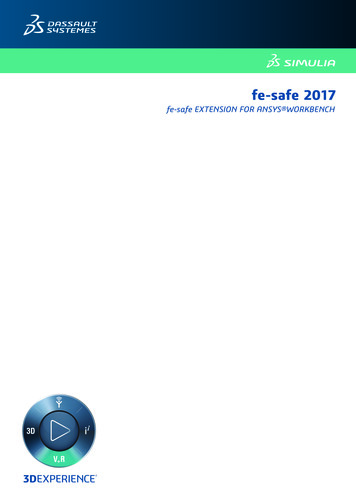
Transcription
fe-safe 2017fe-safe EXTENSION FOR ANSYS WORKBENCH
ContentsFE-SAFE EXTENSION FOR ANSYS WORKBENCH .11INTRODUCTION TO THE FE-SAFE EXTENSION FOR ANSYS WORKBENCH.31.1 ABOUT FE-SAFE. 31.2 ABOUT ANSYS WORKBENCH . 31.3 ABOUT THE FE-SAFE EXTENSION . 31.4 HOW TO USE THIS MANUAL . 42USING THE FE-SAFE EXTENSION FOR ANSYS WORKBENCH .52.1 INSTALLATION INSTRUCTIONS . 52.2 UNDERSTANDING THE EXTENSION . 72.3 HOW TO USE THE FE-SAFE EXTENSION . 932.3.1Specify the model . 92.3.2Configure the project . 102.3.3Parameterisation . 132.3.4File Management . 142.3.5Resetting the cell . 152.3.6Limitations . 15INTERFACE REFERENCE. 173.1 FE-SAFE CLIENT APPLICATION GUI VS COMPONENT GUI . 173.2 FE-SAFE MODEL READING PROPERTIES . 173.3 FE-SAFE PROJECT SETUP PROPERTIES . 1843.3.1Material Properties . 183.3.2Fatigue Analysis Scope . 203.3.3Loading Block . 213.3.4Surface Properties . 223.3.5FOS Properties . 23PREPARING FE MODELS FOR USE WITH THE EXTENSION . 254.1 SUPPORTED ANSYS FILE FORMATS . 254.2 MODEL CONSIDERATION . 254.3 UNITS . 254.4 GENERAL ADVICE . 254.5 TROUBLESHOOTING . 255TUTORIAL: STANDARD FATIGUE ANALYSIS . 275.1 INTRODUCTION . 275.2 SETTING UP THE ANALYSIS IN WORKBENCH . 28
Trademarksfe-safe, Abaqus, Isight, Tosca, the 3DS logo, and SIMULIA are commercial trademarks or registeredtrademarks of Dassault Systèmes or its subsidiaries in the United States and/or other countries. Use of anyDassault Systèmes or its subsidiaries trademarks is subject to their express written approval.Othercompany, product, and service names may be trademarks or service marks of their respective owners.Legal Noticesfe-safe and this documentation may be used or reproduced only in accordance with the terms of the softwarelicense agreement signed by the customer, or, absent such an agreement, the then current software licenseagreement to which the documentation relates.This documentation and the software described in this documentation are subject to change without priornotice.Dassault Systèmes and its subsidiaries shall not be responsible for the consequences of any errors oromissions that may appear in this documentation. Dassault Systèmes Simulia Corp, 2016.
Third-Party Copyright NoticesCertain portions of fe-safe contain elements subject to copyright owned by the entities listed below. Battelle Endurica LLC Amec Foster Wheeler Nuclear UK Limitedfe-safe Licensed Programs may include open source software components. Source code for thesecomponents is available if required by the license.The open source software components are grouped under the applicable licensing terms. Where required,links to common license terms are included below.IP Asset NameIPAssetCopyright NoticeVersionUnder BSD 2-ClauseUnZip(from2.4Info-ZIP)Copyright (c) 1990-2009 Info-ZIP. All rightsreserved.Under BSD 3-ClauseQt Solutions2.6Copyright (c) 2014 Digia Plc and/or itssubsidiary(-ies)All rights reserved.
