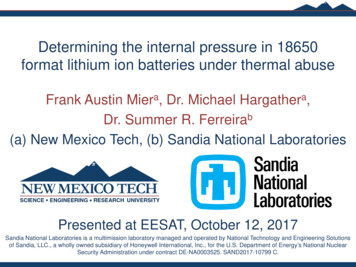
Transcription
Determining the internal pressure in 18650format lithium ion batteries under thermal abuseFrank Austin Miera, Dr. Michael Hargathera,Dr. Summer R. Ferreirab(a) New Mexico Tech, (b) Sandia National LaboratoriesPresented at EESAT, October 12, 2017Sandia National Laboratories is a multimission laboratory managed and operated by National Technology and Engineering Solutionsof Sandia, LLC., a wholly owned subsidiary of Honeywell International, Inc., for the U.S. Department of Energy’s National NuclearSecurity Administration under contract DE-NA0003525. SAND2017-10799 C.
Battery venting under abuse conditions Most cells have a vent torelieve pressure duringthermal runaway– Positive terminal of18650 Venting avoids caserupture but still presentssafety concerns includingflammability Describing these eventscan aid in understandingrisks and smart design LG MG1 (NMC)Overcharge and heatingElapsed time: 160 msFrame rate: 5 kHz2
Previous destructive testing at NMT High speed schlieren allowed imaging of venting gassesand liquid droplets F. A. Mier, R. Morales. C. A. Coultas-McKenney, M. J.Hargather, J. Ostanek, Overcharge and thermaldestructive testing of lithium metal oxide and lithiummetal phosphate batteries incorporating opticaldiagnostics, J. of Energy Storage 13C (2017) pp. 378386.3
Describing the external dynamics of ventingstarts with quantifying internal pressure Current research focuses on the development of twoexperiments:– Pressurization of battery caps and precise directmeasurement of burst pressure for comparison tostrain-pressure curve.– Measurement of case strain under thermal abuseconditions for calculation of to internal pressurebefore and after venting onset. Tests are intended to be performed on 18650 formatbatteries from any manufacturer and with variouschemistries.4
Directly measurements with vent capsremoved from 18650 cells Pipe cutter separates capfrom cell at crimp Foil tab is cut to separatefrom cathode Experiments can beperformed on vent capsfrom any 18650 formatbattery Measurements includeburst pressure andopening area5
Battery vent cap holder for directpressurization tests Sealed mounting ofbattery caps– Adjustability forsize variance Designed to chokeflow at vent cap– Minimum crosssection Known crosssectional area atpressure tap6
Development of a direct pressurizationtest apparatus Pressure gradually increased in 76 L tank withcompressed dry air National Instruments cDAQ system monitoring– Static and stagnation pressures (1 kHz)– Stagnation and ambient temperatures (100 Hz)7
Investigation into determining ventopening area Maximum opening area of vents varies widely betweenmanufacturers– A123: 11.2 mm2– LG: 12.7 mm2– Panasonic: 34.3 mm2 Determining actual opening area helps describe ventingcharacteristics of gases and liquids This measurement can be combined with direct pressuretests– Opening area measurement is made after vents open– Requires no additional vent caps8
Opening area calculation fromisentropic flow relationships Mach number at the flow constriction via pressure ratio:𝑃𝑃𝑡𝑡𝛾𝛾 1 2𝑀𝑀 1 2𝑃𝑃𝛾𝛾𝛾𝛾 1 Vent area is the sonic condition (A*) for choked flow:– Area (A) and Mach number (M) reference constriction𝛾𝛾 12 2𝛾𝛾𝛾𝛾 1𝐴𝐴12 𝐴𝐴 𝑀𝑀 1 𝛾𝛾 1 𝑀𝑀22 Similar calculation made when flow is not choked– Define an arbitrary sonic cross section (A*)– Assume static pressure at the vent is atmospheric9
Opening area validation tests withknown orifices Laser cut acrylic orifice plates to replace battery cap– Twenty individual circular orifices plates– Three mock 18650 vent caps Accumulator tank pressurized to 40 psig for each test Manually operated ball valve to simulate vent opening10
Sample of data recorded during asingle validation test (mock Panasonic)Valve is opened11
Validation test results with orifice plates12
Repeated trials with orifice plates13
Initial testing attempts with vent capsfrom LG HE2 (LCO) cells Reached accumulatortank pressure rating of150 psig without burst Connected caps directlyto 1,400 psig– Minimized flow ratewith needle valves Caps burst at:1. 281.5 psig2. 264.5 psig3. 289.0 psig14
