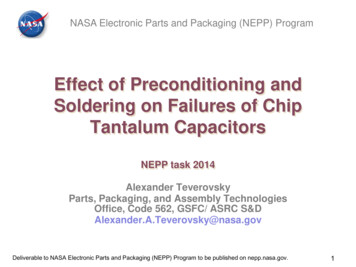
Transcription
NASA Electronic Parts and Packaging (NEPP) ProgramEffect of Preconditioning andSoldering on Failures of ChipTantalum CapacitorsNEPP task 2014Alexander TeverovskyParts, Packaging, and Assembly TechnologiesOffice, Code 562, GSFC/ ASRC S&DAlexander.A.Teverovsky@nasa.govDeliverable to NASA Electronic Parts and Packaging (NEPP) Program to be published on nepp.nasa.gov.1
List of Acronyms and SymbolsACalternating currentMSLmoisture sensitivity levelCcapacitancePIpolyimideCCSconstant current stressRHrelative humidityCTEcoefficient of thermal expansionS&Qscreening and qualificationDCLdirect current leakageSBDSsimulated breakdown screenDFdissipation factorSCTsurge current testEDSenergy dispersive analysisSEMscanning electron microscopyEMelectrical measurementsSTDstandard deviationESRequivalent series resistanceTtemperatureHVhigh voltageTSDterminal solder dipIRinfra redVBRbreakdown voltageLDClot date codeVRrated voltageMCmolding compoundX-sectcross-sectionDeliverable to NASA Electronic Parts and Packaging (NEPP) Program to be published on nepp.nasa.gov.2
AbstractSoldering of molded case tantalum capacitors can result in damage toTa2O5 dielectric and first turn-on failures due to thermo-mechanicalstresses caused by CTE mismatch between materials used in thecapacitors. It is also known that presence of moisture might cause damageto plastic cases due to the pop-corning effect. However, there are onlyscarce literature data on the effect of moisture content on the probability ofpost-soldering electrical failures. In this work, that is based on a casehistory, different groups of similar types of CWR tantalum capacitors fromtwo lots were prepared for soldering by bake, moisture saturation, and longterm storage at room conditions. Results of the testing showed that bothfactors: initial quality of the lot, and preconditioning affect the probability offailures. Baking before soldering was shown to be effective to preventfailures even in lots susceptible to pop-corning damage. Mechanism offailures is discussed and recommendations for pre-soldering bake aresuggested based on analysis of moisture characteristics of materials usedin the capacitors’ design.Deliverable to NASA Electronic Parts and Packaging (NEPP) Program to be published on nepp.nasa.gov.3
Outline Background. History case. Literature data. Test plan. Test results. Initial characterization of the lots.Effect of preconditioning on AC and DC characteristics.Solder reflow profile.Effect of preconditioning on post-soldering characteristics andfailures. Effect of the terminal solder dip testing. Discussions. Moisture in solid chip tantalum capacitors. Mechanism of failures. Summary and recommendations.Deliverable to NASA Electronic Parts and Packaging (NEPP) Program to be published on nepp.nasa.gov.4
Background Both, an engineering and a flight units failed withina few seconds after powering on for the first time. The failure was due to CWR29 10uF 35V capacitors used in the 15Vpower line. Maximum current in the line was limited to 1 A. After capacitors were replaced, the unit operated normally. Out of 20 LDC1307 capacitors from Mfr.A used in the unit, 10 failedcatastrophically. Out of 18 similar capacitors from Mfr.B that were also used in this unit,none failed short circuit. Analysis of leakage currents after desoldering showed that a largeproportion of capacitors from both lots had substantially degradedcharacteristics (70% from Mfr.A and 40% from Mfr.B). Out of two capacitors from Mfr.A that were also used on the board, butinactivated during the first power on, one sample failed short circuit atR 6.8 kOhm. Reflow soldering temperature profile was close to the one recommendedfor tantalum capacitors by manufacturers.Deliverable to NASA Electronic Parts and Packaging (NEPP) Program to be published on nepp.nasa.gov.5