1Introduction to the fe-safe extension for ANSYS Workbench1.1About fe-safefe-safe is a powerful, comprehensive and easy-to-use suite of fatigue analysis software for Finite Elementmodels. It is used alongside commercial FEA software to calculate: where fatigue cracks will occur; when fatigue cracks will initiate; the factors of safety on working stresses (for rapid optimisation); the probability of survival at different service lives (the ‘warranty claim’ curve).Results are presented as contour plots which can be plotted using standard FE viewers.fe-safe has direct interfaces to the leading FEA suites.1.2About ANSYS WorkbenchANSYS Workbench provides powerful methods for interacting with the ANSYS family of solvers. Thisenvironment provides a unique integration with CAD systems, and the user’s design process.ANSYS Workbench Applications are a development framework upon which ANSYS applications are built.Applications are available in the areas of structural mechanics, geometry, CFD, rigid dynamics,electromagnetics, optimization and more.1.3About the fe-safe extensionThe fe-safe extension for ANSYS Workbench is an added capability which allows for fe-safe to be insertedinto an existing project schematic in Workbench with fatigue analyses being configured and conducted fromwithin Workbench.The fe-safe extension has been completely redesigned for the fe-safe 2016 release. It is only compatible withANSYS versions 15 and 16, and incompatible with versions of fe-safe prior to fe-safe 2016.Users of the fe-safe extension for ANSYS Workbench are assumed to have a working knowledge of fe-safe,including such techniques as configuring a fatigue analysis and setting properties for different parts of themodel, defining the fatigue loading, running an analysis and exporting fatigue results. The use and applicationof fe-safe is described in the fe-safe user guide, which should be referred to alongside ANSYS WorkbenchHelp from ANSYS.Features of the fe-safe extension for ANSYS Workbench include: Support for Finite Element solutions from ANSYS RST files Simplify the configuration of the project for basic workflows For more complex fatigue analysis configurations, the fe-safe component mode can still be accessed Verity in fe-safe can be used with automatic weld detection or legacy weld definition filesCopyright 2016 Dassault Systemes Simulia Corp.Issue: 4.0 Date: 31/08/2016fe-safe extension for ANSYS Workbench3
1.4Methods for post-processing fe-safe results files in the ANSYS Mechanical applicationHow to Use This ManualChapter 2 provides installation instructions and an overview of the actions required in order to perform an fe-safe analysis as part of a project schematic in ANSYS Workbench. It also contains details on installing the fesafe extension and briefly explains how the extension works. Chapter 0 (Interface Reference) offers furtherdetails of the available options. The prerequisites for ANSYS Workbench schematics are explained in Chapter4 (Preparing FE Models for use with the extension). Worked examples of the process are provided in atutorial.Users new to fe-safeBecause this manual assumes some familiarity with fe-safe, it will be necessary to learn a little about the mainprogram first. Work through some of the tutorials in the fe-safe user guide, including at least onedemonstrating the use of data from ANSYS, then return here.fe-safe users new to ANSYS WorkbenchSome understanding of the ANSYS Workbench environment and ANSYS Mechanical application is requiredto make the best use of the software. The ANSYS Customer Portal available from www.ansys.com provideslearning material for those unfamiliar with the software.Experienced users of ANSYS Workbench new to the fe-safe extension for ANSYS WorkbenchRead Chapter 4, Chapter 2, then work through the tutorial to familiarise yourself with the fe-safe extension forANSYS Workbench. Once you have done this, follow the procedure described in Chapter 2 with your owndata, referring to Chapter 0 as necessary.4fe-safe extension for ANSYS WorkbenchCopyright 2016 Dassault Systemes Simulia Corp.Issue: 4.0 Date: 31/08/2016
2Using the fe-safe extension for ANSYS Workbench2.1Installation InstructionsFor convenience, the following path contractions are used in the instructions:ShorthandTypical Location fe-safe-installation-dir C:/SIMULIA/fe-safe /2016 fe-safe-data-dir C:/SIMULIA/fe-safe /2016/data ANSYS-installation-dir C:/Program Files/ANSYS Inc/v150 (ANSYS 15.0 64-bit)C:/Program Files/ANSYS Inc/v160 (ANSYS 16.0 64-bit)Go to the Tools menu in ANSYS Workbench, and click Options. From the options on the left, selectExtensions. In the text box Additional Extension Folders, enter the path: fe-safe -installation-dir \components\WorkbenchFigure 2-1The Workbench Options DialogMake sure that the Save Binary Extensions with Project option remains as “Never”. Ticking the Debug Modeis not required for normal use, only troubleshooting.Copyright 2016 Dassault Systemes Simulia Corp.Issue: 4.0 Date: 31/08/2016fe-safe extension for ANSYS Workbench5
