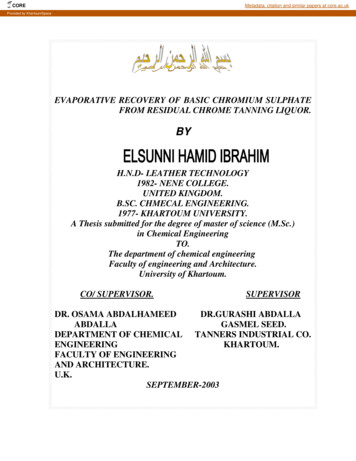
Transcription
COREMetadata, citation and similar papers at core.ac.ukProvided by KhartoumSpaceEVAPORATIVE RECOVERY OF BASIC CHROMIUM SULPHATEFROM RESIDUAL CHROME TANNING LIQUOR.BYH.N.D- LEATHER TECHNOLOGY1982- NENE COLLEGE.UNITED KINGDOM.B.SC. CHMECAL ENGINEERING.1977- KHARTOUM UNIVERSITY.A Thesis submitted for the degree of master of science (M.Sc.)in Chemical EngineeringTO.The department of chemical engineeringFaculty of engineering and Architecture.University of Khartoum.CO/ SUPERVISOR.SUPERVISORDR. OSAMA ABDALHAMEEDDR.GURASHI ABDALLAABDALLAGASMEL SEED.DEPARTMENT OF CHEMICAL TANNERS INDUSTRIAL CO.ENGINEERINGKHARTOUM.FACULTY OF ENGINEERINGAND ARCHITECTURE.U.K.SEPTEMBER-2003
Dedication.To the memory ofMy Mother Eltayia Elobied HassanMy Father Hamid Ibrahim Mohammed AliMy Grand Father Elobied Hassan Fadlallah.My Grand Mother El Haram Shams eldeen Yousif.I pray to Almighty Allah to forgive and place thempermanently in paradise, in association with themessengers and the true believers. Amin.
Acknowledgment.I am very grateful to my supervisor Dr.Osama Abdalhameed Abdallaand co-supervisor Dr.Gurashi Abdallah Gasmelseed for their real help,support, encouragement and guidance through this work until itscompletion.My thanks to Dr.Ibrahim Hassan El Haj Head of Board of Directors ofAl Karam Group of companies and also my thanks to the staff of Al NasrTannery for their kind help and supportive role.My thanks to the staff of the White Nile Tannery speciallyMr.Mohammed Margani, the Ex-General Manager and Dr.AbdurahmanAlasuti the present manager for allowing me to carry all theexperiments,the chemical and physical analysis in their pilot plant andlaboratory.Also I am very grateful to Prof.Osman Saad the ex-deen of theveterinary and animal production college- Sudan University for his helpand support.
