeparate immediate and time-dependent tension losses by tendons (graphs & tables)Bending strength, shear strength & torsional strength checksGeneration of tendon weights and coordinates (calculation of tendon quantity)Transverse rebars check and resistance & factored moment diagramsNormal / principal / shear / inclined stresses using PSC Stress Diagram commandStress check for completed state by construction stagesGeneration of erection cambersGeneration of member forces & stresses by construction stages and maximum &Summary of reactions at specific supports in ILM bridgesminimum stresses summaryExcel format calculation report (Crack Control check as per Eurocode)Tendon loss graphDesign parameters for strength checkTension losses in tendonsPSC bridge-specific stress diagramsMaximum normal stress distribution for a PSC bridgeBending strengthcheckPrincipal stress distribution for a PSC bridgeAnalysis results tableAnalysis results graphmidas CivilBridging Your Innovations to RealitiesPSC bridge-specific stress output
INTEGRATED SOLUTION SYSTEM FOR BRIDGE AND CIVIL ENGINEERING4. PSC Bridge DesignSpecial type of PSC bridgesConstruction stage analysis reflecting time-dependent material properties and pretensioning forcesCompression-only element provided to reflect the effects of temporary bentsExternal type pretension loads provided for inducting cable tensioning forcesCalculation of section properties of an irregular section using AutoCAD and SPCCalculation of normal / principal / inclined stresses using the Beam Stress (PSC) commandConstruction stage analysis of an extradosed bridge (BCM)1Construction stage analysis of an extradosed bridge (FSM)2Analysis results of a completed state modelConstruction stage analysis - tower erectionConstruction stage analysis- staged construction of girders143Construction Stage AnalysisControl dialogue boxConstruction stage analysis - FSM2Construction stage analysis - cable erection3Construction stage analysis - cable erectionCompleted state modelConstruction stage analysis - removal of shoringmidas CivilBridging Your Innovations to Realities14
15INTEGRATED SOLUTION SYSTEM FOR BRIDGE AND CIVIL ENGINEERING4. PSC Bridge DesignGrillage analysis model wizardPrestressed multi-celled box girder bridgesGrillage analysis model wizard automatically converts wide multi-celled PSC box girder sections intoa grillage mesh of longitudinal and transverse elements to perform a grillage analysisBoth slab based and web based divisions are supported to automatically calculate the sectionproperties such as total area, transverse shear area, torsional moment of inertia, etc forthe longitudinal and transverse beam elementsMulti-celled box girder bridge grillage model completed with prestressing tendons andboundary conditionsSlab Based DivisionThe grillage analysis wizard supports tapered bridges with horizontal curvatures, multiple types ofspans, user defined bearing conditions, diaphragm and bent definition, auto live load generation,auto-placement of tendon profiles and reinforcement definitionsWeb Based Divisionmidas CivilDefining bridge layout with spaninformation and bearings dataTransverse member andbent cap definitionTendon and reinforcement auto-generationPermanent and variable actions definitionwith traffic lane arrangementBridging Your Innovations to Realities
INTEGRATED SOLUTION SYSTEM FOR BRIDGE AND CIVIL ENGINEERING5. Cable bridge analysisOptimal solution for cable bridge analysis (completed state& construction stage analysis with advanced analysis functions)Optimal solution forcable bridge analysisCable Stayed BridgeInitial equilibrium state analysis forcable stayed bridgesInitial equilibrium state analysisCable nonlinearity considered (equivalent truss,nonlinear truss & catenary cable elements)1Calculation of initial pretensions for cable stayedbridges & initial shape analysis for suspension bridges23Construction stage analysis reflectinggeometric nonlinearityFinite displacement method (P-delta analysis by construction stages and for completed state)1Behaviours of key segments in real constructionreflected3Large displacement analysis reflecting creep &shrinkageconstraintsGeneration of optimal cable pretension forcessatisfying design constraints1Optimum solutions produced by an optimisation theory basedon object functions2Solutions obtained by simultaneous equations if the numbersof constraints and unknowns are equal12Large displacement method (independent models for backward analysis & forward construction stage)Auto generation of construction stage pretensionsusing the tensions in the completed state(linear & nonlinear)2Optimal initial pretensions generated to satisfy desired girder, tower & cable force and displacementOptimum stressing strategyCompleted state analysis & tower/ girder designLinearised finite displacement method & linear elasticmethodLinear buckling analysis / moving load analysis / inelasticdynamic analysisSteel column design of irregular sectionsSuspension Bridge4Backward construction stage analysis using internalmember forces (reflecting large displacement)5Auto calculation of tensions in main cables andcoordinates for self-anchored and earth-anchoredsuspension bridges45Ideal dead load force diagram assumedDetail output for suspension cables (unstressed lengths,sag, etc.) & detail shape analysis66Steel column design of irregular sectionsInitial equilibrium state analysis results satisfying constraintsmidas CivilBridging Your Innovations to Realities16
