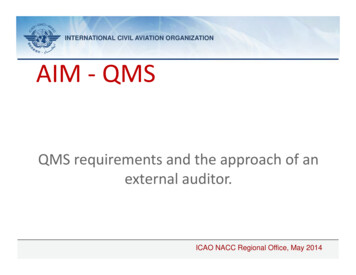
Transcription
INTERNATIONAL CIVIL AVIATION ORGANIZATIONAIM ‐ QMSQMS requirements and the approach of anexternal auditor.ICAO NACC Regional Office, May 20141
HOW to IMPLEMENT a QMS?1. Planning & DesigningFourPhases2. Describing3. Implementing the QMS4. Improving the QMS2
THE FIRST HOWHATQUALITYPOLICYQUALILTYPRINCIPLESISO 9001FOUNDATION3
A POSSIBLE APPROACH8. Refine2. VEMENT1. SetPolicy3. Plan4. Define(SMM)6. Implement7. Controland survey4
Planning and Designing Phase:ActivitiesQuickScanActionPlanSeries ofMeetings5
INITIAL SURVEYStart by reviewing the current situation What elements of a QMS are already in place? Organisation charts Process documents Forms and records Job descriptions6
IDENTIFY MISSING ELEMENTS Identify the items required that are not inplace, these may be for example: some process documents some necessary records an internal quality audit process a formal management review process a continual improvement process In effect you are performing a “Gapanalysis”7
IMPLEMENTATION PLANS In order to ensure a successful implementation it must beplanned, e.g. as a project: Resources must be identified Activities planned and assigned Time scales agreed and documented Responsibilities allocated Progress must be regularly monitored8
ACTIVITYMJJ2014A SONDJF2015M A MJJInitial ISO 9001BriefingAssessment ofcurrent systemsFormulate ActionPlansTypicalISO9001ActionPlanAppoint Project/Quality CoordinatorISO 9001 trainingfor coordinatorWrite procedures/implement systemsInternal QualityAuditor trainingManagement reviewof ISO 9001 systemsContact ISO 9001Assessment BodiesQuality AwarenessTraining (all staff)Implement systems/Internal AuditsFormal ISO 9001Assessment9
Describing Phase: dDescriptionDesign ofNewProcesses10
QMS FRAMEWORKThe framework of the Quality ManagementSystem starts with Top Management: they set the business objectives they must then establish an organisation to put those policies intoaction they must ensure that key processes are controlled they must identify responsibilities and interfaces they must ensure that resources are provided11
SYSTEM DOCUMENTATION The framework of the system documentation willdepend upon the business structure, e.g. The size and complexity of the organisation Is there a department or team‐based structure? A typical documentation structure is shown on thenext slide.12
TYPICAL QMS STRUCTURESTANDARD ‐ ISO 9001 (Annex 15)Policy, objectives, organisation,outline of quality systemQUALITY cesPROCESS DOCUMENTSAND PROCEDURESDetailed instructionson how to carry outspecific tasksINSTRUCTIONSQualityrecordsFORMSDesignIT SupportInstallationTraining13
DOCUMENT FORMATISO 9001:“The documentation may be in any form or type ofmedium” Therefore it could be in text form or in the form ofprocess maps/flowcharts It could be a paper‐based system or could be oncomputer, e.g. accessed via an intranet browser14
CHOOSING a FORMAT Each organisation can choose its own format The majority at present have paper‐based textdocuments Increasingly organisations are using flowcharts and“computerised” systems– a computer based solution often has advantages when itcomes to document and change control15
Implementation Phase: ActivitiesPuttingplanninginto ActionCommunicationTrainingInternalAuditPlan16
PRODUCING the QMS DocumentationTHE QUALITY MANUAL Description of the organisation Quality Policy, key objectives Structure of the organisation Interfaces, responsibilities Overview of the Quality System show approach to Standard requirements detail and justify any exclusions17
PRODUCING the QMS DocumentationPROCESS Documents Do we need process documents? The ISO 9001 standard calls for few mandatoryprocedures The question is do we need documents in orderto effectively control our business processes?18
PRODUCING the QMS DocumentationBenefits of process documents Provide consistency/repeatability Define responsibility/authority Continuity when staff change Assist in staff training Help identify cause of errors Benchmark for improvement19
PROCESSDefinition:Set of inter‐related or interacting activities whichtransforms inputs into outputsISO 900020
ConstraintsPROCESSINPUTPROCESSOUTPUTResources21
PROCEDUREDefinition:Specified way to carry out an activity or processISO 9000i.e. describes how a process is performed22
PROCEDURE DEVELOPMENT Establish current practice Document current practice Review current practice Prepare procedure Review and approve Issue procedure23
