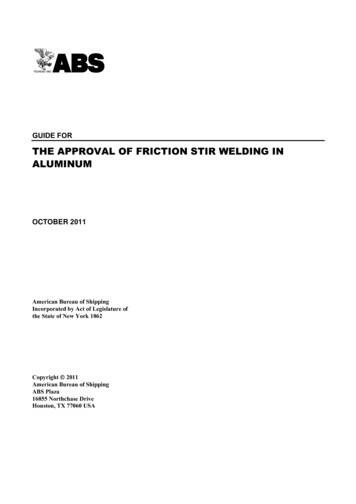
Transcription
Guide for the Approval of Friction Stir Welding in AluminumGUIDE FORTHE APPROVAL OF FRICTION STIR WELDING INALUMINUMOCTOBER 2011American Bureau of ShippingIncorporated by Act of Legislature ofthe State of New York 1862Copyright 2011American Bureau of ShippingABS Plaza16855 Northchase DriveHouston, TX 77060 USA
ForewordForewordThis Guide provides the guidelines for the approval of friction stir welding procedures, operators and thenondestructive testing requirements for production friction stir welding of aluminum. These guidelines arebased on the current knowledge and may be updated as practical experience is gained. The latest knowledgewill be considered in approval tests and may require the test program or the range of approval to be adaptedaccordingly.This Guide becomes effective on the first day of the month of publication.Users are advised to check periodically on the ABS website www.eagle.org to verify that this version ofthis Guide is the most current.We welcome your feedback. Comments or suggestions can be sent electronically by email to rsd@eagle.org.0iiABS GUIDE FOR THE APPROVAL OF FRICTION STIR WELDING IN ALUMINUM . 2011
Table of ContentsGUIDE FORTHE APPROVAL OF FRICTION STIR WELDING INALUMINUMCONTENTSSECTION 1General . 11Scope and Application. 12References . 13Definitions. 1SECTION 2Weld Procedure Qualification . 31General Considerations. 31.11.2Test Assembly Size .31.3Rejection of Test Assembly .31.4Transfer of Qualification .31.5Transverse Tensile Test Specimens and Transverse BendSpecimens.31.6Fixturing.32Qualification of Weld Repair Procedures . 53Operator Qualification . 54FSW – Weld Procedure Specification (WPS) and WelderPerformance Qualification Record Requirements (WPQR) . 6TABLE 1SECTION 3Procedure Qualification Limits .3Essential Elements of a Friction Stir Welding Procedure. 6TABLE 2Weld Procedure Qualification Test Requirements . 9TABLE 3Operator Qualification Test Requirements . 10FIGURE 1Butt Joint Test Assembly . 4FIGURE 2Location of Test Specimens . 4FSW Production Quality Control and NDT Requirements . 111Records . 112Inspection Before Production FSW . 1132.1Verification Before Welding .112.2Joint Setup Variability .11Inspection During Production FSW . 11ABS GUIDE FOR THE APPROVAL OF FRICTION STIR WELDING IN ALUMINUM . 2011iii
456ivInspection After Production FSW – Visual Inspection (VT). 114.1Exit Hole Uniformity .124.2Herring Bone or Chevron Marking .124.3Flash.124.4Dimensional Requirements.124.5Butt Joint Alignment.124.6Irregular Width .124.7Root Reinforcement.124.8Cracks, Porosity, Lack of Penetration.124.9Visual Examination Records.12Other Inspection After FSW . 135.1Macroetch.135.2Penetrant Testing (PT) .135.3Ultrasonic Testing (UT).135.4Radiographic Testing (RT) .135.5Batch Testing Alternative.13FSW NDT Acceptance Requirements. 136.1Visual Inspection (VT) .136.2Penetrant Testing .136.3Ultrasonic Testing (UT).146.4Radiographic Testing (RT) .14ABS GUIDE FOR THE APPROVAL OF FRICTION STIR WELDING IN ALUMINUM . 2011
Section 1: GeneralSECTION11GeneralScope and ApplicationThis Guide has been developed with the objective of setting out the requirements for the qualification offriction stir welding (FSW) procedures and operators. This Guide also provides guidelines for the productionquality control of FSW and the nondestructive testing (NDT) requirements. FSW produces a weld betweentwo abutting workpieces by the frictional heating and plastic material displacement caused by a rotatingtool that traverses along the weld joint. This Guide is for the application of FSW for aluminum groovewelds. No other joint configuration is considered in this Guide.Weld procedure and operator qualification requirements apply for FSW of aluminum alloys identified inRef. 1.2ReferencesThe following documents form a part of this overall Guide to the extent they are referenced.Reference Number13Reference DescriptionABS Rules for Welding and Materials (Part 2)2AWS A3.0 Standard Welding Terms and Definitions3ABS Guide for Nondestructive Inspection of Hull Welds4AWS D1.2/D1.2M Structural Welding Code – Aluminum5AWS D17.3/17.3M Specification for Friction Stir Welding of Aluminum Alloys for AerospaceApplications6NASA document PRC-5010C, Process Specification for Pickling, Etching, and Descaling of MetalsDefinitionsAdjustable Probe (Retractable Pin) Tool – Tool probe length, rotation speed, direction of probe rotationare adjustable.Advancing Side of Weld – Side of the weld where the direction of tool rotation is the same as the directionof welding.Direction