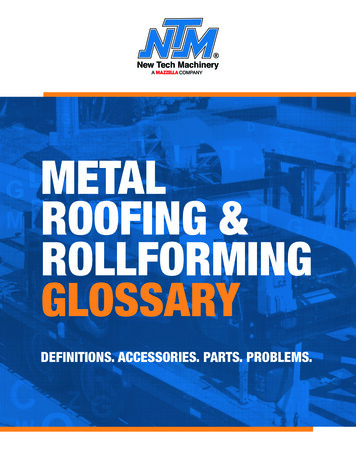
Transcription
New Tech MachineryMETALROOFING &ROLLFORMINGGLOSSARYDEFINITIONS. ACCESSORIES. PARTS. PROBLEMS.
ROLLFORMING DEFINITIONSCONTROLLERManual or computer-operated device that makes the machinefunction and follow the input measurements and preferences.DRIVE ROLLERSWhat moves the metal through the machine; typically madeof metal or polyurethane.FORMING ROLLERSForming rollers and forming stations are the individualcomponents the metal passes through to bend or form adesired shape.FORMING STATIONSThe spots at which the metal is bent or manipulated by a pairof forming rollers.HEMMINGProcess where material is folded back onto itself.HYDRAULIC TANKSThey aren’t standard on all rollforming machines, but theyare commonly added to make the machine faster for higherproduction or to automate the shears.MACHINISTA worker who fabricates, assembles, or repairs machinery;a craftsman skilled in the use of machine tools; one whooperates a machine.METAL COILMetal sheets that have been wound into a large roll. Coils arethe most efficient way to transport or store sheet metal.METAL ROLLFORMINGThe proess of feeding metal, finished, coiled, flat, orotherwise, through a series of rollers where each rollerstation further manipulates the piece of metal into thedesired shape.METAL SHEETMetal formed into thin sheets by a rolling process.NOTCHINGCutting different shapes out of sheet metal from the edge ofa blank strip to prepare a panel for installation.PORTABLE ROLLFORMING MACHINETakes everything a metal rollformer does but in a smallersize so it can be transported easily. A portable rollformer canbe powered by gas or electricity, and often comes with anattached or stand-alone decoiler for the metal and run-outtables for finished panels.PORTABLE ROOF PANEL MACHINEA condensed, transportable piece of machining equipment usedto rollform metal sheets/coils into metal roof or wall panels.PORTABLE SEAMLESS GUTTER MACHINEA condensed, transportable machine used to rollform seamlessgutters (from metal sheets/coils) directly at a job site.POST-CUT SHEARMetal part is formed first in the forming stations and cutafterward.POWER SOURCEHow the rollformer is powered and able to run; usuallyelectric or gas.PRE-CUT SHEARMetal is cut at the entry end of the machine before it goesthrough the forming stations.RUN-OUT TABLEAn adjustable height platform used to support and keeproofing panels level as they exit the rollforming machine.Typically supplied in 10’ (3m) lengths.SHEAR OR GUILLOTINECuts the metal part or component at a specific length.SLITTINGCutting a sheet of metal into narrower strips.TAPERINGMaking a panel narrower at one end.