PRODUCING PROCEDURES Establish standard format/template Indicate approval/revision status Consider using flow charts or process maps Train the procedure writers24
FLOWCHARTUsing a flowchart is a very effective way to describe a process“a picture is worth a thousand words”SYMBOLS25
FLOWCHART SYMBOLSAny process can be represented in the formof a simple flow chart using just two symbols:Activity or processDecision26
FLOWCHART RULESThere is one route into the boxand only one route out for theprocess activity boxesThere is one route in and twopossible routes out for the decisionboxes(e.g. yes/no or pass/fail)PROCESSDecisionNoYes27
ANUALYesIS ITCORRECT?NoMAKECORRECTIONSEND28
Improvement Phase: Audit29
INTERNATIONAL CIVIL AVIATION ORGANIZATIONQualitySystems AuditsProduce a process flow‐chart basedupon the information provided.30
AUDIT OBJECTIVES(1) To ensure that procedures are being followedie. We are doing what we say we do(2) To determine the effectiveness of the systemsand procedures in meeting the qualityobjectives(3) To afford an opportunity to improve the qualitysystem31
AUDITING STANDARDSISO 10011 Guidelines for auditing quality systemsPart 1 : AuditingPart 2 : Qualification criteria for qualitysystems auditorsPart 3 : Management of audit programmes32
AUDITWHAT DOES THE ABOVE STANDARD SAY ABOUTQUALITY SYSTEMS AUDITING? Verify compliance, effectiveness Planned audit programme Independent auditors Documented procedure Timely corrective action Follow‐up activities33
AUDIT PROGRAMME Audits planned in advance Audits are not random spot checks Scheduled usually by department,function, or process Consider the status and importance ofprocess, and previous results34
AUDIT RVE35
AUDIT REPORTSummary of results, including : Scope, dates, auditors Satisfactory areas Nonconformities Observations, recommendations36
FOLLOW‐UP Auditee responsible forcorrective preventive actions Auditor follows‐up action toensure it is taken and effective Audit actions are closed ‐ records37
SUMMARY OF AUDIT PROCESS PLANNINGSchedule,Preparation,Checklist AUDITINGOpening Meeting,Audit, ClosingMeeting COMPLETIONReport, Correctiveaction, Follow‐up
BENEFITS OF AUDITING Verifies that procedures are followed Reviews effectiveness of system Helps to identify problem areas Assists transfer of best practice Effective mechanism for continuousimprovement39
Preparing for CertificationISO 9001‐ Steps in Implementation Management decision/commitment Decide scope of system Review current situation ‐ report gaps Formulate action plan Document & implement processes Formal assessment40
KEY QUESTIONSBefore inviting an external assessmentcheck the following: Are the mandatory documents in place ‐ qualitymanual and procedures? Are key processes identified and controlled? Have internal audits and management reviewsbeen conducted? Are results from these satisfactory?41
FINAL PREPARATION Consider a pre‐assessment– internal– independent consultant– your assessment body Inform all of your staff– explain the process– clarify their responsibilities– seek their feedback regarding any concerns42
The CertificationProcessNational Government(e.g. UK DTI)Regulating Authority(e.g. UKAS, DAR)Regulation ofthe ISO 9001CertificationProcessCertification BodiesCompanies/Organisations43
INTERNATIONAL CIVIL AVIATION ORGANIZATIONSUMMARY44
QUALITY MANAGEMENT PRINCIPLES Customer focused organizationLeadershipInvolvement of peopleProcess approachSystem approach to managementFactual approach to decision makingMutually beneficial supplier relationshipsContinual improvement45
Key Principles of ISO 90001 GET ORGANISED‐ define roles, responsibilities, interfaces2 PROVIDE RESOURCES‐ human resources, training, facilities3 DOCUMENT MANAGEMENT SYSTEMS‐ establish procedures, control documents4 CONTROL PROCESSES‐ plan processes, control operations5 KEEP RECORDS OF ACTIVITIES‐ evidence of effective operation6 CARRY OUT REGULAR CHECKS‐ inspections, tests, surveys, audits7 IMPROVE THE SYSTEMS‐ pro‐active continual improvement process46
MAIN ASUMPTION !!!If the ISO 9001:2008 implementationproject is to be successful, then there MUSTbe support and commitment from TopManagement.47
THANK YOU !Raul MartinezICAO NACCAIM Regional Officerrmartinez@icao.int48
ISO 9001 training for coordinator Write procedures/ implement systems Internal Quality Auditor training Management review of ISO 9001 systems Contact ISO 9001 Assessment Bodies Quality Awareness Training (all staff) Implement systems/ Internal Audits Formal ISO 9001 Assessment Typical ISO 9001 Action Plan. 10 Detailed Description Design of New Processes Process Improvement