of Tool Rotation – Rotation as viewed from the spindle that is rotating the tool.Exit Hole – Hole remaining at the end of a weld after the withdrawal of the tool.Flash – Material expelled along the weld toe during FSW.Friction Stir Re-weld – FSW pass upon FSW pass from one side only.Friction Stir Welding Methods – Methods include, but are not limited to, robotic, single spindle, multiplespindles, adjustable probe (retractable probe) tool, self-reacting (bobbin) tool, and simultaneous two-sidedwelding.Heel – Part of the tool shoulder that is at the rear of the tool relative to its forward motion.Heel Plunge Depth – Distance the heel extends into the workpiece.Joint Line Remnant – Unmixed and distorted layer of Aluminum Oxide, occurring at the root of the jointfaying surfaces, when the joint is welded from one side using anvil backing.ABS GUIDE FOR THE APPROVAL OF FRICTION STIR WELDING IN ALUMINUM . 20111
Section1GeneralProbe – Part of the welding tool that extends into the workpiece to make the weld.Retreating Side of Weld – Side of the weld where the direction of tool rotation is opposite to the weldingdirection.Self-reacting (Bobbin) Tool – Tool with two shoulders separated by a fixed length probe or an adjustable lengthprobe.Sweep – Denotes a curve in the horizontal plane.Tool Offset – The shortest distance from the tool axis to the joint.Tool Shoulder – Surface of the tool that contacts the workpiece surface during welding.Tool Rotation Speed – Angular speed of the welding tool in revolutions per minute.Welding Tool – Rotating component that passes entirely through or partially through the workpiece, andmay or may not have a shoulder.2ABS GUIDE FOR THE APPROVAL OF FRICTION STIR WELDING IN ALUMINUM . 2011
Section 3: Weld Procedure QualificationSECTION12Weld Procedure QualificationGeneral ConsiderationsPrior to production welding, the manufacturer or contractor shall develop and qualify FSW procedures. Awelding procedure qualification test plate schematic with locations for removal of test specimens is shown inSection 2, Figures 1 and 2. The FSW fabricator shall document the essential elements of Section 2, Table 1when developing a FSW procedure. Section 2, Table 2 provides the required destructive and nondestructivetests for FSW qualification test assemblies. Each FSW manufacturer or contractor is responsible for theFSW done by their organization and shall conduct the qualification tests required in this Section.Every weld procedure shall be submitted to and Approved by the ABS Materials Department prior toacceptance. Surveyors shall witness the procedure qualification and test results to their satisfaction.1.1Procedure Qualification LimitsThe FSW manufacturer or contractor shall adhere to the procedure qualification limits for FSW describedin Section 2, Table 1. When welding the procedure qualification test assembly, the welding operator shallbe under the full control and supervision of the FSW manufacturer or contractor.1.2Test Assembly SizeThe procedure qualification test assembly size shall be as shown in Section 2, Figure 1 for square groovewelds. The size of the test assembly shall be sufficient to permit removal of the required test specimens fromthe nominal start, middle, and end of a single weld. The intent of this requirement is to obtain property dataat various locations along the weld length to observe any property variations that may exist within a singleweld. Friction stir welding of additional test assemblies to furnish test specimens shall not be permitted.Multi-pass FSW will be specially considered.1.3Rejection of Test AssemblyIf a procedure qualification fails to meet any of the requirements, the test assembly shall be rejected. Insuch cases, two test assemblies may be welded using the same welding procedure and tested. If the secondset of test assemblies fails, that FSW procedure shall be rejected and a new FSW procedure shall be writtenand tested.1.4Transfer of QualificationQualification resides with the FSW manufacturer or contractor that performed the qualification testing. AFSW manufacturer or contractor may transfer qualified weld procedures from one FSW machine to anotherwhen the FSW machine is of identical model and type. The FSW manufacturer or contractor may usequalified FSW procedures at other facilities which are under the manufacturer or contractor’s operationaland quality control.1.5Transverse Tensile Test Specimens and Transverse Bend SpecimensTransverse tensile test specimens and transverse bend specimens are to be in accordance with Ref. 1. Thepreparation of macroetch specimens is to be to an appropriate standard to reveal the structure of the weld.1.6FixturingSpecial consideration shall be taken for acceptance of procedures where the weld procedure test piece is adifferent shape or arrangement than the production piece. The fixturing arrangement for production work shallbe proven to be equivalent to the procedure qualification fixturing to the satisfaction of the attending Surveyor.ABS GUIDE FOR THE APPROVAL OF FRICTION STIR WELDING IN ALUMINUM . 20113
