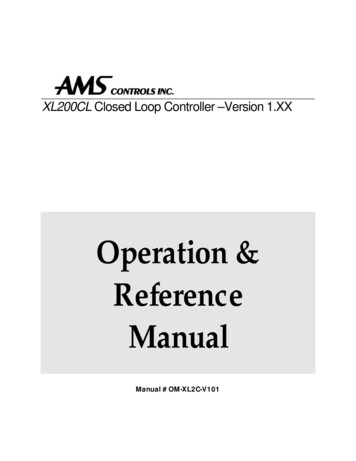
Transcription
XL200CL Closed Loop Controller –Version 1.XXOperation &ReferenceManualManual # OM-XL2C-V101
XL200 Closed Loop Version 1 ControllerOperation & Reference Manual AMS Controls, Inc.12180 Prichard Farm RoadMaryland Heights, MO 63043Phone 314.344.3144 Fax 314.344.9996!! WARNING !!AMS CONTROLS, INC. reserves the right to change the contents of this manual withoutcustomer notice or permission. Although every effort is made to insure the correctnessoff this manual, It should be noted that AMS CONTROLS, INC. is not responsible forpersonal or equipment damage caused by the contents of this manual. It is not the intentof this manual to cover every possible revision or version of controller. For specificcontroller questions contact AMS Controls, Inc.!! Important Version Information !!This manual is an interim manual to be used with the XL200, Version 1 controller only.Some instructions and diagrams may refer to interface techniques as used by the XL200series controller. The manual applies only to Version 1 XL200 controllers.XL200 Series – VERSION 1iiIntroduction
vityxviEasy to UsexviiEasy to InstallxviiAbout this ManualxviiSystem DescriptionThe Closed Loop Control Sys temxviiixviiiXL200 VERSION 1 Hardware DescriptionXL200 SERIES Controller Hardware DescriptionMicrocomputerController Keys and FunctionsF1 – Set to NextF2 – Skip/ReadyF3 – Add LineF4 - DeleteF5 - PrintF6- Decrement QuantityHot KeysHelpDiagnosticsIncrease QuantityProduction DataStatusSetupProgramEnterNavigation KeysArrow Keys , , , Move Up, Move DownPage Up, Page DownHomeNumeric Entry KeysXL200 Series – VERSION troduction
INSEndCE KeyDecimal Point, Dash (-)Number Keys, 0-9Display xivxxvxxviSpecial FeaturesDie Test ModeDie Jog ModeMaterial Change PointPunch PressesBuilt- in Programmable Logic ControllerxxviixxviixxviixxviiixxviiixxixFlexible Punching Options (XL200, XL202, XL206. And XL 212 Only)xxxINSTALLATION1-2Controller Power1-2Emergency Stop Circuit1-2Run Circuit1-4Shear Control Circuit1-6Press Control Circuit1-8Initial Machine TestsManual ShearManual PressJogging1-91-91-91-9MACHINE CONFIGURATION2-1Setup2-1Machine DataGeneral ParametersHalt ModeFormatBundle Qty Reload ValueBundle Qty CountSet Done Items to Ready?2-22-32-32-42-42-42-4XL200 Series – VERSION 1ivIntroduction
Auto-Delete Done OrdersHalt No More Item? (With Punch Only)Use Order Numbers?Halt Delay Minimum (With XL Link Only)Minimum Footage to Request Order (With XL-Link Only)Manual Shear Scrap Length (With XL-Link Only)Shear Dwell DownShear Dwell UpAuxiliary Shear CompensationShear KerfShear ReactionMinimum PartDelay After ShearItem Complete Dwell (XL200CL Only)Shear- Encoder DistanceCoil End PointCoil End OffsetShort Part Length (“U” option only)Short Part Delay (“U” option only)Very Short Part Length (“U” option only)Very Short Part Delay (“U” option only)Mode SelectNo Hole StopShear-DetectMin Hole SpacingHole-Detect LogicLine Movement Select (Single speed, non-stopping lines only)Scrap Length (All Models Except XL200CL Without a Punch)Loop GainJog Select Mode? (Non-Stopping only)Jog VelocityMinimum Die Return Velocity (Non-Stopping only)Maximum Die Return VelocitySlow Run VelocityAccelerationReturn AccelMinimum Die DistanceMaximum Die DistManual Shear Die DistanceEnable Alternate Die ParametersThe setup lockout key locks out all parameters.Die Home OffsetAdvance After CutRetract After CutOn Tolerance Error?ToleranceXL200 Series – VERSION -152-152-152-17Introduction