Now the fe-safe extension is available for use in any Workbench project. To add the fe-safe to extension toany Project Schematic select Extensions Manage Extensions (see below) and check the box next to fe-safe.Figure 2-2 The Workbench Extensions ManagerTicking the checkbox next to fe-safe will make it available in the current Workbench project, and it will appearwithin the Toolbox, ready to be deployed in a Workbench project.Figure 2-3 Analysis SystemsNote: It is important not to use the Install Extension menu item to link the fe-safe extension to Workbench.This copies the extension files elsewhere on the file system and breaks the link with the fe-safe solver and data resources.A failure will be observed when opening the project in ANSYS Mechanical if this has occurred. To resolve this, theextension must be uninstalled via the Extensions Manager and the steps above followed to correctly install the extension.6fe-safe extension for ANSYS WorkbenchCopyright 2016 Dassault Systemes Simulia Corp.Issue: 4.0 Date: 31/08/2016
Figure 2-4 Uninstalling an extensionUnlike most Workbench extensions, the fe-safe extension is not copied when the project is copied, because itis dependent on resources from an fe-safe installation which may not be present on another user’s machine.The advantage of the current installation method is that it’s straightforward to change the options inWorkbench to use the newest installation of fe-safe.The fe-safe data directory fe-safe-data-dir contains Workbench folders for each supported version.Find the archive used in Tutorial: Standard Fatigue Analysis in this directory.2.2Understanding the extensionThe fe-safe extension is dependent on solution data from upstream systems. This means that the fe-safesystem should be placed downstream of Static Structural system or Steady-State Thermal system as shownbelow in Figure 2-5 Connected Systems.Figure 2-5 Connected SystemsDrag-and-drop the fe-safe system onto the Model cell of an existing Static Structural (or Steady-State Thermalsystem) to read results from an existing ANSYS analysis.The system’s task is to define and run an fe-safe job. For this it needs an fe-safe project to be configuredbased on an ANSYS RST file or RTH file, which comes from the upstream system. An fe-safe project must bedefined for the fe-safe system to update correctly. The location of this project directory is determinedautomatically by Workbench.Right-click or double-click on the Setup cell of the fe-safe system to open it in ANSYS Mechanical. The outlinewill contain a selection of common settings to simplify the configuration of the project for basic workflows.Copyright 2016 Dassault Systemes Simulia Corp.Issue: 4.0 Date: 31/08/2016fe-safe extension for ANSYS Workbench7
Figure 2-6 fe-safe Project Basic SetupThe groups of elements to be analysed in fe-safe (i.e. which subsets of the model are to be analysed by fe-safe) is controlled from the settings in ANSYS Mechanical; bodies or named selections can be used to definethe fatigue analysis scope.The material information can be passed from Engineering Data (dependent on your local material databases),or configured within the normal fe-safe GUI. Basic one-block loading definitions and surface finish propertiescan be defined within ANSYS Mechanical.For more complex fatigue analysis configurations and workflows, the Advanced Setup option is provided. Thisopens the standard fe-safe GUI in “component mode” and gives access to the majority of fe-safe controls(including all the export contours). Any setup performed whilst in Advanced Setup mode will override thesettings in ANSYS Mechanical.The output of the fe-safe extension is a potable result for each of the fe-safe contours that were chosen forexport.8fe-safe extension for ANSYS WorkbenchCopyright 2016 Dassault Systemes Simulia Corp.Issue: 4.0 Date: 31/08/2016
Figure 2-7 fe-safe Result Contours2.3How to use the fe-safe extension2.3.1Specify the modelThe first step in setting up an fe-safe system is to specify an FEA solution file to base its analysis upon.Connect the fe-safe system downstream of a Model cell in another system. This will mean you will need tomake sure that the Solution cell is updated before performing the connection (since the FEA solution file willnot exist until the cell is up-to-date.)Pre-scanning of the FEA solution is not supported when using Workbench (see Limitations in section 0below). However, many settings regarding which FEA solution variables and other data are read can be madein the Analysis Settings item in the ANSYS Mechanical project tree. See section 0. Datasets are loaded for allextension workflows using full read settings configured in the Details of “Analysis Settings” panel (see moreabout selecting datasets to read