Section2Weld Procedure QualificationFIGURE 1Butt Joint Test Assembly1tL2L1L1Notes:1Joint preparation and fit-up, as specified in WPSL1Minimum 150 mm (6 in.)L2Minimum 500 mm (20 in.)tProduction material thicknessFIGURE 2Location of Test Specimens (8)132458674ABS GUIDE FOR THE APPROVAL OF FRICTION STIR WELDING IN ALUMINUM . 2011
Section2Weld Procedure QualificationFIGURE 2 (continued)Location of Test Specimens (8)Notes:1Discard at least 50 mm (2 in.) from each end of the test assembly2Direction of welding3Start area for:– 1 tensile test specimen– root and face bend test specimens (1)– macroetch specimen4Middle area for:– 1 tensile test specimen– root and face bend test specimens (1)– macroetch specimen5End area for:– 1 tensile test specimen– root and face bend test specimens (1)– macroetch specimen6Not used7Weld8150 mm (6 in.) minimum between Start area 3 and Middle area 4 and between Middle area 4 and End area 5Note 1: For welds fabricated from both sides, side bend specimens may be substituted.2Qualification of Weld Repair ProceduresWelding repair of friction stir welds by either FSW or arc welding processes requires qualification asindicated in Section 2, Table 1, Essential Elements 26 or 27. The repair procedure shall include the detailsof repair including the qualified Weld Procedure Specification (WPS). If base material nominal tolerances areoutside the qualified thickness range, a change in material thickness 5% from that qualified does not requirerequalification so long as all other essential elements remain unchanged and the base material thickness iswithin the nominal tolerances. The repair WPS procedure qualification test assembly size shall be as shownin Section 2, Figure 1. The size of the test assembly shall be sufficient to permit removal of the requiredtest specimens from the nominal start, middle, and end of the repair weld. The intent of this requirement isto obtain property variability that may exist for the various regions of a single friction stir weld repair.Friction stir welding of additional weld repair test assemblies to furnish test specimens is not permitted.For a given weld repair method, the entire thickness range may be qualified by testing at the minimum andmaximum thickness for a given defect type for each alloy and temper combination identified in Section 2,Table 1.3Operator QualificationThe FSW fabricator shall perform the destructive and nondestructive tests for FSW operator qualificationtest assemblies in accordance with Section 2, Table 3.The FSW fabricator shall adhere to the performance qualification limits described in Section 2, Table 1.Section 2, Table 1 indicates the material thickness range over which a weld operator may be qualified using aspecific weld procedure.The operator qualification test assembly size shall be as shown in Section 2, Figure 1. The size of the testassembly shall be sufficient to permit removal of the required test specimens from the nominal start, middle,and end of the repair weld. The intent of this requirement is to obtain property data for various regions alongthe weld length. Friction stir welding of additional test assemblies to furnish test specimens is not permitted.ABS GUIDE FOR THE APPROVAL OF FRICTION STIR WELDING IN ALUMINUM . 20115
Section42Weld Procedure QualificationFSW – Weld Procedure Specification (WPS) and Welder PerformanceQualification Record Requirements (WPQR)The FSW – Weld Procedure Specification (WPS) and Performance Qualification Requirements (WPQR)that are developed in accordance with Subsections 2/1 through 2/3 and Ref. 1 shall be provided to ABS.TABLE 1Essential Elements of a Friction Stir Welding ProcedureElement6Limits(1)Requires Requalification (2)Notes1.Base material compositionor conditionSpecific alloy used inqualification testChange in alloy or temper(to a higher-strength temperwithin the same alloy group)2.Base material thicknessSpecific thickness used inqualification testChange in material thickness 5% (3)3.Base material cleaningIdentified methodChange in method fromabrasive to chemical orvice-versaShall