Offset Volts (Auto)Offset IntegralLag Compensation (Auto)Lag IntegralDerivativeEncoder DirectionLine ResolutionDie ResolutionMotor ResolutionCorrection FeatureFilter ConstantTool Select (XL202CL, XL206CL, XL212CL Only)Press Dwell (When There Is More Than One 2-202-20Initial Machine TestsDirections and PolarityManual ShearManual PressEncoder Operation on Feed SystemsSingle EncoderTwo EncoderSlip Test on Feed-to-Stop Machines with 2 Encoders2-212-212-212-222-222-222-222-23Testing Without MaterialFeed-To-Stop ModeDie Accelerator Mode2-242-242-24Test Phase of AnalogCalibration2-312-32Calibrate Trim2-33Time Clock2-34Input/Output StatusE-Stop InputFeed-OK Input (Feed-To-Stop only)Setup Lockout InputEnable Output2-352-352-352-362-36Memory TestClearing Memory While Energizing Controller2-372-37CommunicationsCommunications SetupScrap CodeProduct CodeDelay Reason2-382-392-392-402-40XL200 Series – VERSION 1viIntroduction
Employee NumbersCommunications Test2-402-41Request Order2-42EDIT TOOL DATA3-1The AMS Model XL200CL SERIES ControllerGlossary of Terms3-13-2Machine ConfigurationProgramming Press ParametersDetermining the Machine Zero Reference PointProgramming Tool Parameters3-33-33-33-5Nested Tooling3-7PART PROGRAMMING4-1Pattern ProgrammingLEADING EDGETRAILING EDGELEAD CENTERTRAIL CENTEREVEN SPACESPACING LIMIT4-14-44-44-44-44-44-4Order ProgrammingLift NumberQuantityLengthPattern NumberOptionR-(RIGHT)L-(LEFT)A-(ALTERNATE 4-8Application Example 1Single Press with Multiple GagsDie LayoutTool Data ScreenPattern 100 ScreenPattern 200 ScreenSpecial Pattern Notes:XL200 Series – VERSION 14-94-94-104-114-114-124-12viiIntroduction
OPERATING PROCEDURE5-2Programming Overview5-2Entering OrdersOrder NumberMaterial CodeProduct CodeLift (Bundle) NumberQuantityLengthPunch PatternStandard Macro ProgrammingEdit Tool DataProgramming Macro PatternsMacro PatternsInserting Macros Into Other ting the Program Mode5-14Referencing Controller to the Material5-15Running the MachineMain Status DisplayStatus Mode DisplaySetting the Next Order (Item) to RunSkipping an Order or an ItemAdding an Item While in the Run ModeDeleting an Order (Item)Changing the Sequence of Orders (Items)Starting the MachineManual ShearHalting ProductionCompleted Orders (Items)Requesting Order (When using Eclipse -215-21Footage TotalizerCoil InventoryDisplay Coil FootageDisplay Coil MaterialChanging Product CodeShift Totals and Job Totals5-235-235-235-245-245-25Special ProceduresScrap CodeDelay ReasonEmployee Numbers5-275-275-275-27XL200 Series – VERSION 1viiiIntroduction
Changing CoilsWhen No Good Footage is Run for a CoilNo Sheet Detect When a New Coil is EnteredHandling Material FlawsIncrease QuantityDecrease Troubleshooting GuideWhen did the Problem Start?Check the MachineCollect DataRe-check SetupsRun the Calibration modeUse Built- in Diagnostic featuresCheck Incoming PowerCycle PowerElectrical NoiseClear MemoryContact AMSFAX Setup and Parts data to -1Outputs to the PrinterPrint Initiate OutputPrinter EncoderCitoh T4 PrinterTelesis 3225 PrinterMatthews 2001 PrinterFox 8231M PrinterWillett 3150 PrinterTest Print on Part7-37-37-37-77-87-107-137-167-17Bundle Tag PrinterCitoh T4 PrinterCITOH SETUP MODESZebra Z4000 Printer7-187-187-237-25EXPANSION BOARDEXP HardwareExpansion Board Characteristics7-317-317-31Bar Code Scanner7-33XL200 Series – VERSION 1ixIntroduction
