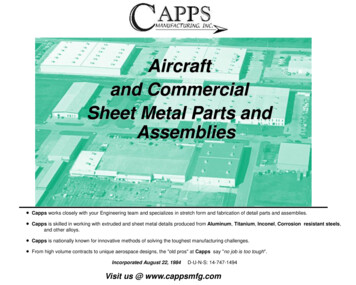
Transcription
Aircraftand CommercialSheet Metal Parts andAssemblies Capps works closely with your Engineering team and specializes in stretch form and fabrication of detail parts and assemblies.Capps is skilled in working with extruded and sheet metal details produced from Aluminum, Titanium, Inconel, Corrosion resistant steels,and other alloys. Capps is nationally known for innovative methods of solving the toughest manufacturing challenges. From high volume contracts to unique aerospace designs, the "old pros" at Capps say "no job is too tough".Incorporated August 22, 1984- Accredited -D-U-N-S: 14-747-1494Visit us @ www.cappsmfg.com
Quality Policy Capps Manufacturing, Inc. is dedicated to be thepreferred supplier of aircraft detail parts,components, and assemblies by providing ourcustomers the best value in:Meeting the customers expectations.Being fair and ethical.Being resourceful, disciplined and flexible.Providing 100% on-time delivery.Providing 100% quality and reliability.Continuously reducing cost and lead-times.Being profitable.
Barney L. Capps, President and majority owner of Capps Manufacturing, Inc., started in theaircraft business in 1952. In 1962, he became Plant Manager of H & H Parts Co. and washeavily involved in the Learjet Model 23 program developing all tooling, production parts andassemblies for the engine nacelles, including static test, access doors, various small assembliesand detail parts. This relationship with Learjet continued through development of the 35, 36,and 55 models and continues today with the 45 and 60 model programs. In 1983, Barneyleft H & H Parts Co. to start Capps Machine, Inc. now Capps Manufacturing, Inc.Ronald L. Capps, Vice President and minority owner of Capps Manufacturing, Inc. Ron’sEducation includes; Bachelor of Science Business Administration and a Masters in ManagementInformation Systems, both from Friends University in Wichita, KS. In addition, Ron is CertifiedProduction & Inventory Management (CPIM) accredited from the American Production & InventorySociety (APICS). Ron worked for the Boeing Commercial Airplane Co. for 19 years. At Boeing,Ron gained experience in Industrial Engineering, Operations Systems, and his last five yearsworking with cycle time reduction and Lean Manufacturing concepts for major assembly of theforward nose fuselage on the Boeing 747, 767, and 777 programs. Ron joined Capps Manufacturingfull-time in July of 1999.
Meet Our Management TeamBarney L. CappsPresidentDon G. SmithSenior Manager Marketing/M.E.Nathan R. ChambersAssembly/Shipping ManagerCody LassleyQuality ControlEd L. StephensQuality, Safety,and Regulatory ComplianceRon L. CappsVice PresidentTony Henning,Processing LineManagerSteven L HudsonIE/IT/CI ManagerRay Schoenecker,Production ManagerRichard Laake, Facilities/ Maintenance Manager4