Background, Cont’d A review of production test documents did not reveal any anomaly with LDC1307. A review of the system design and test condition ruled out the possibility ofvoltage overshooting of the parts during turn-on of the unit. Visual and X-ray analysis of failed capacitors did not show any defects. Stripping of molding compound by Mfr.A and GSFC lab showed that allcapacitors with LDC1307 had damage at the anode shoulder. IR images of 6failed capacitors confirmed that the location of damage is at the anode shoulder. This, as well as comparison with the other lot used inthe unit, lead to a suspicion that the problem islot-related. Another possibility that is usually considered whenfirst turn-on failures happen, is that the capacitorswere damaged during soldering. LDC1307 was marked MSL 1, which means unlimitedfloor life and no need for bake before soldering.The purpose of this study is to evaluate theeffect of preconditioning and lot-t-lot variationson the probability of post-soldering failures.Top view (anode shoulder) of astripped capacitor showingdamaged sitesDeliverable to NASA Electronic Parts and Packaging (NEPP) Program to be published on nepp.nasa.gov.6
Literature Data: Effect of Soldering It is well known that molded case tantalum capacitors can be damagedduring soldering and related to damaging first power-on failures are one ofthe major reasons for voltage derating [1]. The effect is mostly attributed to CTE mismatch between molding compoundand tantalum slug [1, 2] and was directly demonstrated in [3]. Tantalum chip capacitors are the only parts that require 100% reflowsimulation to reduce soldering-related failures. Per MIL-PRF-55365 reflowconditioning requires one exposure to 230 oC for 5 sec. Different lots might have different susceptibility to soldering-related failures[4] and large-size capacitors are assumed to have a higher risk of beingdamaged [5]. Mechanical stresses associated with reflow soldering can reduce breakdownvoltage and increase the probability of failures in humid environments [6]. Manual soldering might be especially detrimental: stresses caused bytouching a part with a soldering iron can cause more damage thantemperature gradients [7]. A terminal solder dip test was recommended to assess the robustness oftantalum capacitors to manual soldering [8].Deliverable to NASA Electronic Parts and Packaging (NEPP) Program to be published on nepp.nasa.gov.7
15 uF 50 V25080706050403020100-101TSpikecyclecycle 2 Tcausedcycleby1dcyclemoisture2 d20015010050001020time, mindeformation, um Direct measurements of deformation of plasticpackages during soldering simulation showed thepresence of pop-corning in tantalum capacitors.Baking before soldering was recommended toeliminate possible problems [4]. Degradation ofVBR after thermal cycling was observed in 4 outof 6 MIL and 2 out of 10 commercial lotsDeformation of Tantalum CapacitorsDuring Reflow Soldering Simulation [4]temperature, oCLiterature Data:Pop-Corning30 Pop-corning-related failures of chip tantalum capacitors were reported by R.Dobson from Raytheon [9]. The failure mechanism was attributed to silvermigration that happen in humid environments prior to soldering. Occasionally, cracks in the packages are observed on parts before soldering [10]. An unusual failure in BGA components that are adjacent to chip tantalumcapacitors was reported in [11]. The failures were attributed to moisture thatpenetrated and was trapped in capacitors. During the board assembly reflowprocess the moisture heated up, built up the pressure resulting in cracking of thecase. Moisture from the caps was out-gassing through the cracks, blowing thesolder, and causing shorts or opens between BGA balls.Deliverable to NASA Electronic Parts and Packaging (NEPP) Program to be published on nepp.nasa.gov.8