ABSTRACTThis research was concerned with the concentration of residualchromium tanning liquor by evaporative techniques and the re-use of thisconcentrated chromium liquor for tannage after adjustment with a makeup of basic chromium sulphate powder.Twelve samples of the residualchromium liquors were collected randomly from ALNASR and theWhite Nile Tanneries. They were analysed mainly for Cr2o3 content,concentration of neutral salts (0Be ) and (PH). The average quantity ofchromium oxide "Cr2o3" for both tanneries which discharged as waste tothe drain was found to be 5.58 g/L. This quantity is equivalent to 32% ofthe chromic oxide added at the beginning of the tannage. This mean, thatmore or less one third of the basic chromium sulphate used in tannage islost as waste. Then two Evaporation experiments were carried out at theWhite Nile Tannery laboratory by direct heating to determine theoptimum evaporation level for maximum chromium oxide recovery.This level of evaporation was found to be about 27% of the water, can beevaporated without much loss of chromium oxide. Then Eight tanningExperiments were carried out at the White Nile Tannery pilot plant in thefollowing manner:A residual chrome liquor (R1) was taken from the White Nile tanneryand it was evaporated to the required level (C1) .Then the chromiumoxide in (C1) was determined and was adjusted with fresh chromiumpowder to maintain the tanning percentage to 7%. Then it was used totan a delimed, bated, pickled pelt. The residual liquor(R2) from (C1)was again evaporated to (C2). Then the chromium oxide in (C2) wasdetermined and adjusted to the required level with fresh chromiumpowder. Then it was used to tan a delimed , bated, pickled pelt. Thisprocess was repeated eight times untill (C8) and (R9). The averagequantity of basic chromium sulphate required to be added as a make-upwas found to be 4.9%. That means 2.1% of basic chromium sulphate issaved all through the year, in addition to the following savings:1) 4% in the sodium chloride2) 60-70% in the water3) 0.1-0.2% in the sulphuric Acid
Then four pelts tanned with (C8), (C7), (C6) plus one side from theWhite Nile Tannery were retanned as usual and they were paste- Dried.Then they were tested for their physical and chemical properties and theresults obtained were found to be within the accepted internationallimits.The economical evaluation of the project was found to be feasible. Theannual profit was found to be 33767 US and the pay-back period wasfound to be about 1.3 year.As with regard to the environmental