CapabilitiesIn-House Tooling SKIN & LEADING EDGE STRETCH FORMING STRETCH FORM DIES EXTRUSION STRETCH FORMING HYDRO BLOCKS FLUID CELL FORMING 5 AXIS CNC ROUTE FIXTURES HYDRO FORMING & DRAW FORMING DRAW FORM TOOLING 3 & 5 AXIS CNC MACHINING FORM BLOCKS THERMAL PROCESSING (Anneal, Age Harden & Heat Treat) ASSEMBLY FIXTURES CHEMICAL PROCESSING (ChemFilm, Anodize, Pent., Prime) JOGGLE DIES COMPONENT ASSEMBLY ROUTER BLOCKS PUNCH PRESS BLANKING TOOLS ROLLFORMING WELD FIXTURES TIG WELDINGCAD/CAM CATIA V.5 Design and Programming Vericut Verisurf verification software Translators including CATIA Portable Romer CMM with 48"radial ability Kubotek Validation & Comparison software Leica Laser Tracker5
Customer BaseJust a sample of our many customersAIDC (Aerospace Industrial Development Corporation)Bombardier – Learjet, Inc.Spirit AeroSystems, Inc.ASC Signal CorporationBoeing Defense & SpaceCobham Mission SystemsGKN AerospaceGulfstream Aerospace Corp.Weatherford Aerospace, Inc.TEXTRON AVIATION (Beechcraft/Cessna/Hawker)MHI CanadaShenyang Aircraft CorporationNORDAM (Northeast Oklahoma Repair Development and Manufacturing)Arnprior AerospaceCPI Aerostructures, Inc.Lockheed Martin AircraftMiddle River Aircraft SystemsFokker Aerostructures B.V.6
Just a sample of our many customers
Capps Manufacturing Campus – 300K Sq. Ft.Building 4 - 79,750 Sq. Ft.manufacturing facility located at2222 S. Custer. - LeasedBuilding 3 - 79,750 Sq. Ft. Assembly,Shipping and Process Line facility locatedat 2120 S. Custer.Capps Proprietary8
Key Equipment ListMachineCyril BathCyril BathCyril BathHuffordHuffordHuffordHuffordErcoErcoErcoCapp DesignVerson WheelonHPMCapp DesignCapp DesignCincinnatiDMS Router (3)DMS Router VTHAASSNKFadal (2)FadalFadalHAASDespatch (2)GehnrichOSIDespatch (2)LVDVersonSummitWebbWarcoNiagraV&OBlissPress RiteModelVTL 800V-75V-30A-15A-12 (2)A-7A-10 (2)DescriptionSkin & Leading Edge StretchStretch Press - ExtrusionStretch Press - ExtrusionStretch Press - ExtrusionStretch Press - ExtrusionStretch Press - ExtrusionStretch Press - ExtrusionSkin & Leading Edge StretchSkin & Leading Edge StretchSkin & Leading Edge StretchA-12Stretch Press - ExtrusionFluid Form PressHydro Press (rubber forming)Hydro PressHydro Press5 axis CNC Gantry Mill5 axis CNC Router3 axis CNC Machining centerVR115 axis CNC Machining centerHPS-120A 5 axis CNC Machining center80303 axis CNC Machining center60303 axis CNC Machining center40203 axis CNC Machining centerVF43 axis CNC Machining centerDrop bottom heat treat ovenAge harden ovenAge harden ovenAge harden ovenPower squaring shearBrake pressBrake pressPower rollPunch pressPunch pressPunch pressPunch pressPunch pressSize800 ton 15'x30' sheet CNC32' Grip- 75 ton CNC24' Grip- 30 ton CNC45' Grip- 225 ton30' Grip- 60 ton18' Grip- 23 ton18' Grip- 17 ton CNC460 ton 14' die table300 ton 10' die table200 ton 10' die table18' Grip- 70 ton16200 ton 36"x120" die tables2500 ton, 4'x8' die tables300 ton 3'x5' die table100 tonx 200" y 140" z 60"x 182" y 120" z 60"x 120" y 40" z 30"x 175" y 55" z 39.3"x 80" y 30" z 30"x 60" y 30" z 30"x 40" y 20" z 20"x 50" y 20" z 25"16'L x 12'H x 6'W, 1000 deg F30'L x 6'H x 8'W, 600 deg F8'L x 8'H x 8'W, 600 deg F3'L x 3'H x 3'W, 600 deg F16' x 1/4"10' 150 ton3' 25 ton8' x 4" dia. Rolls150 ton150 ton50 ton25 ton15 ton