17INTEGRATED SOLUTION SYSTEM FOR BRIDGE AND CIVIL ENGINEERING5. Cable bridge analysisConstruction stage analysis forcable stayed bridgesForward staged analysis using the pretensions in the completed stateForward staged analysis based on application of constraintsAuto calculation of erection pretensions by entering only the pretensions of the completed state &adding Lack of fit force without having to perform backward analysisApplicable for both large displacement and small displacement analysesInitial equilibrium state analysis reflecting the behaviours of the closure of key segments during erectionAuto calculation of construction stage pretensions accounting for creep & shrinkageCalculation of cable pretensions by construction stages satisfying the constraints for the completedstateAuto-iterative function provided to reflect creep & shrinkageSuperb convergence for calculating unknown load factors using simultaneous equations &object functionsSTEP 01. Calculation of pretensions usingUnknown Load FactorProcedure for a construction stage analysisConstruction Stage1Unit pretension loads appliedIterationUnknown Load FactorOptimal tensions in cables foundsatisfying constraintsSTEP 02. Forward stage analysis for a cable stayed bridge using the pretensionsof the completed state and Lack of fit force1Assignment of constraints & calculation of unknownload factors for each stage (good convergence)2Construction StageRe-analysis of construction stagereflecting influence factors32CheckAnalysis of results for each construction stageConstruction stage analysis results- initial erection3Construction stage analysis results- cantilevers erectedEnd4Construction stage analysis results- closure of side spans1Set up constraints and unknowns2Load Factors found3Iteration controlConstruction stage analysis results- immediately before centre span closure5Construction stage analysis resultsConstruction stage analysis results- final stagemidas CivilBridging Your Innovations to RealitiesCompleted state analysis results- MomentAnalysis results of the completed state
INTEGRATED SOLUTION SYSTEM FOR BRIDGE AND CIVIL ENGINEERING5. Cable bridge analysisConstruction stage analysis ofself anchored suspension bridgesConstruction stage analysis ofearth anchored suspension bridgesAccurate analysis with initial member forces to reflect the behaviour of a self anchored suspensionbridge subjected to axial forces in girdersTypical construction methods applicable for self anchored suspension bridges such as hangerinsertion and Jack-down construction methods0.002mAccurate analysis of initialshape performed to satisfythe coordinates of towers and sags0.004mInitial tension forces in cables of a suspension bridgeBackward construction stage analysis - large displacement analysis1Initial shape analysis2Initial tension forces of a self anchored suspension bridgeBackward construction stage analysis - large displacement analysis 1 Final Stage2 Stage 05Removal of superimposed dead load33 Stage 0444 Stage 03Removal of side span girders55 Stage 02Removal of main span girdersRemoval of side span girders completed66 Erection bents,main cables &girders installedRemoval of main span girdersRemoval of hangers & setback calculationmidas CivilBridging Your Innovations to Realities18
19INTEGRATED SOLUTION SYSTEM FOR BRIDGE AND CIVIL ENGINEERING6. Nonlinear analysisSeismic & earthquake resistant system and seismic performanceEvaluation for bridges using high-end nonlinear analysisNonlinear analysis processin midas CivilPushover analysisNonlinear seismic analysis andperformance evaluation for bridgesAnalysis model dataChecking the status of safety limits of a system, which has been considered with dynamic behavioursNonlinear material properties & plastic hinge propertiesof members(hysteresis models, yield strengths, PM interaction &post yielding behaviour properties)Approximate dimensions / section profile/ material propertiesFinite elements (beam, column, plate & solid)Inelastic spring properties (stiffness, effective dampingratios & hysteresis properties)Structural model of a bridgeStatic loads & inelastic response spectrum(damping & ductility ratio)Acceleration time histories & artificial seismic waves)Basic seismic designNonlinear static analysis(pushover analysis)PerformanceDefinition of input loadsDisplacement controlBoundary nonlinearanalysisLoad controlSeismic controlViscoelasticHystereticSeismic performanceevaluationEffective DampingDuctilityLRBFPSEffective stiffness/effective damping devicehysteretic propertiesDampingTime StepInelastic response spectrumSeismic isolationSeismic isolationInelastic time historyanalysisDirect integrationResponse evaluationStaged reactions, memberforces, stresses, displacements,plastic hinge distribution& system displacement ductilityNonlinear modal analysisRunge-Kutta methodResponse evaluationEigenvalues (natural frequencies)Seismic isolator & damper hysteresis loops,Displacement, velocity & acceleration time historymidas CivilCapacity spectrum method provided to efficiently evaluate nonlinear seismic response & performanceProcess of pushover analysisLoad control & Displacement control methodsGravity load effects consideredStatic