in section 3.2).Note: On subsequent executions of the schematic, upstream systems will likely update the FEA solution file. If an fe-safesystem is connected to one of those upstream systems, it will refresh its datasets from the most recent FEA solution filethat was passed from upstream. It does not matter if the filename or location is different, the system will respect whateversolution file was most recently supplied. The caveat to this is that users must be sure that upstream systems will notchange the solution file in a way that will invalidate the fe-safe project you set up. (For example, if the number of steps ormaterial assignments are changed , or if a geometry selection is invalidated). If you think that an fe-safe project setup mayCopyright 2016 Dassault Systemes Simulia Corp.Issue: 4.0 Date: 31/08/2016fe-safe extension for ANSYS Workbench9
have been “invalidated” by upstream changes, you should right-click the Project cell and select Reset to clear the projectconfiguration.2.3.2Configure the projectThis is a description of a basic workflow for the fe-safe extension.Right-click the Setup cell and select Edit to start setting up an fe-safe project. The Mechanical window willappear with the fe-safe system in the outline. The properties can be set up in any order.Project SetupFigure 2-8 fe-safe Basic Project SetupThe settings in the ANSYS Mechanical Details of “Project Setup” panel are provided to accelerateconfiguration of basic workflows that use simple load cases, and to tell fe-safe which regions of the model toanalyse. More details on each property can be found in section 3.3below.The only required property (highlighted in yellow) is the Fatigue Analysis Scope (for details, see section 3.3).All other properties are set to appropriate defaults.The default fatigue loading will create a single elastic-block (1 repeat) with a sequence of FEA solutions(dataset sequence) formed from all of the steps in the upstream system.Anything configured within this panel can be overridden in the Advanced Setup mode. If these properties donot give enough fine-grained control over a particular fatigue configuration, then Advanced Setup modeshould be selected by right-clicking on Project Setup in the outline.10fe-safe extension for ANSYS WorkbenchCopyright 2016 Dassault Systemes Simulia Corp.Issue: 4.0 Date: 31/08/2016
Advanced SetupFigure 2-9 fe-safe Advanced Project SetupThis mode is for any workflows that are not covered by the simplified controls in ANSYS Mechanical. WhenAdvanced Setup is first used, fe-safe will respect any settings that were configured in ANSYS Mechanical tosetup the fe-safe project. Subsequent changes whilst in component mode will take precedence when theanalysis is run.Selecting the Advanced Setup menu item opens the fe-safe GUI in a “component mode” and starts to openthe solution (e.g. file.rst) in fe-safe component mode. This is a special mode used for controlling the inputand output of files for fe-safe, from an external software component. The controls for Source and Resultsfiles/paths, and project directory that users expect to be able to set in a standalone version of fe-safe are notaccessible from the component, but instead are set by the configurations made in Workbench.Whilst in component mode, the workflow is mostly identical to the workflow in the standalone fe-safe product.Any kind of loading can be configured, the analysis groups can be configured individually, and any extraoutput contours that are enabled will be available to plot in ANSYS Mechanical.When the configuration is finished, close the fe-safe component mode GUI and return to ANSYS Mechanical.Notice that the properties are now read-only:Figure 2-10 Disabled PropertiesCopyright 2016 Dassault Systemes Simulia Corp.Issue: 4.0 Date: 31/08/2016fe-safe extension for ANSYS Workbench11
This is to indicate that Advanced Setup now has control over the settings, However, these controls can beunlocked via the Unlock Properties menu item:Figure 2-11 Unlocking PropertiesBe aware that any further changes within these properties can potentially reset configuration in the AdvancedSetup. It is not a problem to change the scope of the analysis within ANSYS Mechanical from one namedselection to another; the effect will be that the now-redundant analysis group will be moved to the list ofUnused Groups in fe-safe.ExecutionTo run the fe-safe analysis, simply solve the schematic or the individual fe-safe system as shown in Figure2-12 (if in the Workbench GUI). From the ANSYS Mechanical window, use the Solve () action on theoutline for the fe-safe Solution cell.Figure 2-12 Update the ProjectAfter execution, the results contours will be available to plot under the Solution item in the fe-safe system inANSYS Mechanical. If results are missing, right-click on Solution to select the Worksheet: Result Summaryoption:12fe-safe extension for ANSYS WorkbenchCopyright 2016 Dassault Systemes Simulia Corp.Issue: 4.0 Date: 31/08/2016