Literature Data: Effect of Preconditioning In a recent study by W. Winkel and E. Rich [12] from Raytheon, the impact thatmoisture and exposure to solder reflow have upon 35V CWR11 capacitors wasstudied. 850 capacitors were tested by different profiles varying by bake-out,humidity, and aqueous cleaning. Results of the testing showed: No failures for parts soldered after bake-out at 40ºC for 72 hours. Simulation of the uncontrolled storage profile (preconditioning at 48 hr, 30 C/91%RH)before soldering and repeat soldering after aqueous wash showed that all parts remainedwithin the specification limits. All parts had breakdown voltages exceeding VR; however, 2% of capacitors in each group had reduced breakdown voltages compared to the initialdistributions measured by SBDS. Exposure to 3 cycles of soldering also reduced VBR measured by SBDS in 5% of parts. The study indicates that the presence of moisture might increase the probability of postsoldering failures. The pop-corning can be initiated by liquid cleaning of PWBs. Warm parts mightsuck liquid in through gaps in the package. The liquid will be trapped in the caseafter cooling and cause its rupture when another side of the board is soldered.Application of a moisture barrier between anode and silver ink reducedsubstantially the probability of pop-corning failures especially in high-humiditycountries that was explained by decreasing silver migration to the dielectric [13].Deliverable to NASA Electronic Parts and Packaging (NEPP) Program to be published on nepp.nasa.gov.9
MSL: Manufacturers’ Approach According to the product catalogs, most MIL-spec tantalum capacitors haveMSL 1, which means unlimited floor life at T 30 C and RH 85%. However,there is no established procedure for testing after soldering, and it is not clearhow the level of MSL was verified. Vishay: The molded series devices meet MSL 1, are not considered moisture sensitiveand are not stored or shipped in moisture protective packaging.www.vishay.com/doc?40135 Some commercial molded case and coated devices areconsidered MSL 2a or 3 http://www.vishay.com/docs/40110/faq.pdf KEMET: all MIL parts have MSL 1. For commercial product, the necessity of moisturebags should be indicated in the ordering log/Attachments/226/KEM TC105 CWR.pdf AVX Biddeford has begun shipping all COTS , military, space level, and medical gradesurface mount tantalum capacitors in moisture resistant bags as part of an upgrade tobest practice. Biddeford product that is considered to be MSL 3 includes TBMs, TCPs,TBJ V, U and E case, and TAZ V and X case sizes. The remainder of tantalumcapacitors are rated MSL 1 (per J STD 020D). http://www.avx.com/docs/masterpubs/highreltant.pdf Per JESD22-A113 “Preconditioning of Nonhermetic Surface Mount DevicesPrior to Reliability Testing”, verification of MSL 1 requires soaking at 85 C, 85%RH for 168 hours. However, a detailed plan for the initial and post-reflowtesting should be developed for each device based on its specifics. MSL testing for tantalum capacitors is not specified.Deliverable to NASA Electronic Parts and Packaging (NEPP) Program to be published on nepp.nasa.gov.10
Part Types and Preliminary Evaluation Parts. 80 samples of CWR29 10uF 35V, LDC1307 (failed on MCE board). 80 samples of CWR09 10uF 35V, LDC1338 (reference parts from the samemanufacturer). Preconditioning. Gr.I - without preconditioning (use “as is”) for manual soldering simulation;Gr.II - without preconditioning, “as is”, for reflow soldering;Gr.III - soldered after moisture soak with Gr.IV and bake at 125 C for 15 hr;Gr.IV - soldered after moisture soak at 85 C, 85%, RH, 100hr. Both lots were soldered onto PI PWBs at the same process, wenttogether through the same preconditioning and tests. All parts passed incoming visual inspection and electricalmeasurements. Gross leak testing without pressurization was performed on 40 CWR29capacitors. One sample appeared to have a few small bubblesemitting from the corner.Deliverable to NASA Electronic Parts and Packaging (NEPP) Program to be published on nepp.nasa.gov.11
Test FlowInitial Characterization (80 pcs)serializeEM: C, DF, ESR, I-t 35V gross leak test (odd numbers only) EM: C, DF, ESR, SCT 35V, I-t 35VEffect of moisture40 pcsEffect of soldering30 pcsGr.IGr.IIMoisture soakat 85C/85%RH 100hrsunbiasedTSD 350 anode10 pcsEM after 3 hr at room conditions:EM: C, DF, ESR,C, DF, ESR, I-t 15V, I-t 35V, SCT 15V,SCT 35VI-t 15V, I-t 35V,SCT 15V, SCT 35VGr.IIITSD 350 cathodeBakeat 125C for 15hr20 pcsEM: C, DF, ESR,I-t 15V, I-t 35V,SCT 15V, SCT 35VGr.IVStorage at room conditionsEM: C, DF, ESR,I-t 15V, I-t 35V,SCT 15V, SCT 35VGSFC reflow chamberSoldering onto PWBSoldering onto PWBSoldering onto PWB20pcs20 pcs20pcsEM: C, DF, ESR;EM: C, DF, ESR,EM: C, DF, ESR,I-t 15V, I-t 35V;SCT 15V, SCT 35VI-t 15V, I-t 35V,SCT 15V, SCT 35VI-t 15V, I-t 35V,SCT 15V, SCT 35VDeliverable to NASA Electronic Parts and Packaging (NEPP) Program to be published on nepp.nasa.gov.12
Initial AC Characteristics100CWR09c u m u l a ti v e p r o b a b i l i ty , %c u m u l a ti v e p r o b a b i l i ty , 010515.E-10.500.600.70dissipation factor, %1.E-10.100.130.160.190.220.25ESR, Ohm100c u m u l a ti v e p r o b a b i l i ty , %CWR2915.E-1capacitance, uF1.E-10.40CWR090.800.90 All characteristics are well within thespecification limits (DFmax 8%,ESRmax 0.5 Ohm). DF values are 10 times less than thespecified limit. Although CWR29 suppose to be alow-ESR version of CWR09, ESRvalues in CWR09 capacitors are 50% less than in CWR29.Deliverable to NASA Electronic Parts and Packaging (NEPP) Program to be published on nepp.nasa.gov.13
Surge Current TestingReproducibility of SCTCWR29 10uF 35V Effect of SCT1.E-07DCL 1000 af ter SCT, AIsp repeat, A80706015V5035V4030687072Isp init, A741.E-081.E-091.E-091.E-081.E-07DCL 1000 init, A The set-up used resulted in surge currents at a minimal additional impedance(Reff 0.2 Ohm), which created current spikes that are within the M55365requirements, but more severe compared to the testing during manufacturing. To better simulate application conditions, the parts were first tested by 3 cyclesat 15V and then by three cycles at 35V. The set-up allowed for verifiable and reproducible test conditions. To confirm that SCT does not damage parts, leakage currents in capacitorswere measured before and after SCT.Deliverable to NASA Electronic Parts and Packaging (NEPP) Program to be published on nepp.nasa.gov.14
Initial Surge Current Testing100c u m u l a ti v e p r o b a b i l i ty , %c u m u l a ti v e p r o b a b i l i ty , %100CWRref.5010515.E-166727884current spike, A8580Isp, A501057570CWRRef .600.1250.150.1750.2ESR, Ohm901.E-13.43.63.84.04.24.4spike width, us900.1CWR15.E-11.E-16065ref.0.2250.25 All 160 parts passed SCT at 35V thatresulted in current spikes 75 A. A good correlation between Isp and ESRindicates low circuit resistance, Reff 0.29 Ω. The difference in Isp for CWR29 and thereference lots corresponds to ESR values. Difference in the pulse widths corresponds tothe characteristic time of the short circuitdischarge: t C ESR.Deliverable to NASA Electronic Parts and Packaging (NEPP) Program to be published on nepp.nasa.gov.15