FramesFrame & DoublerGulfstream Model G650Boeing 737 Thrust ReverserNose BulkheadChannel & AnglesBombardier-Learjet Model 60 Thrust ReverserLockheed C-141 Trust Reverser
Lockheed C-141 Trust ReverseSupport AssemblyBombardier-Learjet Speed brake FAJBoeing 737 Leading EdgeNose gear door assembly
Hufford A-1545’ Grip – 225 ton
Steel Frames “Z” & “L”42”Extruded Hat SectionCyril Bath V-75 CNC32’ Grip – 75 tonCyril Bath V-30 CNC24’ Grip – 30 tonHufford A-12 (2)30’ Grip – 60 tonHufford A-10 (2) CNC18’ Grip LengthHufford A-7 CNC18’ Grip – 23 tonCapps Design A-1220’ Grip – 270 ton72”Sheet Metal Channel
Cyril Bath VTL 800 Ton Skin Stretch 800 tons of Forming Pressure. Complete CNC controls of all functions. Capable of Leading Edge and Drape forming up to 15’ long and “End Pulled” skins up to 30’ long. 400 tons of down acting bulldozer pressure for reverse contour work. Curving auxiliary grippers (24” radius min.).CH-47Side Skin
2121 S. Edwards Wichita, KS 67213-1868(316)942-9351 FAX (316)942-6771 www.cappsmfg.comLeading Edge – Up to 16’Titanium SkinParker HannifinStretch Press3 tonErcoStretch Press150 tonErcoStretch Press – Leading Edge300 tonErcoStretch Press460 ton
46”36”Sheet Metal “Z” Shaped FrameAluminum Bulkhead66”20”Stang Inner PanelHPMFirewallHydro Press2500 Ton Bed 4’x8’
Verson Wheelon 16200R 36-120 Fluid Form Press.Tray size: both 36”x120” with bottom depth of 4 ½” and 6 ½”. Capacity Tonnage – 16,200.Pressure Forming – Maximum psi 7,500.
FramesFramesGulfstream Model G650HAAS VF43 Axis CNC MCTable 50” x 20”Gulfstream Model G650HAAS VR115 Axis CNC MCTable 120” x 40”
Stretch Form BlockDMS5 Axis CNC RouterTable 182” X120” (2)Table 300” X120” (1)737 Bulkhead Web
Hydro Block ToolingStretch Block ToolingSNK HPS-120A5 Axis CNCTable 169”x48”Fitting
5’SparStall Fence Hog OutFadal 40203 Axis CNCTable x40”y20”z20Fadal 60303 Axis CNCTable x60”y30”z30Fadal 80303 Axis CNCTable x80”y30”z30Fadal 80303 Axis CNCTable x80”y30”z30
Cincinnati5 Axis CNC Gantry MillTable 104”x180”
Despatch Drop Bottom Oven.Load capability is 6’ width x 16’ length x 12’height with Operating Range up to 1,000 deg. F.pAC7102 & AC7101/5AMS2770, AMS-H-6088- Accredited -Heat Treat
ChemicalProcessing andandPaint FacilityChemicalProcessingPaint Facility14'Powdered WT Storage3'3'3'14'City WaterMasking SuppliesN2N1ExhaustAnodizeCon.Alk.Wm H20 Ex Seal Ex117 -Dilute Chromate Seal Tank115 - Warm Water114 - Immersion Rinse113 - Spray Rinse116 - Boric/Sulfuric Acid Anodize5'111 - Immersion Rinse109 - Spray Rinse110 - Deoxidizer 6/16108 - Immersion Rinse106 - Aluminux Etch L107 - Immersion Rinse105 - Ridoline 4355104 - Immersion Rinse103 - Immersion Rinse101 - Ridoline 4355102 - Immersion Rinse3'RACKINGANDLOADAREA112 - Alodine 1600Exhaust3 ft Wide Walk Way3'3'Office Area3'Con.Cr 6NaOHChem Tote TanksOperator Walk WayProcess &WT AlkalineChemicalStorageUNLOADAREACr 6ControlAreaWaste andMEK StoragepPaint Mix Room“Control Area”Spray Paint Booth3'MaintenanceCribRinseWaterPumpTank LineHoist3'OfficeDI H2O10'HClChem FeedFinal Discharge TankDrain LineMen’sRest RoomsR1Filter PressProcess & WT Acid StorageWomen’sRest RoomsFlcMasking AreaMechanicalRoomFuture