Extended Macro PatternsProgramming PatternsEdit Tool DataMacro PatternsInserting Macros Patterns Into Standard PatternsA Programming Example Using Macro Patterns7-367-367-367-367-377-37Auxiliary Controller7-41InstallationMechanical InstallationElectrical InstallationController PowerMachine StateEmergency Stop CircuitShear Control CircuitDrive Control CircuitRun Mode Control Circuit7-427-427-427-427-447-447-457-467-46Setting the Customizing Switches7-46Initial Power Test7-47Configuration ProgrammingGeneral ParametersPress (SHEAR) Dwell DownPress Dwell UpPress Reaction TimeRefresh Done Job (SL350HCLR ONLY!)Batching (SL350HCLR ONLY!)Mode (SL350HCLR ONLY!)Press-Detect (Shear-Detect on SL350HCLR)Minimum Hole SpacingNo-Hole StopMinimum Part (SL350HCLR ONLY!)Loop GainJog Die VelocityMax Die VelocityAccelerationReturn AccelMin Die DistMax Die DistAdvance After CutOn Tolerance ErrorToleranceOffset AutoOffset 7-52XL200 Series – VERSION 1xIntroduction
Lag AutoLag IntegralDerivativeLine ResolutionCircumference (SL350HCLR ONLY!)Rotary Count (SL350HCLR ONLY!)Rotary Start (SL350HCLR ONLY!)Rotary Stop (SL350HCLR ONLY!)Die ResolutionCorrection FactorFilter ConstantUnitsJog SelectMinimum VelocityShear Dead BandPrint On Coil ChangesManual Shear Die DistanceHole DetectLine movementEditing the Auxiliary Controller ParametersAuxiliary SetupAuxiliary ProgramQuantityHole CountLength From HoleAuxiliary StatusSearch For All -607-607-617-62Initial Machine TestsManual ShearJoggingReferencing Controller to the MaterialDie Accelerator Test7-637-637-637-637-63Running the MachineTolerance Error DisplayClear Holes7-657-657-65SL 301 H7-66Switch Settings and I/O 7-75SL 301 HCLRSwitch Settings and I/O 7-767-66SL 301 HCLSwitch Settings and I/O 7-777-66SL 301 HCLSSwitch Settings and I/O 7-787-66SL 301 H Plus Switch Settings and I/OXL200 Series – VERSION 17-67xiIntroduction
SL 301 HCLR Switch Settings and I/O7-68SL 301 HCL Switch Settings and I/O7-69SL 301 HCLS Switch Settings and I/O7-70Hole Detect OptionHole Option ParametersModeShear DetectMinimum Hole SpacingNo Hole Stop DistanceHole Detect LogicProgrammingProgramming in Hole 727-747-747-747-74MODEL TYPES8-1Model CustomizationController Model TypesClosed Loop Switch SettingsXL200CL CustomizationXL200HCL CustomizationXL202CLF, XL206CLF, XL212CLF CustomizationsModels: XL202CL, XL206CL, XL212CLEncoder 1 and Encoder 2 are used as follows:Closed Loop Inputs and OutputsNotes:Machine Parameter SheetPress Dwell SheetPress Dwell SheetTool Data SheetPatterns 0SPECIFICATION9-1Mechanical9-1Electrical9-1Input Characteristics9-1Output Characteristics9-1XL200 Series – VERSION 1xiiIntroduction
Encoder ter Requirements9-29-29-2Printer SpecsBundle Tag PrinterLabelPrint HeadLabel CapacityRibbonResolutionBar CodesInkjet Print on Part PrinterPower RequirementsOutputAmbient 49-49-4Bar Code ScannerPower RequirementsScan Repetition RateStart- up TimeData Acquisition TimeSkew TolerancePitch AngleDecode CapabilityElement WidthPrint ContrastAmbient Light ImmunityDurabilityOperating bout Wiring DiagramsXL Series Wiring DiagramsSL (Auxiliary) Series Wiring Diagrams10-110-110-1XL200 Series – VERSION 1xiiiIntroduction