evaluation and since the process is aclosed loop process, then appendix (5) proves that the salinity will bereduced by 25 %, the toxicity by 24%, the B.O.D by 1.2% and the C.O.Dby 1%, from the total pollution load of the tannery. Hence this process isan eco-friendly process, in addition to the reduction in cost of the end ofpipe treatment.
ﺍﻟﺨﻼﺻﺔ ﻋﻨﻲ ﻫﺫﺍ ﺍﻟﺒﺤﺙ ﺒﺘﺭﻜﻴﺯ ﻤﺤﻠﻭل ﻜﺒﺭﻴﺘﺎﺕ ﺍﻟﻜﺭﻭﻡ ﺍﻟﻘﺎﻋﺩﻴﺔ ﺒﻌﺩ ﺇﺴﺘﺨﺩﺍﻤﻬﺎ ﻓﻲ ﻋﻤﻠﻴﺔ ﺍﻟﺩﺒﺎﻏـﺔ ﺒﻭﺍﺴﻁﺔ ﺍﻟﺘﺒﺨﻴﺭ ﻭﺫﻟﻙ ﻟﻐﺭﺽ ﺇﻋﺎﺩﺓ ﺇﺴﺘﺨﺩﺍﻤﻬﺎ ﻤﺭﺓ ﺃﺨﺭﻯ ﻓﻲ ﻋﻤﻠﻴﺔ ﺍﻟﺩﺒﺎﻏﺔ ﺒﻌـﺩ ﻀـﺒﻁ ﺘﺭﻜﻴﺯﻫﺎ ﺒﺈﻀﺎﻓﺔ ﻤﻠﺢ ﻜﺭﻭﻡ ﺠﺩﻴﺩ . ﺤﻴﺙ ﺃﺨﺫﺕ ﻋﻴﻨﺎﺕ ﻋﺸﻭﺍﺌﻴﺔ ﻤﻥ ﻤﺩﺒﻐﺘﻲ ﺍﻟﻨﻴل ﺍﻷﺒـﻴﺽ ﻭﺍﻟﻨﺼﺭ ﻭﻋﺩﺩﻫﺎ ﺇﺜﻨﻰ ﻋﺸﺭ ﻋﻴﻨﺔ ﻭﺘﻡ ﺘﺤﺩﻴﺩ ﺍﻟﺭﻗﻡ ﺍﻟﻬﻴﺩﺭﻭﺠﻴﻨﻲ ﻭﺍﻟﺘﺭﻜﻴﺯ ﺍﻟﻌـﺎﻡ ﻭﺘﺭﻜﻴـﺯ ﺃﻜﺴﻴﺩ ﺍﻟﻜﺭﻭﻡ ﻭﻗﺩ ﻭﺠﺩ ﺘﺭﻜﻴﺯ ﺃﻜﺴﻴﺩ ﺍﻟﻜﺭﻭﻡ ﻓﻲ ﺍﻟﻤﺘﻭﺴﻁ 5.58 ﺠﻡ / ل ، ﺃﻱ ﺒﻨﺴﺒﺔ ﻓﺎﻗـﺩ ﺘﻌﺎﺩل ، %32 ﻭﻗﺩ ﺃﺠﺭﻴﺕ ﺍﻟﺘﺤﺎﻟﻴل ﺒﻤﻌﻤل ﻤﺩﺒﻐﺔ ﺍﻟﻨﻴل ﺍﻷﺒﻴﺽ . ﺜﻡ ﺃﺠﺭﻴﺕ ﺘﺠﺭﺒﺘﻴﻥ ﺒﻤﻌﻤل ﻤﺩﺒﻐﺔ ﺍﻟﻨﻴل ﺍﻷﺒﻴﺽ ﺒﺎﻟﺘﺴﺨﻴﻥ ﺍﻟﻤﺒﺎﺸﺭ ﻟﺘﺤﺩﻴﺩ ﺍﻟﺤﺩ ﺍﻷﺩﻨﻰ ﻟﻠﺘﺒﺨﻴﺭ ﻭﻗﺩ ﻭﺠﺩ ﺃﻨﻪ ﻴﻤﻜﻥ ﺘﺒﺨﻴﺭ %27 ﻤﻥ ﺍﻟﻤﺤﻠﻭل ﺩﻭﻥ ﺃﻥ ﻴﻜﻭﻥ ﻫﻨﺎﻟﻙ ﻓﺎﻗﺩ ﻴﺫﻜﺭ ﻓﻲ ﺃﻜﺴﻴﺩ ﺍﻟﻜﺭﻭﻡ . ﺜﻡ ﺃﺠﺭﻴـﺕ ﺜﻤﺎﻨﻴـﺔ ﺘﺠﺎﺭﺏ ﻓﻲ ﻤﺨﺘﺒﺭ ﺍﻟﻨﻴل ﺍﻷﺒﻴﺽ ﻋﻠﻰ ﺍﻟﻨﺤﻭ ﺍﻟﺘﺎﻟﻲ -: ﺭ ﺃﺨﺫ ﻤﺤﻠﻭل ﺍﻟﻜﺭﻭﻡ ﺍﻟﺭﺍﺠﻊ ﺒﻌﺩ ﺍﻟﺩﺒﺎﻏﺔ ﻤﻥ ﻤﺩﺒﻐﺔ ﺍﻟﻨﻴل ﺍﻷﺒﻴﺽ ﻭﺃﻋﺘﺒﺭ ) ( 1 ﻭﺘﻡ ﺘﺒﺨﻴﺭﻫ ﻡ ﻟﻠﻤﺴﺘﻭﻯ ﺍﻟﻤﻁﻠﻭﺏ ) ( 1 ﺜﻡ ﺤﺩﺩﺕ ﻨﺴﺒﺔ ﺃﻜﺴﻴﺩ ﺍﻟﻜﺭﻭﻡ ﻭﺃﺴﺘﺨﺩﻡ ﻫﺫﺍ ﺍﻟﻤﺭﻜﺯ ﻓـﻲ ﺩﺒﺎﻏـﺔ ﺠﻠﺩ ﺒﻘﺭﻱ ﻤﺤﻨﻁ ﺒﻌﺩ ﺃﻥ ﺃﻀﻴﻑ ﺃﻟﻴﻪ ﻤﻠﺢ ﻜﺭﻭﻡ ﺠﺩﻴﺩ ﺒﺎﻟﻘﺩﺭ ﺍﻟﻤﻁﻠﻭﺏ ﺜﻡ ﺒﻌﺩ ﻨﻬﺎﻴﺔ ﺍﻟﺩﺒﺎﻏـﺔ ﻡ ﺭ ﺘﻡ ﺘﺠﻤﻴﻊ ﻤﺤﻠﻭل ﺍﻟﻜﺭﻭﻡ ﻤﺭﺓ ﺜﺎﻨﻴﺔ ) ( 2 ﻭﺘﻡ ﺘﺒﺨﻴﺭﻩ ﻟﻴﻜﻭﻥ ﺍﻟﻤﺭﻜﺯ ﺍﻟﺜﺎﻨﻲ ) ( 2 ﻭﺤﺩﺩﺕ ﻡ ﻡ ﻨﺴﺒﺔ ﺃﻜﺴﻴﺩ ﺍﻟﻜﺭﻭﻡ ﻓﻲ ) ( 2 ﻭﺘﻡ ﺇﺴﺘﺨﺩﺍﻡ ﺍﻟﻤﺭﻜﺯ ﺍﻟﺜﺎﻨﻲ ) ( 2 ﻓﻲ ﺩﺒﺎﻏﺔ ﺠﻠـﺩ ﺒﻘـﺭﻱ ﻤﺤﻨﻁ ﺜﺎﻨﻲ ﺒﻌﺩ ﻀﺒﻁ ﺍﻟﺘﺭﻜﻴﺯ ﺒﻜﺭﻭﻡ ﺠﺩﻴﺩ ﻭﻜﺭﺭﺕ ﻫﺫﻩ ﺍﻟﺘﺠﺭﺒﺔ ﺤﺘـﻰ ) ﻡ (8 ﻭ) ﺭ (9 ﻭﻭﺠﺩ ﺃﻥ ﻤﺘﻭﺴﻁ ﺍﻟﻜﺭﻭﻡ ﺍﻟﺠﺩﻴﺩ ﺍﻟﺫﻱ ﻴﺠﺏ ﺇﻀﺎﻓﺘﻪ ﻟﻀﺒﻁ ﺍﻟﺘﺭﻜﻴﺯ ، %4.9 ﺍﻷﻤﺭ ﺍﻟـﺫﻱ ﻴﻌﻨﻲ ﺃﻨﻨﺎ ﻗﺩ ﻭﻓﺭﻨﺎ %2.1 ﻤﻥ ﻜﻤﻴﺔ ﺍﻟﻜﺭﻭﻡ ﺍﻟﻤﺴﺘﺨﺩﻤﺔ ﻴﻭﻤﻴﺂ ﻓﻲ ﻋﻤﻠﻴـﺔ ﺍﻟﺩﺒﺎﻏـﺔ ، ﻫـﺫﺍ ﺒﺎﻹﻀﺎﻓﺔ ﺇﻟﻰ ﺒﻌﺽ ﺍﻟﻤﻭﺍﺩ ﺍﻷﺨﺭﻯ ﻤﺜل : * ﺍﻟﻤﻠﺢ ﺒﻨﺴﺒﺔ . %4 * ﺤﺎﻤﺽ ﺍﻟﻜﺒﺭﻴﺘﻴﻙ ﺒﻨﺴﺒﺔ . %0.1 * ﺍﻟﻤﺎﺀ ﺒﻨﺴﺒﺔ . % 70 - 60
ﻡ ﻡ ﻡ ﺜﻡ ﺘﻤﺕ ﺇﻋﺎﺩﺓ ﺩﺒﺎﻏﺔ ﺃﺭﺒﻌﺔ ﺠﻠﻭﺩ ، ﺜﻼﺙ ﺘﻤﺕ ﺩﺒﺎﻏﺘﻬﺎ ﺒﺎﻟﻤﺭﻜﺯﺍﺕ ) ( 7 ) ،( 6 ﻭ ) ( 8 ﻭﺍﻟﺭﺍﺒﻊ ﻤﻥ ﻤﺩﺒﻐﺔ ﺍﻟﻨﻴل ﺍﻷﺒﻴﺽ ، ﺒﺎﻟﻁﺭﻴﻘﺔ ﺍﻟﻌﺎﺩﻴﺔ ﻭﺘﻡ ﺘﺠﻔﻴﻔﻬﺎ ﻋﻠـﻰ ﺍﻷﻟـﻭﺍﺡ ﺍﻟﺯﺠﺎﺠﻴـﺔ ﺒﻭﺍﺴﻁﺔ ﺍﻟﻠﺼﻕ ﻭﺃﺠﺭﻴﺕ ﻟﻬﺎ ﺍﻹﺨﺘﺒﺎﺭﺍﺕ ﺍﻟﻔﻴﺯﻴﺎﺌﻴﺔ ﻭﺍﻟﻜﻴﻤﻴﺎﺌﻴﺔ ﻭﻭﺠـﺩﺕ ﺍﻟﻨﺘـﺎﺌﺞ ﻤﻁﺎﺒﻘـﺔ ﻟﻠﻤﻭﺍﺼﻔﺎﺕ ﺍﻟﻤﻁﻠﻭﺒﺔ ﺍﻟﻌﺎﻟﻤﻴﺔ . ﺍﻟﺘﻘﻴﻴﻡ ﺍﻻﻗﺘﺼﺎﺩﻯ ﻟﻬﺫﺍ ﺍﻟﻤﺸﺭﻭﻉ ﻭﺠﺩ ﺍﻨﻪ ﺫﻭﺠﺩﻭﻯ ﺍﻗﺘﺼﺎﺩﻴﺔ ﺤﻴﺙ ﻜﺎﻨـﺕ ﺍﻟﻔﺎﺌـﺩﻩ 33.767 ﺩﻭﻻﺭ ﺍﻤﺭﻴﻜﻰ ﻓﻰ ﺍﻟﻌﺎﻡ ﻭﻓﺘﺭﺓ ﺍﻟﺴﺩﺍﺩ ﺤﻭﺍﻟﻰ 1.3 ﻋﺎﻡ . ﺒﺎﻟﻨﺴﺒﺔ ﻟﻠﺘﻘﻴﻴﻡ ﺍﻟﺒﻴﺌﻰ ﻭﺒﻤﺎ ﺍﻥ ﺍﻟﻁﺭﻴﻘﺔ ﺍﻟﺘﻰ ﺍﺘﺒﻌﺕ ﻓﻰ ﺇﻋﺎﺩﺓ ﺇﺴﺘﺨﺩﺍﻡ ﺍﻟﻜﺭﻭﻡ ﻤﻐﻠﻘﻪ ، ﻓﻌﻠﻴﻪ ﻭﻤﻥ ﺍﻟﻤﻠﺤﻕ ﺭﻗﻡ ) (5 ﻓﺈﻥ ﺍﻟﺘﺨﻔﻴﺽ ﻓﻰ ﺩﺭﺠﺔ ﺍﻟﻤﻠﻭﺤﻪ ﻴﺼل ﺍﻟﻰ %25 ﻭﻓﻰ ﺍﻟﺴﻤﻴﺎﺕ ﻴﺼل ﺍﻟـﻰ %24 ﻭﻓﻰ ﺍﻟـ B.O.D ﻴﺼل ﺍﻟﻰ %1.2 ﻭﻓﻰ ﺍﻟـ C.O.D ﻴﺼل ﺍﻟﻰ %1 ﻤـﻥ ﺇﺠﻤـﺎﻟﻰ ﺘﻠﻭﺙ ﺍﻟﻤﺩﺒﻐﺔ ، ﻭﺒﺎﻟﺘﺎﻟﻰ ﻓﺈﻥ ﻫﺫﻩ ﺍﻟﻁﺭﻴﻘﻪ ﺘﻌﺘﻴﺭ ﺼﺩﻴﻘﺔ ﻟﻠﺒﻴﺌﺔ ﺍﻀﻑ ﺍﻟﻰ ﺫﻟﻙ ﻓﺎﻨﻬـﺎ ﺘﺨﻔـﺽ ﺘﻜﻠﻔﺔ ﺍﻟﻤﻌﺎﻟﺠﺔ ﻓﻰ ﻨﻬﺎﻴﺔ ﺍﻻﻨﺒﻭﺏ .