include degreasing andremoval of oxides from plateedges within 8 hours ofwelding4.Applicable joint designs –gap and sweep of adjoiningmembers (reference orsketches)Joint type used in qualificationtesting sets limitsChange in joint type orvariations – allowable range 1 mm (0.039 in.)A min/max range may bequalified.5.ProcessShall indicate whetherfixed-probe or self-reacting/bobbin or adjustable probe/retractable pin mode isemployedChange from the qualifiedmode6.Machine model and typeSpecific model, type, andcooling methodChange to a different modeltype, or cooling method7.Tool holder model and typeSpecific model, type, andcooling methodChange to a different modelor typeShall include whether toolholder employs activecooling8.Fixturing method (2)Limits to method appliedChange to method appliedShall include method offixturing (e.g., clamping,etc.). Shall include whetherfixturing employs activecooling, hydraulic, fixedclamping, adjustable9.Travel speedSpecific speed used inqualification test( 5% variation allowed)An increase or decrease ofmore than 5%Speed of tool travel traversingthe workpiece10.PositionPosition used in qualificationtestChange in position11.Preheat/Interpass/Post-WeldHeat Treatment (PWHT)Preheat/interpass/PWHTused in qualification testChange in preheat/interpass/PWHT12.Weld type – FSW(variation limited)Variation testedChange from or to doublesided or multiple passesSingle-sided, double-sided,number of passesABS GUIDE FOR THE APPROVAL OF FRICTION STIR WELDING IN ALUMINUM . 2011
Section2Weld Procedure QualificationTABLE 1 (continued)Essential Elements of a Friction Stir Welding ProcedureElementLimits(1)Requires Requalification (2)Notes13.Welding tool and probeSpecific tool material, design,and mode (i.e., fixed, bobbin,etc.) used in qualification testAny change to tool and probetype from that used inqualification testTool and probe material; tooland probe geometry/design[e.g., shoulder diameter, probediameter, probe length, probeshape (conical, cylindrical,etc), threads or no threads,number of flats (if applicable)tool ID, probe ID (if two-piecetool) and shoulder design];fabrication process (i.e.,fixed, bobbin, retractable).A tool is a component that isinserted into the tool holderthat consists of a largerdiameter shoulder and aprotruding smaller diameterprobe. A tool can be either amonolith or a two-piececomponent. A probe is acomponent protruding fromthe shoulder of the FSW toolbelow the surface of theparent metal during welding.14.Welding tool inspection andcleaning (2)Method used in qualificationtestA change in tool inspectionand cleaning methodIndicate the condition of tooland probe prior to weld (i.e.,new, used and cleaned, usedand not cleaned, indicationof wear on tool). Indicatecleaning method.15.Process control method (2)Method used in qualificationtestChange, for example, to orfrom force or position controlForce or Position control16.Process loadsSetting used in qualificationtest ( 10% variation allowed) 10%Z-axis (forge) loads at aminimum; recommendmonitoring X-axis loads17.Tool rotational speedSetting used in qualificationtest ( 5% variation allowed) 5%During plunge, dwell time atstart and end of weld, andduring welding. The dwelltime at the start of weld isthe time interval between thecompletion of tool plungeand the start of travel. Thedwell time at end of weld isthe interval of time aftertravel has stopped but beforethe rotating tool has begunto withdraw from the weld.18.Tool rotational directionFor "featured" tools designedfor specific rotationaldirection, qualification islimited to direction used inqualification testing. Forfeatureless tool, one directionqualifies the other.Change to or from clockwiseor counterclockwise if"direction-specific" tooldesign used (e.g., threadedtool designed to rotate in aspecific direction)Clockwise (CW) orcounterclockwise (CCW)ABS GUIDE FOR THE APPROVAL OF FRICTION STIR WELDING IN ALUMINUM . 20117