METAL ROOFING DEFINITIONSBATTEN PANELTwo legs of the panels are rollformed and butted up next toeach other, a metal cap goes over the legs to create a seam,and either snaps on or is mechanically seamed into place.The two common types of parts that can go over the legsare tee seam (mechanically seamed into place, resemblinga “T”) and snap cap (snap over the panel legs without anymechanical seaming).COOL METAL ROOFINGPainted or coated metal panels that reflect the sun’s energyto dissipate heat.EPDM ROOFINGEthylene propylene diene monomer; a synthetic rubber usedas roofing material for slow slope or flat roofing applications;common in commercial structures.METAL COILS/SHEETSMetal roofing starts out as metal coils or sheets, whichare then rolled out, cut, and rollformed into panels forinstallation. Metal coils are long, continuous metal rolls thathave been treated or coated with paint.METAL PANEL SEAM TYPESThe shape and way two or more metal panels are seamedtogether vertically, including these types: snap-lock,mechanical lock, batten panel, nail/fastener flange, andexposed fastener lap seam.METAL ROOFINGA roofing system made from metal panels or tilescharacterized by its high wind/storm resistance,impermeability, and longevity.NAIL/FASTENER FLANGEEXPOSED FASTENER LAP SEAMThe overlapping ends of the lap panels are fastened down tothe deck from the top of the panel.EXPOSED FASTENER METAL ROOFINGSimilar to a snap-lock panel system, but it’s directly fasteneddown to the deck of the roof through the male leg of the metalpanel instead of using a clip to attach the panel to the deck. Oncethe fasteners are in place, the female leg of the panel snaps overthe entirety of the male leg, which hides the fastener head.A roofing system where the panels are fastened to the structurethrough the face of the metal and directly into the roof deck orframing below, and are left visible on top of the panels.PANEL PROFILEFLANGEPANELSA projecting rim or edge of a part, usually narrow and ofapproximately constant width for stiffening or fastening.GALVALUME A metal coating that begins as a carbon steel base that iscontinuously hot-dipped with aluminum and zinc alloys untilit reaches a coating consisting of 55% aluminum, 43.4% zincand 1.6% silicone.The shape and way two or more panels are seamed together.The rollformed pieces of metal coil that have been shapedinto the desired profile/ribbing structure and are ready to beseamed together to form a roof.PROFILEThe shape metal panels are formed into; they also determinehow the panels fit and connect together.RIB ROLLERSGAUGEMeasurement for the thickness of a metal. Smaller gaugenumbers indicate thicker metal.MECHANICAL LOCKPanels that have been rollformed with specific edges that lineup with each other. Once the panels are engaged, a hand ormechanical seamer is used to bend the edges and lock thepanels together. Types of mechanical lock panels include singlelock (one fold of the seam at 90 degrees) and double lock (twofolds of the seam, resembling a paper clip at 180 degrees).The “patterns” or striations rollformed into a metal roofingpanel between the seams. Common kinds include: flat(no indents between the seams), ribbed (some shape orindentation between seams), striated (small, consistentindentation lines in the pane), corrugated (larger, constantwaving of the metal panel), and clip relief (stiffening ribadjacent to the seam that allows the space for a clip).ROLLFORMING EQUIPMENTThe machinery, stationary or portable equipment, that formsand shapes the coil or sheets into individual panels.
SEAMThe side rib at which two metal panels come together andare connected.STANDING SEAM METAL ROOFINGA concealed fastener metal roof system featuring a raisedvertical seam and a broad, flat area between the two panel legs.SNAP-LOCKPanels that have been carefully rollformed with specificallyshaped edges, male and female leg, that snap together, thusnot requiring hand or mechanical seam during installation.INSTALLATION ACCESSORIES FOR METAL ROOFINGATTACHMENT CLAMPSClamps are small metal parts that are tightened and attachedto the top of the metal roof at its standing seam. Theseclamps have screws at the top used to attach extra roofingitems such as a snow retention system, solar panels, satellitedishes, signs, AC units, etc.BUTYL TAPEUsed in a similar fashion as sealant to seal cracks and seamson metal roofs, but it’s in the form of one or two-sided tapeand seals by compression. Also used for trimming purposes.CLIPSA concealed anchor that attaches a metal panel to thesubstrate (roof deck or other material beneath the metalpanels) with the use of fasteners. Clips are sometimesreferred to as cleats as well.FASTENERSPIPE BOOTThe cone-like fitting that is installed around an exhaust pipethat exits through the roof.RIVETSSimilar to fasteners but require a special rivet gun to install.SEALANTUsed during installation to seal out water, dirt, wind, andother substances that can get into small spaces, making theroof as weather-tight as possible. Typically made of siliconeand polyurethane.UNDERLAYMENTThe layer of material that goes underneath the metal panelsand protects them from water and moisture, ice, hightemperature and vapors. Synthetic and felt are the two mostpopular underlayments used for metal roofs.Any mechanical securement device used to attach the metalroof to the roof deck during installation.PARTS OF A ROOFCRICKETA peaked saddle construction installed between a chimneyand the roof surface to help prevent accumulation of snowand water.CURBAn accessory used to mount additions (AC units, fans, signs,etc.) to provide a level resting structure on a sloped roof.DECKA structural component of the roof of a building; the materialbetween the structural components (trusses, joists, purlins,etc.) and the roofing material.DRIP EDGEA long piece of metal installed on a roof to keep water awayfrom the fascia and running into the gutter.EAVEThe projecting edge of a roof that extends beyond thesupporting wall.FASCIAA vertical or steeply sloped roof or trim located at theperimeter of a building.