ContentsSubject- List of Tables- List of Figures-Abbreviations & Symbols usedChapter One – Introduction1.1-Chrome tannage1.2-Leather industry in Sudan1.3-Research Problems1.4-Research objectives.Chapter Two - Literature Review2.1-Historical Development in Chrometannage.2.2- The chemistry of basic chromium sulphate.2.3- Practice of chrome tannage2.4- Factors controlling the course of chrometannage.2.5-Mechnism of chrome tannage.2.6- Conventional chrome tannage.2.7-Environmental issues and theirconsequences.2.8- Evaporation.2.9-Previous studies on chrome recovery ofresidual chrome liquor .Chapter Three - Materials and methods:3.1- Analysis of residual chrome liquor.3.2-Evaporative recovery of the residualchrome liquor.3.3-Tannage experiments with concentratedchrome liquors after evaporation.3.4- Physical and chemical testing of the tannedleather.3.5-Test for Hexavalent Chrome.3.6-Determination of C.O.DPage No.IIIIII1-322334-35569121416202935-39363738393939
Chapter Four - Results & Discussion.4.1- Analysis of Residual chrome liquor fromWhite Nile and Al Nasr Tanneries.4.2- Evaporation of residual chrome liquors todetermine the optimum level ofevaporation4.3- Tannery runs using the concentrates of theresidual chrome liquors (C1-C8)4.4- Analysis of residuals chrome liquorsbefore and after evaporation. (For tanneryruns)4.5- Amount of fresh chrome powder added asatopping to concentrates to maintain theoriginal tanning % age.4.6- Analysis of residual of concentrates aftertanning.4.7- Physical and chemical analysis of leather4.8- Values of Cr6 and C.O.D.Chapter Five - Design & Economical evaluation of theconcentration unit.5.1- Basic design data5.2- Equipments for the evaporation unit5.3-Flow sheet for the evaporation unit ofresidual basic chromium sulphate.5.4- Calculation of the heating surface of theevaporator.5.5- Economical EvaluationChapter Six - Conclusion and recommendations6.1- Conclusions.6.2- 8595960-70616164656771-73727374-7879-80
List of s of residual chrome liquor fromWhite Nile Tannery.Analysis of residual chrome liquor fromAl Nasr Tannery.Direct Heating Evaporation Experiment(I)Direct heating evaporation experiment(II)Average of optimum concentrationEvaporation experiment (I) by the use ofthe climbing film evaporator. Naturalcirculations.Evaporation experiment (II) by the use ofthe climbing film evaporator. Naturalcirculation.Tannery Runs.Analysis of residual chrome liquorsbefore evaporation.Analysis of residual chrome liquors afterevaporation.Amount of fresh chrome powder addedas a topping.Analysis of residual of concentrates afterpretanning.Physical and chemical analysis of leather.Values of Cr6 & C.O.DPage No.4141424246454647-54565658595959
List of FiguresS.No.123456-78Subjects.Conventional process for chrome tannag.Flow chart for the tanning process andassociated pollutants.Forced circulation evaporator typesIere chrome process.Flow sheet for the re-use of residualchrome liquor.A plot of Cr2O3 g/l Vs Evaporation /mlFlow sheet for evaporation unit ofresidual chrome liquor.Page No.15263143-4464
Abbreviations & symbols sCpm'T Tq-Badische Anili & Soda-Fabric AGBiochemical Oxygen demand-Chemical Oxygen Demand-Environmental Protection Agency (U.S.A)-Khartoum University.-United Nations Industrial DevelopmentOrganisationHeat transfer area, m2Over all heat transfer coefficient , w/m2 - ocResidual chrome liquors of Tannery Runs (1-8)Concentrates of residual chrome liquorsBoiling point elevation, ocLatent heat of condensation of steam kj/kgSpecific heat , J/g- ocMass flow rate, kg/hr, of liquid leaving theevaporator, m'f feed, m's of steam and steamcondensate.Temperature, ocTemperature drop, ocRate of heat transfer W.