Section2Weld Procedure QualificationTABLE 1 (continued)Essential Elements of a Friction Stir Welding ProcedureElement (2)Limits (1)Requires RequalificationNotes19.Lateral tool offset anddirectionTool offset and directionused in weld procedurespecificationChange from tool offset plusor minus tolerance specifiedin weld procedure qualificationor change in rotationaldirection of a tool withlateral offset.Distance from the toolcenterline axis to one side ofthe joint centerline. Tool iseither offset towards theadvancing side or retreatingside of the weld20.Tool tilt anglePitch angle(s) used inqualification testChange in pitch angleoutside range used inqualification test.Angle of tool (vertical axis)with respect to workpiecesurface21.Side tilt angleSide tilt angle(s) used inqualification testChange in side tilt angleoutside range used inqualification test.Angle by which the tool isinclined away from thevertical, in a directiontransverse to the weldingdirection.22.Post weld surface dressingNot permitted prior to NDTand mechanical testing23.Tack weldingTacks shall be welded by aqualified welder using anapproved WPS. Tacks shallbe no more than 5% of weldlength.Tacks 5% of weld lengthMethod, length, and frequencyalong length of joint line24.Exit hole repair or removalmethod (2)Any demonstrated exit holerepair or removal procedure(can be qualified separatelyfrom FSW procedure)Change in exit hole repairprocedure. Not required ifexit hole is removed.Method used to eliminatethe exit hole25.Restart procedure (2)Limited to procedurequalified, if anyChange from the qualifiedprocedureShall describe proceduresfor restart weld in case ofmachine malfunction or toolbreakage. Procedure shallinclude tool removal method,termination area cleaningand preparation method,restart location relative toweld termination point.26.Friction Stir Weld Over aFriction Stir Weld(i.e., Friction Stir Re-weld) (2)Any FSW over an existingFSW shall require a separateFSW procedure specificallyapproved by ABS Materialsprior to implementationAny change in the setup of afriction stir re-weld over anexisting friction stir weld shallrequire a new qualification.27.Fusion Weld Repair of aFriction Stir Weld (2)Base metal used inqualification shall be frictionstir welded using the samenumber of passes as thefriction stir weld to berepaired.28.Shielding Gas(special applications)Composition, flow rate,addition or deletion, etc.Change requires requalificationNotes:81Any change in an essential element requires requalification if it is outside the allowable limits above.2Facility shall provide descriptive narrative related to application and limits of this essential element. For narrativerelated to Element 26 or Element 27, the precise nature of the repair and why it is needed shall be specified. Thequalified repair procedure shall only be used to repair the specific defect(s) indicated in the narrative.3In production, if base material nominal tolerances are outside the qualified thickness range, a change in materialthickness 5% from that qualified does not require requalification so long as all other essential elements remainunchanged and the base material thickness is within the nominal tolerances.ABS GUIDE FOR THE APPROVAL OF FRICTION STIR WELDING IN ALUMINUM . 2011
Section2Weld Procedure QualificationTABLE 2Weld Procedure Qualification Test Requirements (1, 2, 3, 8)Test MethodsTesting RequirementsCommentsTransverse Tensile (5)3 specimensSpecimens taken from nominal start, middle, andend of weld.Transverse GuidedBend (4, 5)3 face bends and 3 root bends1 face bend specimen and 1 root bend specimentaken from each area – nominal start, middle, andend of weld.For thickness 19 mm (3/4 in.) 3 side bends may besubstituted for the 3 face bends. The 3 root bendsare still required.Macroetch (5)3 specimensSpecimens taken from nominal start, middle, andend of weld.Visual (5, 6)100% required prior to other NDTUltrasonic (6)100% requiredRadiographicInspection (6)100% requiredEtched DyePenetrant (7)100% requiredUnless qualified for an unetched specimenNotes:1Testing specimens and results to be to the requirements of Ref. 1.2Repair of qualification test assemblies is not permitted.3Retests of qualification test assemblies are not permitted.4For welds fabricated from both sides, a total of six side bends shall be used in lieu of three face and threeroot bends.5Visual inspection shall be performed prior to any destructive testing.6NDT procedures and requirements are provided in Ref. 3 ABS Guide for Nondestructive Inspection ofHull Welds. Acceptance criteria shall be to Class A. Additional NDT requirements are in Subsection 3/6.7For procedure qualification in accordance with Ref. 1, photographs of chemical polish (etch) specimens shallbe provided to ABS Materials for review and approval prior to beginning production. Ref. 6, NASA documentPRC-5010C, Process Specification for Pickling, Etching, and Descaling of Metals, may be consulted for guidelineson etchant selection.8A welding procedure qualification test plate schematic with locations for removal of test specimens is shownin Section 2, Figure 2.9The tensile strength of each specimen, when it breaks in the weld, is not to be less than the minimumspecified tensile strength of the base metal. When broken in the base metal and the weld shows no signsof failure, is not to be less than 95% of the minimum specified tensile strength of the base material.10Guided bend tests after bending shall not show any cracking or other open defect exceeding 3.2 mm(1/8 in.).11NDE acceptance criteria shall be in accordance with the requirements of Class A welds as contained inABS Guide for Nondestructive Inspection of Hull Welds.ABS GUIDE FOR THE APPROVAL OF FRICTION STIR WELDING IN ALUMINUM . 20119