Breakdown Voltages in CapacitorsDesoldered from MCE Boards Mf.A capacitors were removed from the failed engineering board (LDC1215) andboth, Mfr.A (LDC1307) and Mfr.C capacitors were removed from the flight board. Breakdown voltages for these parts as well as for LDC1307 and referencecapacitors were compared to average values for different types of 35V capacitors.Tantalum capacitors rated to 35Vvarious PNCWR29 DC1307CWR29 DC1215ReferenceMfr.C130VBR avr, Vc u m u l a ti v e p r o b a b i l i ty , %150991109070C WR 10uF 35V capacitors90Mfr.A, desoldered50Mfr.A10Mfr.C, desoldered55001020capacitance, uF3040150100150breakdown voltage, V Intrinsic breakdown voltages in 10uF capacitors from Mfr.A exceed 3 VR andare above average values typical for capacitors rated to 35V. All types of capacitors removed from the units had low-voltage tails of VBRdistributions indicating presence of large proportion of defects in the dielectric.Deliverable to NASA Electronic Parts and Packaging (NEPP) Program to be published on nepp.nasa.gov.16
Initial DCL Characteristics100c u m u l a ti v e p r o b a b i l i ty , %CWR initcurrent@35V, A1.E-061.E-071.E-08y 1.73E-06x -8.04E-01Polarization1.E-091.E 1ref .CWR5010515.E-11.E 21.E 31.E-11.E-91.E-8time, sec1.E-7DCL 1000s, ALeakage currents in 35V capacitorsCWR init1.E-061.E-06DCL 1000s, Acurrent@0V, Ay 8E-10x1.50911.E-071.E-08y 1.51E-06x -8.57E-01Depolarization1.E-091.E 11.E-071.E-08dif f erent PN1.E-09CWR29 10uFREF 10uF1.E 2time, sec1.E 31.E-1001020C, uF3040Analysis of initialcharacteristicsshowed that both lotshad tight distributionsof AC and DCcharacteristicsindicative to highquality products.No anomalies wereobserved duringsurge current testing,which rules out thepossibility ofscreening escapees. DCL was measured after 1000 sec to increase the sensitivity to defects. Majority of parts ( 80%) had leakage currents caused by absorption. All parts were well (more than 100X) within the specification, DCLmax 4 mA. Both lots had similar DCL that were below median values for 35V capacitors.Deliverable to NASA Electronic Parts and Packaging (NEPP) Program to be published on nepp.nasa.gov.17
Effect of Preconditioning and Soldering onAC Characteristics of Gr.III Capacitors0.3510.210.310.10.8DF, %109.99.8ESR, Ohm1.210.3capacitance, uFCWR DC1307CWR DC1307CWR DC13070.60.40.059.700INITHUMBAKEINITSOLDCWR09 , 8.9BAKE0.10.29HUMCWR09 DC1338CWR09 DC1338DF, %capacitance, OLD All 160 capacitors passed electrical measurements for C, DF, and ESR. No substantial variations through preconditioning and soldering (ESR raise 16%). An increase of capacitance after moisture soak (0.41% for CWR29 and 2.1% for Ref.) isconsistent with literature data [12] and indicates good coverage during MnO2 impregnation.Deliverable to NASA Electronic Parts and Packaging (NEPP) Program to be published on nepp.nasa.gov.18
Effect of Preconditioning on DCL andMoisture UptakeC WR29 DC 1307 effect of preconditioning0.3100.308mass, gc u m u l a ti v e p r o b a b i l i ty , %10050CWR0.304Ref .soak at 85C 85%RH 100hr1050.302bake at 125C 15hrInitial15.E-11.E-11.E-90.306Effect ofpreconditioningon average massof the parts (errorbars STD).0.300INIT1.E-81.E-7HUMBAKE1.E-6DCL 1000s, Ac u m u l a ti v e p r o b a b i l i ty , %100Ref. D C 1338 effect of preconditioning5010515.E-11.E-11.E-91.E-81.E-7DCL 1000s, A Moisture soak and bake did not affect DCL. Moisture uptake after soak was 0.067mg for CWR29 and0.68mg for ref. parts indicating that CWR29 capacitorswere close to saturation. Baking resulted in mass loss of 0.27mg for CWR29 and0.23mg for CWR09 (ref.) capacitors suggesting similarmoisture content in “as is” condition. Moisture uptake in humidity chamber was greater in ref.parts (0.91 mg vs. 0.33 mg for CWR29). This might1.E-6indicate a larger volume of micropores in ref. parts.Deliverable to NASA Electronic Parts and Packaging (NEPP) Program to be published on nepp.nasa.gov.19