Expansion Board DiagramsPrinter Diagrams4390-1 Encoder Expander/Driver4390-2 Printer Encoder Driver10-110-110-2510-26SOFTWARE CHANGESFaster ProcessingNew 10.5-inch color display“Downloadable” software upgradesStandardized and Expanded Input and OutputsIsolated (Floating) interfaceFunction key inputsVersion 1.00 to 1.01Version 1.01 to L200 Series – VERSION 1xivIntroduction
IntroductionAMS Controls Inc. has years of experience with controls for roll formers.Much of this is with multiple press machines that punch and notch prior tocutoff. The XL200 VERSION 1 SERIES is the ultimate controller for rollforming and cut-to-length machines. Unlike general-purpose controllers, AMScontrollers are designed specifically for the needs of the roll forming industry.With an AMS controller installed on the roll forming line, many customersreport a 20-30% increase in productivity due to the elimination of costlydelays. Production can also be monitored with a PC from the office. TheModel XL200 VERSION 1 SERIES controller is the latest and best of a longline of controllers.With the XL200 VERSION 1 SERIES, parts are produced with a minimumamount of scrap. The powerful microprocessor can sequence from one sizeto another without waste. This unique feature makes in line punchingpractical for JIT (just in time) production systems.Of equal importance to roll forming, is the ease of interfacing with the programand control system. Many machines are not used to their full potentialbecause the controls are too complicated for the average production workerto understand. This is not the case with the AMS controller. AMS strives tomake programming as simple as possible without loss of capability.With the controller design, AMS incorporated the following objectives:Ø Describe a part in finished part dimensions.Ø Prompt for data with plain English prompts using standardindustry terminology.Ø Allow user flexibility to use the same controller on severalmachine configurations.Ø Minimize the amount of data that must be entered.Note: This manual applies to Version 1 Controllers (XL200 Series)XL200 Series – VERSION 1xvIntroduction
AccuracyOn cut-to-length machines without servo drives, accuracy depends onthe repeatability of the machine to run at a constant speed and therepeatable reaction delays for each type of operation, punch and shear.If an electronic length controller is used, accuracy is lost when machinefluctuations occur.The XL200 VERSION 1 SERIES Controller however, constantlymonitors the performance of the machine and compensates for thesevariations resulting in improved accuracy. For flying cutoff machines, theexclusive Speed Compensation feature allows accurate punches andcuts at any line speed. For feed-to-stop machines, the automat
TROUBLESHOOTING 6-1 Troubleshooting Guide 6-2 When did the Problem Start? 6-2 Check the Machine 6-2 Collect Data 6-3 Re-check Setups 6-3 Run the Calibration mode 6-3 Use Built-in Diagnostic features 6-3 Check Incoming Power 6-3 Cycle Power 6-4 Electrical Noise 6-4 Clear Memory 6-5 Contact AMS 6-6 FAX Setup and Parts data to AMS 6-6 OPTIONS 7-1 Outputs to the Printer 7-3 Print Initiate