Figure 2-13 Results SummaryAll of the result contours that were found in the fe-safe results file (*.FER) file should be listed under ListAvailable Solution Quantities.Figure 2-14 ANSYS Solution QuantitiesTo plot any of these results, right-click and choose Create User Defined Result.Figure 2-15 Creating a viewable resultThese results should now appear under the Solution item and can be evaluated like any other ANSYSMechanical result.2.3.3ParameterisationParameterisation is not supported in the current release of the fe-safe extension.Copyright 2016 Dassault Systemes Simulia Corp.Issue: 4.0 Date: 31/08/2016fe-safe extension for ANSYS Workbench13
2.3.4File ManagementThe fe-safe project directory can be set manually when starting a regular instance of fe-safe. When using thefe-safe extension for the Workbench environment, this directory resides in the project directory for the sameWorkbench project, alongside the other systems. These fe-safe working files in the project directory will besaved when the Workbench project is saved or archived (and reloaded when the schematic is loaded). Thedirectory structure logic is identical to other ANSYS Workbench systems with respect to design points. Thenaming convention for fe-safe files within the working directory is for an “SYS” prefix, possibly followed by “-1”,“-2” etc depending on how many instances of the fe-safe system were dropped into the schematic.Identifying the fe-safe working files and their location (if required) in the Workbench project directory can beaccomplished by selecting the View Files menu selection from the Workbench interface as shown below inFigure 2-16.Figure 2-16 Files Table14fe-safe extension for ANSYS WorkbenchCopyright 2016 Dassault Systemes Simulia Corp.Issue: 4.0 Date: 31/08/2016
2.3.5Resetting the cellIf required, you can reset the fe-safe project to its initial state using the Reset Project menu item. This deletesthe underlying fe-safe project directory, forcing fe-safe to create a new project and re-read the FEA solutionfrom scratch.Figure 2-17 Resetting the project2.3.6LimitationsPre-scanning of the FEA solution is not supported when using Workbench, as fe-safe has no way at presentto replay the pre-scan choices when the solution is refreshed by subsequent runs. The steps in the FEAsolution are loaded in full every time it is updated by Workbench.PSD-based loading from Harmonic Analyses are not possible at the current release.Nodal groups are not supported and fe-safe only reads the element-nodal (corner) data from the FEAsolution.Plug-in modules (fe-safe/Rubber, or user-defined plugin algorithms defined using Custom Module Frameworkor CMF for fe-safe cannot be used at this release.The Engineering Data cell provides its material data as a MatML file (an XML extension designed to supportstandardised material data). Presently fe-safe has no interpreter for MatML so cannot receive its material datafrom this cell, although in this release there is an option for matching material names with a fe-safe materialdatabase file.At this release, fe-safe does not support concurrent execution. Measures have been put in place to stop fe-safe being invoked concurrently within a Workbench schematic; however you should take care not to design aschematic where this could occur.Copyright 2016 Dassault Systemes Simulia Corp.Issue: 4.0 Date: 31/08/2016fe-safe extension for ANSYS Workbench15
16fe-safe extension for ANSYS WorkbenchCopyright 2016 Dassault Systemes Simulia Corp.Issue: 4.0 Date: 31/08/2016
3Interface ReferenceNote that only those interface elements of particular importance for using fe-safe with Workbench aredescribed here.3.1fe-safe client application GUI vs component GUIWhen Advanced Setup is selected, fe-safe opens up in component mode. The look of this is essentiallyidentical to standalone fe-safe, with some minor differences. These are shown in Figure 3-1.Figure 3-1fe-safe stand-alone GUI (left) and Workbench component GUI (right)The differences are mostly located in the Fatigue from FEA window. In component mode, the buttons forchoosing the source file and output file have been removed (they have been moved to the Workbench projectschematic). Also, the Analyse! button has been removed, since the purpose of the Workbench extension is torun fe-safe from inside the Workbench project environment.3.2fe-safe Model Reading propertiesAs noted in 2.3.1 above, pre-scanning is not available in the component mode, and the default full readsettings for Ansys RST files in fe-safe can be configured using the Details of “Analysis Settings” panelaccessible from of the fe-safe Analysis Settings in Mechanical. These settings are used to control what modeldata and FEA solutions from the RST/RTH file are read by fe-safe as shown below:Figure 3-2 RST full read optionsCopyright 2016 Dassault Systemes Simulia Corp.Issue: 4.0 Date: 31/08/2016fe-safe extension for ANSYS Workbench17