Effect of Preconditioning on SCTCWR29Ref. capacitors8474Isp post testing, AIsp post testing, A767270hum 35Vbake 35V688280hum 35Vbake 35V666668707274767878Isp init, A80CWR2984Ref. capacitors4.13.8hum 35Vhum 35V4tau post testing, ustau sp post testing, us82Isp init, Abake 35V3.93.83.73.75bake 35V3.73.653.63.73.83.9tau sp init, us44.13.63.653.73.753.8tau sp init, us SCT was repeated after moisture soak and then after bake. All parts passed the testing and no significant effect on the amplitude and widthof the current spikes was observed. Some increase in Isp after bake for CWR29 corresponds to ESR variations.Deliverable to NASA Electronic Parts and Packaging (NEPP) Program to be published on nepp.nasa.gov.20
Reflow Soldering Temperature profile was selected to comply with manufacturer'srecommendations (AVX: max rate 2 C/sec, Tmax 225 C; KEMET: 3 C/sec,Tmax 235 C) and mimic soldering conditions for flight boards. The chamber is a 10-zone convection reflow oven (Vitronics XPM3). No N2purging was not used. Solder paste: Nordson, Sn63/Pb37, RMA-P200. After placing parts on boards with solder, they were “de-moisturized” for twohours at 93 C before reflow. No cleaning or touch-up to improve fillets after soldering was used. To simulate worst case conditions, each board passed through 3 reflow cycles. Parts were soldered in 2 days after bake and in 4 days after moisture soak. Optical examinations of soldered capacitors showed no defects.Deliverable to NASA Electronic Parts and Packaging (NEPP) Program to be published on nepp.nasa.gov.21
Effect of Reflow Soldering on ACCharacteristics10.29.89.6ESR af ter soldering, Ohm10C af ter soldering, uF0.35CWR as isCWR bakeCWR humRef . as isRef . bakeRef . hum9.49.2999.29.49.69.81010.2C bef ore soldering, uFDF af ter soldering, %CWR as isCWR bakeCWR humRef . as isRef . bakeRef . hum0.90.70.50.50.60.70.8DF bef ore soldering, %0.25CWR as isCWR bakeCWR humRef . as isRef . bakeRef . hum0.20.150.10.10.12 0.14 0.16 0.180.20.22 0.24 0.26ESR bef ore soldering, Ohm1.31.10.30.91 All post-soldering AC characteristics werewithin the specification limits. Minimal changes occur for parts afterbaking. Parts soaked in moisture had decreased C. ESR increases as a result of soldering for alltypes of preconditioning; however,degradation was greater in capacitors aftermoisture soak.Deliverable to NASA Electronic Parts and Packaging (NEPP) Program to be published on nepp.nasa.gov.22
Effect of Reflow Soldering on ACCharacteristics, Cont’d70DF deviation, %60Effect of solderingDF CWR50DF ref40characteristicas ishumbake20DC CWR29, %-0.11 (0.1)-0.07 (0.12)-0.12 (0.06)10DDF CWR29, %14.8 (4.9)23.4 (13.3)15.2 (6.17)DESR CWR29, %16.8 (7.68)28.7 (6.03)10.8 (7.17)DC ref, %0.28 (0.57)1.15 (0.17)0.26 (0.31)DDF ref, %22.9 (3.65)54.1 (8.66)22.9 (9.6)DESR ref, %18.3 (7.5)46.3 (8.2)15.7 (4.5)300as ishumbake60Effect of soldering50ESR deviation, %Changes in AC characteristics as a result ofsoldering compared to the initial valuesmeasured on loose partsESR CWR40ESR ref3020100as ishumbake No substantial changes in capacitance. Degradation of DF and ESR is greater forreference parts for all types of preconditioning. Parts after baking increase ESR on 10% to16%, but in the presence of moisture theincrease is 29% to 46%.Deliverable to NASA Electronic Parts and Packaging (NEPP) Program to be published on nepp.nasa.gov.23