FLASHINGComponents used to direct water away from critical areas ofthe roof wherever the roof plane meets a vertical surface, likea wall or dormer.GABLEThe triangular section of a wall between the edges of asloping roof. The trim occupying this area of the roof istypically called “gable trim” or “rake trim.”RIDGEThe highest point on the roof, represented by a horizontal linewhere two roof areas intersect, running the length of the area.SEAMA joint formed by joining two separate sections of material.SOFFITThe underside of any exterior overhanging section of a roof eave.HEMThe edge created by folding metal back on itself.SUBSTRATEThe surface upon which the roofing or waterproofingmembrane is applied.HIPThe inclined external angle formed by the intersection of twosloping roof panels.PITCHVALLEYThe internal angle formed by the intersection of two slopingroof planes.The slope of a roof, measured by dividing the roof rise by its run.PROBLEMS WITH METAL ROOFING & ROLLFORMING METAL COILS / SHEETSCAMBERCoil that has a stretched edge and curves slightly from sideto side.CHALKINGThe whitish residue that can become visible on a paintedor coated metal surface over time due to degradation of aningredient in paints, coatings, or other materials.FADINGThe color change in painted metal roofs or walls caused bythe breaking down of pigment when substances (water,pollution, chemicals, etc.) in the atmosphere and specificenvironments react with the pigment.OIL CANNINGThe perceived waviness of a metal panel and is an inherentcharacteristic of light-gauge, cold-formed metal products.Oil canning can occur with nearly any type of metal materialused in construction.PANEL CURVATUREWhat happens when panels don’t come out of the machinein a straight line. There are two types of panel curvature:uphill (the ends of the panel are coming up off the deckwhile the middle of the panel is touching the deck) anddownhill (the center of the panel is coming up of the deckwhile the ends touch the deck).PANEL MARKINGSMarks on the panel that occur during the rollforming process. These may take the form of long streaks or imperfectspots on top or bottom of panels, and are usually caused bytrapped dirt or debris in the forming or drive rollers, film onthe metal sheet, coil catching a roller or getting stuck in themachine, pieces of plastic caught in the machine, or the metalscraping against the exit or entry shear dies.SHEAR MISALIGNMENTThis happens when the shear is not accurately cutting panels,which could mean the Entry/Exit Shear Dies are misaligned orthe shear blades aren’t appropriately positioned according tothe profile type.If you have any additional questions or want to schedule a consultation, feel free to contact us at 1.800-574.1717 orinfo@newtechmachinery.com to speak to one of our knowledgeable and helpful rollforming specialists!
The shape metal panels are formed into; they also determine how the panels fit and connect together. METAL COILS/SHEETS Metal roofing starts out as metal coils or sheets, which are then rolled out, cut, and rollformed into panels for installation. Metal coils are long, continuous metal rolls that have been treated or coated with paint. RIB ROLLERS