Burst vent caps remain open and areretested to calculate area Maximum possibleopening area: 12.7 mm2 Calculated area of burstvents:1. 7.3 mm22. 7.1 mm23. 6.5 mm2 Not enough data tosuggest trends betweenopening area and burstpressureVent opening15
Quantifying internal pressure duringthermal abuse tests to describe venting Pressure is an importantparameter in explaininggas and liquid flows Strain provides a noninvasive approach forpressure calculation Able to perform tests onlive cells with various:– Heating rates– Manufacturers– Chemistries– States of charge LG MG1 (NMC)Thermal abuseElapsed time: 30 msFrame rate: 20 kHz16
Pressure will also be inferred from twomeasurements of strain on the cell case Measuring hoop andlongitudinal strain– Functions oftemperature andpressure No modifications arenecessary to cells whichcould skew results Can test on 18650 cellswith different chemistriesand manufacturers17
Calculating internal pressure fromstrain measurements Strain measurements will be the sum of stress due tointernal pressure and linear thermal expansion of thebattery case:– Circumferential component:𝑃𝑃𝑃𝑃 𝛼𝛼𝑑𝑑𝑑𝑑𝜀𝜀Η 𝐸𝐸2𝑡𝑡– Longitudinal component:𝑃𝑃𝑃𝑃 𝛼𝛼𝑑𝑑𝑑𝑑𝜀𝜀L 𝐸𝐸4𝑡𝑡 Since εH and εL are both measured, internal pressure (P)can be solved for:𝑡𝑡𝑃𝑃 𝜀𝜀𝐻𝐻 𝜀𝜀𝐿𝐿4𝐸𝐸𝐸𝐸18
Considerations for internal pressurecalculation Pressure equation:𝑡𝑡𝑃𝑃 𝜀𝜀𝐻𝐻 𝜀𝜀𝐿𝐿4𝐸𝐸𝐸𝐸 Young’s modulus (E) and case thickness (t) are notprecisely known without further testing Maximum case strain and internal pressure can beassumed to occur at vent burst– Strain-pressure curve can be calibrated with directlymeasured burst pressures Potentially non-uniform pressure inside cells due tolocalized internal failure locations– To be addressed by measuring multiple pairs of straingauges located in different locations on the battery 19
Laboratory setup installed at NMT13241. Lab overview2. Battery holder3. Chamber withinsulation box4. Window view 20
Test chamber for strain measurementexperiments21
Test chamber end-cap instrumentationports22
Data acquisition system detailsThermocouples: Heat flux through pipe Gas temperature Battery terminal Battery sideStrain gauges: Hoop strain Longitudinal strainAnalog voltage: Chamber static pressure23
Calibration tests performed todetermine test chamber heating rate Tests performed between 20% and 100% of maximumheater power of 2,340 W Nominal heating rate determined by linear fit24
Planned trials for strain measurementexperimentValidation experiments with simplified geometries: 18 mm diameter, thin wall steel tube to confirm identicalthermal strain Pressurized gas cylinder under increasing temperatureas internal pressure response can be predictedaccuratelyTests on LG HE2 cells at 100% SOC: Trial with two strain gauge pairs placed on oppositesides of battery Sets of three trials with single pair of gauges on cell at2 C/min and 5 C/min25
Progress and expected outcomes fromthermal abuse and direct pressurization testing Designed and validated test apparatus to measure theburst pressure and opening area of vent caps from18650 cells Direct pressurization tests describe when vent caps canbe expected to open and how subsequent flow of gasesand liquids will occur Fabrication and heat rate calibration for test chamber tobe used for measurement of battery case strain Case strain measurements will give quantification of howinternal pressure increases leading up to battery venting26
Questions?Shock and Gas Dynamics Lab: www.nmt.edu/mjh/Frank Austin Mier: frank.mier@student.nmt.eduDr. Michael Hargather: michael.hargather@nmt.eduDr. Summer Ferreira: srferre@sandia.govThis work is funded by the U.S. Department of Energy Officeof Electricity under contract: PO 173987527
measurement of burst pressure for comparison to strain-pressure curve. – Measurement of case strain under thermal abuse conditions for calculation of to internal pressure before and after venting onset. Tests are intended to be performed on 18650 format batteries from any manufacturer and with various chemistries. 4. Directly measurements with vent caps removed from 18650 cells Pipe .