Failures after Reflow Soldering After soldering the parts were tested in the sequence shown in the table. Out of 11 CWR29 parts that failed at 15V ( 1A after 50 msec),one failed the first SCT cycle, 8 after the second, and 2 after the third cycle. Allnine parts tested at 35VCWR29, DC1307CWR09 (Ref.) DC1338failed at the first cycle.Precond./ One CWR29 part inas isBake Moisture as isBake MoistureTest“as is” condition failed0/200/200/200/200/200/20AC testingafter 1 hour of DCLtesting at 35V.2/200/209/200/200/200/20SCT at 15V Some SCT failures1/180/208/110/200/201/20SCT at 35Vresulted in mechanical0/170/200/30/200/200/19DCL at 15Vdamage to the parts;1/170/200/30/200/200/19DCL at 35Vhowever, no burningwas observed.20%085%005%Total The probability of post-soldering failures depends on both factors:preconditioning and lot date code.Deliverable to NASA Electronic Parts and Packaging (NEPP) Program to be published on nepp.nasa.gov.24
SCT Failures After Reflow Soldering Board B was populated with CWR29 capacitors that were preconditioned inhumidity chamber (samples A1-A20) and reference parts (samples B1-B20). Cracks were observed on the top and at the bottom of the CWR29 capacitors. No case defects were observed after soldering. Case cracking and damage occur in 50% of CWR29 capacitors after SCT. SCT did not cause damage to CWR09 (reference) parts.Deliverable to NASA Electronic Parts and Packaging (NEPP) Program to be published on nepp.nasa.gov.25
Effect of Reflow Soldering on DCLE ffect of soldering, C WR29virgin"as is", PWB"bake", PWB"moisture soak", PWB"bake", desoldered10515.E-11.E-81.E-7E ffect of soldering, ref. capacitorsc u m u l a ti v e p r o b a b i l i ty , %501.E-11.E-9virgin"as is", PWB"bake", PWB"moisture soak", PWB"bake", desoldered1.E-8DCL 1000s, A1.E-071.E-071.E-081.E-091.E 110015.E-11.E-06SN54-10m at 15VSN46- 1hr at 35VDCL 1000s, A1051.E-06current, A501.E-11.E-9Ref. soldered after moisture soakCWR 10uF 35V soldered as iscurrent, Ac u m u l a ti v e p r o b a b i l i ty , %1001.E-71.E 21.E 31.E 41.E 5sample had excessiveDCL before soldering1.E-081.E-091.E 11.E 2time, sec1.E 31.E 41.E 5time, sec One CWR29 sample from Gr.II (“as is”) failedafter 10 min at 15V and another after 1 hr at 35V. No difference in distributions of leakage currentfor not-failed capacitors with differentpreconditioning. Non-failed CWR29 samples from the group thatwas soaked in moisture before soldering had lowleakage currents. Desoldering of baked capacitors did not changeDCL distributions.Deliverable to NASA Electronic Parts and Packaging (NEPP) Program to be published on nepp.nasa.gov.26
Effect of Reflow Soldering on SCTCWR29 DC13077570656055666870727480Isp post testing, ACorrelation betweencurrent spikeamplitudes measuredinitially, after differentpreconditioning, andafter solderinghum 35Vbake 35Vsold 35V80Isp post testing, ARef. capacitors8585757065hum 35Vbake 35V60sold 35V557678Isp init, A8084Ref. capacitorsCWR29 DC13075.55.5Similar correlation forcurrent spike width5hum 35V4.5bake 35Vsold 35V4tau post testing, ustau sp post testing, us82Isp init, A5hum 35V4.5bake 35Vsold 35V43.53.53.73.83.9tau sp init, us44.13.63.653.73.753.8tau sp init, us SCT of soldered samples resulted in current spikes of a lesser amplitude(decrease 10%) and greater width (increase 30%). The result are due to increased ESR, and to using 4” wires to interconnectthe parts with the set-up that increased inductance of the circuit.Deliverable to NASA Electronic Parts and Packaging (NEPP) Program to be published on nepp.nasa.gov.27