Checkboxes corresponding to Read Geometry and Detect Surface are enabled by default to complete surfacedetection in fe-safe as described in the fe-safe user guide. If you are using a 3D shell model, this is notnecessary but not detrimental either.FEA solutions of elemental-nodal strain, force, and temperature can be added to the Dataset Read Options byengaging checkboxes for those options, and subsequently used in the fe-safe extension. Stress is read bydefault since most FEA Fatigue analysis are based on elastic material with plasticity correction during theanalysis process in fe-safe.Note that it is the responsibility of the engineer to read strains only when elastic-plastic material propertieshave been applied to the body selected for FEA Fatigue analysis in fe-safe. Similarly, forces are only requiredin the case of welded joint fatigue using Verity in fe-safe (loading them is not detrimental to analysis).Temperatures will only have an impact if a material with temperature variability is selected for FEA Fatigueanalysis (loading them is not detrimental to analysis). As with all FEA interfacing, loading unnecessarydatasets may take more time.3.3fe-safe Project Setup propertiesThe properties below are configured as part of the Details of “Analysis Settings” panel in the Mechanicalwindow.3.3.1Material PropertiesAt the present release, the materials supplied by default with ANSYS Engineering Data do not have all thematerial properties that fe-safe requires for a fatigue analysis. Conversely the material databases that aresupplied with fe-safe are not compatible with ANSYS. Accordingly, for fe-safe to find the material data itneeds, a material database file (*.dbase) must be the source of the data. There are two methods availablewith the fe-safe extension for specifying the material data:Figure 3-3 Comparison of Material Properties defined with Advanced Setup (above)versus Match with Engineering data (below)18fe-safe extension for ANSYS WorkbenchCopyright 2016 Dassault Systemes Simulia Corp.Issue: 4.0 Date: 31/08/2016
Define within fe-safe Advanced SetupThis is the default option. It requires that the Advanced Setup mode be used to open up the fe-safe GUI andassign materials to analysis groups, as in a normal fe-safe workflow. Any .dbase file that is opened in fe-safecan be used; if this step is omitted then fe-safe will report an error to the Workbench log when the system issolved.Match with Engineering DataWith this option, fe-safe will attempt to match the materials from Engineering Data to a given fe-safe materialsdatabase, based on the material name.The fe-safe material *.dbase file must be specified in the Material Database Location field (this is a filebrowser field).fe-safe will look at each body in the model to discover which material has been assigned:Figure 3-4 Determining the material for a given bodyCopyright 2016 Dassault Systemes Simulia Corp.Issue: 4.0 Date: 31/08/2016fe-safe extension for ANSYS Workbench19
In this case, “Structural Steel” is associated with the body “Solid 1”. Then when the analysis groups arecreated, fe-safe will expect to find a “Structural Steel” material in the database (the name match is casesensitive and punctuation-sensitive), and it will assign fatigue properties with the same name to the group infe-safe created for that body. If the fatigue analysis is based on named selections, fe-safe will create ananalysis group for each named selection and apply the material associated with that named selections. If anamed selection spans several materials, analysis groups will be created for each.To use this approach effectively, a *.dbase file must be maintained with materials that match those availablein Engineering Data. It is only recommended for organisations with a standardised library of materials.3.3.2Fatigue Analysis ScopeThis is where the scope of the analysis can be restricted to regions of the model. Under Scoping Method thereare three options:Geometry SelectionFigure 3-5 Scoping a fatigue analysis to GeometryWith this mode, either bodies or faces can be selected. fe-safe will create an analysis group for the chosenentity. Click on the yellow field, use the body/element pickers in ANSYS Mechanical to choose the entity, thenclick Apply.Named SelectionFigure 3-6 Scoping a fatigue analysis to a Named SelectionWith this mode, either bodies or faces can be selected. fe-safe will create an analysis group for the chosennamed selection. The drop-down box displays any
Experienced users of ANSYS Workbench new to the fe-safe extension for ANSYS Workbench Read Chapter 4, Chapter 2, then work through the tutorial to familiarise yourself with the fe-safe extension for ANSYS Workbench. Once you have done this, follow the procedure described in Chapter 2 with your own data, referring to Chapter 0 as necessary.