analysis& member designPushover analysis reflecting P-delta effectsVarious load patterns supported (Mode Shape / Static Load /Uniform Acc.)Load control ordisplacement controlAnalysis results checked by pushover steps (hinge status /distribution, displacements, member forces & stresses)Inelastic propertiesof membersCapacity spectrum methodVarious types of capacity curves suppliedPushover analysisDemand spectrums supplied for each design standardBeam-ColumnLumped Hinge TypeDistributed Hinge TypeNewmark -ⱖ- Linear acceleration method- Average acceleration methodResponse evaluationDisplacement, velocity & acceleration time historyInelastic hinge distributionMember curvature & rotational ductilitySeismic performance evaluated using Performance PointCapacity ofa structure evaluatedAuto generation of plastichinge propertiesPerformance pointsfound by demand curvesSatisfactoryperformanceNoYesEvaluationof seismic performanceAccurate behaviour analysis using nonlinearseismic response of a bridgeSeismic performanceevaluationStructural inelastic behaviours & resistance capability calculated efficientlyInelastic elementSpring, TrussCapacity spectrum methodDisplacement coefficient methodDisplacement based design method& load redistribution, after yieldingSeismic resistance& isolation system evaluationBridging Your Innovations to RealitiesCapacity spectrum methodAccurate seismicsafety evaluationVarious plastic hinge models
INTEGRATED SOLUTION SYSTEM FOR BRIDGE AND CIVIL ENGINEERING6. Nonlinear analysisBoundary nonlinear analysisAnalysis capabilities fordampers & base isolatorsStructural analysis function including nonlinear link elements (General Link)Dampers, base isolators & inelastic elements simultaneously considered in nonlinear time historyStructural analysis using spring elements having nonlinear properties (Inelastic Hinge Property)analysis (nonlinear direct integration method)Various dampers & base isolators (Gap, Hook, Viscoelastic Damper, Hysteretic System, Lead RubberGood convergence by Runge-Kutta method (Step Sub-Division Control & Adaptive Stepsize Control)Bearing Isolator & Friction Pendulum System Isolator)Static loads converted into the form of dynamic loads (Time Varying Static Loads)Lead Rubber BearingViscoelasticDamperFriction Pendulum SystemHysteretic SystemLead RubberBearingIsolatorHysteretic SystemFriction Pendulum System IsolatorViscoelastic DamperRunge-Kutta method analysis conditionmidas CivilBridging Your Innovations to Realities20
21INTEGRATED SOLUTION SYSTEM FOR BRIDGE AND CIVIL ENGINEERING7. Moving Load OptimiserGeneration of influence lines and surfaces for multiple lanesof traffic to produce the most adverse live load patternsMoving load analysispre-processorMoving load analysispost-processorEasy and multiple lane generation techniques along any type of curvilinear pathLoad models and vehicles from Eurocode, AASHTO LRFD, BS and other specificationsHighway traffic loads, railway traffic loads and footway pedestrian loads can be combinedautomatically for moving load analysisConstruction stage analysis and moving load analysis can be done in the same modelSpecial vehicles can be made to straddle between two lanesTraffic line lane with crossbeam type load distributionMotorway vehiclesmidas CivilBridging Your Innovations to RealitiesTraffic surface lane for shell elementsRail loadsAuto moving load combinationconsidering straddling of axlesbetween two lanes for special vehiclesFast generation of analysis results using clever result filtering techniques that saves physicalmemory and timeCombined member force checks are possible due to availability of corresponding force componentsfor the max/min force effects. Eg: At maximum bending moment, combined shear bending resultcan be seenMoving load tracer displays the adverse live load pattern for all vehicle combinationsMoving loads can be converted into equivalent static loads for detail analysisConcurrent force table for a given max/minforce component due to live loadInfluence line diagram for bending momentVehicular loads converted toequivalent static loads for detail analysisMoving load tracer diagram to identify the adverse location ofvehicle for minimum / maximum force & bending moment
INTEGRATED SOLUTION SYSTEM FOR BRIDGE AND CIVIL ENGINEERING8. Soil-Structure InteractionAutomatic modelling of soil-structure interface facilitatingthe analysis of integral bridges and box culvertsIntegral bridge and culvert wizardIntegral bridge spring supportsBuilt-in wizard for RC frame/box culvert can model a 3 dimensional plate model of box culverts withall boundary conditions and ground pressure loadsAuto calculation of soil springs from simple modulus of subgrade reaction inputAutomatic calculation of earth pressure loads considering the submerged condition of soil andthe ground water levelNonlinear soil behaviour can be automatically modelledSoil structure interaction around the abutment and pile can be simulated by entering basicgeotechnical inputsStress distribution along the
midas Civil enables the user to auto-generate an MS Word report using analysis and design results All the input and output data can be plotted (ie. material properties, section properties, reactions, member forces, displacements, stresses, section verification results, etc.) in a diagram, graph, text or table format