Ten samples from each lot in “as is” condition were stressed by 3 cycles of TSDtesting at a solder temperature of 350 C, first at anode, and then at cathode sides. Post-TSD measurements were carried out in the sequence shown in the table. 60% of CWR29 capacitors failedTSD350TSD350the anode-side testing, whereasanode sidecathode sideTestno reference parts failed.CWR29, CWR09 Ref., CWR29, CWR09 Ref., One CWR29 part had aDC1307DC1338DC1307DC1338substantial increase of DF.0*/100/100/50/8AC testing Two CWR29 parts recovered at DCL at 15V 6/100/101/50/8higher voltages and passed SCT, DCL at 35V2/50/101/50/8but one failed DCL again after0/50/9**0/50/9SCT at 15Vcathode-side testing.0/50/8**0/50/9SCT at 35V No failures happened after* DF 4.4%; ** two samples were not tested by mistakecathode side solder dip. Most failures happened at low voltages after anode-side thermal stress. Self-healed capacitors have a high risk of repeat failures. Parts with parametric DCL failures can pass surge current testing. Results are in agreement with the solder reflow test: soldering-related stressesaffected CWR29 capacitors to a much greater degree than the reference parts.Deliverable to NASA Electronic Parts and Packaging (NEPP) Program to be published on nepp.nasa.gov.28
Effect of TSD350 on AC and DCCharacteristicsEffect of TSD 350Effect of TSD 3500.25ESR TSD350 anode, OhmC TSD350 anode, uF10.510CWR anode9.5ref . anodeCWR cathoderef . cathode999.51010.50.2CWR anoderef . anodeCWR cathoderef . cathode0.150.10.10.15C init, uFPost anode-TSD3501.E-04CWR anoderef . anodeCWR cathoderef . cathode4.5%1.E-05current, ADF TSD350 anode, SR init, OhmEffect of TSD 3500.90.20.60.7DF init, %0.81.E-101V3V15V35V All AC characteristics werewithin the specification. One CWR29 part increasedDF almost an order ofmagnitude (this part had alsolarge DCL at 1V). Anode-side TSD practicallydid not change ESR;whereas ESR increased on11% in CWR and 18% in ref.capacitors (similar to theeffect of reflow soldering). Two CWR29 parts failingDCL at 3V recovered at 15V,but then failed again at 35V. No degradation of DCL forthe reference capacitors.Deliverable to NASA Electronic Parts and Packaging (NEPP) Program to be published on nepp.nasa.gov.29
Effect of Soldering on Breakdown Voltages VBR for “moisture soak” and “as is” capacitors was measured with parts soldered onto PWB. “Bake, desoldered” parts were desoldered from the PI PWB, manually soldered onto FR4 PWB, and then desoldered again. Initial SCT failures were also used for calculations of VBR distributions.C WR 10uF 35V DC 1307c u m u l a ti v e p r o b a b i l i ty , %99"moisture soak", PWB9050"as is", PWBvirgin105"bake", desoldered from PWB150100150breakdown voltage, Vc u m u l a ti v e p r o b a b i l i ty , %99Reference 10uF 35V capacitors9050"mloisture soak", PWB105"as is", PWBvirgin"bake", desoldered from PWB150100breakdown voltage, V150Results ofVBR testsSCT shortcircuitSCT selfhealed“as is”Moist.“as 11(55%)8(44.4%)Sample size1632018Median VBR, V112.7113.3116.5115.2CWR29CWR09 (Ref.) Most non-failed parts had intrinsic VBRs. Tails of the distributions indicate defects in Ta2O5. There is a trend of increasing the number ofdefects after soldering capacitors with greatermoisture content. Desoldering can cause damage to dielectric. 95% of CWR95 parts failed short circuit, whereas 50% of the reference parts self-healed afterscintillation breakdown.Deliverable to NASA Electronic Parts and Packaging (NEPP) Program to be published on nepp.nasa.gov.30
IR Images of Capacitors Failed after ReflowSolderingCWR-25CWR29 capacitors soldered after moisture soakSN62 failed SCT, 1.5Ω;SN68 failed SCT, 0.7Ω;SN72 failed SCT, 1.3Ω
Literature Data: Effect of Soldering It is well known that molded case tantalum capacitors can be damaged during soldering and related to damaging first power-on failures are one of the major reasons for voltage derating [1]. The effect is mostly attributed to CTE mismatch between molding compound