1-INTRODUCTION1.1- Chrome Tannage:Chrome tannage was introduced into the leather industry in the year(1858) (18) and it is now the most commonly used tanning methodworldwide (3).The tanning material is basic chromium sulphate. Substantial quantity ofthis material (7-8% on pelt weight) is used to convert hide into leather inthe conventional chrome tanning process. About thirty percent of thistanning material flows as wastage along with the effluent (3). Thismaterial if discharged without recovery, it causes considerableenvironmental pollution and economical loss. Therefore its recovery canbring down cost of production, save money, preserve the valuableresource of this very important material, comply with the cleanerproduction technology and protect the environment.1.2- Leather Industry in Sudan1.2.1- Raw Material:According to official estimations, Sudan in the year 2002 has about(133) millions heads of live stock (17).The hides and skins production in the year 1999 is (4.4) millions cattlehides, (10) millions sheep skins, (10) millions goatskins and (0.1)millions camel hides (7).1.2.2 - The Tanneries:There are (22)-mechanized tanneries in Sudan. The tanning capacities ofthese tanneries are estimated to be (1.5) millions hides and (15) millionssheep and/ or goatskins (7). These tanneries process pickled, wet - blueand crust hides and skins for export and finished leather for local market.All these tanneries use basic chromium sulphate extensively and theyadopt the conventional chrome tanning process. Hence a considerablequantity of this material is discharged to the sewer. This quantity as
estimated for the designed capacities of these tanneries will be asfollows: 7/100 X 30/100 (1,500,000 hides X18 kg/hide 15,000,000 skins X 1.2 kg/skin) 945 tons/ year.Which is equivalent to 945 X 475 US X 1.25 561093.8 US .1.3- Research Problem:1.3.1- Risk of pollution and environmental hazards.1.3.2 -Depletion of a valuable resource.1.3.3 -Economical loss.1.4- Objectives:1.4.1- To minimizes the chromium concentration in the effluent tocomply with the environmental regulations.1.4.2- To find a reasonable and ever lasting solution to the chromiumpollution problem:1.4.3- To recycle the residual concentrated chrome liquor and reuse itwith a fresh make - up to produce a leather with standardspecifications.1.4.4- To reduce the production cost by saving the lost chrome.To achieve these objectives, the evaporative technique to recoverchromium from spent chrome tan liquor was adopted in thisstudy.
2 – Literature Review2.1- Historical Development in Chrome Tannage:About 1797 the French chemist Louis N.Vauquelin, while investigatingthe chemical properties of an ore from Siberia, observed many brilliantlycolored compounds, thus, he named this new element chrome(Chromium) from the Greek word Chroma, meaning Colour. Not onlydid vauquelion make a detailed record of his discovery and hisexperiments but also he recognized its importance and predicted a greatfuture for it (18).For about 30 years chromium minerals and chromiu
the climbing film evaporator. Natural circulations. 45 7 Evaporation experiment (II) by the use of the climbing film evaporator. Natural circulation. 46 8-15 Tannery Runs. 47-54 16 Analysis of residual chrome liquors before evaporation. 56 17 Analysis of residual chrome liquors after evaporation. 56 18 Amount of fresh chrome powder added as a topping. 58 19 Analysis of residual of concentrates .