Section2Weld Procedure QualificationTABLE 3Operator Qualification Test Requirements (2, 3, 6, 8)Test MethodsTesting RequirementsCommentsTransverse Tensile (1)3 specimensSpecimens taken from nominal start, middle, andend of weld.Transverse GuidedBend (1, 3, 4)3 face bends and 3 root bendsSpecimens taken from nominal start, middle, andend of weld. F For thickness 19 mm (3/4 in.) 3side bends may be substituted for the 3 face bends.The 3 root bends are still required.Macroetch (1, 4)3 specimensSpecimens taken from nominal start, middle, andend of weld.Visual (5)100% required prior to other NDTUltrasonic(5)100% requiredRadiographicInspection (5)100% requiredEtched and UnetchedDye Penetrant (7)100% requiredUnless qualified for an unetched specimen.Notes:101Testing specimens and results to be to the requirements of Ref. 1.2Qualifying an operator for friction stir welding with one 5000 series base material of NAVSEA TechPub 248 qualifies that operator to weld all 5000 series base materials 2/3T to 4T of the original test withinthe requirements of this Guide. Similarly, qualifying an operator to friction stir weld one 6000 seriesaluminum alloy qualifies that operator to weld all 6000 series aluminum alloys 2/3T to 4T of the originaltest within the requirements of this Guide. For other materials, approval of ABS NED Materials orHouston Materials is specifically required.3Repair of qualification test assemblies is not permitted.4For welds fabricated from both sides, a total of six side bends shall be used in lieu of three face and threeroot bends.5NDT procedures and related requirements shall conform to Ref. 3 ABS Guide for NondestructiveInspection of Hull Welds and Ref. 1. Additional NDT requirements are in Subsection 3/6.6Operators qualifying for friction stir re-weld of an existing friction stir weld shall be qualified to a specificprocedure according to this document.7Ref. 6 NASA document PRC-5010C, Process Specification for Pickling, Etching, and Descaling ofMetals, may be consulted for guidelines on etchant selection.8A welding procedure qualification test plate schematic with locations for removal of test specimens isshown in Section 2, Figure 2.9The tensile strength of each specimen, when it breaks in the weld, is not to be less than the minimumspecified tensile strength of the base metal. When broken in the base metal and the weld shows no signsof failure, is not to be less than 95% of the minimum specified tensile strength of the base material.10Guided bend tests after bending shall not show any cracking or other open defect exceeding 1.6 mm(1/16 in.).11NDE acceptance criteria shall be in accordance with the requirements of Class A welds as contained inABS Guide for Nondestructive Inspection of Hull Welds.ABS GUIDE FOR THE APPROVAL OF FRICTION STIR WELDING IN ALUMINUM . 2011
Section 3: FSW Production Quality Control and NDT RequirementsSECTION13FSW Production Quality Control and NDTRequirementsRecordsFSW fabricator records are required for each friction stir weld. The records are intended to providedocumentation that each FSW meets all the requirements of this Guide. These records shall document thatall required inspections were performed and include inspection results. The records are to be kept in accordancewith the Rule requirements.2Inspection Before Production FSW2.1Verification Before WeldingBefore welding, the FSW Fabricator shall verify the following:i)The essential elements of the production job are consistent with the approved qualification as requiredby Section 2, Tables 1 and 2.ii)The operator has a valid qualification/certification for the intended job in accordance with Section 2,Table 3.2.2Joint Setup Variab
Section 1 General 2 ABSGUIDE FOR THE APPROVAL OF FRICTION STIR WELDING IN ALUMINUM . 2011 Probe - Part of the welding tool that extends into the workpiece to make the weld. Retreating Side of Weld - Side of the weld where the direction of tool rotation is opposite to the welding direction. Self-reacting (Bobbin) Tool - Tool with two shoulders separated by a fixed length probe or an .