Lab(not in use)Clarifier- Accredited -FINALINSPECTION3'14'Wet Line:Boric Acid Anodize – BAC 5632Chem Film – AMS 2473, BAC 5719,CSFS027, MIL-C-5541, MIL-DTL 5541, RPS13.53Clean – BAC 5763, BAC 5765, BAC 5786,BMS 11-6, CSFS 035, CSFS 036, CSFS037, CSFS 039, CSFS 044, CSFS 046,CSFS 047, CSFS 048, CSFS 049, MIL-P85891,TABLES/RACKS FOR FIXTURES AND WALL GRID FOR PHOTOGRAPHSPaint:BAC 5736, BAC 5793, BAC 5710, BAC5755, BAC 5882, BS25032, BS22455,BS361, CSFS 084, CSFS 007, MIL-F18264, MISL-PRF-23377, DHC 5.2,NP5059, RPS 13.75, RPS 13.97, RPS13.98Penetrant:AMS-2644, ASTM E 1417, BAC 5423,BAC 5652, BS25691, BSS 7039, CSTI002, MIL-STD-1907, NAS 410Penetrant Inspection RoomDeveloperProcessBasketPush CartBridge Crane Hoist3'INCOMING PARTS FROM MANUACTURING10'8'MAINTENANCEWORK AREAHoldingRECEIVINGINSPECTIONAND PARTSPHOTOGRAPHINGDrip enetrantInspectionSpray RinseWash BasinElectricalGear Box3'Hexavalant ChromiumOSHA “Regulated Area”NonConformanceArea3'Air Compressor in the northeast cornerof the south half of the building.3'BoricAcid3'CaClBoiler Room3'3'uvTABLES AND MASKING SUPPLIES3'POTW Waste Water DischargeOven3'
Chemical Processing and Paint FacilityPaint BoothWaste Water TreatmentAnodized PartPaint OvenPaint BoothpPainted Parts20’Processing LinePenetrant BoothFinished Parts20’Alodined Part
LocationClose to Mid-Continent InternationalAirport with easy access to U.S. 54 andInterstate Highways I-35, I-135 & I-235.2121 S. EdwardsWichita, Kansas 67213Phone: 316-942-9351
Technical Approvals & CertificationsCheck out our complete list of OEM approvals on our web site.http://www.cappsmfg.com/approvals/Request a Quote or Contact UsUse our web site to request a quote or contact www.cappsmfg.com/contact-us/- Accredited -Snap the code to theright with your smartphone to request aquote using ourconvenient on-lineform!
Our Vision and Strategy for the FutureTo do what ever it takes to gain and maintain the respect and admiration of ourCustomers, Employees, and the Community.By Recruiting, retaining, and motivating the most highly skilled employees available.Which will help us Increase capacity with current levels of capabilities by becoming more efficient andimplementing lean manufacturing concepts.Which will allow us to make profit and reinvest Striving to become self contained by bringing outsourced manufacturing processesinternally as cost/benefits become feasible.And Become “one-stop-shopping” for our Customers by offering services from special toolingto detail parts fabrication to assemblies.Which will make us the preferred Partner for our Customers and for them to share in our evolving from a job shop tobecome a full design/build aerospace manufacturing facility.Visit us @ www.cappsmfg.com
Barney L. Capps, President and majority owner of Capps Manufacturing, Inc., started in the aircraft business in 1952. In 1962, he became Plant Manager of H & H Parts Co. and was heavily involved in the Learjet Model 23 program developing all tooling, production parts and assemblies for the engine nacelles, including static test, access doors, various small assemblies